Dressing a grinding wheel to remove unwanted material loaded between the grits causes a host of headaches. The process:
- lengthens cycle time because abrasive performance between conditionings is cyclical;
- consumes dressing sticks;
- generates debris in the coolant that can damage equipment and must be filtered and disposed of;
- adds variance to the process; and
- increases the risk of a repetitive-motion injury if done manually.
Courtesy of Saint-Gobain Abrasives
Saint-Gobain Abrasives says its Norton Paradigm diamond and CBN grinding wheels can last 2.5 times longer and achieve a 30 percent higher metal-removal rate than conventional superabrasive wheels.
These problems are pronounced when processing very hard materials, such as tungsten carbide and PCD, with the required superabrasive grinding wheels. Those workpiece materials tend to dull the pricey wheels quickly if not frequently dressed. Overdressing, on the other hand, can damage the bonding agent, prematurely releasing diamond or CBN mineral and shortening wheel life.
Seeing a need, wheel manufacturers have developed superabrasive grinding wheels that can eliminate dressing, including ones from 3M Co., Abrasive Systems Div., St. Paul, Minn.; Abrasive Technology Inc., Lewis Center, Ohio; and Saint-Gobain Abrasives Inc., Worcester, Mass. The wheels are typically used to grind carbide, ceramic and stainless steel parts, coated parts and cutting tools.
Ditch the Stick
Wheel dressing is such an ingrained activity that many end users feel it is mandatory. Troy Heuermann, business manager for 3M Abrasive Systems, said customers with wheel dressing issues “essentially told us they have to live with dressing sticks and there was no way to get around them. But we found a way.”
3M offers 637BI diamond wheels for grinding PCD and carbide parts, which can reportedly eliminate wheel conditioning. In addition, the wheel enables users to boost productivity up to 25 percent, according to Heuermann. “The biggest thing is that by eliminating dressing, you simplify the process,” he said. “It speeds up the whole process.”
The application of white aluminum-oxide, silicon-carbide and other dressing sticks and stones can cost shops $200 to $1,000 through the life of a large centerless wheel. But that cost pales in comparison to the toll workers pay for dressing.
“The biggest benefit of eliminating dressing is in reduced operator fatigue and increased operator safety,” Heuermann said. “In some cases [with a conventional superabrasive wheel], they’re pressing the dressing stick into the wheel as the wheel is processing parts.”
According to Nicholas Orf, marketing supervisor for 3M, the new wheel grinds more consistently without the need to dress, increasing the metal-removal rate without additional motor load or amp draw. “We’re able to maintain higher productivity with the same amount of energy consumption,” he said.
One prominent application for the 637BI wheel is OD grinding PCD drill bits and cutters for the oil and gas industry. A bit’s PCD compact is supported by a thicker tungsten-carbide “puck,” so the dissimilar materials are ground simultaneously. However, effectively grinding PCD typically requires a different wheel formulation than grinding carbide, Orf said. “We’ve been able to identify a new bond construction that can grind both without detrimental effects on the part or the wheel.” Similar grinding improvements have also been observed on diamond-veined round tooling, mining bits and other diamond-containing components.
Another bimetal application for the 637BI wheel is OD grinding carbide thermal spray coatings, which have a steel substrate topped with carbide. Orf explained that problems occur when both the carbide-containing coatings and steel base materials are ground at the same time. Diamond wheel performance can degrade when grinding steel substrates, causing them to become ineffective on the carbide coating. The 637BI wheel does not tend to degrade when grinding steel, according to Orf.
One thing that doesn’t change when applying 637BI wheels is the grinding system, Heuermann noted. This includes the grinder, coolant delivery equipment, coolant pressure and other machining parameters. “It’s a plug-and-play deal,” he said. “We’re just taking the dressing stick out of the system and simplifying it. You have fewer variables to worry about in the process and you get more focused on making good parts.”
Flying through the Workpiece
Abrasive Technology took a different approach to creating self-dressing diamond and CBN grinding wheels and developed induced-porosity wheels. “With industry trending to much more automated and sophisticated machinery, wheel technology needs to advance too, which means wheels need to grind at a faster pace, more freely and, at the same time, withstand cutting forces,” said Glen Rosier, who handles product development and application engineering. “Induced porosity is a way of creating space between the abrasive particles and creating a wheel that is freer cutting yet withstands those forces.”
