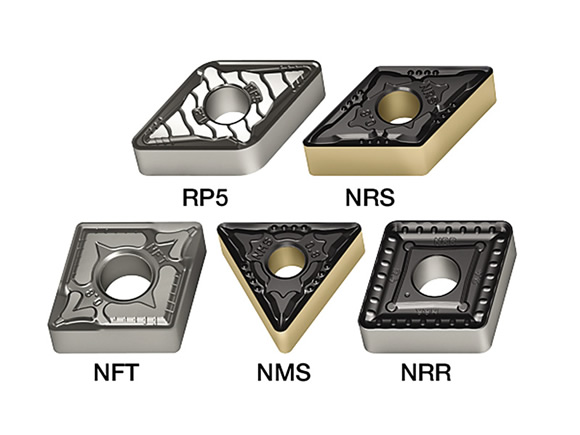
Inserts boost productivity in difficult-to-turn applications
Walter USA LLC has introduced insert geometries for turning difficult-to-machine workpieces. The NMS and NRS geometries are for turning high-temperature alloys, the NFT geometry is for turning titanium alloys, and the NRR and RP5 geometries are for roughing steel and iron. In addition to high-temperature alloys, the NMS geometry is for semifinishing ISO M materials, such as 304/316 austenitic stainless steel, and the NRS geometry is suitable for roughing forged and cast surfaces.
The WSM10 or WSM20 coating on the NMS and NRS inserts allows them to resist notching and built-up edge. This increases tool life up to 150 percent, according to the company. The NFT inserts resist crater wear and have a fully ground periphery for enhanced accuracy. The NRR is for roughing forged materials with a DOC up to 0.700 " (18mm). The RP5 has a positive 3° chamfer for roughing with low power requirements. Its open groove design produces a low cutting temperature and reduces wear compared to other geometries. It also has a wide chamfer to prevent notching when machining forging and casting skins.
Walter USA LLC; www.walter-tools.com/us
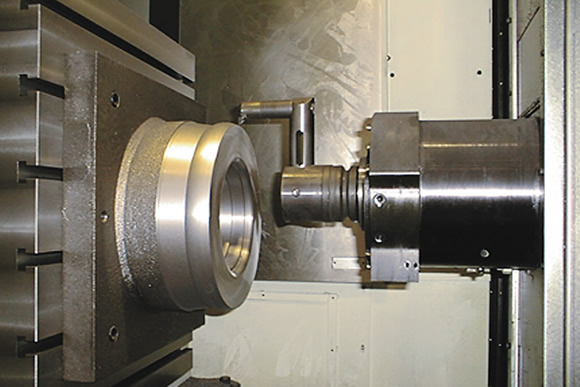
Machining function enables turning on a horizontal machining center
The Turn-Cut function from Okuma America Corp. allows turning on an HMC without the need for special-purpose machines and the associated tooling, fixtures and add-on components. The Turn-Cut function is available as an option on the company’s MA and MB series HMCs and can be retrofitted to some Okuma machining centers. The programming option allows a machine to create bores and diameters that include circular and angular features. This enables users to turn features on large, unbalanced parts on the same platform where standard CNC machining is performed. Cutting with the Turn-Cut function is performed by synchronizing the circular motion of the feed axis with the spindle’s turning angle. The surfaces created can be on the ID or OD of the machined part.
