I started working for my father in 1993, buying and selling machined parts. Not long afterward, we visited a small machine shop. It was my first trip to a shop, and I was hooked.
The shop had several Bridgeports, Monarchs and LeBlonds, all of which were manufactured in the 1940s and ’50s. A few graybeard craftsmen with scales in their pockets turned dials, read indicators and manufactured parts without computers. Since then, I have been enamored with craftsmanship and have admired the skill of well-seasoned machinists and toolmakers.
Advances in machine tools, cutting tools and manufacturing processes are inevitable and necessary to ensure we remain productive, but they cannot replace the skill of craftspeople or replace processes fundamental to manufacturing. That is why I become frustrated reading articles that talk about dying crafts or predict obsolescence of old-school methods.
I recently read a story about a small broach manufacturer whose owner was concerned that other technologies eventually would make broaching obsolete. Impossible. Broaching is one of the most productive metal removal processes available to manufacturers regardless of size.
Automotive manufacturing relies heavily on broaching technologies to deliver low-cost, accurate parts like gear racks, internal splines and other complex internal shapes. Gas turbines and aerospace engine components depend on broaching for complicated internal shapes with close tolerances and fine surface finishes. Firearms makers utilize broaching technology to generate barrel rifling. Even small tool shops use inexpensive broach tools to create internal keyways and hexagonal and square holes in parts.
Broaching has four advantages that protect it from obsolescence: speed, stability, accuracy and versatility.
The cutting speed of traditional broaching operations is around 762 mm/min. (30 ipm), whereas the surface speed of other processes, such as milling, can be several hundred inches per minute, making broaching appear slower. When judged on surface speed alone, broaching is slower. However, when compared with milling, for example, broach tooling does not need separate roughing and finishing passes. Accurately milling complex geometries often involves changing from a roughing tool to a finishing tool and making finish passes with low chip loads to achieve size and finish requirements. A broach tool is made so its finishing portion has the optimum number of cutting edges and spacing to produce the required finish. No tool change is necessary.
Milling tools also require constant adjustment to maintain desired geometry. And when they are sharpened, the diameter changes, which forces adjustments. Broach tools are capable of repeated sharpening before modification is needed to maintain geometric requirements. Broaching also spreads work over a larger number of cutting edges, which greatly increases the number of parts that can be machined before the tools must be changed.
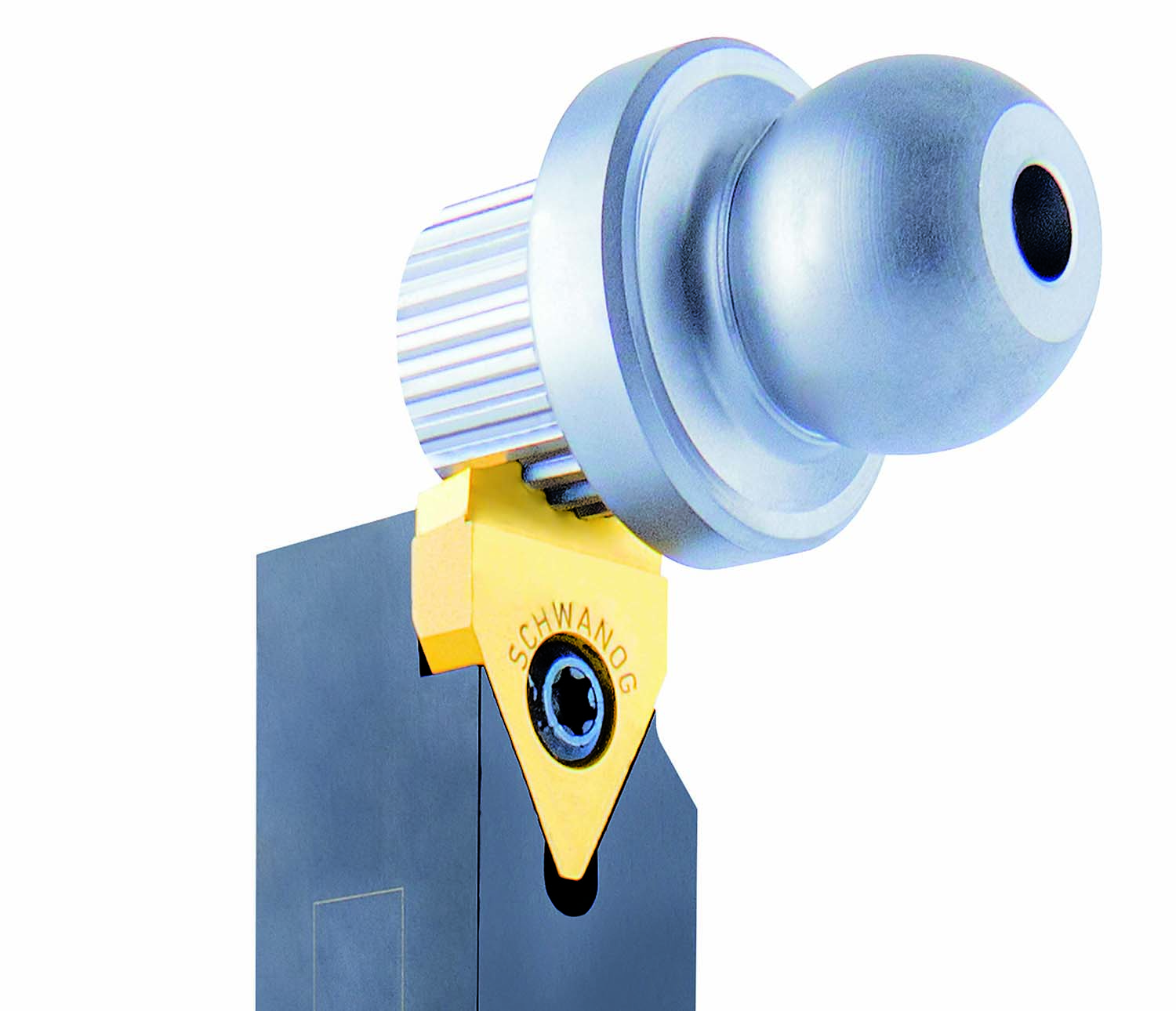
