As vice president of waterjet machine tool builder Flow International Corp., Chip Burnham frequently debunks common misconceptions about waterjets. One is that technological advancements have made the equipment more flexible and versatile over the years. “The waterjet has always been very flexible and versatile,” he countered. “Most consider it the most flexible and versatile machine tool available.”
This includes the waterjet’s ability to precisely cut nearly any material—from paper and food to brittle stone and the nastiest superalloys—in a host of environments, including short-run job shops, R&D labs, contract manufacturers and high-volume OEMs. A pure waterjet is suitable for cutting software materials, while an abrasive waterjet cuts hard materials, and most waterjet machines can perform either function.
Video presentation from Flow International Corp. offers overview of the waterjet machining process.
Burnham came to this realization when wanting to work with a pedestal robot for his senior project as an undergraduate in the mid-1980s at the University of Rhode Island. “I finagled my way into the lab that had the robot and, lo and behold, a waterjet was attached to it,” he said. “Shortly after that the robot became second to the waterjet for me.”
Flow had donated the waterjet to the university to promote “this whole intriguing technology,” Burnham said.
Take it Easy
What has changed is the ease of programming and operating an abrasive waterjet machine, according to Burnham. This enables someone with average rather than advanced skill to set up and cut a workpiece.
Nonetheless, to take advantage of a waterjet’s inherent versatility, high-end systems have advanced controls and built-in knowledge to take the guesswork out of waterjet programming and operation. “The programmer enters the pattern, material type, material thickness and desired quality level, and the machine knows how to select the right speeds and lead-ins and lead-outs without needing a series of test cuts,” Burnham said. “The easier the programming the better, since finding great programmers gets tougher and tougher.”
Process software plays a key role in transferring the knowledge a waterjet machine tool builder has acquired to end users—especially new ones, added Jeff Schibley, Midwest regional manager for St. Michael, Minn.-based Jet Edge Inc. “Regardless of whether you processed 1 "-thick steel in the past, the software instructs the machine that these are the parameters it will operate at and create this quality,” he said. “Now, the customer doesn’t have to have knowledge of abrasive waterjetting to run that machine.”
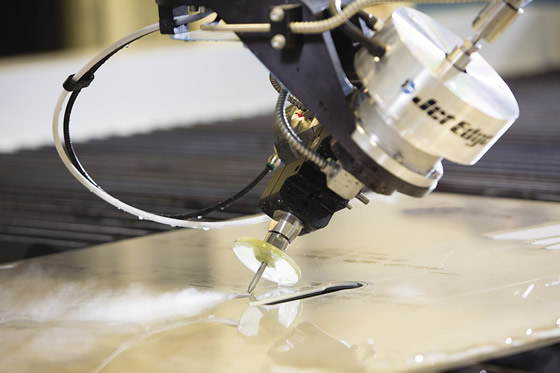
An EDGE X-5 5-axis waterjet system from Jet Edge can produce complex contours. Image courtesy Jet Edge.
Software that provides tutorials can also prove beneficial. Michael Ruppenthal, vice president North American Sales for OMAX Corp., Kent, Wash., gave the example of using a rotary axis on a waterjet machine to cut or create letters around a pipe. “Programming that job used to be difficult. You needed a highly educated programmer and machinist to figure out how to waterjet cut it,” he said. “Now all I need to do is tell the computer the diameter and thickness of the pipe and the size of the feature and the software does everything else.”
Technology Transfer
Along with making abrasive waterjet machines easier to run, builders frequently add features to entry-level equipment previously found only on higher-end offerings. “It’s what I call a ‘technology waterfall,’ which gradually happens in all machine tools,” Burnham said.
He noted Flow’s most affordable line, the Mach 2 series, has capabilities previously available only on the more-advanced Mach 3 and 4 series. For example, an entry-level machine, which starts at about $90,000, came with a 60,000-psi pump a few years ago and now can have a HyperJet 94,000-psi pump to cut faster, and instead of just having a conventional cutting head fixed perpendicular to the workpiece, the machine can now carry the company’s Dynamic Waterjet head.
OMAX has followed a similar path. Ruppenthal pointed out that the company carries two brands: OMAX and Maxiem, the latter being a standard entry-level line. “Maxiem has transitioned into an à la carte offering more so than the OMAX premium line, where you get the features even though you may not want each one for your application,” he said. “With Maxiem, you can put on almost all the same features that you can on an OMAX.”
