A polyethylene insert goes between the femoral and tibial components in knee replacements that MicroPort Orthopedics Inc. produces, said Michael Hipp, project engineer/engineering operations at the Arlington, Tennessee, manufacturer. The insert is in high demand and that demand is forecast to continue.
“This part is a double-sided product,” he explained. “It has a lock detail that locks into the tibia and then there’s an articulating surface that mates with the femoral component.”
The insert product line varies by size and thickness to suit the requirements of a diverse range of implant patients, with more than 150 part numbers that require an equal number of part programs, he added.
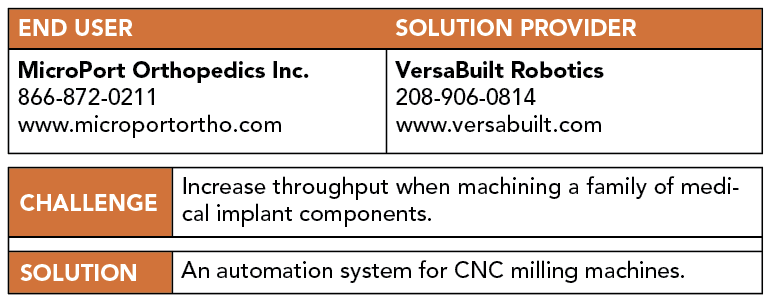
To satisfy demand, Hipp said the company previously produced them in work cells that consisted of a CNC milling machine for the initial mill lock detail operation, and two other mills on the articulating side due to long cycle times of the articulating surface. MicroPort Orthopedics produces them during its three-shift operation and required scheduling multiple days of overtime throughout the year to keep pace.
Hipp said his boss instructed him to contact Phillips Automation, who initially encouraged VersaBuilt Robotics in Boise, Idaho, to move forward with a project to automate insert production. The first iteration of the CNC Mill Automation System from VersaBuilt involved a Universal Robots collaborative robot feeding one Robodrill milling machine and VersaBuilt’s Multigrip base and top jaws to enable a one-operation cycle stop.
“Within the application, the trunnion table would rotate on axes, change tools and machine parts to print, and then as the parts were completed, the robot would swap out part blanks, mill lock detail/mill articulating surface for the finished components,” Hipp said.
Seeing room for improvement, Hipp said MicroPort Orthopedics “challenged” VersaBuilt to enhance the system to enable one robot feed for two CNC mills. “We paid for engineering time, but it was very well worth it.”
He added, “We now have the Versabuilt VersaCart stationing two orders and the Automation System feeding two separate Robodrills. Once the operation is started, all loading, swapping parts from operation one and operation two, and unloading were with one automation system. This in turn freed up time for machinists and machine availability.”
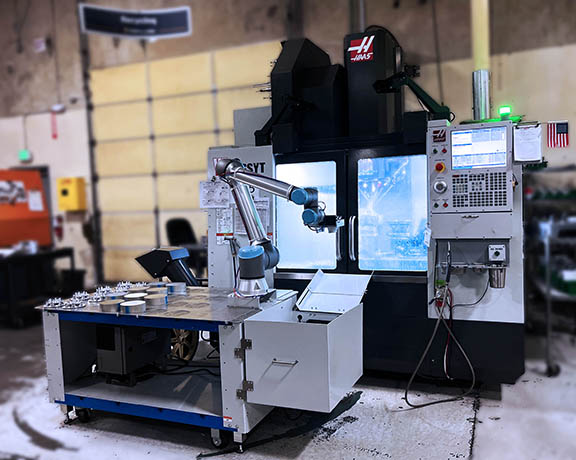
The medical implant manufacturer now has three automation systems to produce the implants, with three UR cobots feeding six Fanuc Robodrill compact machining centers, Hipp noted. “The operators are responsible for inspecting the parts as they’re being run on a statistical inspection plan, but then the parts go through a separate inspection area, or final inspection, after the machining process.”
Depending on the part program, cycle time improved from 20 to 30 minutes collectively from start to finish to less than 20 minutes, he explained. “Pretty much the machines do not have to stop, so throughput has improved.”
One aspect of the automation system that Hipp said is beneficial is that end users are not required to do any robot programming.