He noted the wheels, which the company has been developing over the past 2 years, do not yet have a brand name. “Our sales guys have nicknamed it ‘the product with pixie dust,’” Rosier said.
Bond choices are phenolic resin, polyamide and hybrid metal. The latter removes high levels of material, typically when peripheral grinding carbide. It maintains the strength and toughness of a metal bond but grinds at about twice the rate of a typical resin bond, according to Rosier.
Although manufacturers make sophisticated phenolic resin- and polyamide-bond diamond and CBN wheels to provide self-dressing capability, they have little porosity and users can’t easily control wheel breakdown and wear in some situations, according to Rosier. “While the wheels stand up for an extended length of time,” he said, “they don’t generate the types of cutting rates people want in today’s market.”
Abrasive Technology manufactures its induced-porosity wheels similar to conventional superabrasive products, but proprietary additives provide a wheel structure that breaks down at a rate commensurate with the specific application. To determine that rate, the company enters critical factors, such as machine type, coolant type, machine horsepower and desired cutting rate, into an application flow chart, Rosier explained.
He noted the wheels are suitable for peripheral, centerless, flute and double-disc, or Blanchard, grinding. They extend wheel life in these applications, providing two to four times the mrr and boosting the feed rate compared to conventional superabrasive wheels, according to the company.
“We’ve seen anywhere from approximately 20 to 75 percent increases in feed rates in Blanchard grinding applications,” Rosier said. “Not only is the wheel designed to increase productivity, it reduces the amount of direct labor that gets applied to a specific grinding operation because you don’t have to dress the wheel as frequently,” he said.
Medical applications and difficult- to-grind industrial applications were the impetus for developing the wheels. One of those difficult applications is grinding cermet materials, which have a primary binder of titanium. Because the titanium wants to laminate to the wheel, the application requires a wheel with self-dressing characteristics to break down and expose new abrasive particles, Rosier explained. This keeps the wheel open and cutting freely while preventing chip loading.
Stainless steels, such as 17-7 PH, is another challenging group of materials. “They are difficult to grind because they generate a very unusual chip that wants to, once again, attach itself to the bond surface, which impedes its ability to cut,” Rosier said.
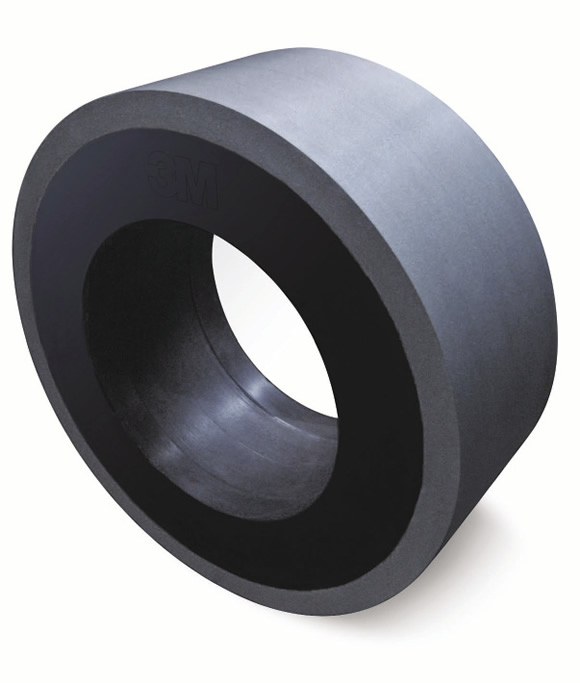
Courtesy of 3M Abrasive Systems
The 3M 637BI diamond wheel is for centerless grinding of PCD and other hard materials with little or no wheel conditioning required.
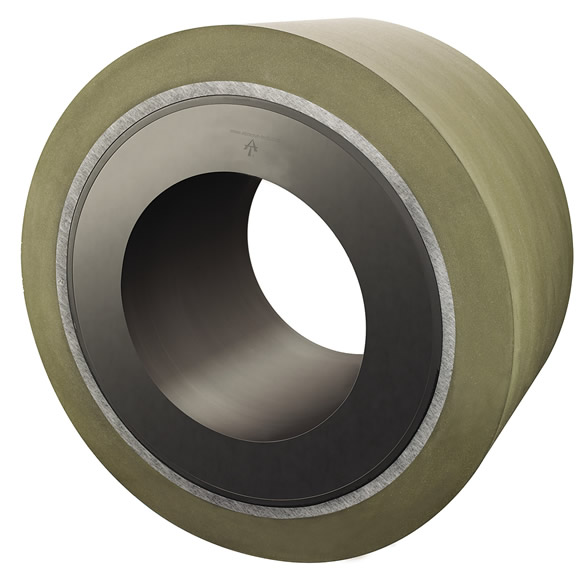
Courtesy of Abrasive Technology
Abrasive Technology says its induced-porosity wheels, such as this diamond centerless wheel with 10 percent induced porosity, cut freely while withstanding forces generated during grinding.
