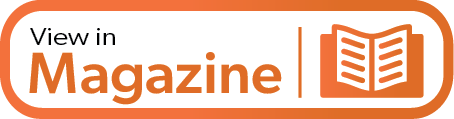
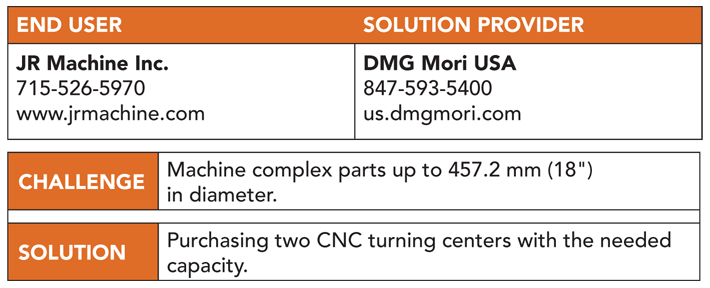
Previously, JR Machine Inc. branded itself as a provider of machining services for complex, accurate parts from 1" to 10" (25.4 mm to 254 mm) but continued to regularly receive quote requests for larger parts, as well as consultation requests about larger parts from customers who knew the contract manufacturer’s capabilities, according to Parker Tumanic, president of the Shawano, Wisconsin, company.
The level of complexity of the parts JR Machine produces meant satisfying those large-part demands must be done in-house, he noted, because outsourcing production would present too much liability.
Shane Kunschke, vice president of manufacturing, explained that JR Machine produces a large majority of parts that require multitasking, or milling and turning, to create their complicated features in one setup. “All of our machines are equipped with live tooling.”
To pursue larger-size work, JR Machine, therefore, needed to purchase equipment to accommodate it. And because the shop uses machine tools from DMG Mori exclusively, Tumanic said the decision was made to purchase two NLX 4000 CNC universal turning centers, which can machine workpieces up to 18" in diameter, from DMG Mori USA in Hoffman Estates, Illinois. “We only purchase DMG Mori machines because of the rigidity of the machine and the accuracy of it.”
The machine tool builder offers other turning centers to handle large diameters, but Kunschke said the NLX 4000 best fits the shop’s capabilities.
The turning center has large-diameter ball screws and the largest through-spindle hole diameter in its class to provide a high level of rigidity, according to DMG Mori. In addition, coolant circulates inside the machine’s castings to control thermal displacement and enhance part accuracy. These features are particularly beneficial when cutting difficult- to-machine nickel-based superalloys, such as Inconel, Monel and Hastelloy alloys. Many of the parts JR Machine makes are for industries such as space exploration and energy that require components made of these materials because of their strength, durability and resistance to high temperatures and corrosion.
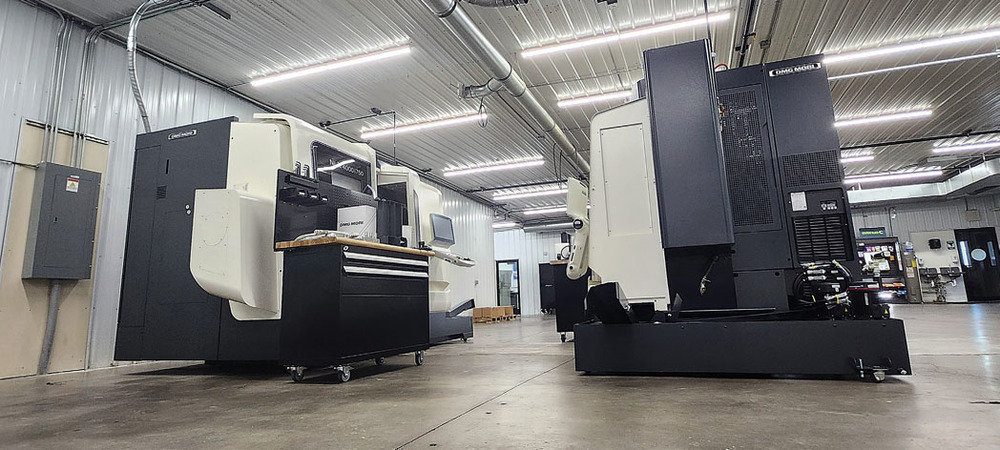
“The accuracy of the equipment combined with the skill of our technicians makes us the perfect partner for companies looking for high-mix, low-volume parts made from nickel- based superalloys,” Tumanic said.