Those same attributes make broaching a stable process. Once set, a broach will deliver very accurate parts for a long time with no adjustments. Broaching processes like those found in automotive and aerospace applications require little or no operator intervention. Gear racks for power steering gears are a good example. A rack can be produced in less than a minute with part-to-part consistency in the 0.0127 mm (0.0005") range. A set of broach tools can produce 5,000 racks (about five days’ worth of production) before sharpening is needed. No other machining operation can boast that kind of capability.
Broaching operations are also less susceptible to system inaccuracies. When milling complex shapes, the state of a machine tool can affect accuracy. Other processes, such as milling and electrical discharge machining, require the machine tool to change direction while generating complicated geometries, thereby making part geometry contingent on the accuracy of the machine or program. Broach tools always travel in a straight line with no directional changes, minimizing the effects of machine tool condition. Unlike milling tools, broach tools are captured by the workpiece. Broach tools also are self-supporting in the cut. Therefore, they are not subject to error from spindle runout, and they resist the effects of machine tool deflection.
Broaching is versatile too. It can create very complex shapes, such as splines, gear teeth and turbine blade interfaces. Broaching also can be used to generate flat surfaces better than milling and faster than grinding. Milling cutters never are presented to the work surface with perfect perpendicularity, so a milled surface is never flat. There is always some concavity, which is why surface grinding is needed to produce flat surfaces after milling. Slab broaching is an alternative that is faster and produces a much flatter surface that can eliminate secondary processes like grinding.
Broaching does not always require a broach machine. The most common broach tools are push broaches used to create square and hexagonal holes and internal keyways. Because the tools are self-supporting, a simple hand-operated arbor press can be used to push the broach through the workpiece. These tools also improve productivity by removing work from a machining center, allowing a machinist to complete the broaching operation while another part is in the machine.
In other cases, special rotary broach tools can be used inside a machining center or lathe. These tools allow the creation of internal polygonal shapes like those on socket head screws or Torx screws while the machine operates. The broach is held in a special holder that enables the broach to rotate at the same speed as the part, and the machine simply pushes the broach forward to create the shape. Many different broach tools are available for modern CNC machines that permit unattended operation of machines and eliminate the need for secondary broaching.
Broaching is a fundamental machining operation for machine shops of all sizes. It is still a critical process for high-volume automotive manufacturers and makers of complex turbine components. It likewise will remain a common operation at maintenance shops when internal keyways or polygonal shapes are needed for repairs. There are no indications that broaching will become obsolete.
Related Glossary Terms
- arbor
arbor
Shaft used for rotary support in machining applications. In grinding, the spindle for mounting the wheel; in milling and other cutting operations, the shaft for mounting the cutter.