The new wheels are also appropriate for polishing, which still requires metal removal. “To do that at a reasonable rate, the customer needs to have a wheel that has some porosity induced into it,” he said. “Otherwise, the wheel simply runs across the surface and burnishes the part.”
To illustrate the reduced load requirements for the induced-porosity wheel, Rosier described an application where a customer was grinding a full table of carbide on a Blanchard machine, which is set up to control the down feed in steps from 0.003 to 0.009 to 0.016 ipm. After starting at 0.003 ipm and not seeing any movement in the amp meter, the customer switched to 0.009 ipm and still didn’t see any movement. “So the customer increased his feed rate to 0.016 ipm and it barely registered a load on the wheel,” he said, adding that wheel wear was 60 to 70 percent less than a conventional superabrasive product after grinding three tables of workpieces without a single dress.
Paradigm Shift
Instead of an induced-porosity structure, Saint-Gobain Abrasives builds levels of natural porosity into the metal bond of its Norton Paradigm diamond and CBN wheels, noted the company’s Corporate Senior Application Engineer Kenneth A. Saucier. (Natural porosity is what remains in the product during its manufacture, without the help of any pore inducers.) The result is a free-cutting wheel that doesn’t load when ID, OD, thread and peripheral grinding and when fluting carbide and HSS round cutting tools, he added.
In one application, an operator was pausing the automatic cycle and dressing a conventional superabrasive wheel, which is typically performed with a 220-grit Al2O3 stick, after every 10 to 15 tools were produced, Saucier noted. “When we tested the Paradigm, they ran a wheel for 2½ days and never had to touch it,” he said. “It allows a true lights-out operation, where the operators can just load a pallet and run it to the end without having to worry about maintaining wheel sharpness.”
Saucier added, however, that while complete elimination of stick dressing is possible for 5/8 "-dia. tools and smaller, larger tools might require an occasional light sticking. “But even with the large tools, we’re looking at two to three times the number of parts per stick.”
The wheel is also suitable for grinding nonmetallic materials. “Ceramic grinding is showing a tremendous amount of promise,” Saucier said, noting the wheel’s porosity enables the necessary chip clearance to prevent the material’s tendency to “gum up” a wheel. A typical feed rate for grinding ceramic is 0.2 ipm and a Paradigm wheel achieves 2.0 ipm, he added.
The ease of wheel truing is one of the technology’s most important attributes, according to Saucier. Truing can be done online, but is usually performed offline and it is time-consuming to create the needed form because the bonds are hard and durable. “With Paradigm, it literally trues like butter,” he said, noting that operators need to be careful not to quickly remove more abrasive than needed. “It acts so soft when they’re truing that most operators flat-out believe the wheel is going to fall apart when they grind with it, but it does the opposite.”
With its high level of grain retention and uniform structure, the wheel provides a high G-ratio with up to 2.5 times the wheel life and a 30 percent higher mrr than conventional superabrasive wheels, according to the company. That includes the Norton G-force wheel, which is part of the company’s highest tier product line, Saucier added.
Scrubbing the Paradigm wheel with high-pressure coolant to remove loading is not necessary and can damage the wheel. For example, a user was experiencing high Paradigm wheel wear because the scrubber nozzle was incorrectly positioned almost directly on top of the wheel—“so close it was almost touching the wheel”—and the coolant was prematurely breaking down the bond system, Saucier said. “When you have a 2 gpm nozzle delivering 600-psi coolant, it’s almost like a waterjet.”
