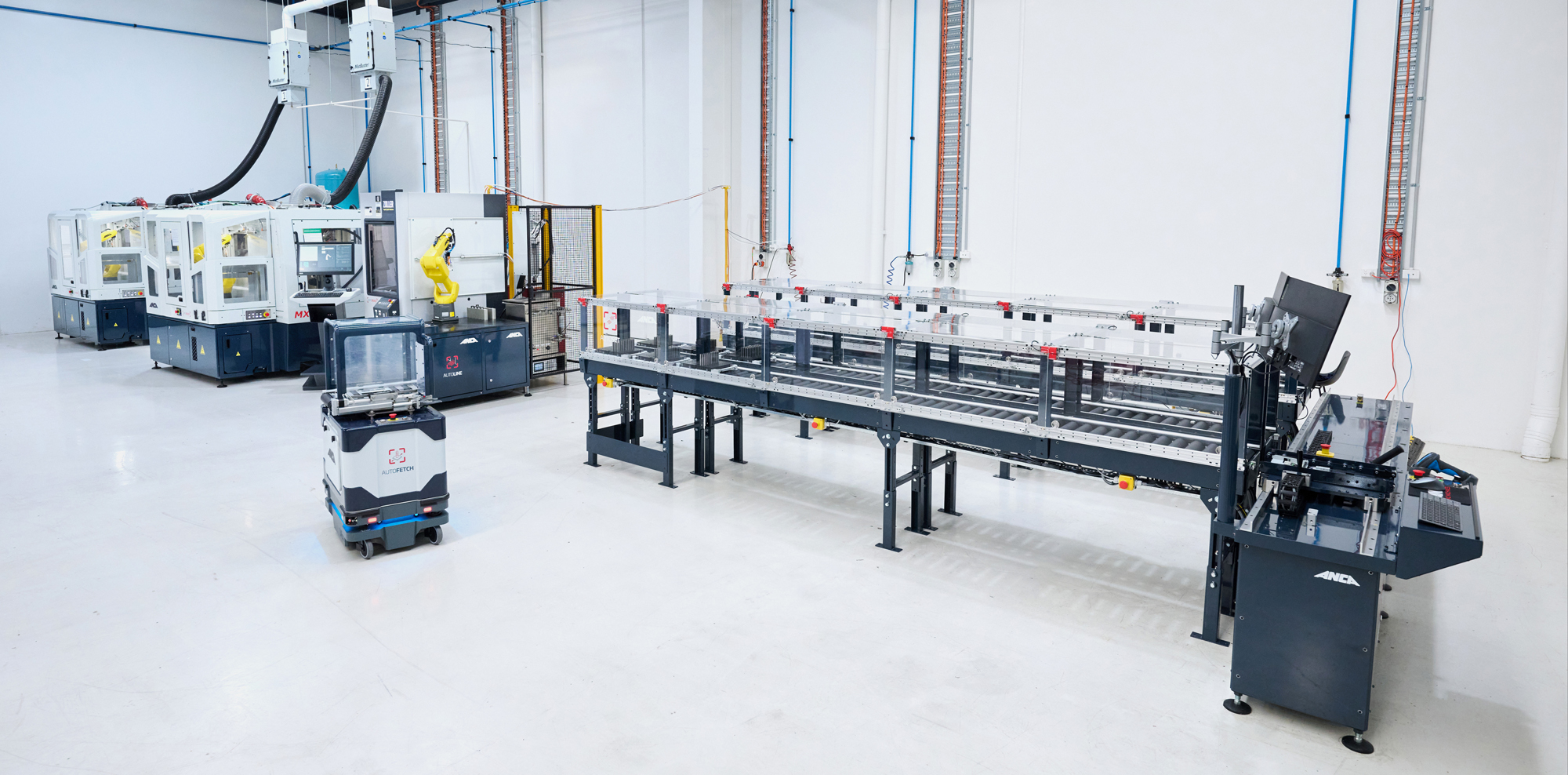
CNC grinding technology company ANCA will showcase its latest products and industry-specific grinding and automation solutions at EMO (Booth F52, Hall 6) in Hanover, Germany, in September.0
The winner of the Tool of the Year competition will be announced live Wednesday, Sept. 20 at 4.30 pm (GMT). Attendees are invited to join the celebrations and witness the range of cutting tools.
Edmund Boland, ANCA CNC Machines general manager said, “We are excited to bring not one but several world premieres to EMO, promising premium value, higher productivity and extended capabilities. Visitors can see firsthand ANCA’s latest technology that spans tool precision, integrated manufacturing systems, industry focus applications and optimization across the process chain.”
