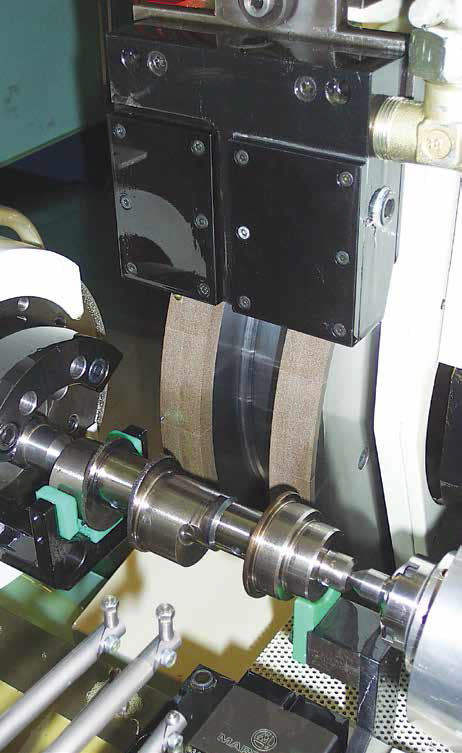
Courtesy of Norton/Saint-Gobain Abrasives
Plunge grinding a balance shaft with vitrified CBN wheels.
Increased speeds have allowed grinding to move beyond its status as a finishing operation to become a primary metal-removal method in some applications. High-speed grinding (HSG) combines high metal-removal rates with minimal wheel wear. But are those higher removal rates and faster production speeds worth the higher grinding machine costs and pricier CBN wheels needed for HSG compared to the machines and aluminum-oxide and silicon-carbide wheels used for conventional grinding? In most cases, the answer appears to be “yes.”
HSG is commonly used to grind ODs. It is a well-established method for making camshafts and crankshafts, as well as transmission shafts, drive shafts, power steering components, turbine components, gears and aerospace fasteners. Workpiece materials ground with CBN wheels for HSG include nodular iron, hardened carbon and alloy steels, soft steels and nickel-base superalloys.
How Fast is Fast?
The main benefit of HSG is its higher mrr compared to conventional OD grinding while imparting the same surface finish. This is accomplished by maintaining comparable chip thickness and reduced grinding forces at a comparable power (spindle power = tangential force × wheel velocity) when performing HSG.
“When you get into high speeds, you can definitely achieve some very high removal rates in certain materials and applications,” said Mike Hitchiner, OEM technology manager, Norton/Saint-Gobain Abrasives, Worchester, Mass. “I have applications pushing Q prime values, or mrr [mm3 per mm per second], as high as 600, although numbers around 100 to 300 are more typical. These are typically achieved by grinding burn- insensitive parts made from gray or nodular iron or soft steel, such as crankshafts or balance shafts. I’m also achieving comparable numbers on more burn-sensitive parts, even Inconel, but under specific grind conditions such as peel grinding, which is conducive to low heat generation.”
Hitchiner noted HSG does not have to generate a massive mrr to be successful. In many cases, the gains are modest improvements in Q prime values, but also enhanced surface finish and consistency, as well as long wheel life.
Most agree that the borderline between conventional grinding and HSG of precision parts are wheel speeds of 80 to 120 m/sec. Conventional OD grinding starts at about 30 m/sec., with 60 m/sec. being the usual limit in terms of the need for special guarding and additional safety factors. OD camshaft and crankshaft grinding typically runs between 60 and 120 m/sec., while transmission parts tend to be ground at 80 to 120 m/sec.
Machine Needs
An HSG machine needs to be stable, with high dynamic stiffness and a higher-power spindle than one used for conventional grinding.
“Also, the headstock on the machine, whether a chuck or some other kind of workholding, has to be able to go faster as well to be able to get the correct ratio between wheel speed and part speed,” said Rob Titus, senior applications engineer for machine tool builder Okuma America Corp., Charlotte, N.C.
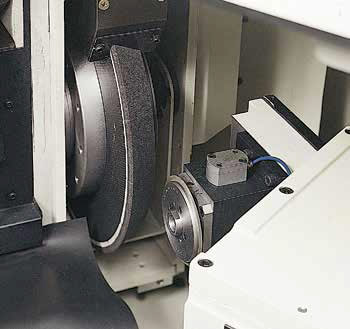
Courtesy of Okuma
A vitrified CBN grinding wheel with a rotary dresser. Okuma offers an HSG spindle (120 m/sec.) on its GP-25TII grinding machine.