This includes automatic abrasive feeding, which previously required manual delivery of abrasive to the cutting head, and automatic abrasive removal. Ruppenthal explained that abrasive, typically garnet, fills a catcher tank at a rate of approximately 1 lb. (0.45 kg) per minute, and the abrasive must be periodically removed via a shovel or sucker truck when a machine doesn’t have an automatic removal system. The system takes the solid material out of the tank and puts it in a disposal container, eliminating the need to shut down the machine and empty it. “More importantly, it saves somebody’s back from having to shovel that,” he said. “It’s the accessory we sell most often after the sale.”
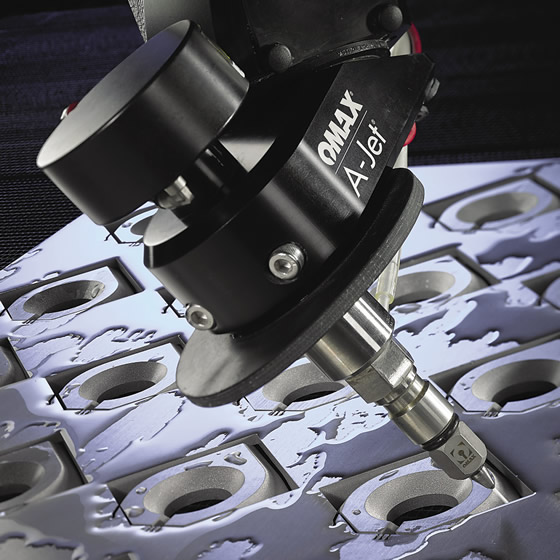
The A-Jet from OMAX is a software-controlled, multiple-axis cutting head that expands the versatility of a waterjet machine by being able to produce a variety of features, such as beveled edges, angled sides and countersinks. Image courtesy OMAX.
Ruppenthal added that having the ability to raise and lower the water level and enable cutting underwater is another recent addition to the standard entry-level line. Cutting underwater increases workplace hygiene by keeping the shop cleaner and reducing worker fatigue, according to Ruppenthal. “The quieter the machine is, the less it affects the person standing around or near it all day long.”
In addition, a company that purchases either brand of machine can have 5-axis capability. Besides being able to remove taper, Ruppenthal noted that capability enables producing a part with complex contours, such as a turbine blade, and generating helpful features, such as a weld-prep bevel. “If you’re a job shop, it opens up business opportunities that you didn’t have before.”
Nonetheless, the vast majority of waterjet work is for flat-plate cutting or flat-plate bevel cutting rather than full 3D machining, including at part manufacturers with 5-axis waterjets, according to Burnham. Therefore, shops need a waterjet that can be easily programmed and used to execute bevels and K-bevels. “True 5-axis, 3D cutting requires your shop to have programmers and operators who can handle that type of work,” he said.
Not all builders introduce features found predominantly on higher-end machines to entry-level offerings. “When you’re building machines, you don’t add features and reduce the cost,” Jet Edge’s Schibley said. “You add features and increase the cost.”
Some shops are looking to bring the waterjet work in-house that they previously outsourced, but they don’t necessarily have 40 hours of work for machine. For this situation, Jet Edge offers the Boss-Cutter line. The machine has a 59 "×59 " (1.51m) work envelope. “If the customer is used to buying 4 '×4 ' or 5 '×5 ' material, it will easily fit within the cutting tank of that work envelope,” Schibley said. He added that larger work envelopes are available for high-volume customers that prefer to buy larger full sheets at the most economical rate and avoid the saw cut and corresponding mark up from a metal service center.
Pressure Point
When helping a customer specify an abrasive waterjet machine, the first question is about the size of sheet to be cut, followed by the thickness of the material, the expected level of accuracy and whether a taper-eliminating cutting head is required, Ruppenthal said. “If you’re a fab shop, taper might be completely acceptable. Or if you’re going to put everything on a machining center after you cut it on the waterjet, some slight taper that the waterjet puts into the part might be OK.”
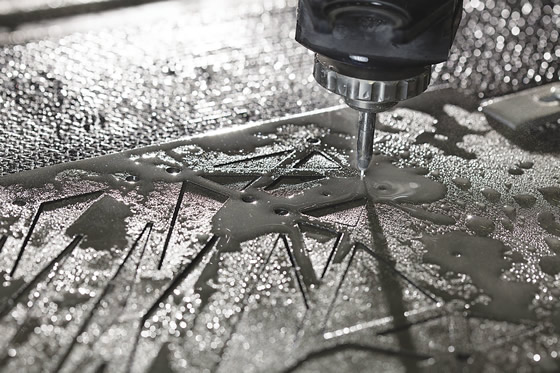
A Flow Mach 2c waterjet machine with a Dynamic Waterjet head cuts 7⁄8 "-thick carbon fiber. Image courtesy Flow International.