- broach
broach
Tapered tool, with a series of teeth of increasing length, that is pushed or pulled into a workpiece, successively removing small amounts of metal to enlarge a hole, slot or other opening to final size.
- broaching
broaching
Operation in which a cutter progressively enlarges a slot or hole or shapes a workpiece exterior. Low teeth start the cut, intermediate teeth remove the majority of the material and high teeth finish the task. Broaching can be a one-step operation, as opposed to milling and slotting, which require repeated passes. Typically, however, broaching also involves multiple passes.
- computer numerical control ( CNC)
computer numerical control ( CNC)
Microprocessor-based controller dedicated to a machine tool that permits the creation or modification of parts. Programmed numerical control activates the machine’s servos and spindle drives and controls the various machining operations. See DNC, direct numerical control; NC, numerical control.
- cutting speed
cutting speed
Tangential velocity on the surface of the tool or workpiece at the cutting interface. The formula for cutting speed (sfm) is tool diameter 5 0.26 5 spindle speed (rpm). The formula for feed per tooth (fpt) is table feed (ipm)/number of flutes/spindle speed (rpm). The formula for spindle speed (rpm) is cutting speed (sfm) 5 3.82/tool diameter. The formula for table feed (ipm) is feed per tooth (ftp) 5 number of tool flutes 5 spindle speed (rpm).
- finishing tool
finishing tool
Tool, belt, wheel or other cutting implement that completes the final, precision machining step/cut on a workpiece. Often takes the form of a grinding, honing, lapping or polishing tool. See roughing cutter.
- flat ( screw flat)
flat ( screw flat)
Flat surface machined into the shank of a cutting tool for enhanced holding of the tool.
- gang cutting ( milling)
gang cutting ( milling)
Machining with several cutters mounted on a single arbor, generally for simultaneous cutting.
- grinding
grinding
Machining operation in which material is removed from the workpiece by a powered abrasive wheel, stone, belt, paste, sheet, compound, slurry, etc. Takes various forms: surface grinding (creates flat and/or squared surfaces); cylindrical grinding (for external cylindrical and tapered shapes, fillets, undercuts, etc.); centerless grinding; chamfering; thread and form grinding; tool and cutter grinding; offhand grinding; lapping and polishing (grinding with extremely fine grits to create ultrasmooth surfaces); honing; and disc grinding.
- inches per minute ( ipm)
inches per minute ( ipm)
Value that refers to how far the workpiece or cutter advances linearly in 1 minute, defined as: ipm = ipt 5 number of effective teeth 5 rpm. Also known as the table feed or machine feed.
- lathe
lathe
Turning machine capable of sawing, milling, grinding, gear-cutting, drilling, reaming, boring, threading, facing, chamfering, grooving, knurling, spinning, parting, necking, taper-cutting, and cam- and eccentric-cutting, as well as step- and straight-turning. Comes in a variety of forms, ranging from manual to semiautomatic to fully automatic, with major types being engine lathes, turning and contouring lathes, turret lathes and numerical-control lathes. The engine lathe consists of a headstock and spindle, tailstock, bed, carriage (complete with apron) and cross slides. Features include gear- (speed) and feed-selector levers, toolpost, compound rest, lead screw and reversing lead screw, threading dial and rapid-traverse lever. Special lathe types include through-the-spindle, camshaft and crankshaft, brake drum and rotor, spinning and gun-barrel machines. Toolroom and bench lathes are used for precision work; the former for tool-and-die work and similar tasks, the latter for small workpieces (instruments, watches), normally without a power feed. Models are typically designated according to their “swing,” or the largest-diameter workpiece that can be rotated; bed length, or the distance between centers; and horsepower generated. See turning machine.
- machining center
machining center
CNC machine tool capable of drilling, reaming, tapping, milling and boring. Normally comes with an automatic toolchanger. See automatic toolchanger.
- milling
milling
Machining operation in which metal or other material is removed by applying power to a rotating cutter. In vertical milling, the cutting tool is mounted vertically on the spindle. In horizontal milling, the cutting tool is mounted horizontally, either directly on the spindle or on an arbor. Horizontal milling is further broken down into conventional milling, where the cutter rotates opposite the direction of feed, or “up” into the workpiece; and climb milling, where the cutter rotates in the direction of feed, or “down” into the workpiece. Milling operations include plane or surface milling, endmilling, facemilling, angle milling, form milling and profiling.
- surface grinding
surface grinding
Machining of a flat, angled or contoured surface by passing a workpiece beneath a grinding wheel in a plane parallel to the grinding wheel spindle. See grinding.