He added that a chiller unit is added to the spindles because of the increased heat. “On the grinders we build, we try to control that high-speed spindle’s oil. We keep the temperature constant so there are no tolerance control issues.”
HSG also requires a specialized coolant system, adding to machine cost. A rule of thumb in any grinding operation is the coolant velocity or pressure must match the wheel speed. Therefore, with a higher speed wheel, coolant pressure has to be higher as well. “For example, 60 m/sec. would need about 250 psi, 80 m/sec. around 400 psi and 120 m/sec. would be upwards of 900 to 1,000 psi,” Titus said.
A coolant system with a high-pressure and -volume capability is required to produce the required coolant velocity, according to Tom Namola, product development and application engineer for Abrasive Technology Inc., Lewis Center, Ohio. “There is a relationship between the coolant velocity and the peripheral wheel speed,” he said. “When you fall below a certain number, you start to starve the cut. If it is an oil run with plated CBN wheels, the coolant velocity really needs to be, at minimum, 60 percent of the wheel speed.”
And typically with CBN wheels run at high speeds, oil needs to be applied. “Because water-based coolant doesn’t have the lubricity and clinginess of oil, it has to match the wheel speed closer or it really won’t get carried through the cut,” Namola said. “Oil is more forgiving and easier to apply. With water-based coolant, that 60 percent number goes up to 85 or 90 percent.”
Namola also emphasized carefully checking grinding calculations. With the higher coolant pressure and volume needed for HSG, it is a challenge to keep the coolant stream from spreading and slowing down.
“What matters is the coolant speed at the workpiece/wheel intersection,” he said. “If you calculate coolant speed based on nozzle opening area, then you must factor this back by the increase in coolant stream area at the workpiece/wheel intersection.”
An additional machine need in the U.S. is special guarding when grinding above 60 m/sec., per ANSI standards.
Wheel Needs
Most HSG of metal is done with vitrified-bond or plated CBN wheels. High speeds place special challenges on wheel design with regard to preventing bursting or distorting under higher centrifugal loads. Wheel mounting methods must be able to hold the wheels without slippage or imbalance. Vitrified CBN wheels for 80 m/sec. and above are segmented, with segments cemented to a steel or carbon fiber core (to reduce weight).
Vitrified CBN wheels are dressable, but it is required much less often than with conventional wheels.
Single-layer plated CBN wheels, however, are not dressed. With plated wheels, a single layer of CBN grain is bonded with nickel plating to a steel wheel core.When the wheel wears out, the coating is stripped and the wheel is replated. Replating, in general, costs about 40 percent less than a new wheel, according to Namola. Plated CBN wheels are typically replated up to 5 times.
The main advantage of using plated CBN wheels when form grinding is that the form can be complicated because the wheel is not dressed, he added. When grinding with bonded wheels, complex forms are challenging because the wheels must be dressed.
The grinding wheel itself is challenging to rotate at high speeds, requiring a machine with substantial spindle power to run wide wheels at high speeds. “For example, let’s say a shop has been grinding bearing journals instead of turn broaching them using a plated CBN form wheel at 160 m/sec. using a 20mm-wide (0.787 ") wheel,” Hitchiner said. “The wheel is only 20mm wide yet consumes 80kW motor power. Of that 80kW, 40 of it is used just to spin the wheel and overcome the resistance of the coolant. When running at 160 m/sec., a lot of what you gain in the grind energy, making it more efficient to the grind, can be lost in the wheel energy and the drag of the coolant.”
Therefore, he continued, applications for HSG frequently use narrow wheels, such as for circlip groove grinding, rotor slots and peel grinding. “You don’t have to worry about the wheel mass and the coolant drag is a lot less. Having 3kW to 4kW per mm of wheel width is good rule of thumb.”
Peel Grinding
Peel grinding, performed with vitrified CBN wheels, is an alternative to formed-wheel plunge grinding. CBN wheels are well-suited for peel grinding because they offer extra strength at the edge of the wheel.
With peel grinding, a narrow wheel—6.4mm (0.25 ") or less in width—is moved along the contour, completing the full grind in a single pass. The last 2mm to 3mm of the wheel face generates the required surface finish.
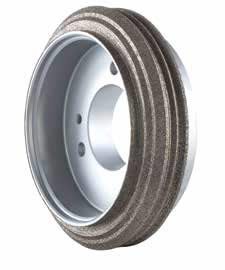
Courtesy of Abrasive Technology
A single-layer plated CBN form wheel for grinding turbine vanes.
