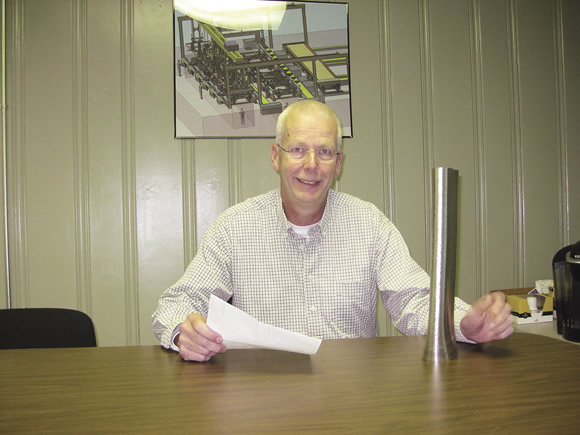
All images courtesy Chesterfield Tool
Greg Julian, vice president of technical operations at Chesterfield Tool and Engineering.
Many employees dream about being their own boss and setting their own hours. For Greg Julian, vice president of technical operations at Chesterfield Tool and Engineering Inc., and Rick Ray, president, the desire to spend more time with their families led them to follow that dream. The two worked together as toolmakers at a large job shop and wished to own and run an employee-friendly shop. They wanted to create an atmosphere that enabled employees to have more family time, such as getting time off to attend a child’s school play.
The toolmakers and their wives, Luanne Julian and Nichola Ray, purchased Chesterfield Tool in 1989. The company was established in 1960 as a small job shop in Chesterfield, Ind., but was later moved to Daleville, Ind., where it retained the Chesterfield name.
Chesterfield Tool specializes in designing and building custom machines and tooling, trepanning, honing, gundrilling and remanufacturing hydraulic cylinders. Its clientele varies from small machine shops to Fortune 500 companies and their overseas subsidiaries.
Yesenia Salcedo, senior editor of CTE, checked in with Greg Julian to see how the company manages to be profitable and create jobs.
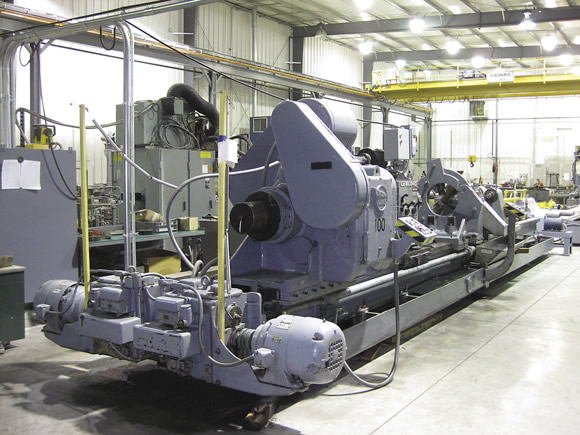
Chesterfield Tool uses this gundrilling and deep-hole boring machine renovated with a high-speed gearbox to drill small-diameter holes.
CTE: How has your team kept Chesterfield Tool successful for more than 20 years?
Julian: Diversification. We followed the compass toward the needs of the industry. For example, when the opportunity came along to make large, precision shafts for a client, we invested in a large CNC lathe and large manual OD grinder, knowing our client had trouble finding vendors capable of making these parts to their close tolerance requirements. The client said this work could only be done on an expensive CNC grinder. We begged to differ. Also, when a local honing company closed, we purchased its equipment and added contract honing. Chesterfield did not have previous honing experience, so we hired a technician. From this acquisition, we branched off into repairing and remanufacturing commercial hydraulic cylinders.
CTE: How do you keep adding jobs in this economy?
Julian: When we bought the company, it consisted of a 4,000-sq.-ft. building with a few pieces of machinery and no employees. We now have 48,000 sq. ft. with all work areas under an overhead crane. Our number of employees stayed consistent through the recent recession until December 2011, at which time we added seven employees, increasing employment by 25 percent. The demise of a few tool shops around the area has allowed us to pick up new work and hire some of their people. One of our secrets to success is having larger equipment and more equipment than is typical for a machine shop of our size.
