Dear Doc: We do nital etching of the entire workpiece after grinding. There’s constant bickering about whether a part is burned. What can we do?
The Doc replies: Accept it. The bickering will continue. Indefinitely. Why? Because nital etching (where you dip the entire part in acid) is a very subjective test. One operator says it’s not burned; a different operator says it’s burned. And if somebody dims the lights slightly, the first operator changes his mind — now it’s burned.
But there are things you can do to reduce the uncertainty of the test so that the bickering is less often and less severe.
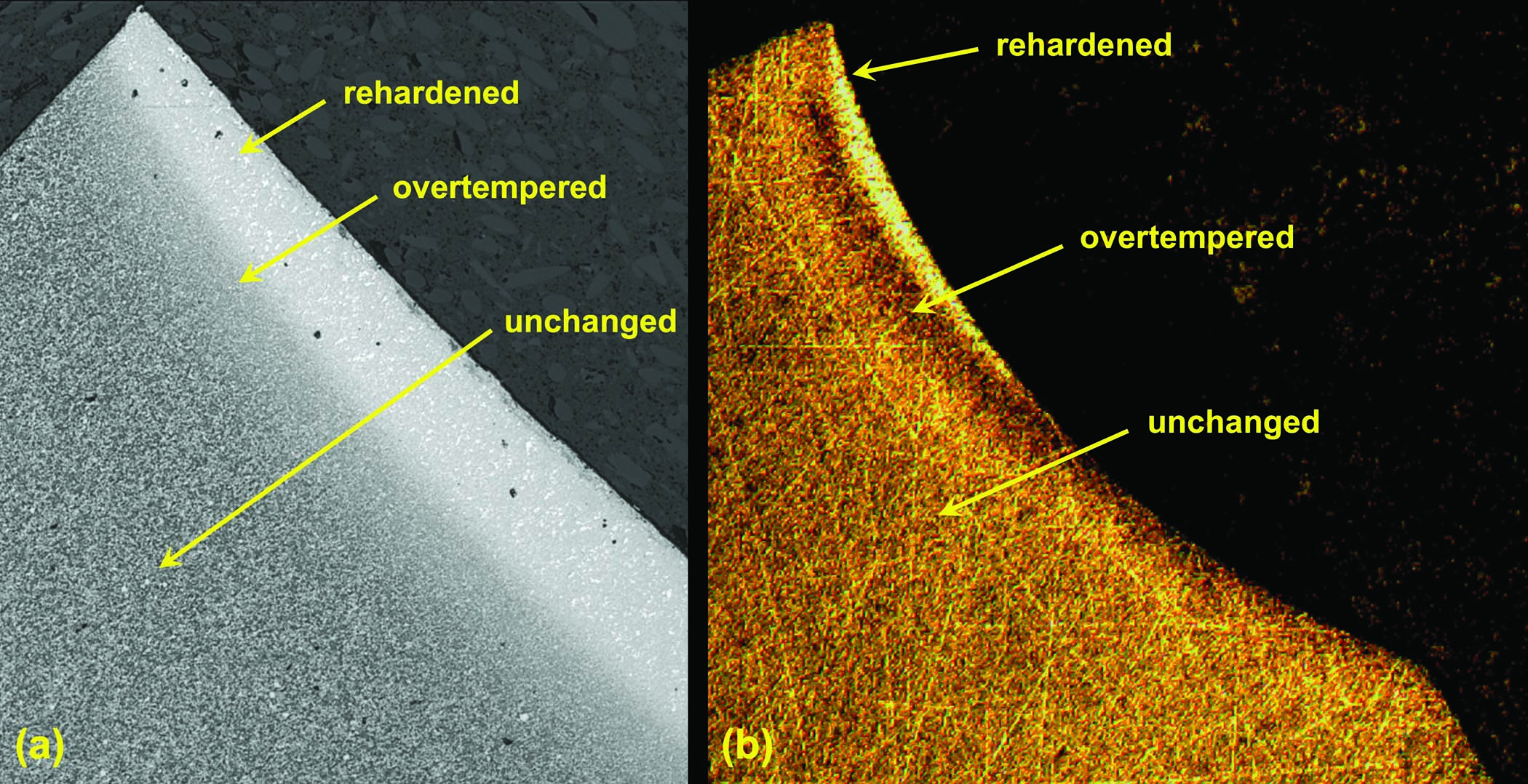
Here’s one thing I encourage my customers to do: “Calibrate” your nital etch so you feel more confident in the 50 inconsistent shades of gray that the test produces. The best way to “calibrate” it? Purposely burn a few parts to various degrees. Do your regular nital-bathing test and take photos (in the same room under the same light where they are typically examined). Then send the workpieces out for either (1) residual-stress measurements (via X-ray diffraction) or (2) cutting, mounting, polishing and nital etching (where you can see the depth of the burn).
With these methods, you can see the degree of the thermal damage and the depth of the thermal damage. You’ll probably have to send the workpiece out for X-ray diffraction. Cutting, mounting and polishing can be done in-house, if you have the equipment. Both are destructive. The workpieces will be chopped up into pieces.
I’ve helped companies get themselves set up with a cheap lab for cutting, mounting and polishing. New equipment can get pricey, but what we’re doing is not fancy and we don’t need pretty pictures. You can find a used cutting-off machine, mounting equipment, polishing machine and a cheap microscope (preferably with a digital camera) on Ebay or any of the used-equipment sites online. A few thousand bucks later, you’re looking at the depth of your thermal damage. Now we know if the rehardening is 3 µm deep, or 25 µm or 1,000 µm. Also, interpreting the picture of damage-versus-depth is less fickle than dipping the entire part in acid.
Now you can compare those depths with the pictures of the workpiece from nital bathing.
The graphic shows nital etching results using (a) fancy equipment; and (b) cheap, used equipment on Ebay. They didn’t do a great job polishing. They didn’t get a pretty picture. The workpiece is very scratchy. But it didn’t matter. They can see the depth of the burn.
Nital bathing of the entire workpiece is a fickle test. But, if you want something non-destructive, it’s either nital bathing or Barkhausen. And Barkhausen brings different complications. So nital-bathing may be what we have to work with. If you’re going to do it, spend a few days doing a rough calibration. It’s not the be-all-end-all, but it helps reduce uncertainty and bickering.
Related Glossary Terms
- calibration
calibration
Checking measuring instruments and devices against a master set to ensure that, over time, they have remained dimensionally stable and nominally accurate.
- grinding
grinding
Machining operation in which material is removed from the workpiece by a powered abrasive wheel, stone, belt, paste, sheet, compound, slurry, etc. Takes various forms: surface grinding (creates flat and/or squared surfaces); cylindrical grinding (for external cylindrical and tapered shapes, fillets, undercuts, etc.); centerless grinding; chamfering; thread and form grinding; tool and cutter grinding; offhand grinding; lapping and polishing (grinding with extremely fine grits to create ultrasmooth surfaces); honing; and disc grinding.
- polishing
polishing
Abrasive process that improves surface finish and blends contours. Abrasive particles attached to a flexible backing abrade the workpiece.