How does a shop that makes 4,000 toolholders a day effectively manage the toolholder assembly process to be as efficient and cost-effective as possible? In addition, how does the business manage to do the work in a consistent, accurate manner without depending on the ever-shrinking trained workforce available today?
Most people think about adding automation to the parts production side of a manufacturing operation, and this is of course a good thing to look at in general to become more efficient. However, how many companies look at the toolroom as a place where automation can play a key role in reducing costs and eliminating human interaction with the process while still providing the most accurate, consistent toolholder assembly in the production each and every time?
Igenhausen, Germany-based Haimer GmbH, an innovative global player in tool management for machine tools, asked itself this exact question for its own production, and it is convinced that production engineering needs to advance by implementing automation and digitization. (Haimer USA LLC is in Villa Park, Illinois.) This development is an established part of Haimer’s own production and also has found its way into the product range: from Industry 4.0-capable devices all the way up to the Automation Cube robotic cell, which can be scaled as required and is suitable for automated shrinking, presetting and balancing.
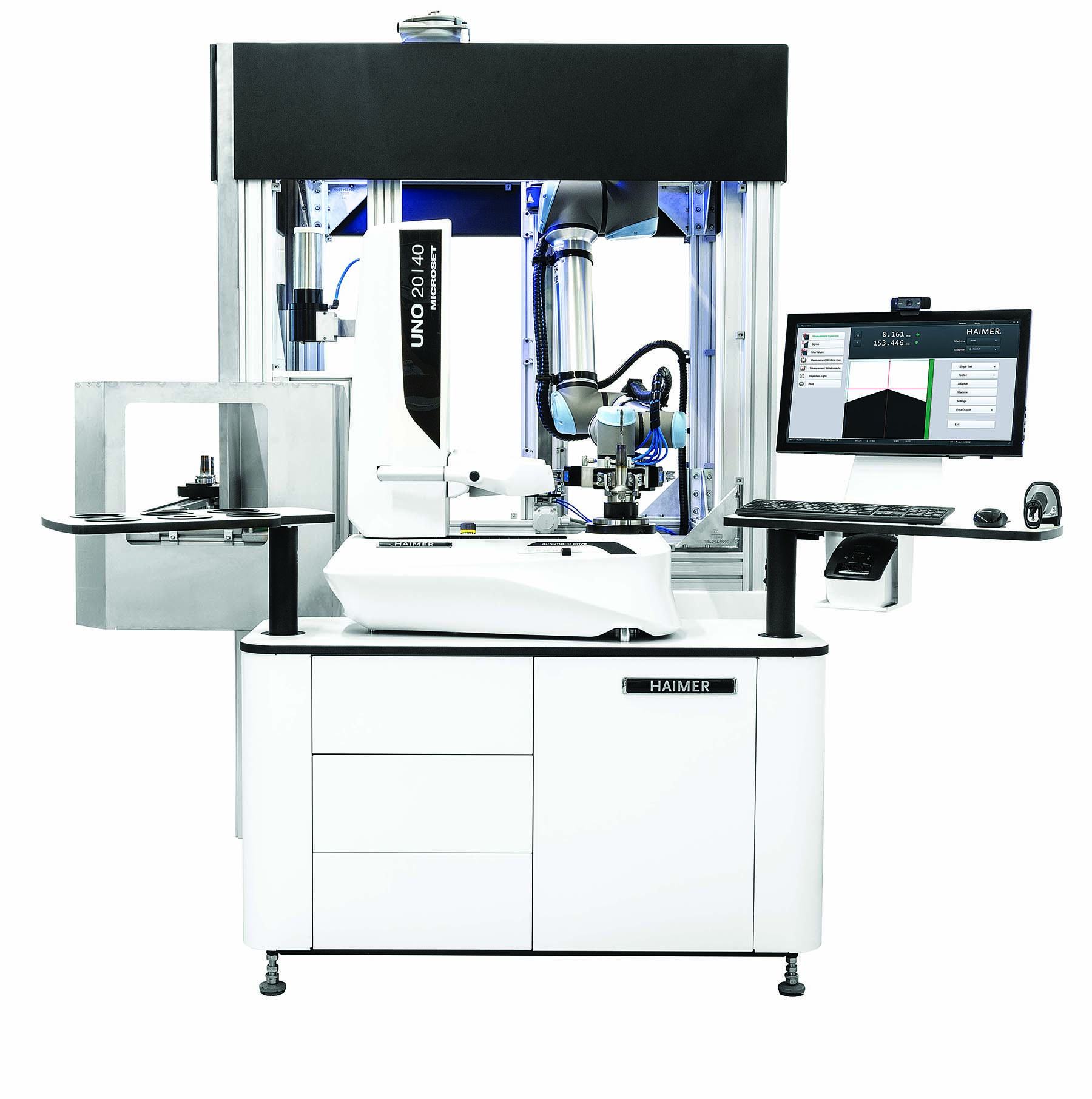
Efficient machining demands powerful machines and tools, “as well as high-precision toolholding technology, which ensures that the precision of the spindle is transferred from the spindle to the cutting edge,” said Andreas Haimer, managing director of Haimer GmbH.