CTE: What kinds of large equipment?
Julian: Our lineup includes two boring mills with 20 ' of travel, five honing machines from 2.5 " to 18 " ID and up to 24 ' in length, and a very large trepanning and gundrilling machine. We continue to add additional equipment and recently bought a heavy-duty TOS lathe, which will help us work on large shafts. It handles work from 33 " in diameter and 140 " between centers. We have found we can process more shafts if we “take the bark off” prior to CNC lathe profiling. However, to do this we needed a larger lathe, one stout enough for continuous duty, and the TOS lathe fit the bill.
CTE: So adding more machines led to hiring more employees?
Julian: Yes. We recently diversified into another business segment: building our own machining cells for short-run production. This allowed us to run the machines with fewer employees. Increased business allowed us to add more employees, but not as many as we would have if we didn’t have the machining cells. Wouldn’t it be great if it took only half your workforce to run your daily production? Well, in essence, that is what we oftentimes do with the layout of our CNC milling machines. This is a newly implemented secret of operating efficiently. When one operator runs one machine, all of the labor cost is directed to the single part being machined. When the operator runs two machines, at least one of the machines is running without an operator. This allows you to split the operator’s cost over two machines or by the number of parts per process.
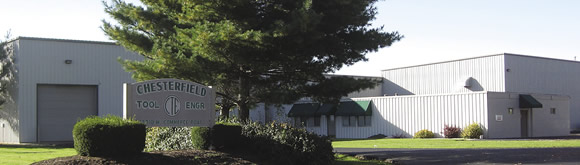
Chesterfield Tool specializes in designing and building custom machines and tooling, trepanning, honing, gundrilling and remanufacturing hydraulic cylinders.
There are two attributes that come out of this practice: You can lower your operating costs, and you can run twice the amount of labor through each operator. The machining cells aid us in getting our costs down. We are now a low-cost solution for machined parts. On some machine building RFQs, we have been asked to buy parts from China, for example, to help keep our selling price competitive. We can compete on this global level of cost, yet make the parts in the U.S.A. Further, because we are running twice the number of parts through the machines, our delivery times are shrinking. Low cost plus quick turnaround equals happy clients.
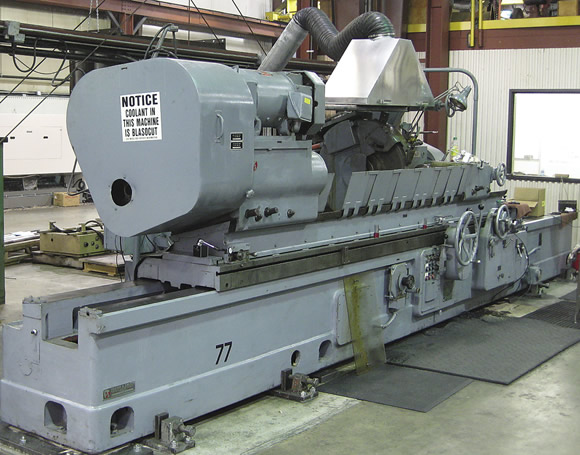
Chesterfield Tool grinds shafts from 5 " to 8 " in length with a 0.0002 " tolerance on this OD grinder.
CTE: What makes Chesterfield Tool a solutions-oriented company that tackles jobs other shops won’t?
Julian: We are skilled toolmakers and problem solvers. Many times we are asked to make new or reproduce one-of-a-kind parts. Having skilled toolmakers and manually operated equipment is still the best and most cost-effective way to make such parts. We do not produce a product and attempt to sell it. We are approached by customers who have a specific need for a product that no one has ever designed or built a machine before for their process. It’s nice to know that in these times of everything leaving the country, we are still able to produce something of value the rest of the world doesn’t have. If we’re going to be competitive in the U.S. and world markets, we have to continue to work smarter and be the vanguards of innovation and ingenuity. CTE
Related Glossary Terms
- boring
boring
Enlarging a hole that already has been drilled or cored. Generally, it is an operation of truing the previously drilled hole with a single-point, lathe-type tool. Boring is essentially internal turning, in that usually a single-point cutting tool forms the internal shape. Some tools are available with two cutting edges to balance cutting forces.