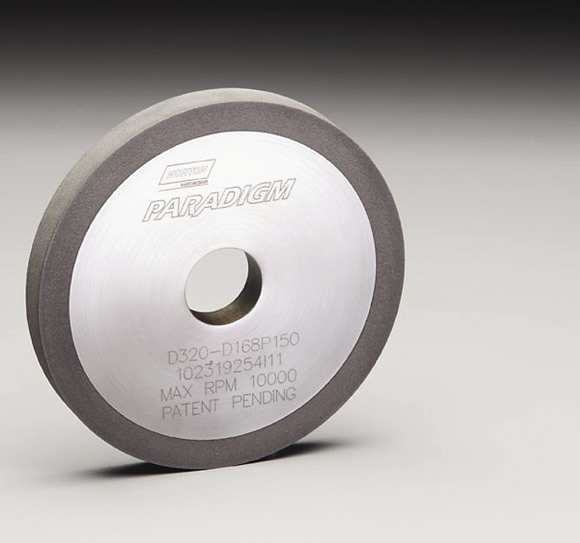
Courtesy of Saint-Gobain Abrasives
Norton Paradigm grinding wheels provide a low specific cutting energy to reduce power draw and burn, according to the manufacturer.
Coolant is still applied for cooling the wheel/workpiece interface and helping chip evacuation, and the wheel’s enhanced porosity pulls some of the coolant into the cutting zone, Saucier said. “It’ll actually make a poor situation better without changing a thing.”
He explained that because the free-cutting Paradigm wheel has a 30 percent lower specific cutting energy than conventional wheels, which enables a low power draw and reduces the risk of burn, users can increase the feed rate 30 percent while drawing the same load as the conventional wheel. This avoids compromising workpiece integrity while grinding faster.
To help apply the technology, Saint-Gobain Abrasives provides operator training to new users. “When people use Paradigm,” Saucier said, “they have to change their thought process and treat it like a totally different technology because that’s exactly what it is.”
Dressing tool manufacturers may not like these developments in self-dressing superabrasive wheels, but the wheels will enable grinding machine operators to feel a great sense of relief. CTE
About the Author: Alan Richter is editor of CTE. He joined the publication in 2000. Contact him at (847) 714-0175 or [email protected].
Continuous improvement
Since its founding in 1988, Aggressive Grinding Service Inc. has committed itself to continuous improvement to satisfy its mission of quickly delivering high-quality carbide and ceramic parts, according to President/CEO Lester Sutton. As part of that improvement process, the Latrobe, Pa.-based company recently began testing and evaluating hybrid metal-bond, induced-porosity grinding wheels from Abrasive Technology Inc.
“While certainly not a stranger to this type of bond in other departments, we made the switch in our surface grinding department, specifically on our double-disc grinders,” said Engineering and Quality Manager Randy Lechner.
The shop has two Stahli DLM 705 double-disc grinders, both with a 28 " wheel diameter and six-carrier arrangement. Sutton explained that a double-disc grinder simultaneously grinds the top and bottom of workpieces. Workpieces are held in a round fixture, which rotates with a drive ring in the center of the machine, so the parts are moving in a circle from inside to outside and around the grinding wheels. “It’s kind of like a Spirograph,” he said. “We find, in many cases, double-disc grinding is from 10 to 30 times faster than surface grinding.”
According to Lechner, Aggressive Grinding Service grinds 2 "-dia. carbide discs, with six carriers holding three parts for a total of 18 per load. The coolant is SintoGrind TTS-US synthetic cutting oil, applied at 40 psi and cleaned with a One Micron filtration system from Transor Filter. The company removes 0.040 " from the workpieces. It previously applied ATI pie-segment, resin-bond wheels with the following parameters:
- 15-minute cycle time;
- 0.0027-ipm feed rate;
- 0.153-cu.-in./min. mrr;
- 325 rpm for the top and bottom wheels;
- 20 rpm for the center ring; and
- Pressure of 400 to 900 lbs. (controlled by the feed rate).
In this operation, wheel dressing took place once every 234 parts.
Courtesy of Aggressive Grinding Service
One of two Stahli DLM 705 double-disc grinders Aggressive Grinding Service uses to grind carbide discs with ATI’s hybrid metal-bond, induced-porosity wheels.
After switching to ATI pie-segment, hybrid metal-bond, induced-porosity wheels, the shop achieved the following:
- 12-minute cycle time;
- 0.0034-ipm feed rate;
- 0.192-cu.-in./min. mrr;
- 325 rpm for the top and bottom wheels;
- 20 rpm for the center ring; and
- Pressure of 250 to 600 lbs. (controlled by the feed rate).