According to VersaBuilt, all robot motion is preprogrammed yet fully customizable. “Simply enter part dimensions and CNC milling program numbers and enjoy the benefits of CNC automation,” the company stated.
Hipp said: “The canned program is written and validated. The load and unload portion of that and how and where it designates the completed parts to go to on the table was nothing that we had to deal with. It’s nice to see something that was purchased still be as accurate, as reliable and functioning the same as it was on day one.”
For part of the fixturing, he said VersaBuilt teamed up with Martin Manufacturing in Elsmere, Kentucky, which makes CNC trunnion tables, as well as other workholding products. “Those trunnions came in at a fair price and have been nothing but outstanding.”
Tsudakoma rotaries had already been in use on Robodrills for an existing machining process. “There were a few design changes made on the fly to get everything dialed in, but the cooperation between all parties was seamless.”
Like numerous manufacturers that implement automation, Hipp said there was anxiety among some of the workers initially. “The first thing that people ask is, ‘Is this going to replace my job?’ The goal was never to reduce head count and we have not done that.”
The goal instead is to add more automation, he added. “It has proven itself to work and work very well.”
Contact Details
Related Glossary Terms
- centers
centers
Cone-shaped pins that support a workpiece by one or two ends during machining. The centers fit into holes drilled in the workpiece ends. Centers that turn with the workpiece are called “live” centers; those that do not are called “dead” centers.
- computer numerical control ( CNC)
computer numerical control ( CNC)
Microprocessor-based controller dedicated to a machine tool that permits the creation or modification of parts. Programmed numerical control activates the machine’s servos and spindle drives and controls the various machining operations. See DNC, direct numerical control; NC, numerical control.
- feed
feed
Rate of change of position of the tool as a whole, relative to the workpiece while cutting.
- gang cutting ( milling)
gang cutting ( milling)
Machining with several cutters mounted on a single arbor, generally for simultaneous cutting.
- milling
milling
Machining operation in which metal or other material is removed by applying power to a rotating cutter. In vertical milling, the cutting tool is mounted vertically on the spindle. In horizontal milling, the cutting tool is mounted horizontally, either directly on the spindle or on an arbor. Horizontal milling is further broken down into conventional milling, where the cutter rotates opposite the direction of feed, or “up” into the workpiece; and climb milling, where the cutter rotates in the direction of feed, or “down” into the workpiece. Milling operations include plane or surface milling, endmilling, facemilling, angle milling, form milling and profiling.
- milling machine ( mill)
milling machine ( mill)
Runs endmills and arbor-mounted milling cutters. Features include a head with a spindle that drives the cutters; a column, knee and table that provide motion in the three Cartesian axes; and a base that supports the components and houses the cutting-fluid pump and reservoir. The work is mounted on the table and fed into the rotating cutter or endmill to accomplish the milling steps; vertical milling machines also feed endmills into the work by means of a spindle-mounted quill. Models range from small manual machines to big bed-type and duplex mills. All take one of three basic forms: vertical, horizontal or convertible horizontal/vertical. Vertical machines may be knee-type (the table is mounted on a knee that can be elevated) or bed-type (the table is securely supported and only moves horizontally). In general, horizontal machines are bigger and more powerful, while vertical machines are lighter but more versatile and easier to set up and operate.
- milling machine ( mill)2
milling machine ( mill)
Runs endmills and arbor-mounted milling cutters. Features include a head with a spindle that drives the cutters; a column, knee and table that provide motion in the three Cartesian axes; and a base that supports the components and houses the cutting-fluid pump and reservoir. The work is mounted on the table and fed into the rotating cutter or endmill to accomplish the milling steps; vertical milling machines also feed endmills into the work by means of a spindle-mounted quill. Models range from small manual machines to big bed-type and duplex mills. All take one of three basic forms: vertical, horizontal or convertible horizontal/vertical. Vertical machines may be knee-type (the table is mounted on a knee that can be elevated) or bed-type (the table is securely supported and only moves horizontally). In general, horizontal machines are bigger and more powerful, while vertical machines are lighter but more versatile and easier to set up and operate.
- robotics
robotics
Discipline involving self-actuating and self-operating devices. Robots frequently imitate human capabilities, including the ability to manipulate physical objects while evaluating and reacting appropriately to various stimuli. See industrial robot; robot.