Similar to cutting tool technology leapfrogging machine tool technology and vice versa, grinding wheels can trail the capabilities of grinding machines before gaining ground. To keep pace with grinder technology, Norton/Saint-Gobain has developed the Norton-brand Vitrium3 grinding wheel.
The core of the technology is the wheel’s glass, or vitrified, bond, which is the company’s strongest, according to Jim Gaffney, senior product manager for Norton/Saint-Gobain. “We’re trying to stay in step with or be ahead of the machine builders,” he said, noting the wheel is suitable for grinders with spindle speeds up to 80 m/sec.
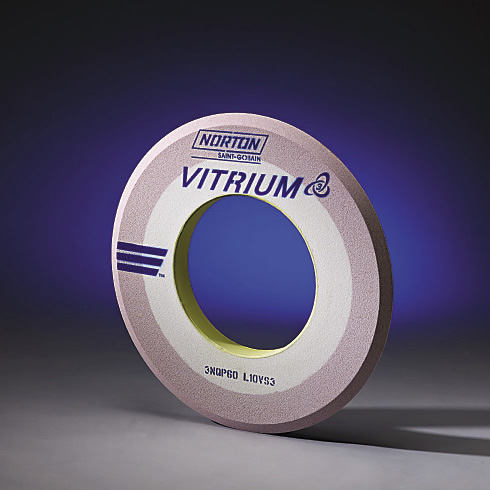
The Norton Vitrium3 grinding wheel features a strong glass bond to enhance grinding efficiency.
The strength of the glass enables the company to produce wheels with less of it than previous offerings while still maintaining grain adhesion, Gaffney noted. The grain type ranges from conventional aluminum oxide to Norton Quantum ceramic alumina, depending on the application.
He explained that the lower bond-to-abrasive ratio, or having less glass, improves coolant flow, opens the wheel’s porosity and increases exposure of the abrasive grains to enable the wheel to more efficiently discharge swarf and grind at a higher metal-removal rate. The increased grain exposure also reduces grinding forces up to 25 percent, which minimizes part deflection and grinding burn, Gaffney added. This is especially critical when grinding heat-sensitive materials, such as nickel-based superalloys, tool steels and chromium molybdenum. Applications for the wheel include grinding automotive crankshafts and camshafts and jet engine vanes and turbine blades.
In addition to grinding more efficiently, the Vitrium3 wheel’s stronger bond increases wheel life compared to conventional bonds, Gaffney said. “Just by changing the glass, we’re seeing about a 30 percent improvement in wheel life.”
He added that it took the company about 3 years to develop the wheel and bring it to market, with a formal launch scheduled for May.
For more information, contact Norton/Saint-Gobain, Worcester, Mass., at (508) 795-2183 or visit www.nortonindustrial.com.
Related Glossary Terms
- abrasive
abrasive
Substance used for grinding, honing, lapping, superfinishing and polishing. Examples include garnet, emery, corundum, silicon carbide, cubic boron nitride and diamond in various grit sizes.
- aluminum oxide
aluminum oxide
Aluminum oxide, also known as corundum, is used in grinding wheels. The chemical formula is Al2O3. Aluminum oxide is the base for ceramics, which are used in cutting tools for high-speed machining with light chip removal. Aluminum oxide is widely used as coating material applied to carbide substrates by chemical vapor deposition. Coated carbide inserts with Al2O3 layers withstand high cutting speeds, as well as abrasive and crater wear.
- coolant
coolant
Fluid that reduces temperature buildup at the tool/workpiece interface during machining. Normally takes the form of a liquid such as soluble or chemical mixtures (semisynthetic, synthetic) but can be pressurized air or other gas. Because of water’s ability to absorb great quantities of heat, it is widely used as a coolant and vehicle for various cutting compounds, with the water-to-compound ratio varying with the machining task. See cutting fluid; semisynthetic cutting fluid; soluble-oil cutting fluid; synthetic cutting fluid.
- grinding
grinding
Machining operation in which material is removed from the workpiece by a powered abrasive wheel, stone, belt, paste, sheet, compound, slurry, etc. Takes various forms: surface grinding (creates flat and/or squared surfaces); cylindrical grinding (for external cylindrical and tapered shapes, fillets, undercuts, etc.); centerless grinding; chamfering; thread and form grinding; tool and cutter grinding; offhand grinding; lapping and polishing (grinding with extremely fine grits to create ultrasmooth surfaces); honing; and disc grinding.
- grinding wheel
grinding wheel
Wheel formed from abrasive material mixed in a suitable matrix. Takes a variety of shapes but falls into two basic categories: one that cuts on its periphery, as in reciprocating grinding, and one that cuts on its side or face, as in tool and cutter grinding.
- metal-removal rate
metal-removal rate
Rate at which metal is removed from an unfinished part, measured in cubic inches or cubic centimeters per minute.
- superalloys
superalloys
Tough, difficult-to-machine alloys; includes Hastelloy, Inconel and Monel. Many are nickel-base metals.
- swarf
swarf
Metal fines and grinding wheel particles generated during grinding.
- tool steels
tool steels
Group of alloy steels which, after proper heat treatment, provide the combination of properties required for cutting tool and die applications. The American Iron and Steel Institute divides tool steels into six major categories: water hardening, shock resisting, cold work, hot work, special purpose and high speed.