With the addition of the two turning centers, Tumanic said the shop has 30 DMG Mori machines, which are operated by 34 machinists during two shifts. He added that having all its machines from one builder, which all have the “user friendly” CELOS control, provides continuity between machines. “Once you can run one, you can run them all.”
In addition, being exclusive to one builder provides “buying power” and streamlines maintenance requirements, Tumanic noted. “Our staff can be more efficient. It makes everything faster.”
The CELOS control not only enhances the human-machine interface but helps increase production efficiency and quality by providing data that supports JR Machine’s Industry 4.0 initiatives, Tumanic said. “We have everything wired by Ethernet from the machine to the server. On the machine side, we are sending programs back and forth, as well as using DMG Mori Messenger to monitor overall equipment effectiveness of how much spindle time we have.”
In addition, the shop’s two coordinate measuring machines collect part inspection data and store the data on a server for later retrieval and use, he noted.
With the two new NLX 4000 turning centers in operation since spring, Tumanic said JR Machine is seeing steady demand for parts larger than 10" in diameter. “We’re confident we will fill these two up quickly and, hopefully, down the line have to purchase another two.”
Related Glossary Terms
- alloys
alloys
Substances having metallic properties and being composed of two or more chemical elements of which at least one is a metal.
- centers
centers
Cone-shaped pins that support a workpiece by one or two ends during machining. The centers fit into holes drilled in the workpiece ends. Centers that turn with the workpiece are called “live” centers; those that do not are called “dead” centers.
- computer numerical control ( CNC)
computer numerical control ( CNC)
Microprocessor-based controller dedicated to a machine tool that permits the creation or modification of parts. Programmed numerical control activates the machine’s servos and spindle drives and controls the various machining operations. See DNC, direct numerical control; NC, numerical control.
- coolant
coolant
Fluid that reduces temperature buildup at the tool/workpiece interface during machining. Normally takes the form of a liquid such as soluble or chemical mixtures (semisynthetic, synthetic) but can be pressurized air or other gas. Because of water’s ability to absorb great quantities of heat, it is widely used as a coolant and vehicle for various cutting compounds, with the water-to-compound ratio varying with the machining task. See cutting fluid; semisynthetic cutting fluid; soluble-oil cutting fluid; synthetic cutting fluid.
- gang cutting ( milling)
gang cutting ( milling)
Machining with several cutters mounted on a single arbor, generally for simultaneous cutting.
- milling
milling
Machining operation in which metal or other material is removed by applying power to a rotating cutter. In vertical milling, the cutting tool is mounted vertically on the spindle. In horizontal milling, the cutting tool is mounted horizontally, either directly on the spindle or on an arbor. Horizontal milling is further broken down into conventional milling, where the cutter rotates opposite the direction of feed, or “up” into the workpiece; and climb milling, where the cutter rotates in the direction of feed, or “down” into the workpiece. Milling operations include plane or surface milling, endmilling, facemilling, angle milling, form milling and profiling.
- superalloys
superalloys
Tough, difficult-to-machine alloys; includes Hastelloy, Inconel and Monel. Many are nickel-base metals.
- turning
turning
Workpiece is held in a chuck, mounted on a face plate or secured between centers and rotated while a cutting tool, normally a single-point tool, is fed into it along its periphery or across its end or face. Takes the form of straight turning (cutting along the periphery of the workpiece); taper turning (creating a taper); step turning (turning different-size diameters on the same work); chamfering (beveling an edge or shoulder); facing (cutting on an end); turning threads (usually external but can be internal); roughing (high-volume metal removal); and finishing (final light cuts). Performed on lathes, turning centers, chucking machines, automatic screw machines and similar machines.