Grinding a complex cutting tool can be, well, complex. And defining what makes a cutting tool complex can be challenging too.
“A complex cutting tool is generally defined by the tool profile and its tolerances,” said Paul Ehrlich, senior applications engineer for grinding machine builder United Grinding North America Inc., Miamisburg, Ohio. “You really need to take both of those parameters into consideration, because you might have a wide open geometry with a tolerance of two or three thousandths, and that’s not a big deal, but an odd shape, even with a looser tolerance, would be complex.”
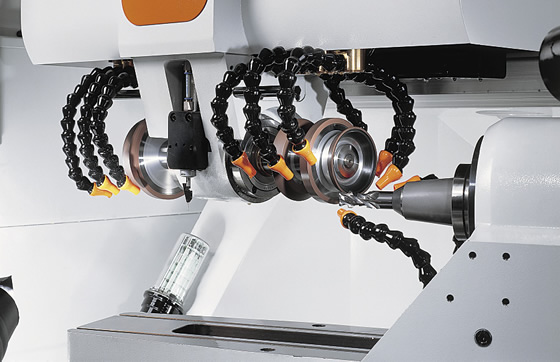
The Walter Helitronic Vision grinding machine produces rotationally symmetrical tools and parts with complex geometries. Image courtesy United Grinding North America.
Bill Freese, president of grinding machine builder Rush Machinery Inc., Rushville, N.Y., concurred, adding that multifunction tools, which may feature geometries intended to serve multiple purposes, are also complex.
Toolmaker and machine tool builder Star Cutter Co., Farmington Hills, Mich., expands the definition of complex to encompass anything outside of its normal range, noted Paul Schulte, manager of advanced technology.
“We view ‘complex’ as a tool with more than one diameter or a tolerance that is tighter than our off-the-shelf products,” he explained. “Our customers serve the automotive industry, which covers a range of tooling, so anything outside of that would definitely be complex.”
Software SolutionsWhile some disagree about what is the most important factor when grinding tools with complex forms, software always plays a big part in the discussion.
“You must ensure that whatever you see in the software is what comes out of the machine,” said Frank Holubeck, president of Reinecker Grinders, Pompano Beach, Fla., which sells grinding machines from German builder Ulmer Werkzeugschleiftechnik GmbH & Co. KG. “We urge our customers to spend time designing tools and running 3D simulations in NUMROTO software so blanks aren’t wasted. Carbide is expensive, so we want to make sure we are right on the screen, our machine is set up properly and the wheels are dressed properly. It’s not a time for trial and error.”
“The machine tool is not going to be the problem,” added United Grinding’s Ehrlich. “All toolmakers have 5- or 6-axis machines that can interpolate the most complex geometry you can think of. The real questions are, does the software possess the ability to process that kind of geometry, and can you produce the tools consistently?”
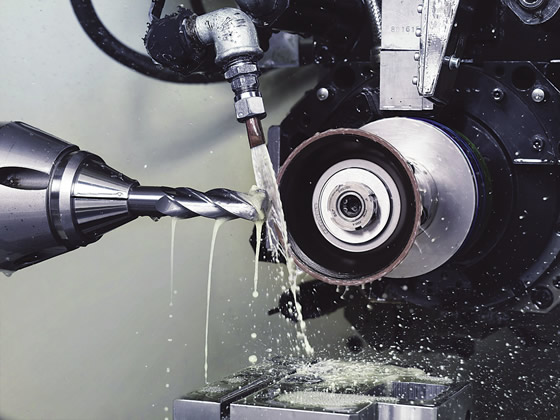
Radiac says its STARTEC XP-P abrasive reduces cycle times when grinding the flutes of round tools through effective profile retention, minimized tool deflection and reduced machine load. Image courtesy Radiac Abrasives.
United Grinding’s tool grinding machines utilize proprietary grinding software, which imports CAD drawings and feeds toolpaths to the machine. According to the company, what sets its software apart is specially developed correction software called FTC (Form Tool Compensation), which feeds data from the company’s Helicheck CNC measuring machines into the grinding machine’s CNC.
“If there are any deviances in the tool profile beyond a certain, predetermined tolerance, the Helicheck will correct the shape of the profile, and FTC will send that corrected shape to the grinder,” he explained. “A CNC grinder can usually be accurate to ±10µm; if we are checking regularly, we not only can account for variables like wheel wear, we can reduce that tolerance to ±3µm.”
In addition, whereas tool design and production were previously treated as separate processes, customer demands for high repeatability has led to the grinding process becoming more integrated with the design process, said Jason Walter, plant manager for the machine tool operations at Star Cutter. “We want to create an accurate simulation, and then we want to take that simulation and bring it to the shop floor as quickly as we can. The goal is keeping control over the process from beginning to end, without having to hand off the job from one point in the process to another.”
Wheel Be BackGrinding wheels, of course, are a key part of making complex tools. “Obviously, you want a grinding wheel that is going to have good form-holding qualities, good mrr and be well balanced with excellent axial and radial runout.” said John Guenther, business unit manager–cutting tools for Radiac Abrasives, Oswego, Ill. “That means the tool you’re making plays a part. A small-diameter tool will be more vulnerable to pressure from the grinding wheel, so you won’t be able to really push the wheel the way you might on a large tool. Larger tools are a bit more forgiving, so you can shoot for a higher mrr.”