Okuma America Corp.; www.okuma.com
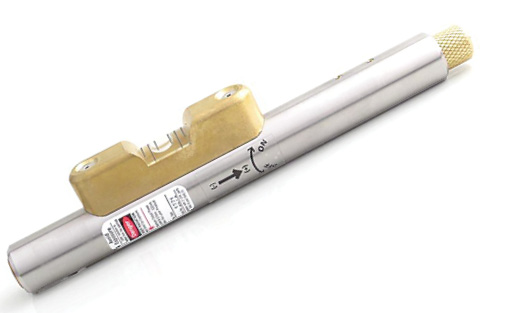
Bar feeder alignment laser enhances machine efficiency
Laser Tools Co. Inc.’s L56SS bar feeder alignment laser is chucked within a lathe’s spindle so the laser beam travels through the spindle and down the carriage of the bar feeder. Two targets register the left and right and up and down positions of the front and back of the bar feeder’s carriage. Left and right of center is adjusted during installation of a bar feeder but is often readjusted when the feeder is moved or bumped. Depending on the bar feeder style, the up and down height is adjusted manually each time a new bar stock diameter is loaded into the feeder. The alignment laser lowers operating cost by reducing setup time, maintenance cost, energy consumption and unplanned downtime, according to Laser Tools. The system accommodates bores as small as ¾ " (19.05mm) in diameter.
Laser Tools Co. Inc.; www.lasertoolsco.com
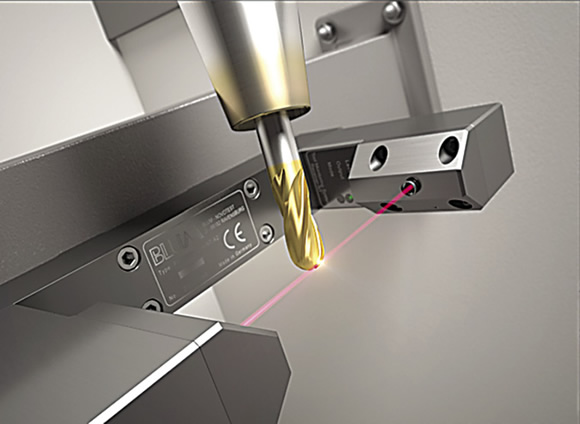
Blum LMT Inc.’s Gauging Guide is a graphical user interface that complements many of the company’s core metrology products, including lasers, tactile tool setters and workpiece probes. According to the company, the GUI makes its products easy to use for operators and programmers, and was developed for THINC controls. The company developed the software after realizing that some of the advanced features on its products were not being used because of the programming knowledge required. The company’s product software offers many advanced measurement capabilities, and the Gauging Guide utilizes these advanced measuring capabilities in the macro programming software by channeling access to advanced programs through a straightforward GUI.
“Their software guides a machinist through simple and very logical steps to program probe and laser routines,” said Jeff Estes, director of Okuma’s Partners in THINC Technology Program. “This allows for faster setups while empowering less-experienced machinists to perform these steps. It’s a win-win since the metrology technologies are used more effectively and routinely.”
Blum LMT Inc.; www.blum-novotest.com
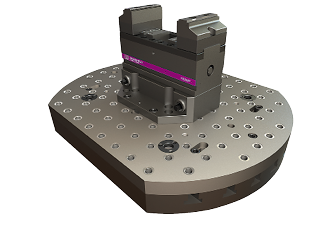
Quick-change workholder has three components
The CL5 quick-change, 5-axis workholding system from Carr Lane Manufacturing Co. consists of three components: a subplate, riser and top tooling (vise or fixture plate). According to the company, the subplate transforms a T-slot table into a modular fixturing plate, allowing flexible and easy clamping and locating of other tooling and fixtures. Every plate has built-in clamping and locating for risers, allowing quick and accurate setups. The Quintus quick-change riser allows five-sided part access. A range of fixture plates or vises can be mounted on top of the riser.
Carr Lane Manufacturing Co.; www.carrlane.com
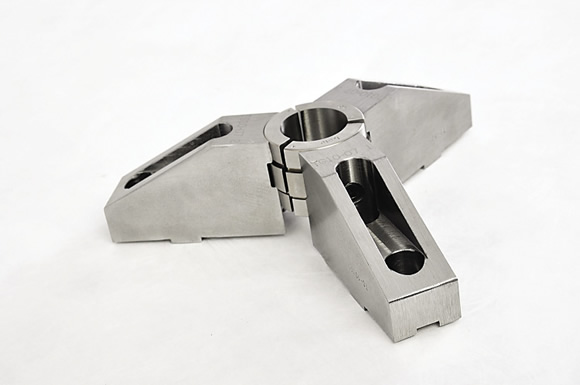
Collet pad jaws maximize part productivity
Dillon Manufacturing Inc.’s collet pads and collet pad jaws are for small-diameter parts, such as stems, spools, crimp assemblies, manifolds for high-pressure air systems and specialty valves. Users can change pads quickly and adapt the jaws to many styles of chucks, according to the company. A collet pad top jaw system increases a chuck’s range of workholding capabilities, allowing more varied part geometries to be machined with the same jaw system.