Peel grinding concentrates all the grinding force in one small area, grinding relatively small-diameter parts at high work speeds to minimize heat generation; the wheel is similar to a single-point tool on a lathe. “Peel grinding works by having a very small contact area and very high wheel and work speeds, taking typical DOCs of 0.005 " to 0.015 ",” Hitchiner said.
This small contact area between the workpiece and the grinding wheel reduces the cutting forces. Reduced cutting forces generate less heat, which means peel grinding can be performed at higher speeds. “The impact of the grain on the workpiece is not as much as with slower speeds, so it doesn’t induce heat into the part,” said Hans Ueltschi, vice president of sales, cylindrical division, for United Grinding North America Inc., Miamisburg, Ohio. “The part stays cool, there is less pressure, and the part doesn’t bend as much.”
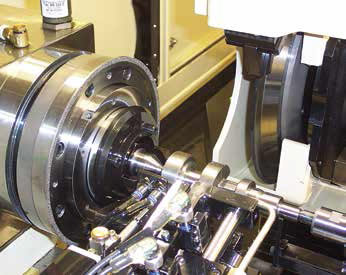
Courtesy of Norton/Saint-Gobain Abrasives
Peel grinding a balance shaft with a vitrified CBN wheel.
One of the biggest advantages of peel grinding is flexibility. “The process is really flexible, so it is good for parts that require quick changeover,” Ueltschi said. “To go from one part to another, all you have to change is the program on the machine. You don’t have to tear down the grinding wheel and dressing system and put in new ones. You just put in the dimensions and you are good to go.” This allows for low-volume runs.
For high-volume jobs where no flexibility is required, such as when making crankshafts, the plunge method is used because it reduces cycle times.
In addition to replacing conventional grinding, HSG can match or exceed many conventional machining processes, according to Hitchiner. One example is gear hobbing. “Right now, customers buy a grinding machine to get final gear shape after heat treatment, but they still broach the rough form beforehand,” he said. “If you are repairing big gears for the oil or mining industry, you could wait 10 weeks for a hob. If you have a grinder already available that can generate the form, and a grinding process that can cut as fast as a broach in the soft state, you can turn around a part in a fraction of the time. There are huge savings for just-in-time work instead of waiting around for expensive cutters.” CTE
Contributors
Abrasive Technology Inc.
(800) 964-8324
www.abrasive-tech.com
Okuma America Corp.
(704) 588-7000
www.okuma.com
Norton/Saint-Gobain Abrasives
(254) 918-2313
www.nortonindustrial.com
United Grinding North America Inc.
(937) 859-1975
www.grinding.com
Related Glossary Terms
- abrasive
abrasive
Substance used for grinding, honing, lapping, superfinishing and polishing. Examples include garnet, emery, corundum, silicon carbide, cubic boron nitride and diamond in various grit sizes.
- alloy steels
alloy steels
Steel containing specified quantities of alloying elements (other than carbon and the commonly accepted amounts of manganese, sulfur and phosphorus) added to cause changes in the metal’s mechanical and/or physical properties. Principal alloying elements are nickel, chromium, molybdenum and silicon. Some grades of alloy steels contain one or more of these elements: vanadium, boron, lead and copper.
- broach
broach
Tapered tool, with a series of teeth of increasing length, that is pushed or pulled into a workpiece, successively removing small amounts of metal to enlarge a hole, slot or other opening to final size.
- broaching
broaching
Operation in which a cutter progressively enlarges a slot or hole or shapes a workpiece exterior. Low teeth start the cut, intermediate teeth remove the majority of the material and high teeth finish the task. Broaching can be a one-step operation, as opposed to milling and slotting, which require repeated passes. Typically, however, broaching also involves multiple passes.
- chuck
chuck
Workholding device that affixes to a mill, lathe or drill-press spindle. It holds a tool or workpiece by one end, allowing it to be rotated. May also be fitted to the machine table to hold a workpiece. Two or more adjustable jaws actually hold the tool or part. May be actuated manually, pneumatically, hydraulically or electrically. See collet.
- concentrates
concentrates
Agents and additives that, when added to water, create a cutting fluid. See cutting fluid.
- coolant
coolant
Fluid that reduces temperature buildup at the tool/workpiece interface during machining. Normally takes the form of a liquid such as soluble or chemical mixtures (semisynthetic, synthetic) but can be pressurized air or other gas. Because of water’s ability to absorb great quantities of heat, it is widely used as a coolant and vehicle for various cutting compounds, with the water-to-compound ratio varying with the machining task. See cutting fluid; semisynthetic cutting fluid; soluble-oil cutting fluid; synthetic cutting fluid.