That statement has many years of experience behind it. The company started 45 years ago as a machining service provider for the aerospace and die mold industry and soon began to develop high-precision toolholders for its own use.
Necessity of Automation
Haimer also has ample experience in automation. The Bavarian family company decided to equip its machine tools with robots for loading and unloading over 20 years ago. Since then, automation at the company has advanced swiftly as evidenced by manufacturing facilities at the headquarters in Igenhausen and in Motzenhofen, which is just six minutes away. Motzenhofen’s production plant in particular, which has been operating since 2018, was equipped from the beginning with numerous automated machining centers.
“If, like us, you depend on a very high level of in-house production completely made in Germany, or for other shops manufacturing in other high-cost manufacturing markets,” Andreas Haimer said, “there is no way you can avoid extensive digitization and automation. Otherwise we would not be able to keep up economically with our global competitors.”
Soft machining of toolholders is carried out in Motzenhofen, alongside all precision components for shrink-fit and balancing machines, including accessories. Up to 4,000 rotating toolholders can be turned and milled there per day before heat treatment, followed by µm-precise grinding in Igenhausen. Fine balancing also is conducted in Igenhausen using systems that have been developed in-house and are automated fully.
Not All Automation Is Complex
Among others, in Motzenhofen the company operates a totally automated manufacturing cell with several five-axis DMG Mori MillTap 700 machines. These highly dynamic vertical machining centers, which were installed at the beginning of 2019, are perfect for boring and milling components, such as BT30 and SK30 steep-taper toolholders.
“Here we use a simple plug-and-play complete solution, which includes a fully automated loading and unloading system using a Kuka robot,” said Manfred Mayr, who completed his apprenticeship at Haimer over 40 years ago and is responsible for about 100 machine tools as plant and production manager. “Blanks and the components that have been produced are placed in three drawers, each of which has around 78 positions. This ensures that unmanned production is possible for a minimum of eight hours up to 20 hours.”
He said the automation of four identical DMG Mori NHX 4000 machining centers, which are equipped with a pallet pool flexible manufacturing system, is considerably more demanding.
“There are 12 pallets, each with 400 places, ready to process various components” Mayr said. “This provides us with ideal flexibility — also when it comes to smaller batch sizes and short-notice changes in the production flow.”
The machines generally work highly productively and trouble-free in a three-shift operation supervised by just one employee. To operate the machines as autonomously as possible with a large variety of products, the company had the machines equipped with a tool magazine with 183 tool pots.
Mayr considers the fact that all tools for these machines are equipped with a radio frequency identification chip on the toolholder to be key. The chips are read in at a dedicated station when they are changed into the magazine. This means that the control digitally receives the correct tool data from Haimer’s Microset VIO linear presetter, eliminating input errors and mix-ups.
Digital Data Flow
Mayr said a basic requirement for economical operation of the NHX and all other machine tools is a perfectly operating, well-organized
toolroom.
“This technology represents a central component of our expertise,” he said. “Of course we use our own products here, from shrink-fit, balancing and presetting machines to toolholders and cutting tools. This enables end-to-end digitization all the way to the machine, which is an essential component for automated, economic manufacturing operations.”
This means that all tools for milling and turning machines are prepared centrally and managed in the toolroom. The tools are mounted, shrank, measured and balanced, and all data is recorded digitally. This takes place on the aforementioned RFID chips, by means of digital interfaces, such as post-processors, or via QR codes. Only then are the tools packed onto special tool wagons as required, where a machine operator can pick them up for a machine. This eliminates extra walking throughout the shop.
“Only with optimal tool presetting (can) the machines run and not the employee,” Mayr said.
The digitization of production processes represents a key factor for success for not merely Haimer but every company.
“As the tool with its specific data is a central component of the process chain for machining,” Andreas Haimer said, “it needs to fit into the digital production environment.”
This necessitates consistent implementation of all digital options, including the tool, the toolholder, the clamping process, the balancing, the tool presetting and the use on the machine. Especially when making new investments, he said a user should ensure that every element in the tool environment is Industry 4.0-capable and can be incorporated into the digital workflow.
“Our products are fully prepared for digital production,” Andreas Haimer said. “We have even developed our own tool management software, the Haimer Data Analyzer and Controller, which establishes and manages the exchange between the actual and target values, along with other tool data between the individual stations in the toolroom and the company network. Our equipment in the Industry 4.0 series (is) prepared for automation with modern digital features and interfaces. Moreover, they have been designed to be robust with a long service life, which is a guarantee of the highest process reliability — a decisive factor for successful automation.”