Wheel selection, added Rush’s Freese, also involves the tool geometry and determining the proper grit size, core material and bond.
“When you’re working with complex profiles, the grinding wheel itself becomes critical,” he said. “You are trying to hold a lot of tolerances in a lot of areas, and the more complicated the geometry, the more those come into play. We supply the machines for dressing and truing the wheels to do the job, because more complex geometries can require a more complex shape on the wheel itself.
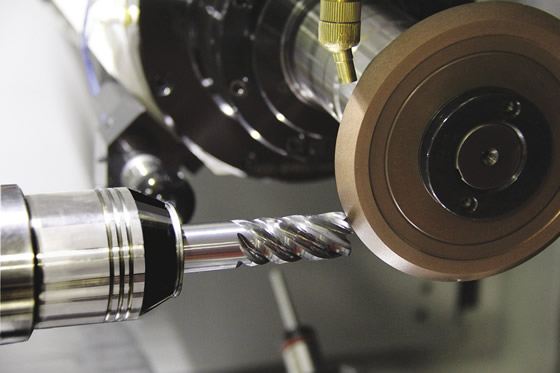
The Star PTG-6L linear motor tool gashes a specialized geometry on the tip of an endmill. Image courtesy Star Cutter.
“When you have multiple shapes and profiles within the same tool, being able to get in with the grinding wheel and get the work done can be tricky,” Freese continued. “That’s why we like to leave wheel selection up to the customer. The software on our machines can provide some information to help with wheel selection, but when the tool is being engineered, the necessary wheels will typically be spec’d out along with the material of the tool and the finish required.”
United Grinding’s Ehrlich said the main consideration boils down to what wheels the customer can use.
“A lot of customers don’t have a wheel dresser, nor do they want to invest in one,” he said. “In that case, we typically recommend a resin-type wheel for roughing the profile, then source an electroplated wheel from another manufacturer, because it is less likely to lose shape. On the other hand, if a customer has dressing capabilities, we will tool them up on different types of abrasives because they can redress that wheel as it wears.”
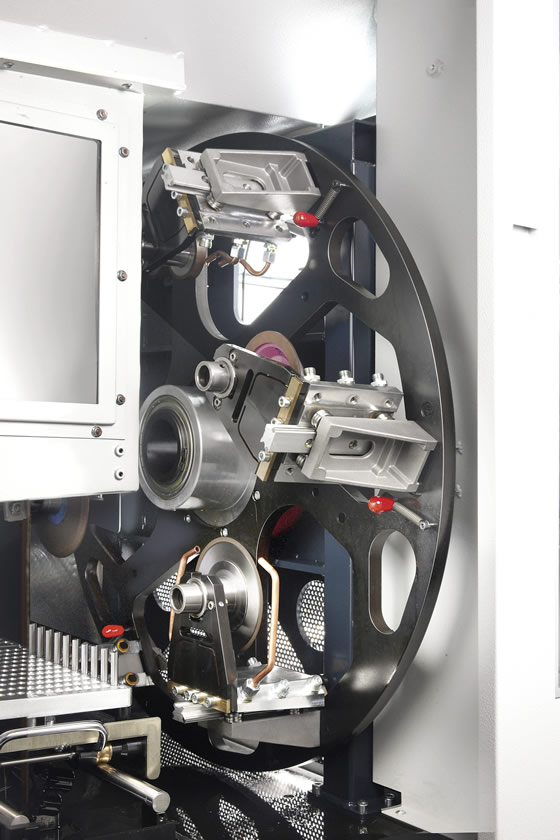
Reinecker’s WZS-700 tool grinder comes with an automatic wheel changer, allowing peel and profile grinding in a single setup. Reinecker Tool Grinders.
Ehrlich added that for holding tight profiles, a metal-bond or copper-bond wheel is best.
“In some cases, you are faced with trying to make a critical tool on an older machine,” Radiac’s Guenther noted, “so you need to be cognizant of the limitations when selecting a grinding wheel spec versus someone with a brand new machine who can take advantage of the latest technologies from grinding wheel companies.”
Blank GenerationA crucial—and sometimes overlooked—consideration for all cutting tools, including complex cutters, is the actual tool blank. According to Radiac’s Guenther, this is especially the case for complex form tools.
“You must have minimal runout on the blank,” he said. “The machine tool, the rigidity of the spindle, the method of holding and supporting the blank and the quality of the grinding wheel are important, but if the blank isn’t good, there’s only so much those other factors can do to account for it.”
Guenther said Radiac has seen more cutting tool manufacturers using peel grinding—a process that reduces the part OD prior to grinding the tool—because it allows them to make custom blanks in small batches for tools, which reduces machining time.
Reinecker’s Holubeck pointed out that, in addition to manufacturing dedicated peel grinders, the company’s WZS 700 tool grinder comes with a wheel changer, allowing customers to perform peel and profile grinding in a single setup.