Dillon Manufacturing Inc.; www.dillonmfg.com
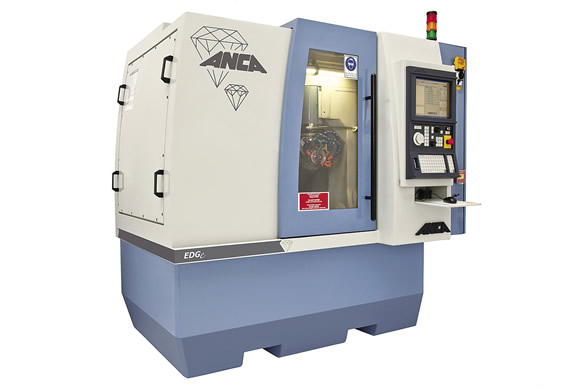
Machine erodes and grinds cutting tools
ANCA Inc.’s EDGe machine tool offers the flexibility to erode PCD cutting tools and grind carbide and HSS tools on the same machine. The EDGe-Spark generator monitors and controls the energy level of every erosion spark to achieve optimal surface finish, material-removal rate and cycle time, according to the company. The company’s ToolRoom software reportedly enables fast and versatile tool design capabilities.
ANCA Inc.; www.anca.com
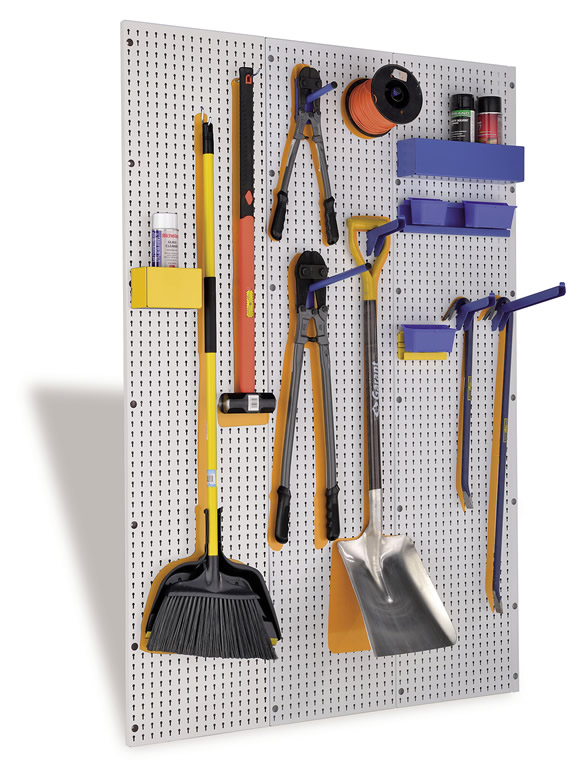
Rousseau Metal Inc.’s 5S wall panel is a multifunctional panel system that allows end users to visually identify where each item should go on a single surface. A single panel can combine round hooks for small and light articles, spike hooks for heavy and bulky items, holders for cans and supports for plastic bins. These options help optimize available space.
