Whether you are grinding HSS or Tungsten Carbide, the flute grinding process is the most difficult feature to grind in round tool manufacturing. Though there are many reasons why, the main reason is that this operation is where most material is being removed from the tool, introducing the most heat and spindle load. There are several techniques that can be used to allow the grinding wheel to perform this operation more effectively. Before these techniques can be applied, understanding the concept of contact surface area and how it relates to force per grit is very important. From a microscopic perspective, a grinding wheel consists of thousands of cutting points. The more of these cutting points in contact with the part being ground, the more the work being done is “shared.” This allows each cutting point to remove smaller chips. As the surface area increases, this will decrease the force being done per grit, and allow the abrasive to continue working until dulling, or abrasive “pull out” occurs. A reduction in chip size will also produce a finer work piece surface finish and will cause the grinding wheel to act harder.
![]() |
![]() |
Since the grinding wheel peripheral speed directly affects the number of cutting points in contact with the work piece, a higher wheel speed will decrease the chip thickness, thus reducing the force/grit and causing the wheel to “act” harder. Lowering the wheel speed will have the adverse effect. Another method of lowering the force/grit is through abrasive concentration. Higher abrasive concentration adds more cutting points to the grinding process and would also provide better finishes and cause the wheel to act harder. Lowering the concentration will have the adverse effect.
![]() |
Another way to increase the effectiveness of the flute grinding process is to understand how the approach angle, or “Sku” angle, affects both the grinding wheel and tool being ground and the shape of grinding wheel. In general, an angled fluting wheel will grind with less spindle load than a straight faced wheel. The angled face tends help the wheel penetrate the work material more easily and creates less plowing. In Figure 1 courtesy of Walter United Grinding using Tool Studio shows where the energy is being applied on both the tool and the grinding wheel.
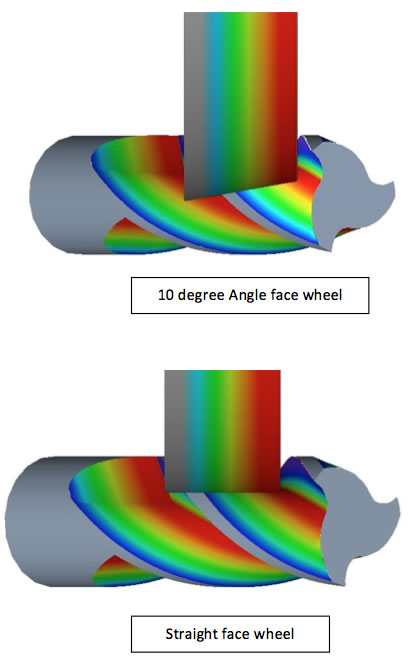
Figure 1
In the manufacturing of drills, the flute grinding process is much different than on end mills. The contact area is higher and the force/grit is much higher. There are two methods companies use to flute these tools. Method 1 utilizes straight faced wheels as this greatly reduces the amount of grinding wheel inventory used for many sized tools. However, this method tends to create high machine load and wheel wear. Most of the work being done is at the leading edge of the wheel as depicted in figure 2. Another drawback using this method is since the wheel travels below the tool, companies cannot use steady rests to help with deflection. (See figure 3).
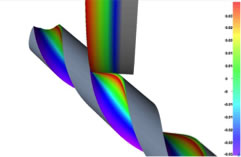
Figure 2
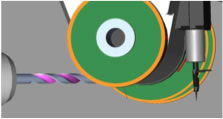
Figure 3
The other method of flute grinding drills is using full radius or gothic radius wheels. This allows stock removal to take place across the full width of the wheel thus maximizing wheel life. (See figure 4)
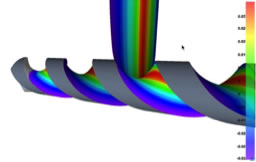
Figure 4
However this method requires the width of the grinding wheel to be very specific to the size of the drill being ground and will require many different wheel widths to accommodate different drill sizes. Because the shape of the wheel is producing the shape of the flute and not relying on the machine to generate the same geometry using severe axis repositioning as with the first method, it allows for very uniform temperature distribution and allows the use of steady rest for long flute grinding and minimize deflection. (See figure 5)
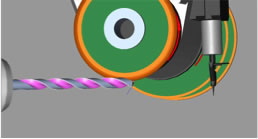
Figure 5
Related Glossary Terms
- abrasive
abrasive
Substance used for grinding, honing, lapping, superfinishing and polishing. Examples include garnet, emery, corundum, silicon carbide, cubic boron nitride and diamond in various grit sizes.
- approach angle
approach angle
Angle between the insert’s side-cutting edge and the line perpendicular to the milling cutter’s axis of rotation. Approach angle, which is also known as cutting edge angle, is used with metric units of measurement. See lead angle.
- fluting
fluting
Cutting straight or spiral grooves in drills, endmills, reamers and taps to improve cutting action and remove chips.
- grinding
grinding
Machining operation in which material is removed from the workpiece by a powered abrasive wheel, stone, belt, paste, sheet, compound, slurry, etc. Takes various forms: surface grinding (creates flat and/or squared surfaces); cylindrical grinding (for external cylindrical and tapered shapes, fillets, undercuts, etc.); centerless grinding; chamfering; thread and form grinding; tool and cutter grinding; offhand grinding; lapping and polishing (grinding with extremely fine grits to create ultrasmooth surfaces); honing; and disc grinding.
- grinding wheel
grinding wheel
Wheel formed from abrasive material mixed in a suitable matrix. Takes a variety of shapes but falls into two basic categories: one that cuts on its periphery, as in reciprocating grinding, and one that cuts on its side or face, as in tool and cutter grinding.
- high-speed steels ( HSS)
high-speed steels ( HSS)
Available in two major types: tungsten high-speed steels (designated by letter T having tungsten as the principal alloying element) and molybdenum high-speed steels (designated by letter M having molybdenum as the principal alloying element). The type T high-speed steels containing cobalt have higher wear resistance and greater red (hot) hardness, withstanding cutting temperature up to 1,100º F (590º C). The type T steels are used to fabricate metalcutting tools (milling cutters, drills, reamers and taps), woodworking tools, various types of punches and dies, ball and roller bearings. The type M steels are used for cutting tools and various types of dies.
- steady rest
steady rest
Supports long, thin or flexible work being turned on a lathe. Mounts on the bed’s ways and, unlike a follower rest, remains at the point where mounted. See follower rest.
- tungsten carbide ( WC)
tungsten carbide ( WC)
Intermetallic compound consisting of equal parts, by atomic weight, of tungsten and carbon. Sometimes tungsten carbide is used in reference to the cemented tungsten carbide material with cobalt added and/or with titanium carbide or tantalum carbide added. Thus, the tungsten carbide may be used to refer to pure tungsten carbide as well as co-bonded tungsten carbide, which may or may not contain added titanium carbide and/or tantalum carbide.
Paul Ehrlich, who co-authored this report, is Sr. Application Engineer at Walter United Grinding.