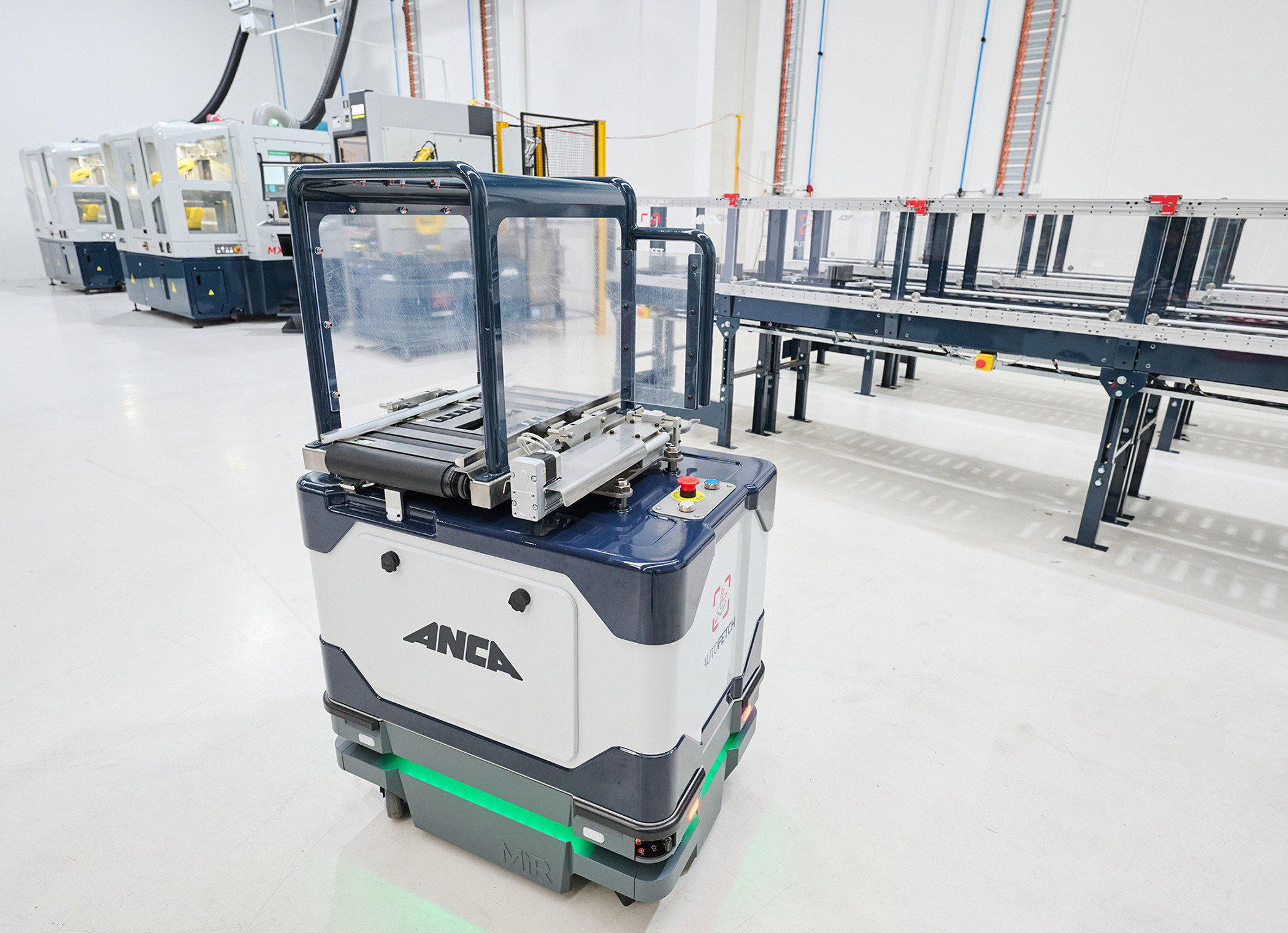
At IMTS 2024, ANCA CNC Machines has much to offer the market and is also celebrating several highpoints in its storied history. In addition to the introduction of an advanced, high-precision tool grinder, the MicroX ULTRA, as well as the next generation of integrated manufacturing technology, AIMS Connect, ANCA will further highlight its commitment to offering the best-in-class solutions for tool grinding production, start to finish, with the celebration of its 50th anniversary in business (1974-2024) and the recent opening of its newest Tech Center in Temecula, California to serve its fast-growing West Coast market base.