Rousseau Metal Inc.; www.rousseaumetal.com
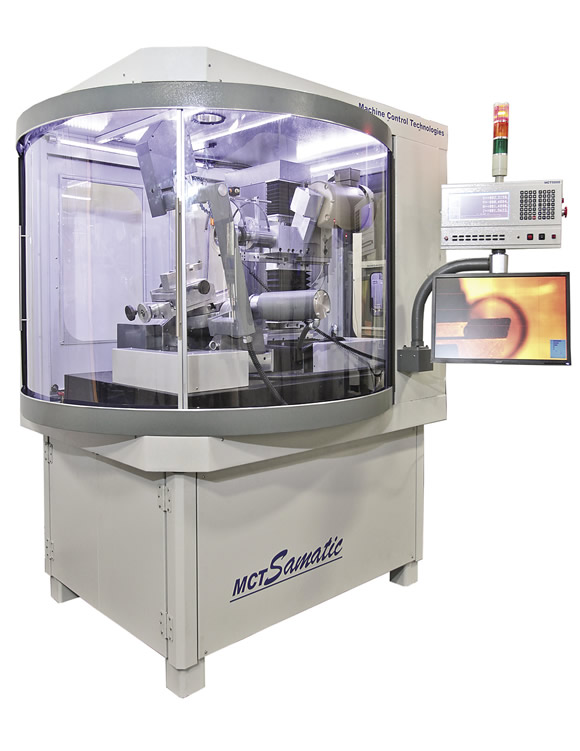
Machine tool is forgrinding PCD inserts
Machine Control Technologies Inc.’s MCT5000I CNC PCD insert grinding machine provides 7- or 8-axis freedom of movement and adjustment to produce a variety of tool geometries. The machine comes with an automatic measuring system, and can produce tool dimensions to within 5µm (0.0002 "), according to the company.
Machine Control Technologies Inc.; www.machinecontroltechnologies.com
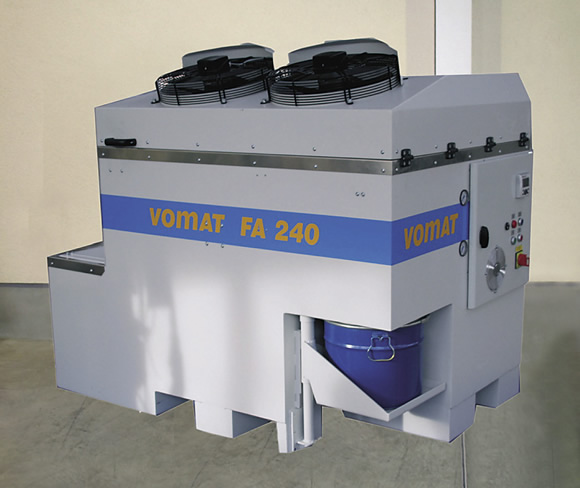
Filtration of metalworkingfluids can improve quality
Vomat GmbH’s FA 120 to 420 series microfiltration systems for metalworking fluids are distributed by oelheld U.S. Inc. Depending on the model, the system filters from 32 to 126 gpm (120 to 420 l/min.) and filters particles as fine as 3µm. The units measure 40 "×40 "×60 " (1.0m × 1.0m × 1.6m) and have a maintenance-friendly design, according to the company. Full-stream filtration with on-demand, automatic backwash cycles cleans the filter cartridges and extends service life.
Vomat GmbH; www.vomat.de oelheld U.S. Inc.; www.oelheld-us.com
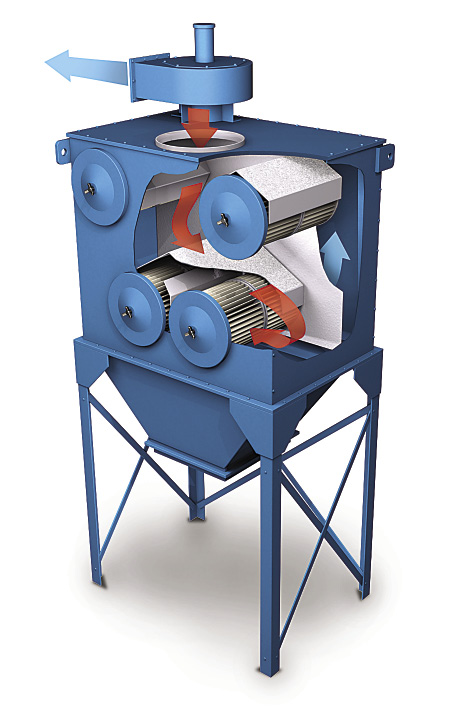
Oil mist collection and filtration system protects workers, reduces costs
Airflow System Inc.’s Model MPH10 mist collection and filtration system produces up to 1,000 cfm of airflow in industrial applications. The system features a low-profile cabinet design, which simplifies installation and makes it suitable for virtually any facility or equipment configuration, according to the company. It has a 10 " (0.25m) bottom inlet and 2 "-deep (50.8mm) sump to provide high-volume, continuous operation without manual handling of liquid. Even with a 1.0-hp motor blower, the acoustic-line cabinet maintains a 77.5-dBA noise level, protecting personnel against workplace noise. The 16/18-gauge, zinc-coated, welded steel cabinet has a powder-coated finish.