In this operation, wheel dressing takes place only at the end of the 600-part order.
“The induced porosity of this bond allows for a cooler, more free-cutting action,” Lechner said. “The wheel has shown a 50 percent increase in life as a function of material removed and the number of parts ground between wheel dressings.” Dressing is done with a circular, 150-grit, Al2O3 stone.
He noted, however, that the resin-bond wheels impart a surface finish of 8 to 10 µin. Ra while the finish is 16 to 20 µin. Ra for the hybrid metal-bond ones. “Overall, we feel this metal-bond wheel is more cost-efficient based on stock removal vs. wheel life alone,” Lechner said, adding that reduced cycle time and dressing frequency are added benefits.
“It’s probably as significant of an improvement as I’ve seen in my 30 years of grinding,” Sutton said.
—A. Richter
Contributors
Abrasive Technology Inc.
(800) 964-8324
www.abrasive-tech.com
Aggressive Grinding Service Inc.
(724) 537-7722
www.ags-fast.com
Saint-Gobain Abrasives Inc.
(800) 551-4413
www.nortonabrasives.com
3M Co., Abrasive Systems Div.
(866) 279-1235
www.3m.com/abrasives
Related Glossary Terms
- G-ratio
G-ratio
Measure of the grinding performance defined as the volume of metal removed divided by the volume of grinding wheel worn away in the operation.
- abrasive
abrasive
Substance used for grinding, honing, lapping, superfinishing and polishing. Examples include garnet, emery, corundum, silicon carbide, cubic boron nitride and diamond in various grit sizes.
- centerless grinding
centerless grinding
Grinding operation in which the workpiece rests on a knife-edge support, rotates through contact with a regulating or feed wheel and is ground by a grinding wheel. This method allows grinding long, thin parts without steady rests; also lessens taper problems. Opposite of cylindrical grinding. See cylindrical grinding; grinding.
- chip clearance
chip clearance
In milling, the groove or space provided in the cutter body that allows chips to be formed by the inserts.
- clearance
clearance
Space provided behind a tool’s land or relief to prevent rubbing and subsequent premature deterioration of the tool. See land; relief.
- coolant
coolant
Fluid that reduces temperature buildup at the tool/workpiece interface during machining. Normally takes the form of a liquid such as soluble or chemical mixtures (semisynthetic, synthetic) but can be pressurized air or other gas. Because of water’s ability to absorb great quantities of heat, it is widely used as a coolant and vehicle for various cutting compounds, with the water-to-compound ratio varying with the machining task. See cutting fluid; semisynthetic cutting fluid; soluble-oil cutting fluid; synthetic cutting fluid.
- cubic boron nitride ( CBN)
cubic boron nitride ( CBN)
Crystal manufactured from boron nitride under high pressure and temperature. Used to cut hard-to-machine ferrous and nickel-base materials up to 70 HRC. Second hardest material after diamond. See superabrasive tools.
- dressing
dressing
Removal of undesirable materials from “loaded” grinding wheels using a single- or multi-point diamond or other tool. The process also exposes unused, sharp abrasive points. See loading; truing.
- fatigue
fatigue
Phenomenon leading to fracture under repeated or fluctuating stresses having a maximum value less than the tensile strength of the material. Fatigue fractures are progressive, beginning as minute cracks that grow under the action of the fluctuating stress.
- feed
feed
Rate of change of position of the tool as a whole, relative to the workpiece while cutting.
- fixture
fixture
Device, often made in-house, that holds a specific workpiece. See jig; modular fixturing.
- fluting
fluting
Cutting straight or spiral grooves in drills, endmills, reamers and taps to improve cutting action and remove chips.
- grinding
grinding
Machining operation in which material is removed from the workpiece by a powered abrasive wheel, stone, belt, paste, sheet, compound, slurry, etc. Takes various forms: surface grinding (creates flat and/or squared surfaces); cylindrical grinding (for external cylindrical and tapered shapes, fillets, undercuts, etc.); centerless grinding; chamfering; thread and form grinding; tool and cutter grinding; offhand grinding; lapping and polishing (grinding with extremely fine grits to create ultrasmooth surfaces); honing; and disc grinding.