ANCA, a global leader in CNC grinding machines and automated manufacturing technologies, celebrates its 50th anniversary, displaying its latest innovations at IMTS. As a mainstay in the precision tool industry, ANCA will showcase its commitment to excellence through new products, cutting-edge technologies and exciting business events, including its popular Tool of the Year and Female Machinist of the Year awards. The anniversary showcase addresses manufacturers’ needs for highest quality and lowest cost tools, plus freeing operators from repetitive and non-value-add tasks to make room for progress and creativity.
Pat Boland, ANCA co-founder, remarks, "For 50 years, ANCA has been on a journey to change the shape of the cutting tool industry. To celebrate our 50th anniversary, we look forward to meeting with our customers and partners at IMTS. As innovation has motivated us throughout our history, new products and developments will be at the center of our celebrations. ANCA’s future is exciting, we are focused on continuing to invent and deliver groundbreaking technology to help take cutting tool production into areas not previously thought possible.”
Edmund Boland, ANCA CNC Machines General Manager, adds, "IMTS is the major global event in this milestone year for our company, so it's thrilling to showcase our latest products and technologies for high performance cutting tools produced with optimized efficiency and cost. Building on ANCA’s heritage of producing industry-leading software, the latest release of our signature ToolRoom software, RN35, takes cycle time optimization even further, elevating productivity – it’s the future of tool production.”
“ToolRoom and AIMS really pave the way for highly productive, autonomous production. Our investment in AIMS for connected and automated processes is our commitment to solving key challenges such as labor shortages and consistent production processes with smart, future-ready solutions. Our ULTRA technology has made a splash in the market, and now enables micro tool production, regrinding and small batch production with the MicroX and FX7 ULTRA,” notes Edmund.
50 years of innovation and “thinking outside of the box”
ANCA started with a minicomputer and teletype installed at co-founder Pat Boland’s home, followed by a CNC and then the design and manufacture of machine tools with co-founder Pat McCluskey. Throughout the years, ANCA has brought significant advantages to the industry with pioneering innovations like the first touch probe, soft axes and 3D simulation.
Naturally, software and automation are key highlights of ANCA’s anniversary innovation portfolio. The latest version of ANCA's ToolRoom software, RN35, offers:
- Average performance increase of up to 20% with advanced features and functions, optimizing feedrate, improving cycle time and surface finish, while extending wheel life.
- New developments including the integration of material removal rate calculations, allowing manufacturers to automatically set parameters for constant removal rates, plus air-time reduction.
- Statistical Process Control (SPC) software for statistical analysis and evaluation of manufactured part characteristics streamlines manufacturing processes.
- Profile fluting further enhancing the popular flute from solid feature of the proprietary ANCA software.
Experts will present these and other upgrades to IMTS visitors, plus further exciting news in CIM3D simulation software.
The Future of Automation in Tool Production IS here today…AIMS
The ANCA Automated Manufacturing System (AIMS) is a highly integrated, advanced automation system that brings together machining, metrology and materials handling plus data management in a leading-edge ecosystem for a lights-out production of tools used in myriad industries.
ANCA's AIMS (ANCA Integrated Manufacturing System) is the smart manufacturing solution for cutting tool production, enabling manufacturers to connect, automate and create like never before. The modular system comprises hardware and software components for automated, closed loop manufacturing. AIMS Server controls production processes and AutoComp, the intelligent compensation module maintains part quality automatically, while the new AIMS Connect function covers job management.
With AIMS Connect, recently debuted at GrindingHub in Germany, visitors can experience firsthand the power of digital production control and modular automation, now available for existing installations. The system has proven in the field that it empowers manufacturers to explore new opportunities, products and features while maximizing productivity and quality.
AIMS is growing in popularity, as it enables shops of all sizes plus huge production departments the flexibility to integrate machining, metrology and materials handling into a unified ecosystem with full data capture and management capabilities.
Machines and technology for highest quality and lowest cost tools
ANCA’s GCX machine and gear tool technology is set to redefine the production of skiving cutters with a turnkey solution package. To address the complexity of gear tool manufacturing, this offering includes features for the design of gear cutting tools, manufacturing and integrated tool measurement, as well as providing the skiving machine setup parameters.
IMTS visitors will witness live how this configuration enables short setup times, simulation and monitoring, plus quality enhancing features like the ANCA Motor Temperature Control (MTC) and integrated balancing (iBalance) for unparalleled longtime grinding profile accuracy within +/-0.0015mm. This turnkey package facilitates easy entry into the gear tools sector while ensuring top-quality results.