The company supports a wide range of automation models with its products. The range starts with individual machines that combine several work steps, such as the Microset VIO linear tool-shrink presetter. It is capable of shrinking tools with a length adjustment on the μm scale while simultaneously measuring them. Among other things, the presetter is ideal for sister tools, which always need to be shrank to the same dimensions. The use of these tools in series production or in multispindle machines promises to increase process reliability and minimize setup times.
In 2021 at EMO Milano and in 2022 at IMTS in Chicago, Haimer presented a much more far-reaching solution: the Shrink Automation Cube. This automated shrink station contains a collaborative robot that supports shrinking and unshrinking of tools with highly accurate length repeatability. The cell is scalable according to the requirements of a customer. The cube is controlled by Data Analyzer and Controller tool management, and Haimer’s presetting and balancing technology can be integrated into the cube. A scanner for reading out unique tool combinations and a conveyor belt that is variable in length are also available.
Such equipment allows the following procedure to be carried out, for example: The operator places a worn-out tool — consisting of a toolholder and a cutting tool — on the conveyor belt and provides a new cutting tool. The cobot picks up the complete toolholder assembly and identifies it via its unique data matrix code, optionally via RFID. The cobot then picks up the new cutting tool and measures the cutting edge. In the meantime, the coil moves onto the worn-out toolholder assembly, unshrinks the old cutting tool and then shrinks the new one to the required projection length. After air cooling, the new, complete tool is ready for use, and the old cutting tool is disposed of.
“This automation solution is suitable for companies that perform a very large number of shrink operations every day,” Andreas Haimer said.
Especially if a company has limited expertise with automation, a complete solution like this from a single source is a good idea. He pointed out as well that Haimer components can be integrated into almost any existing automation environment.
“We are also happy to partner on larger automation projects,” Andreas Haimer said.
It is clear that automation will be an important part of the future for Haimer's production facilities in Germany and for manufacturing plants throughout the world to be efficient, consistent and cost-competitive. Automation must be considered in the toolroom and not just on the parts production side of a manufacturing facility.
Contact Details
Related Glossary Terms
- boring
boring
Enlarging a hole that already has been drilled or cored. Generally, it is an operation of truing the previously drilled hole with a single-point, lathe-type tool. Boring is essentially internal turning, in that usually a single-point cutting tool forms the internal shape. Some tools are available with two cutting edges to balance cutting forces.
- centers
centers
Cone-shaped pins that support a workpiece by one or two ends during machining. The centers fit into holes drilled in the workpiece ends. Centers that turn with the workpiece are called “live” centers; those that do not are called “dead” centers.
- flexible manufacturing system ( FMS)
flexible manufacturing system ( FMS)
Automated manufacturing system designed to machine a variety of similar parts. System is designed to minimize production changeover time. Computers link machine tools with the workhandling system and peripherals. Also associated with machine tools grouped in cells for efficient production. See cell manufacturing.
- gang cutting ( milling)
gang cutting ( milling)
Machining with several cutters mounted on a single arbor, generally for simultaneous cutting.
- grinding
grinding
Machining operation in which material is removed from the workpiece by a powered abrasive wheel, stone, belt, paste, sheet, compound, slurry, etc. Takes various forms: surface grinding (creates flat and/or squared surfaces); cylindrical grinding (for external cylindrical and tapered shapes, fillets, undercuts, etc.); centerless grinding; chamfering; thread and form grinding; tool and cutter grinding; offhand grinding; lapping and polishing (grinding with extremely fine grits to create ultrasmooth surfaces); honing; and disc grinding.
- milling
milling
Machining operation in which metal or other material is removed by applying power to a rotating cutter. In vertical milling, the cutting tool is mounted vertically on the spindle. In horizontal milling, the cutting tool is mounted horizontally, either directly on the spindle or on an arbor. Horizontal milling is further broken down into conventional milling, where the cutter rotates opposite the direction of feed, or “up” into the workpiece; and climb milling, where the cutter rotates in the direction of feed, or “down” into the workpiece. Milling operations include plane or surface milling, endmilling, facemilling, angle milling, form milling and profiling.
- toolholder
toolholder
Secures a cutting tool during a machining operation. Basic types include block, cartridge, chuck, collet, fixed, modular, quick-change and rotating.
- turning
turning
Workpiece is held in a chuck, mounted on a face plate or secured between centers and rotated while a cutting tool, normally a single-point tool, is fed into it along its periphery or across its end or face. Takes the form of straight turning (cutting along the periphery of the workpiece); taper turning (creating a taper); step turning (turning different-size diameters on the same work); chamfering (beveling an edge or shoulder); facing (cutting on an end); turning threads (usually external but can be internal); roughing (high-volume metal removal); and finishing (final light cuts). Performed on lathes, turning centers, chucking machines, automatic screw machines and similar machines.