Airflow Systems Inc.; www.airflowsystems.com
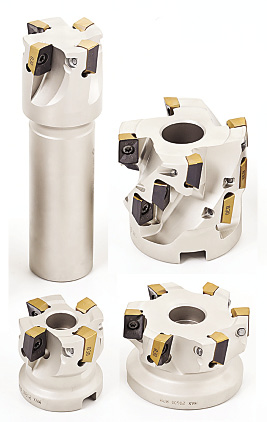
Indexable-insert tools provide chatter-free milling
Iscar Metal Inc.’s one-sided HM90 ADC 1505 …-CF insert has different helix angles on two cutting edges, and the two cutting edges are colored gold and black. The concept is to alternately mount gold and black edges, resulting in a variable-helix configuration. This reduces vibration when shoulder milling, extends tool life by 15 to 20 percent and reduces power consumption 10 percent or more, according to the company. The tools are ideally suited for less rigid setups, long overhang applications, milling thin-walled workpieces and problematic workholding arrangements. The new asymmetric insert is suitable for existing Iscar Heli-Mil milling cutters.
Iscar Metals Inc.; www.iscarmetals.com
Related Glossary Terms
- alloys
alloys
Substances having metallic properties and being composed of two or more chemical elements of which at least one is a metal.
- built-up edge ( BUE)
built-up edge ( BUE)
1. Permanently damaging a metal by heating to cause either incipient melting or intergranular oxidation. 2. In grinding, getting the workpiece hot enough to cause discoloration or to change the microstructure by tempering or hardening.
- centers
centers
Cone-shaped pins that support a workpiece by one or two ends during machining. The centers fit into holes drilled in the workpiece ends. Centers that turn with the workpiece are called “live” centers; those that do not are called “dead” centers.
- collet
collet
Flexible-sided device that secures a tool or workpiece. Similar in function to a chuck, but can accommodate only a narrow size range. Typically provides greater gripping force and precision than a chuck. See chuck.
- computer numerical control ( CNC)
computer numerical control ( CNC)
Microprocessor-based controller dedicated to a machine tool that permits the creation or modification of parts. Programmed numerical control activates the machine’s servos and spindle drives and controls the various machining operations. See DNC, direct numerical control; NC, numerical control.
- feed
feed
Rate of change of position of the tool as a whole, relative to the workpiece while cutting.
- fixture
fixture
Device, often made in-house, that holds a specific workpiece. See jig; modular fixturing.
- gang cutting ( milling)
gang cutting ( milling)
Machining with several cutters mounted on a single arbor, generally for simultaneous cutting.
- grinding
grinding
Machining operation in which material is removed from the workpiece by a powered abrasive wheel, stone, belt, paste, sheet, compound, slurry, etc. Takes various forms: surface grinding (creates flat and/or squared surfaces); cylindrical grinding (for external cylindrical and tapered shapes, fillets, undercuts, etc.); centerless grinding; chamfering; thread and form grinding; tool and cutter grinding; offhand grinding; lapping and polishing (grinding with extremely fine grits to create ultrasmooth surfaces); honing; and disc grinding.