- boring machine
boring machine
Similar to a turning machine except that the cutting tool (single-point or multiple-cutting-edge), rather than the workpiece, rotates to perform internal cuts. However, boring can be accomplished by holding the tool stationary and turning the workpiece. Takes a variety of vertical, slanted and horizontal forms, and has one or more spindles. Typically a large, powerful machine, it can readily hold tolerances to 0.0001". See jig boring; lathe; turning machine.
- centers
centers
Cone-shaped pins that support a workpiece by one or two ends during machining. The centers fit into holes drilled in the workpiece ends. Centers that turn with the workpiece are called “live” centers; those that do not are called “dead” centers.
- computer numerical control ( CNC)
computer numerical control ( CNC)
Microprocessor-based controller dedicated to a machine tool that permits the creation or modification of parts. Programmed numerical control activates the machine’s servos and spindle drives and controls the various machining operations. See DNC, direct numerical control; NC, numerical control.
- gang cutting ( milling)
gang cutting ( milling)
Machining with several cutters mounted on a single arbor, generally for simultaneous cutting.
- gundrilling
gundrilling
Drilling process using a self-guiding tool to produce deep, precise holes. High-pressure coolant is fed to the cutting area, usually through the gundrill’s shank.
- inner diameter ( ID)
inner diameter ( ID)
Dimension that defines the inside diameter of a cavity or hole. See OD, outer diameter.
- lathe
lathe
Turning machine capable of sawing, milling, grinding, gear-cutting, drilling, reaming, boring, threading, facing, chamfering, grooving, knurling, spinning, parting, necking, taper-cutting, and cam- and eccentric-cutting, as well as step- and straight-turning. Comes in a variety of forms, ranging from manual to semiautomatic to fully automatic, with major types being engine lathes, turning and contouring lathes, turret lathes and numerical-control lathes. The engine lathe consists of a headstock and spindle, tailstock, bed, carriage (complete with apron) and cross slides. Features include gear- (speed) and feed-selector levers, toolpost, compound rest, lead screw and reversing lead screw, threading dial and rapid-traverse lever. Special lathe types include through-the-spindle, camshaft and crankshaft, brake drum and rotor, spinning and gun-barrel machines. Toolroom and bench lathes are used for precision work; the former for tool-and-die work and similar tasks, the latter for small workpieces (instruments, watches), normally without a power feed. Models are typically designated according to their “swing,” or the largest-diameter workpiece that can be rotated; bed length, or the distance between centers; and horsepower generated. See turning machine.
- milling
milling
Machining operation in which metal or other material is removed by applying power to a rotating cutter. In vertical milling, the cutting tool is mounted vertically on the spindle. In horizontal milling, the cutting tool is mounted horizontally, either directly on the spindle or on an arbor. Horizontal milling is further broken down into conventional milling, where the cutter rotates opposite the direction of feed, or “up” into the workpiece; and climb milling, where the cutter rotates in the direction of feed, or “down” into the workpiece. Milling operations include plane or surface milling, endmilling, facemilling, angle milling, form milling and profiling.
- outer diameter ( OD)
outer diameter ( OD)
Dimension that defines the exterior diameter of a cylindrical or round part. See ID, inner diameter.
- profiling
profiling
Machining vertical edges of workpieces having irregular contours; normally performed with an endmill in a vertical spindle on a milling machine or with a profiler, following a pattern. See mill, milling machine.
- tolerance
tolerance
Minimum and maximum amount a workpiece dimension is allowed to vary from a set standard and still be acceptable.
- trepanning
trepanning
Drilling deep holes that are too large to be drilled by high-pressure coolant drills or gundrills. Trepanning generates a solid core and normally requires a big, powerful machine. Shallow trepanning operations can be performed on modified engine or turret lathes or on boring machines. See boring; drilling; spade drilling.