Ruppenthal added that a “dream” waterjet application involves the latter, particularly when processing difficult-to-machine workpieces, such as Inconel, Hastelloy and titanium, which might require 500 passes or more. After waterjet machining such a workpiece, say for 45 minutes, to near-net shape, the part will require significantly less time on a machining center.
In addition, waterjetting a workpiece to within 0.002 " to 0.005 " (0.051mm to 0.127mm) of the specified size for the various features can also enable a manufacturer to eliminate the need for heat treatment after machining and prior to finishing, he noted. Instead, it can obtain hardened material from the mill and EDM or machine the features that need tighter tolerances after waterjetting them. “A waterjet is not going to replace an EDM or CNC machine, but it is a great complementary tool.”
Another factor when deciding on a waterjet machine is pump pressure. The higher the pressure, the higher the productivity, because higher pressure is inherently more efficient, according to Burnham.
Waterjet machines use two types of pumps: rotary direct drive and linear intensifier. The design of a direct-drive pump enables it to deliver pressures up to 60,000 psi (4,137 bar), while an intensifier pump tops out at more than 90,000 psi (6,205 bar). Flow offers both varieties, including the Hyplex Prime direct-drive pump (55,000 psi, or 3,792 bar) and the HyperJet intensifier pump (94,000 psi, or 6,481 bar).
“We will typically advise customers that the best way to get productivity and ease of use is to take the pressure up and cut faster with one head than trying to put multiple heads on,” Burnham said.
He added that, while intensifiers have longer maintenance intervals and are better suited for applications where the cutting head will have a lot of on/off cycles, direct drives are smaller and more electrically efficient. About 80 percent of the installed waterjets have intensifier pumps.
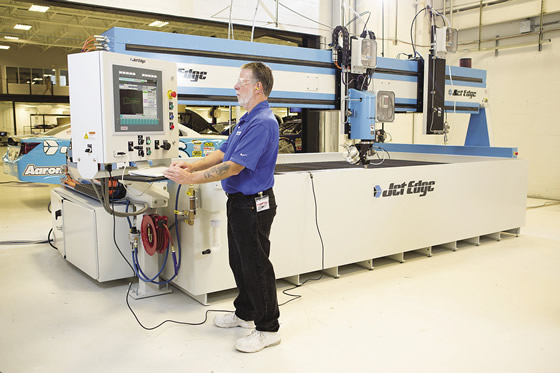
A waterjet machine can help maximize the efficiency of the machinists who run machining centers by premachining parts. Image courtesy Jet Edge.
Jet Edge also offers both pump types, but Schibley noted the extreme intensifier that operates at 90,000 psi is primarily for cutting materials thicker than 1 " (25.4mm) because it cuts quicker. “We can reduce the amount of garnet utilized in the water stream by accelerating it with higher pressures,” he said. “In some instances, we can enhance productivity up to 40 percent.”
However, Schibley cautioned that as pressure increases, maintenance costs rise because metal parts experience more fatigue from the higher pressure and, therefore, require more frequent replacement. “When we enhance pressure, waterjetting becomes a self-destructing process.”
Rather than increasing the pressure in a single cutting head, Schibley recommends boosting throughput by cutting with two heads at lower pressures. For example, when producing a high-quality cut in a ½ "-thick piece of aluminum, two heads at 100-hp and 55,000-psi will yield 20 ipm (508 mm/min.), while one 100-hp, 90,000-psi head will provide a cutting speed of 13.4 ipm (340.4 mm/min.).
Some shops might contemplate stacking sheets of material to increase the cutting speed, but Schibley pointed out that doubling the workpiece thickness reduces the cutting speed 60 percent. So, when producing the same high-quality cut in a ½ "-thick piece of aluminum as his previous example, the cutting speed for one 55,000-psi head will drop from 10 ipm to 4 ipm (101.6mm) when cutting two aluminum sheets that equal 1 " in thickness. “The only reason for stacking is to minimize handling time,” he said.
Don’t Believe the Hype(r)
OMAX, on the other hand, stays in the ultrahigh-pressure range and avoids the hyper, or extreme, pressure-range above 75,000 psi (5,171 bar) by only offering waterjet machines with direct-drive pumps. “Pressure in and of itself is great, but like everything in nature, nothing comes for free,” Ruppenthal said. “If you increase pressure, you typically have to decrease flow rate. Our philosophy is to try and find a happy medium where we get the most horsepower at the nozzle to push each particle of abrasive out.”