- grinding machine
grinding machine
Powers a grinding wheel or other abrasive tool for the purpose of removing metal and finishing workpieces to close tolerances. Provides smooth, square, parallel and accurate workpiece surfaces. When ultrasmooth surfaces and finishes on the order of microns are required, lapping and honing machines (precision grinders that run abrasives with extremely fine, uniform grits) are used. In its “finishing” role, the grinder is perhaps the most widely used machine tool. Various styles are available: bench and pedestal grinders for sharpening lathe bits and drills; surface grinders for producing square, parallel, smooth and accurate parts; cylindrical and centerless grinders; center-hole grinders; form grinders; facemill and endmill grinders; gear-cutting grinders; jig grinders; abrasive belt (backstand, swing-frame, belt-roll) grinders; tool and cutter grinders for sharpening and resharpening cutting tools; carbide grinders; hand-held die grinders; and abrasive cutoff saws.
- high-speed steels ( HSS)
high-speed steels ( HSS)
Available in two major types: tungsten high-speed steels (designated by letter T having tungsten as the principal alloying element) and molybdenum high-speed steels (designated by letter M having molybdenum as the principal alloying element). The type T high-speed steels containing cobalt have higher wear resistance and greater red (hot) hardness, withstanding cutting temperature up to 1,100º F (590º C). The type T steels are used to fabricate metalcutting tools (milling cutters, drills, reamers and taps), woodworking tools, various types of punches and dies, ball and roller bearings. The type M steels are used for cutting tools and various types of dies.
- inner diameter ( ID)
inner diameter ( ID)
Dimension that defines the inside diameter of a cavity or hole. See OD, outer diameter.
- machining center
machining center
CNC machine tool capable of drilling, reaming, tapping, milling and boring. Normally comes with an automatic toolchanger. See automatic toolchanger.
- metalworking
metalworking
Any manufacturing process in which metal is processed or machined such that the workpiece is given a new shape. Broadly defined, the term includes processes such as design and layout, heat-treating, material handling and inspection.
- metrology
metrology
Science of measurement; the principles on which precision machining, quality control and inspection are based. See precision machining, measurement.
- milling
milling
Machining operation in which metal or other material is removed by applying power to a rotating cutter. In vertical milling, the cutting tool is mounted vertically on the spindle. In horizontal milling, the cutting tool is mounted horizontally, either directly on the spindle or on an arbor. Horizontal milling is further broken down into conventional milling, where the cutter rotates opposite the direction of feed, or “up” into the workpiece; and climb milling, where the cutter rotates in the direction of feed, or “down” into the workpiece. Milling operations include plane or surface milling, endmilling, facemilling, angle milling, form milling and profiling.
- modular fixturing
modular fixturing
System in which fixtures are constructed from standardized, reusable components. Fixtures are assembled and disassembled quickly. Basic styles are subplate, dowel-pin and T-slot. See fixture; modular tooling.
- outer diameter ( OD)
outer diameter ( OD)
Dimension that defines the exterior diameter of a cylindrical or round part. See ID, inner diameter.
- polycrystalline diamond ( PCD)
polycrystalline diamond ( PCD)
Cutting tool material consisting of natural or synthetic diamond crystals bonded together under high pressure at elevated temperatures. PCD is available as a tip brazed to a carbide insert carrier. Used for machining nonferrous alloys and nonmetallic materials at high cutting speeds.
- turning
turning
Workpiece is held in a chuck, mounted on a face plate or secured between centers and rotated while a cutting tool, normally a single-point tool, is fed into it along its periphery or across its end or face. Takes the form of straight turning (cutting along the periphery of the workpiece); taper turning (creating a taper); step turning (turning different-size diameters on the same work); chamfering (beveling an edge or shoulder); facing (cutting on an end); turning threads (usually external but can be internal); roughing (high-volume metal removal); and finishing (final light cuts). Performed on lathes, turning centers, chucking machines, automatic screw machines and similar machines.