Modern society has become reliant on connectivity. We have a continuous connection to each other and the devices we use, from phones and watches to refrigerators and washing machines. We live in a world that was a science fiction story 50 years ago.
By now, only those living under rocks or off the grid can deny knowing of the impending changes brought by the industrial Internet of Things. Commonly accepted as part of the Fourth Industrial Revolution, the IIoT is defined by the ability of devices to be linked across networks and in constant communication.
Our industrial community, though slowly catching up, is behind in the connectivity game. Even though we have the necessary infrastructure and a common desire to advance the connectedness of industrial environments, we struggle to proceed in the same way as broader society.
There are basic explanations for the lag, especially technological limitations. Industrial machines often are outdated compared with cellphones and computers. Consumers routinely trade 2- or 3-year-old phones for the newest technology while life spans of industrial machines frequently are measured in decades. Obviously, a machine manufactured in the 1990s does not have the hardware, software and computing horsepower to efficiently connect with the devices of today. Of course, a user can install aftermarket hardware to make connections, but the transfer of data and the overall interaction are not what we expect from a modern device.
Another barrier is the perceived value of interconnectedness. On paper, industrial leaders profess a desire to implement IIoT concepts, often expending resources to research and plan for transformation. However, many leaders do not fully understand the complexities and costs that come with this transition.
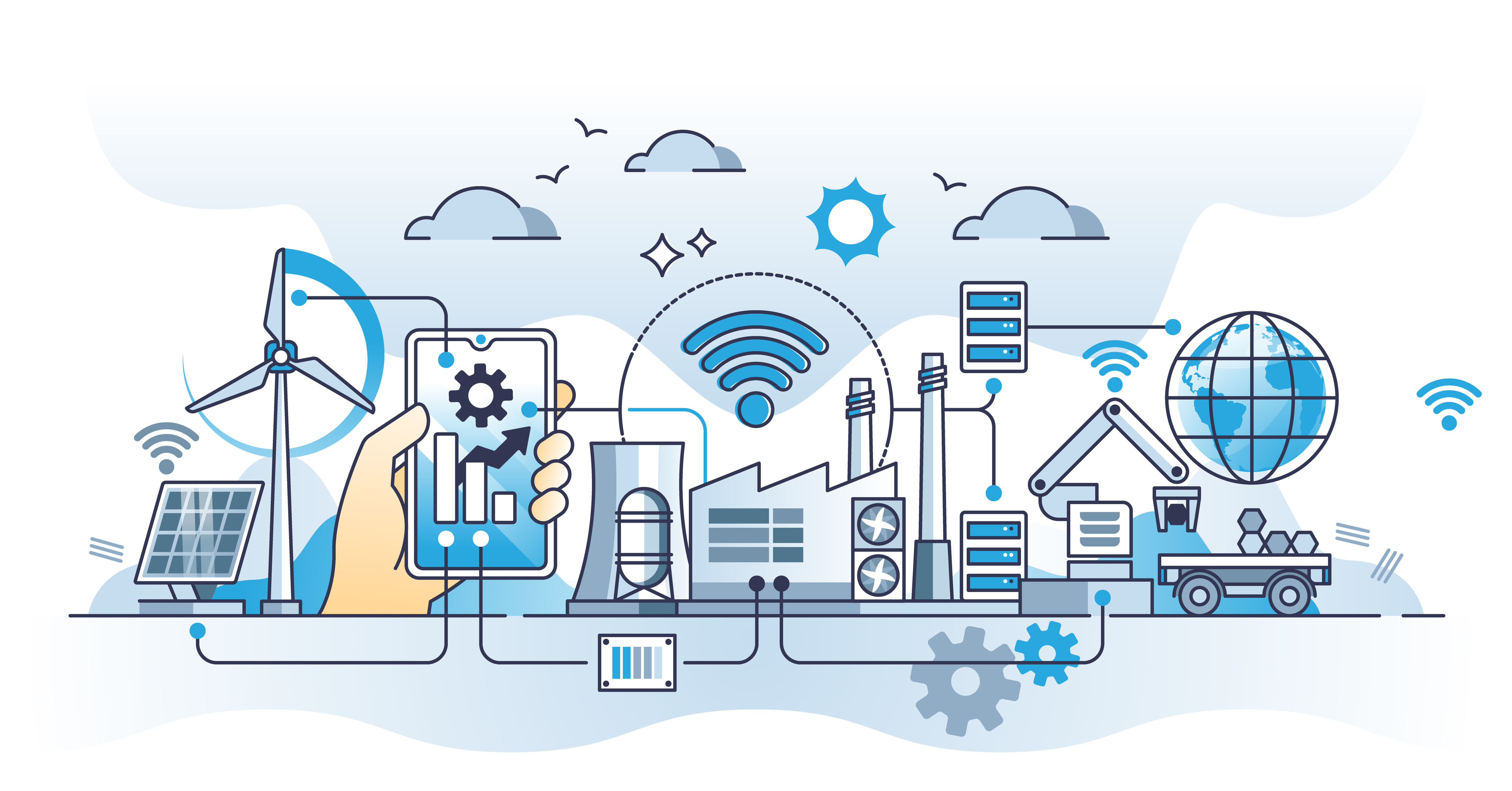
As manufacturing engineers, we are charged with improving safety, quality, delivery and cost. Each project is expected to have measurable improvement in those areas. New tools, machines and processes have very linear calculations that justify resources.
IIoT projects are not straightforward in their justification and regularly rely on an “If you build it, they will come” faith. Unfortunately, profit-and-loss owners generally do not share that faith as it is difficult to see how interconnectedness can improve key performance indicators. This reluctance manifests itself in the funding stage when projects usually stagnate or die.
IIoT projects often require the interaction of every department in an organization beyond the normal approval processes, such as those associated with the purchase of a machine tool. Reconstructing the IT infrastructure of a company can force departments to change processes, update equipment and endure transformational pain. These challenges may be so great that full commitment to change by all parties is impossible to achieve. Advancing this type of initiative demands significant effort for benefits not recognized until later.
It is difficult to achieve interdepartmental cooperation, but the IT community can be especially resistant because creating an IIoT environment places a tremendous burden on IT professionals. Building the infrastructure, writing code and testing during implementation are daunting at best. Supporting the resulting network necessitates additional resources from professionals who already are overburdened at many organizations. The extra security risks must be managed, and most IT departments are wary of adding industrial machines to networks due to those risks.
Will we see industry adopt the concepts and develop into functioning IIoT organizations? Yes, but the change will be slow and require evolution in a few areas.
As new machine tools and industrial devices are introduced, we see the necessary technology arriving on the market. CNCs, programmable logic controllers and similar hardware now have the foundational technology to function in an IIoT environment. Controls increasingly are PC-based, making them more readily connected. Wi-Fi capability and Bluetooth technology give new controls a platform that is familiar to the rest of society and facilitate easier machine-to-machine connections.
Makers of industrial machines and devices will be forced by hardware suppliers to adopt newer technologies. As hardware advances, outdated technologies often associated with industrial machines become obsolete without support. Historically, these conditions have forced the advancement of industrial devices.
The older generations are retiring or soon will be. People like me are a barrier to creating an IIoT environment. It is difficult for a person who started manufacturing without computer-aided machines and while answering a landline phone to appreciate the benefits of a connected factory. Because the value can be intangible or hard to calculate, some people recoil at the trials and tribulations of implementation. But industry will suffer if we fail to recognize that those coming behind us are accustomed to being connected, and talented young people will not be attracted to companies that do not advance.
Although evolution in the industrial sector will be slow, IIoT is no longer the future. It is here and will become a key component for successful industrial companies.