He added that direct drives have “an unfair advantage” of being more efficient than intensifiers, with an efficiency rating of 85 to 90 percent. Because it has a hydraulic system, an intensifier pump loses about 30 percent of the energy of the electric motor because of the hydraulic system’s inefficiencies. “As a result, we’re able to do more work at a lower pressure.”
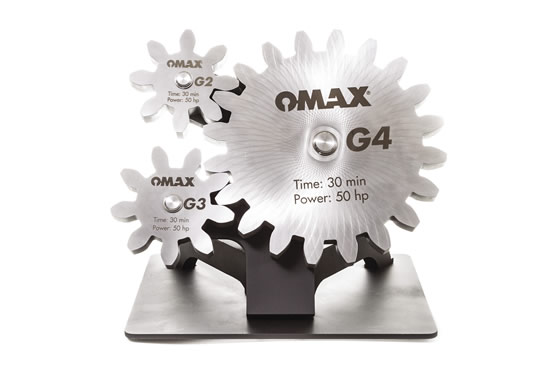
The only difference in the production of these three gears was the OMAX software that was used to control the jet, with the second-generation software for G2, the third-generation software for G3 and the latest, fourth-generation software for G4. Image courtesy OMAX.
To illustrate the company’s ability to do that with the assistance of its software that controls the jet, the OMAX exhibit at this year’s EASTEC trade show included a display with three gears. Ruppenthal explained that one gear was marked G2 for the company’s second generation cutting model, the G3 gear was larger and represented the third generation model, and the G4 gear was drastically larger than the others and showcased the new fourth generation cutting model. “The only difference between the sizes of those gears is the software, the way we control the jet,” he said. “They were cut in the same amount of time and with the same amount of abrasive and the same amount of horsepower. The latest software version allows dramatically faster cutting.”
While a waterjet cutting machine has always been versatile, that doesn’t mean technological developments haven’t enhanced that versatility while removing the guesswork and creating more market opportunities for job shops. “That versatility isn’t as valuable if your waterjet doesn’t come equipped with an intelligent control that knows how to cut the materials,” Flow’s Burnham said. CTE
About the Author: Alan Richter is editor of CTE. Contact him at (847) 714-0175 or [email protected].
Manufacturer donates waterjet to local college
Smalley Steel Ring Co. has donated an OMAX 2652 abrasive waterjet machining center to the College of Lake County. Headquartered in nearby Lake Zurich, Ill., Smalley manufactures retaining rings and wave springs. The waterjet machine is the college’s first and reportedly broadens its CNC/machine tool trade department’s ability to offer the waterjet technology skills sought by many employers recruiting CLC graduates, including Smalley. The cantilever-style machine has a 5 '9 "×2 '6 " (1.75m × 0.76m) table and can achieve tolerances as tight as ±0.001 " (±0.025mm).
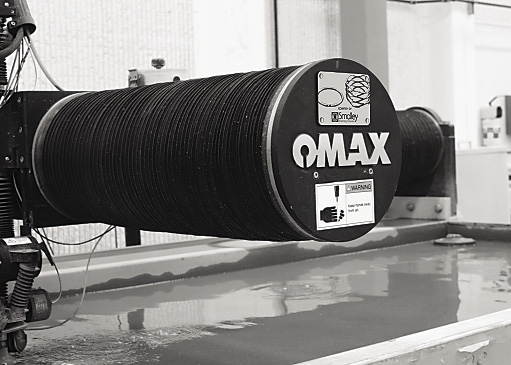
To help students learn about waterjet technology, Smalley Steel Ring donated an OMAX 2652 abrasive waterjet machine to the College of Lake County. Image courtesy OMAX.
Jeff Hines, department chairman for CNC programming at the college, plans to integrate the machine into several courses, including fabrication, wire EDM and welding, beginning in the fall. “The addition of waterjet technology to our program will give students a stronger skills and training portfolio when they complete their degrees, which now includes a basic understanding of waterjet and how to safely operate the machine.”
“With the addition of this machine, CLC is one of the few schools with a waterjet machining center in its classroom setting, which gives these students a huge advantage,” said Tim Doran, owner of OMAX distributor Tristate Machinery Inc., Wheeling, Ill., and a member of CLC’s career advisory committee for manufacturing.
The partnership with the college is a win-win situation, said Michael Greenhill, president of Smalley. “Students and instructors now have access to this advanced technology, and we hope some of the well-trained students might become future employees of Smalley,” he said.
Contributors
Flow International Corp.
(800) 446-3569
www.flowwaterjet.com
Jet Edge Inc.
(800) 538-3343
www.jetedge.com
OMAX Corp.
