I usually make a small number of parts per order, often one or two. My main customer is a builder of industrial machinery. I have made parts for their machines since 1995. Over the years they have built a great variety of machines and I have made thousands of different parts for those machines. Many of their machines are in operation after decades of use. If somebody out in the field calls my customer for a repair part, my customer calls me. Then I look in my files, find the drawing of the needed part, look for any notes or CNC program I used before, and then make the part again.
Recently, my customer presented me with a very different situation. They have a family of machines that use a part that might be called a consumable. The part is a knife made of A2 tool steel that is used to cut cardboard and eventually wears. This was a high-volume job for me and required a different strategy than I normally use. One of the features on the part is a deep slot with a full radius bottom and a specific width. The volume and geometry of the slot called for an indexable insert slotting cutter. A problem arose because the radius of the slot was not available with off-the-shelf inserts.
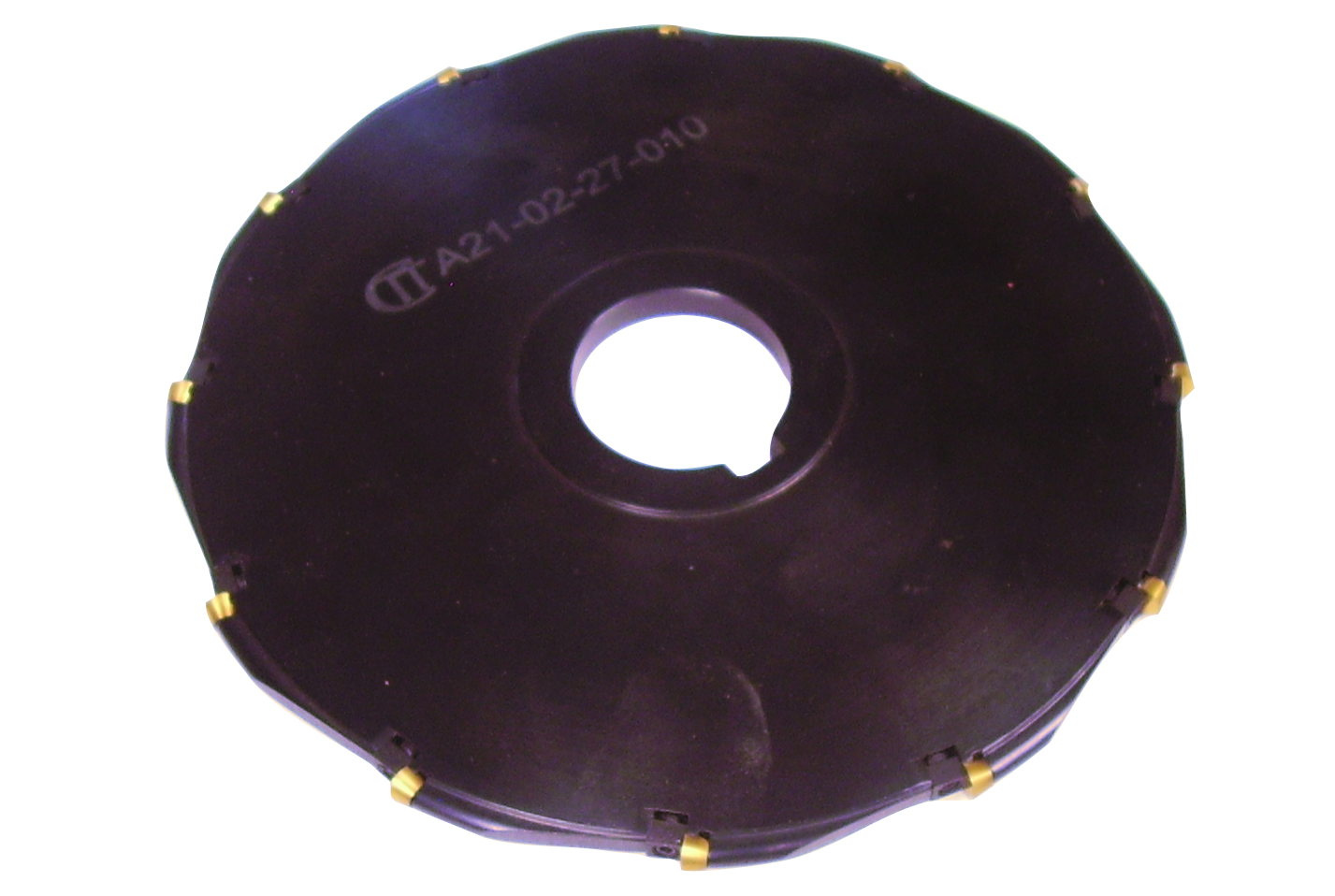
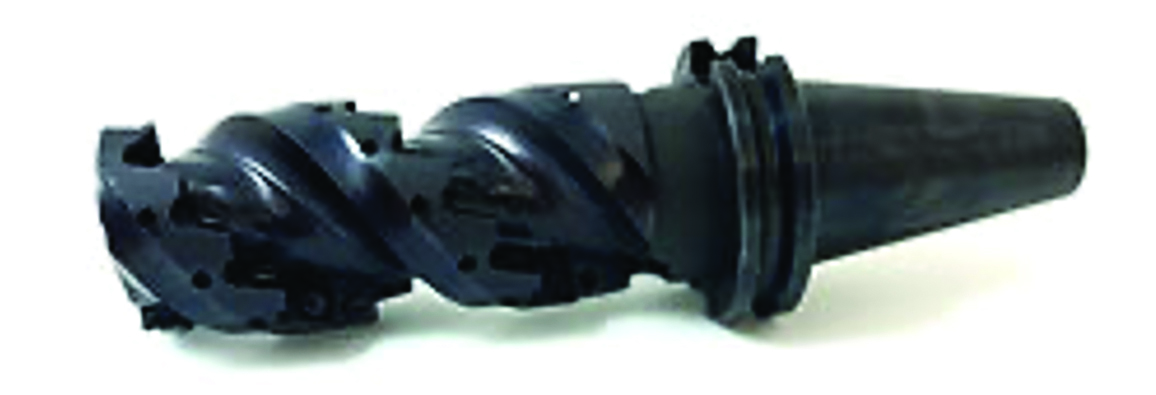
I found my solution at Cutting Tool Technologies Inc. in Wilton, New Hampshire. They make an array of standard indexable tools for slotting, as well as endmills, chamfer mills, radius cutters, turning tools, indexable broaches and others. They also make custom indexable tools. I called and talked to an engineer at CTT and explained my problem. The CTT people came up with a cutter design. I didn’t have to provide a drawing because they understood what I was talking about. Their design for my application uses an insert with a custom geometry so the slot could be finished in one pass. They made a slotting cutter with pockets to fit the custom insert. I got a quality tool at a reasonable price in two months. It all worked well.
Figure one shows the tool that CTT made for me. It is a 6" -dia. cutter with a 11/4-dia. hole to mount on an arbor. The pockets mount 12 round, 0.219" -dia. inserts with a positive rake angle. The carbide inserts have a titanium nitride coating.
They also make more complex specials than the one I got. Figure two shows an example of what they can do. It’s a muti-insert indexable endmill with an integral V-flange shank. It’s a tool designed to minimize tool deflection and maximize metal removal in a production environment. If you have an idea for a tool you need, a sketch or engineered drawing can be useful but is not necessary. Smart people working together makes work go smoothly.
Related Glossary Terms
- arbor
arbor
Shaft used for rotary support in machining applications. In grinding, the spindle for mounting the wheel; in milling and other cutting operations, the shaft for mounting the cutter.