- grinding machine
grinding machine
Powers a grinding wheel or other abrasive tool for the purpose of removing metal and finishing workpieces to close tolerances. Provides smooth, square, parallel and accurate workpiece surfaces. When ultrasmooth surfaces and finishes on the order of microns are required, lapping and honing machines (precision grinders that run abrasives with extremely fine, uniform grits) are used. In its “finishing” role, the grinder is perhaps the most widely used machine tool. Various styles are available: bench and pedestal grinders for sharpening lathe bits and drills; surface grinders for producing square, parallel, smooth and accurate parts; cylindrical and centerless grinders; center-hole grinders; form grinders; facemill and endmill grinders; gear-cutting grinders; jig grinders; abrasive belt (backstand, swing-frame, belt-roll) grinders; tool and cutter grinders for sharpening and resharpening cutting tools; carbide grinders; hand-held die grinders; and abrasive cutoff saws.
- grinding wheel
grinding wheel
Wheel formed from abrasive material mixed in a suitable matrix. Takes a variety of shapes but falls into two basic categories: one that cuts on its periphery, as in reciprocating grinding, and one that cuts on its side or face, as in tool and cutter grinding.
- high-speed steels ( HSS)
high-speed steels ( HSS)
Available in two major types: tungsten high-speed steels (designated by letter T having tungsten as the principal alloying element) and molybdenum high-speed steels (designated by letter M having molybdenum as the principal alloying element). The type T high-speed steels containing cobalt have higher wear resistance and greater red (hot) hardness, withstanding cutting temperature up to 1,100º F (590º C). The type T steels are used to fabricate metalcutting tools (milling cutters, drills, reamers and taps), woodworking tools, various types of punches and dies, ball and roller bearings. The type M steels are used for cutting tools and various types of dies.
- inches per minute ( ipm)
inches per minute ( ipm)
Value that refers to how far the workpiece or cutter advances linearly in 1 minute, defined as: ipm = ipt 5 number of effective teeth 5 rpm. Also known as the table feed or machine feed.
- inner diameter ( ID)
inner diameter ( ID)
Dimension that defines the inside diameter of a cavity or hole. See OD, outer diameter.
- metal-removal rate
metal-removal rate
Rate at which metal is removed from an unfinished part, measured in cubic inches or cubic centimeters per minute.
- micron
micron
Measure of length that is equal to one-millionth of a meter.
- outer diameter ( OD)
outer diameter ( OD)
Dimension that defines the exterior diameter of a cylindrical or round part. See ID, inner diameter.
- polishing
polishing
Abrasive process that improves surface finish and blends contours. Abrasive particles attached to a flexible backing abrade the workpiece.
- polycrystalline diamond ( PCD)
polycrystalline diamond ( PCD)
Cutting tool material consisting of natural or synthetic diamond crystals bonded together under high pressure at elevated temperatures. PCD is available as a tip brazed to a carbide insert carrier. Used for machining nonferrous alloys and nonmetallic materials at high cutting speeds.
- relief
relief
Space provided behind the cutting edges to prevent rubbing. Sometimes called primary relief. Secondary relief provides additional space behind primary relief. Relief on end teeth is axial relief; relief on side teeth is peripheral relief.
- stainless steels
stainless steels
Stainless steels possess high strength, heat resistance, excellent workability and erosion resistance. Four general classes have been developed to cover a range of mechanical and physical properties for particular applications. The four classes are: the austenitic types of the chromium-nickel-manganese 200 series and the chromium-nickel 300 series; the martensitic types of the chromium, hardenable 400 series; the chromium, nonhardenable 400-series ferritic types; and the precipitation-hardening type of chromium-nickel alloys with additional elements that are hardenable by solution treating and aging.
- surface grinding
surface grinding
Machining of a flat, angled or contoured surface by passing a workpiece beneath a grinding wheel in a plane parallel to the grinding wheel spindle. See grinding.
- truing
truing
Using a diamond or other dressing tool to ensure that a grinding wheel is round and concentric and will not vibrate at required speeds. Weights also are used to balance the wheel. Also performed to impart a contour to the wheel’s face. See dressing.
- tungsten carbide ( WC)
tungsten carbide ( WC)
Intermetallic compound consisting of equal parts, by atomic weight, of tungsten and carbon. Sometimes tungsten carbide is used in reference to the cemented tungsten carbide material with cobalt added and/or with titanium carbide or tantalum carbide added. Thus, the tungsten carbide may be used to refer to pure tungsten carbide as well as co-bonded tungsten carbide, which may or may not contain added titanium carbide and/or tantalum carbide.