- cubic boron nitride ( CBN)
cubic boron nitride ( CBN)
Crystal manufactured from boron nitride under high pressure and temperature. Used to cut hard-to-machine ferrous and nickel-base materials up to 70 HRC. Second hardest material after diamond. See superabrasive tools.
- dressing
dressing
Removal of undesirable materials from “loaded” grinding wheels using a single- or multi-point diamond or other tool. The process also exposes unused, sharp abrasive points. See loading; truing.
- dynamic stiffness
dynamic stiffness
Measure of a machining system’s ability to dampen vibration from a forced input. If the dynamic stiffness of a system is not sufficient to dampen vibration, chatter occurs. See static stiffness; stiffness.
- grinding
grinding
Machining operation in which material is removed from the workpiece by a powered abrasive wheel, stone, belt, paste, sheet, compound, slurry, etc. Takes various forms: surface grinding (creates flat and/or squared surfaces); cylindrical grinding (for external cylindrical and tapered shapes, fillets, undercuts, etc.); centerless grinding; chamfering; thread and form grinding; tool and cutter grinding; offhand grinding; lapping and polishing (grinding with extremely fine grits to create ultrasmooth surfaces); honing; and disc grinding.
- grinding machine
grinding machine
Powers a grinding wheel or other abrasive tool for the purpose of removing metal and finishing workpieces to close tolerances. Provides smooth, square, parallel and accurate workpiece surfaces. When ultrasmooth surfaces and finishes on the order of microns are required, lapping and honing machines (precision grinders that run abrasives with extremely fine, uniform grits) are used. In its “finishing” role, the grinder is perhaps the most widely used machine tool. Various styles are available: bench and pedestal grinders for sharpening lathe bits and drills; surface grinders for producing square, parallel, smooth and accurate parts; cylindrical and centerless grinders; center-hole grinders; form grinders; facemill and endmill grinders; gear-cutting grinders; jig grinders; abrasive belt (backstand, swing-frame, belt-roll) grinders; tool and cutter grinders for sharpening and resharpening cutting tools; carbide grinders; hand-held die grinders; and abrasive cutoff saws.
- grinding wheel
grinding wheel
Wheel formed from abrasive material mixed in a suitable matrix. Takes a variety of shapes but falls into two basic categories: one that cuts on its periphery, as in reciprocating grinding, and one that cuts on its side or face, as in tool and cutter grinding.
- just-in-time ( JIT)
just-in-time ( JIT)
Philosophy based on identifying, then removing, impediments to productivity. Applies to machining processes, inventory control, rejects, changeover time and other elements affecting production.
- lathe
lathe
Turning machine capable of sawing, milling, grinding, gear-cutting, drilling, reaming, boring, threading, facing, chamfering, grooving, knurling, spinning, parting, necking, taper-cutting, and cam- and eccentric-cutting, as well as step- and straight-turning. Comes in a variety of forms, ranging from manual to semiautomatic to fully automatic, with major types being engine lathes, turning and contouring lathes, turret lathes and numerical-control lathes. The engine lathe consists of a headstock and spindle, tailstock, bed, carriage (complete with apron) and cross slides. Features include gear- (speed) and feed-selector levers, toolpost, compound rest, lead screw and reversing lead screw, threading dial and rapid-traverse lever. Special lathe types include through-the-spindle, camshaft and crankshaft, brake drum and rotor, spinning and gun-barrel machines. Toolroom and bench lathes are used for precision work; the former for tool-and-die work and similar tasks, the latter for small workpieces (instruments, watches), normally without a power feed. Models are typically designated according to their “swing,” or the largest-diameter workpiece that can be rotated; bed length, or the distance between centers; and horsepower generated. See turning machine.
- lubricity
lubricity
Measure of the relative efficiency with which a cutting fluid or lubricant reduces friction between surfaces.
- outer diameter ( OD)
outer diameter ( OD)
Dimension that defines the exterior diameter of a cylindrical or round part. See ID, inner diameter.
- stiffness
stiffness
1. Ability of a material or part to resist elastic deflection. 2. The rate of stress with respect to strain; the greater the stress required to produce a given strain, the stiffer the material is said to be. See dynamic stiffness; static stiffness.
- superalloys
superalloys
Tough, difficult-to-machine alloys; includes Hastelloy, Inconel and Monel. Many are nickel-base metals.
- tolerance
tolerance
Minimum and maximum amount a workpiece dimension is allowed to vary from a set standard and still be acceptable.