- computer numerical control ( CNC)
computer numerical control ( CNC)
Microprocessor-based controller dedicated to a machine tool that permits the creation or modification of parts. Programmed numerical control activates the machine’s servos and spindle drives and controls the various machining operations. See DNC, direct numerical control; NC, numerical control.
- endmill
endmill
Milling cutter held by its shank that cuts on its periphery and, if so configured, on its free end. Takes a variety of shapes (single- and double-end, roughing, ballnose and cup-end) and sizes (stub, medium, long and extra-long). Also comes with differing numbers of flutes.
- indexable insert
indexable insert
Replaceable tool that clamps into a tool body, drill, mill or other cutter body designed to accommodate inserts. Most inserts are made of cemented carbide. Often they are coated with a hard material. Other insert materials are ceramic, cermet, polycrystalline cubic boron nitride and polycrystalline diamond. The insert is used until dull, then indexed, or turned, to expose a fresh cutting edge. When the entire insert is dull, it is usually discarded. Some inserts can be resharpened.
- rake
rake
Angle of inclination between the face of the cutting tool and the workpiece. If the face of the tool lies in a plane through the axis of the workpiece, the tool is said to have a neutral, or zero, rake. If the inclination of the tool face makes the cutting edge more acute than when the rake angle is zero, the rake is positive. If the inclination of the tool face makes the cutting edge less acute or more blunt than when the rake angle is zero, the rake is negative.
- shank
shank
Main body of a tool; the portion of a drill or similar end-held tool that fits into a collet, chuck or similar mounting device.
- slotting
slotting
Machining, normally milling, that creates slots, grooves and similar recesses in workpieces, including T-slots and dovetails.
- titanium nitride ( TiN)
titanium nitride ( TiN)
Added to titanium-carbide tooling to permit machining of hard metals at high speeds. Also used as a tool coating. See coated tools.
- turning
turning
Workpiece is held in a chuck, mounted on a face plate or secured between centers and rotated while a cutting tool, normally a single-point tool, is fed into it along its periphery or across its end or face. Takes the form of straight turning (cutting along the periphery of the workpiece); taper turning (creating a taper); step turning (turning different-size diameters on the same work); chamfering (beveling an edge or shoulder); facing (cutting on an end); turning threads (usually external but can be internal); roughing (high-volume metal removal); and finishing (final light cuts). Performed on lathes, turning centers, chucking machines, automatic screw machines and similar machines.