ULTRA Technology: the platform for highest precision and micro tool work
Revolutionary ULTRA technology combines nanometer control, servo-controlled algorithms and mechanical stiffness upgrades to achieve unprecedented accuracy. The FX7 ULTRA and MicroX ULTRA demonstrate ANCA's commitment to precision, enabling continuous batch production down to 0.03mm and setting new standards in tool manufacturing.
The MicroX ULTRA premiered at EMO 2023 and was released to the market at GrindingHub, giving micro tool manufacturers all the advantages of the ULTRA technology and ANCA’s Machine Intelligence in a unit tailored to this application. As the only micro tool grinder with nanometer control, optimized mechanical layout and axes travel, integrated tool measurement and progressive automation, this six-axis grinder is the ideal solution for volume production of tools down to 0.03mm.
Customer-centric solutions enable enhancements
The new EPX-SF stream finishing machine was released to the market at GrindingHub. ANCA’s advanced edge preparation and surface finishing solution addresses productivity targets, delivers superior IP cutting tool performance and succeeds in precision-critical industries – in a design that’s ready to be integrated in automated tool manufacturing systems. With 11-axis automation and smart recipe fine-tuning, the machine is engineered by tool experts to optimize media utilization while providing precise edge control. The machine has the capability to reduce edge roughness to under 100 nm and refine edge radii to mere microns with controllable K-factor, achieving nano-smooth surfaces and micron-honed edges in record time.
The EPX-SF’s cyclic mode with pulse rotation serves as a potent defense against surface burrs and edge imperfections. With adjustable positive and negative angles, the EPX-SF spindle traverses the optimal cutting path, optimizing potential chip flow and reducing the surface roughness of the cutting workpiece. Within ANCA’s automation ecosystem, the EPX-SF seamlessly integrates into production lines, operating autonomously with robotic assistance round the clock for tool loading/unloading.
The CPX blank preparation machine is a prime example of how to include the voice of the customer in product development. Tool manufacturers around the world were asked and given their ideal solution for blanks with high material removal rates, application flexibility and integrated quality control. With features like statistical process control and top surface finishes below 0.2Ra, manufacturers can achieve high productivity at minimal cost with the CPX Linear. Some further application capability will be introduced at IMTS.
ANCA invites visitors to join us at IMTS Booth 237406 to experience firsthand the future of tool manufacturing.
Related Glossary Terms
- computer numerical control ( CNC)
computer numerical control ( CNC)
Microprocessor-based controller dedicated to a machine tool that permits the creation or modification of parts. Programmed numerical control activates the machine’s servos and spindle drives and controls the various machining operations. See DNC, direct numerical control; NC, numerical control.
- edge preparation
edge preparation
Conditioning of the cutting edge, such as a honing or chamfering, to make it stronger and less susceptible to chipping. A chamfer is a bevel on the tool’s cutting edge; the angle is measured from the cutting face downward and generally varies from 25° to 45°. Honing is the process of rounding or blunting the cutting edge with abrasives, either manually or mechanically.
- fluting
fluting
Cutting straight or spiral grooves in drills, endmills, reamers and taps to improve cutting action and remove chips.
- grinding
grinding
Machining operation in which material is removed from the workpiece by a powered abrasive wheel, stone, belt, paste, sheet, compound, slurry, etc. Takes various forms: surface grinding (creates flat and/or squared surfaces); cylindrical grinding (for external cylindrical and tapered shapes, fillets, undercuts, etc.); centerless grinding; chamfering; thread and form grinding; tool and cutter grinding; offhand grinding; lapping and polishing (grinding with extremely fine grits to create ultrasmooth surfaces); honing; and disc grinding.
- materials handling
materials handling
Methods, equipment and systems for conveying materials to various machines and processing areas and for transferring finished parts to assembly, packaging and shipping areas.
- metrology
metrology
Science of measurement; the principles on which precision machining, quality control and inspection are based. See precision machining, measurement.
- process control
process control
Method of monitoring a process. Relates to electronic hardware and instrumentation used in automated process control. See in-process gaging, inspection; SPC, statistical process control.
- quality assurance ( quality control)
quality assurance ( quality control)
Terms denoting a formal program for monitoring product quality. The denotations are the same, but QC typically connotes a more traditional postmachining inspection system, while QA implies a more comprehensive approach, with emphasis on “total quality,” broad quality principles, statistical process control and other statistical methods.
- statistical process control ( SPC)
statistical process control ( SPC)
Statistical techniques to measure and analyze the extent to which a process deviates from a set standard.
- stiffness
stiffness
1. Ability of a material or part to resist elastic deflection. 2. The rate of stress with respect to strain; the greater the stress required to produce a given strain, the stiffer the material is said to be. See dynamic stiffness; static stiffness.