“The biggest bottleneck on a standard tool and cutter machine is getting the blank prepared,” he said. “There are already many steps required to make the tool, and it takes a lot of additional work to blank out the diameter. Good blank preparation can greatly reduce the amount of time spent on the tool and cutter grinder.”
The Human TouchHowever, for all the advances made in machine tools, grinding wheels and manufacturing software, they can’t replace experience. Reinecker’s Holubeck noted that while design and simulation software is arguably critical to the process, ensuring a tool is ground at the proper speeds and feeds frequently comes down to the operator’s experience and ability to find the “sweet spot.” This ability pushes the wheel as hard as it can go without having it break apart or produce an out-of-spec tool.
“The interface with the wheel is arguably the most important aspect of the entire process,” Radiac’s Guenther added. “It really comes down to having a skilled operator. You can have the best machine tool and the best raw material in the world, but the human element can make or break anything.
“What I love about the American worker is that so many of them have a wonderful imagination, an imagination that helps them produce things that might not exist in software,” he continued. “Talented machinists know ways around limitations in the software, because they understand how the tool interacts with the wheel.” CTE
About the Author: Evan Jones Thorne is assistant editor for CTE. Contact him at (847) 714-0177 or ejonesthorne@jwr.com.
Related Glossary Terms
- abrasive
abrasive
Substance used for grinding, honing, lapping, superfinishing and polishing. Examples include garnet, emery, corundum, silicon carbide, cubic boron nitride and diamond in various grit sizes.
- computer numerical control ( CNC)
computer numerical control ( CNC)
Microprocessor-based controller dedicated to a machine tool that permits the creation or modification of parts. Programmed numerical control activates the machine’s servos and spindle drives and controls the various machining operations. See DNC, direct numerical control; NC, numerical control.
- computer-aided design ( CAD)
computer-aided design ( CAD)
Product-design functions performed with the help of computers and special software.
- dressing
dressing
Removal of undesirable materials from “loaded” grinding wheels using a single- or multi-point diamond or other tool. The process also exposes unused, sharp abrasive points. See loading; truing.
- endmill
endmill
Milling cutter held by its shank that cuts on its periphery and, if so configured, on its free end. Takes a variety of shapes (single- and double-end, roughing, ballnose and cup-end) and sizes (stub, medium, long and extra-long). Also comes with differing numbers of flutes.
- flutes
flutes
Grooves and spaces in the body of a tool that permit chip removal from, and cutting-fluid application to, the point of cut.
- grinding
grinding
Machining operation in which material is removed from the workpiece by a powered abrasive wheel, stone, belt, paste, sheet, compound, slurry, etc. Takes various forms: surface grinding (creates flat and/or squared surfaces); cylindrical grinding (for external cylindrical and tapered shapes, fillets, undercuts, etc.); centerless grinding; chamfering; thread and form grinding; tool and cutter grinding; offhand grinding; lapping and polishing (grinding with extremely fine grits to create ultrasmooth surfaces); honing; and disc grinding.
- grinding machine
grinding machine
Powers a grinding wheel or other abrasive tool for the purpose of removing metal and finishing workpieces to close tolerances. Provides smooth, square, parallel and accurate workpiece surfaces. When ultrasmooth surfaces and finishes on the order of microns are required, lapping and honing machines (precision grinders that run abrasives with extremely fine, uniform grits) are used. In its “finishing” role, the grinder is perhaps the most widely used machine tool. Various styles are available: bench and pedestal grinders for sharpening lathe bits and drills; surface grinders for producing square, parallel, smooth and accurate parts; cylindrical and centerless grinders; center-hole grinders; form grinders; facemill and endmill grinders; gear-cutting grinders; jig grinders; abrasive belt (backstand, swing-frame, belt-roll) grinders; tool and cutter grinders for sharpening and resharpening cutting tools; carbide grinders; hand-held die grinders; and abrasive cutoff saws.
- grinding wheel
grinding wheel
Wheel formed from abrasive material mixed in a suitable matrix. Takes a variety of shapes but falls into two basic categories: one that cuts on its periphery, as in reciprocating grinding, and one that cuts on its side or face, as in tool and cutter grinding.
- grit size
grit size
Specified size of the abrasive particles in grinding wheels and other abrasive tools. Determines metal-removal capability and quality of finish.
- linear motor
linear motor
Functionally the same as a rotary motor in a machine tool, a linear motor can be thought of as a standard permanent-magnet, rotary-style motor slit axially to the center and then peeled back and laid flat. The major advantage of using a linear motor to drive the axis motion is that it eliminates the inefficiency and mechanical variance caused by the ballscrew assembly system used in most CNC machines.
- outer diameter ( OD)
outer diameter ( OD)
Dimension that defines the exterior diameter of a cylindrical or round part. See ID, inner diameter.
- tolerance
tolerance
Minimum and maximum amount a workpiece dimension is allowed to vary from a set standard and still be acceptable.
- truing
truing
Using a diamond or other dressing tool to ensure that a grinding wheel is round and concentric and will not vibrate at required speeds. Weights also are used to balance the wheel. Also performed to impart a contour to the wheel’s face. See dressing.