Lasers and ray guns have been part of our lexicon since H.G. Wells published “The War of the Worlds” in 1898. For the common person in the early part of the 20th century, lasers were tools of destruction in novels and movies. For scientists, lasers were an idea born from a concept put forth by Albert Einstein, who theorized that it was possible to emit light energy from excited atoms.
Drawing from Einstein’s theory, scientists experimented with various methods to generate a working device that would turn theory into reality. Around 1960, the first functional laser was demonstrated, and development accelerated from that point.
Lasers have become ubiquitous in 21st-century life, and this technology that once was confined to laboratory environments can be found on the shelf at the local dollar store. For industry, the development and use of laser technology has altered the metalworking landscape.
Laser technology and the physics needed to explain its operation are complex. For those of us who do not hold a graduate degree in physics, lasers are simply a source of heat that can be controlled with extreme precision. As a heat source, they can be applied in the same manner as other heat sources used in manufacturing processes.
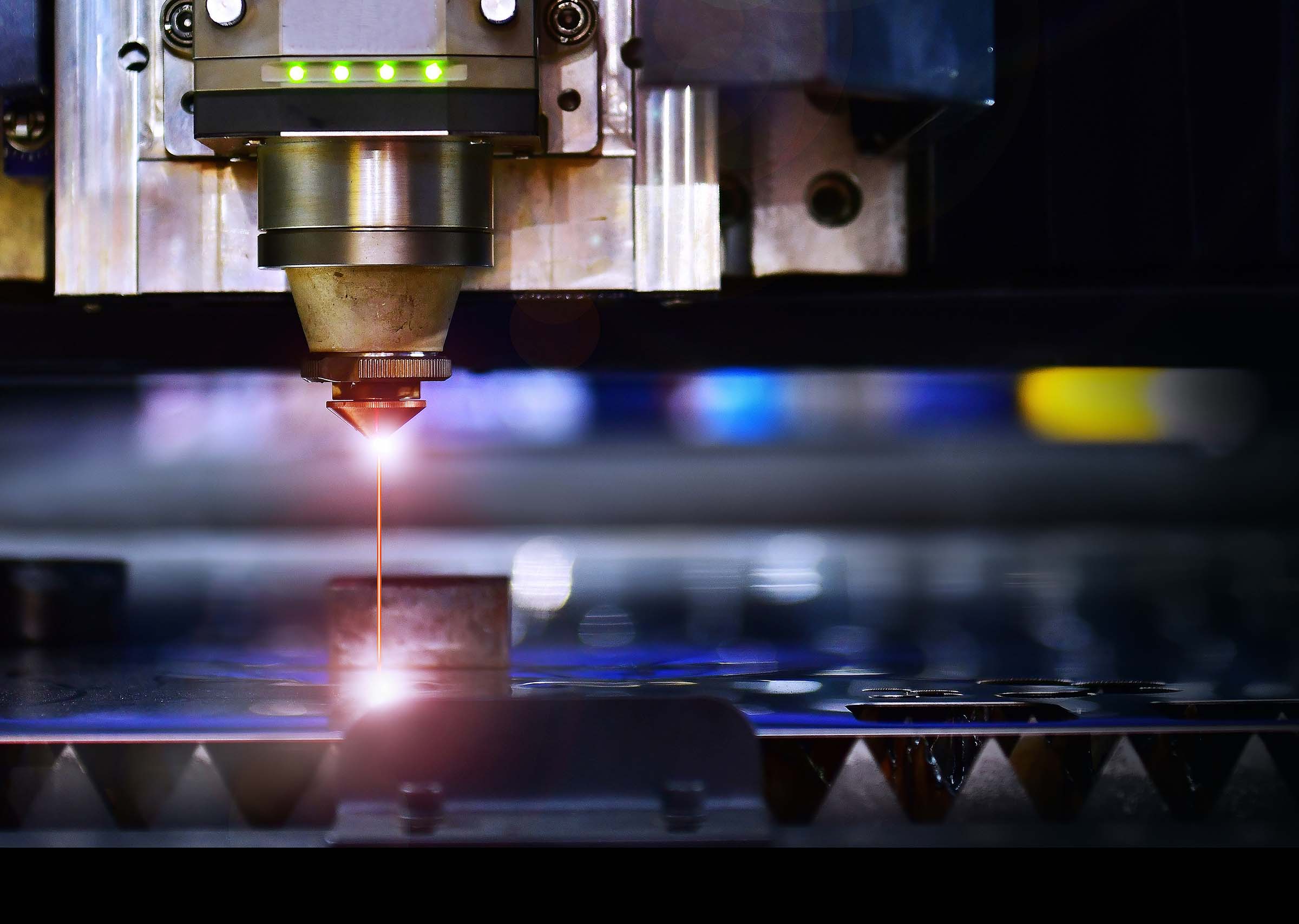
In manufacturing, laser technology is used predominantly for cutting metals. Lasers offer distinct advantages over more traditional thermal cutting methods like oxy-fuel and plasma. With any thermal cutting process, the metal is heated to its melting point and a high-velocity gas ejects the liquefied metal, leaving a void. In all cases, the cut path is left with a rough edge formed when the molten metal solidifies. The cut edge has a dark, oxidized crust commonly known as recast. It is probably no surprise that a recast edge usually is unacceptable.