(253) 872-2300
www.omax.com
Related Glossary Terms
- abrasive
abrasive
Substance used for grinding, honing, lapping, superfinishing and polishing. Examples include garnet, emery, corundum, silicon carbide, cubic boron nitride and diamond in various grit sizes.
- abrasive waterjet ( AWJ)
abrasive waterjet ( AWJ)
System that uses high-pressure waterjets in combination with a slurry of fine abrasive grains to machine materials. See waterjet cutting.
- centers
centers
Cone-shaped pins that support a workpiece by one or two ends during machining. The centers fit into holes drilled in the workpiece ends. Centers that turn with the workpiece are called “live” centers; those that do not are called “dead” centers.
- computer numerical control ( CNC)
computer numerical control ( CNC)
Microprocessor-based controller dedicated to a machine tool that permits the creation or modification of parts. Programmed numerical control activates the machine’s servos and spindle drives and controls the various machining operations. See DNC, direct numerical control; NC, numerical control.
- cutting speed
cutting speed
Tangential velocity on the surface of the tool or workpiece at the cutting interface. The formula for cutting speed (sfm) is tool diameter 5 0.26 5 spindle speed (rpm). The formula for feed per tooth (fpt) is table feed (ipm)/number of flutes/spindle speed (rpm). The formula for spindle speed (rpm) is cutting speed (sfm) 5 3.82/tool diameter. The formula for table feed (ipm) is feed per tooth (ftp) 5 number of tool flutes 5 spindle speed (rpm).
- electrical-discharge machining ( EDM)
electrical-discharge machining ( EDM)
Process that vaporizes conductive materials by controlled application of pulsed electrical current that flows between a workpiece and electrode (tool) in a dielectric fluid. Permits machining shapes to tight accuracies without the internal stresses conventional machining often generates. Useful in diemaking.
- fatigue
fatigue
Phenomenon leading to fracture under repeated or fluctuating stresses having a maximum value less than the tensile strength of the material. Fatigue fractures are progressive, beginning as minute cracks that grow under the action of the fluctuating stress.
- inches per minute ( ipm)
inches per minute ( ipm)
Value that refers to how far the workpiece or cutter advances linearly in 1 minute, defined as: ipm = ipt 5 number of effective teeth 5 rpm. Also known as the table feed or machine feed.
- machining center
machining center
CNC machine tool capable of drilling, reaming, tapping, milling and boring. Normally comes with an automatic toolchanger. See automatic toolchanger.
- milling machine ( mill)
milling machine ( mill)
Runs endmills and arbor-mounted milling cutters. Features include a head with a spindle that drives the cutters; a column, knee and table that provide motion in the three Cartesian axes; and a base that supports the components and houses the cutting-fluid pump and reservoir. The work is mounted on the table and fed into the rotating cutter or endmill to accomplish the milling steps; vertical milling machines also feed endmills into the work by means of a spindle-mounted quill. Models range from small manual machines to big bed-type and duplex mills. All take one of three basic forms: vertical, horizontal or convertible horizontal/vertical. Vertical machines may be knee-type (the table is mounted on a knee that can be elevated) or bed-type (the table is securely supported and only moves horizontally). In general, horizontal machines are bigger and more powerful, while vertical machines are lighter but more versatile and easier to set up and operate.
- sawing machine ( saw)
sawing machine ( saw)
Machine designed to use a serrated-tooth blade to cut metal or other material. Comes in a wide variety of styles but takes one of four basic forms: hacksaw (a simple, rugged machine that uses a reciprocating motion to part metal or other material); cold or circular saw (powers a circular blade that cuts structural materials); bandsaw (runs an endless band; the two basic types are cutoff and contour band machines, which cut intricate contours and shapes); and abrasive cutoff saw (similar in appearance to the cold saw, but uses an abrasive disc that rotates at high speeds rather than a blade with serrated teeth).
- waterjet cutting
waterjet cutting
Fine, high-pressure (up to 50,000 psi or greater), high-velocity jet of water directed by a small nozzle to cut material. Velocity of the stream can exceed twice the speed of sound. Nozzle opening ranges from between 0.004" to 0.016" (0.l0mm to 0.41mm), producing a very narrow kerf. See AWJ, abrasive waterjet.
- wire EDM
wire EDM
Process similar to ram electrical-discharge machining except a small-diameter copper or brass wire is used as a traveling electrode. Usually used in conjunction with a CNC and only works when a part is to be cut completely through. A common analogy is wire electrical-discharge machining is like an ultraprecise, electrical, contour-sawing operation.
- work envelope
work envelope
Cube, sphere, cylinder or other physical space within which the cutting tool is capable of reaching.