This rough edge typically must be removed before further processing, which adds time and labor, so improving edge quality reduces processing time and improves productivity. Compared with other thermal processes like plasma, laser cutting is exceptionally clean and provides an almost burr-free edge. In many cases, no post-processing is required before using the laser-cut parts.All thermal processes create an area on the part where the heat has altered the mechanical and chemical properties of the metal. This is called the heat-affected zone. For critical applications, it is necessary to keep the HAZ as small as possible. Because lasers quickly and precisely can apply large amounts of energy to comparatively small areas, the HAZ on laser-cut parts is very small — again, often eliminating the need for further processing before use.
Welding is the second most common use of laser technology for manufacturing processes. Lasers benefit welding for the same reason that they benefit cutting processes. The laser energy is infinitely controllable and can be applied with extreme precision to infinitely small areas. Because of this, precision laser welding is the first choice for difficult applications.
Laser welding is ideal for miniature components, especially when welds require magnification to see. Some of the earliest laser welding was done on watch parts. Laser welding is also optimal when HAZ is a concern. Just like with cutting, the HAZ from laser welding is minuscule compared with other processes, such as tungsten inert gas, or TIG, welding.
Laser welding is also very clean, making it a good option for critical components like turbine combustion hardware. Turbine components perform in extremely harsh conditions, often operating under a continuous load at temperatures over 2,500 degrees Fahrenheit. In this type of environment, welding defects and imperfections can lead to mechanical failures capable of destroying a turbine. Using lasers not only reduces the HAZ but reduces the opportunities for contamination that exist with other welding processes, ultimately reducing the chances of a weld failing in service.
So using lasers in manufacturing has significant advantages. However, there are substantial drawbacks as well.
Lasers are expensive. Laser cutting machines are two or three times the cost of similar plasma or waterjet machines. Laser welding machines are exponentially more costly than a standard arc welding machine. Maintenance costs are also high. The parts are very expensive, and they require installation by a technician from the manufacturer.
There are safety challenges that other thermal sources do not have. In some cases, special training is needed and a laser safety officer must be on-site. Although becoming certified as an LSO is not difficult, it is another safety program that must be managed. Laser applications also require special enclosures and special personal protective equipment. All these factors add cost and complexity to a shop environment.
Lasers are typically less powerful and flexible in their applications than other technologies. Waterjet technology is one-third the cost of laser tech and easily can cut any material that fits under the head, making this one of the most flexible cutting methods available in the metalworking industry. On the other hand, lasers are limited by their power, and it is not common to find lasers capable of cutting thick materials. Unlike with plasma and oxy-fuel, reflective materials like stainless, aluminum and copper often need to be treated so they do not reflect light back into the laser head.
All the common welding methods, such as metal inert gas, TIG and stick, are portable, and you possibly passed a truck with a gas-powered welding rig on the way to work this morning. While there are small, hand-held laser units on the market today, they are still complex and fragile. Safety concerns, fragility and complexity issues need to be overcome before we see laser welding become a common practice at construction sites anytime soon.
Laser technology brings distinct advantages that are unmatched by other technologies. However, lasers also have significant baggage that needs to be investigated before adopting laser-powered processes.
Related Glossary Terms
- heat-affected zone
heat-affected zone
That portion of the base metal that was not melted during brazing, cutting or welding, but whose microstructure and mechanical properties were altered by the heat.
- metalworking
metalworking
Any manufacturing process in which metal is processed or machined such that the workpiece is given a new shape. Broadly defined, the term includes processes such as design and layout, heat-treating, material handling and inspection.