Martin Winterstein, general manager of ANCA Europe said, “EMO is the global leading manufacturing technology show, it is where the current market trends and innovations are on display. Our setup in Hanover really shows hands-on opportunities for tool manufacturers, with new application and automation solutions tailored to industries’ needs. I am excited to show visitors our enhanced portfolio to include micro tools with the FX ULTRA, according to the high demand from this growing segment. Experts from ANCA and our partners will be on-site to show and discuss individual requirements at the booth.”
ULTRA value
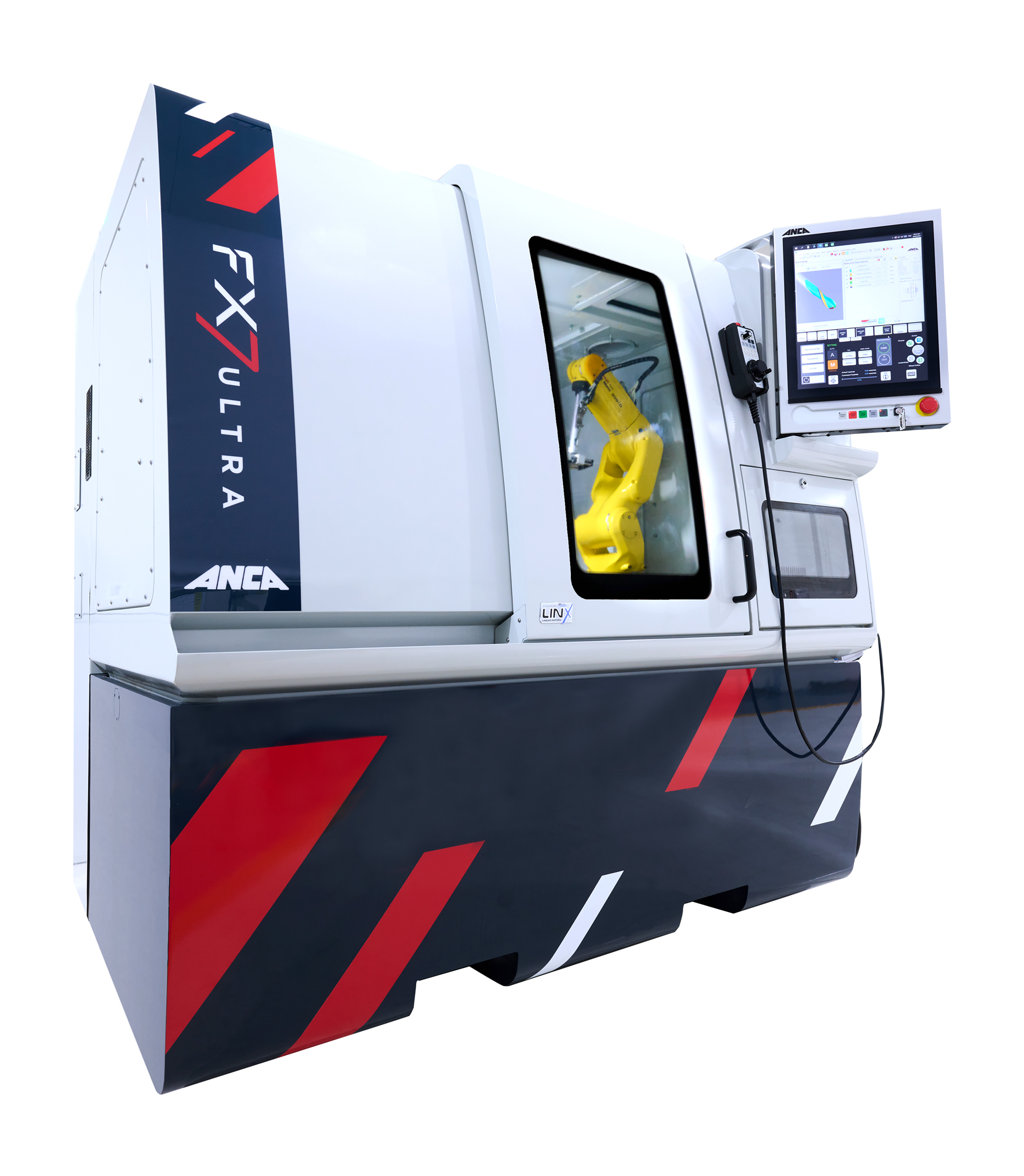
Years of continuous refinements at ANCA have made the ULTRA technology possible. The company says ANCA’s vertical integration is key to its success - where machines, controls, drives and precision components are all designed and manufactured in-house.
The ULTRA unit was introduced to the industry last year on the MX machine platform, it boasts the highest accuracy and quality cutting tools in the world. The MX7 ULTRA achieves one-nanometer axis resolution, and can maintain better than +/- 0.002mm line form accuracy of any profile which includes ballnose and corner radius endmills.
At EMO, visitors will find out how ANCA spreads the ULTRA advantages to further fields of application, including smaller batches, regrinding and tools with small diameters.
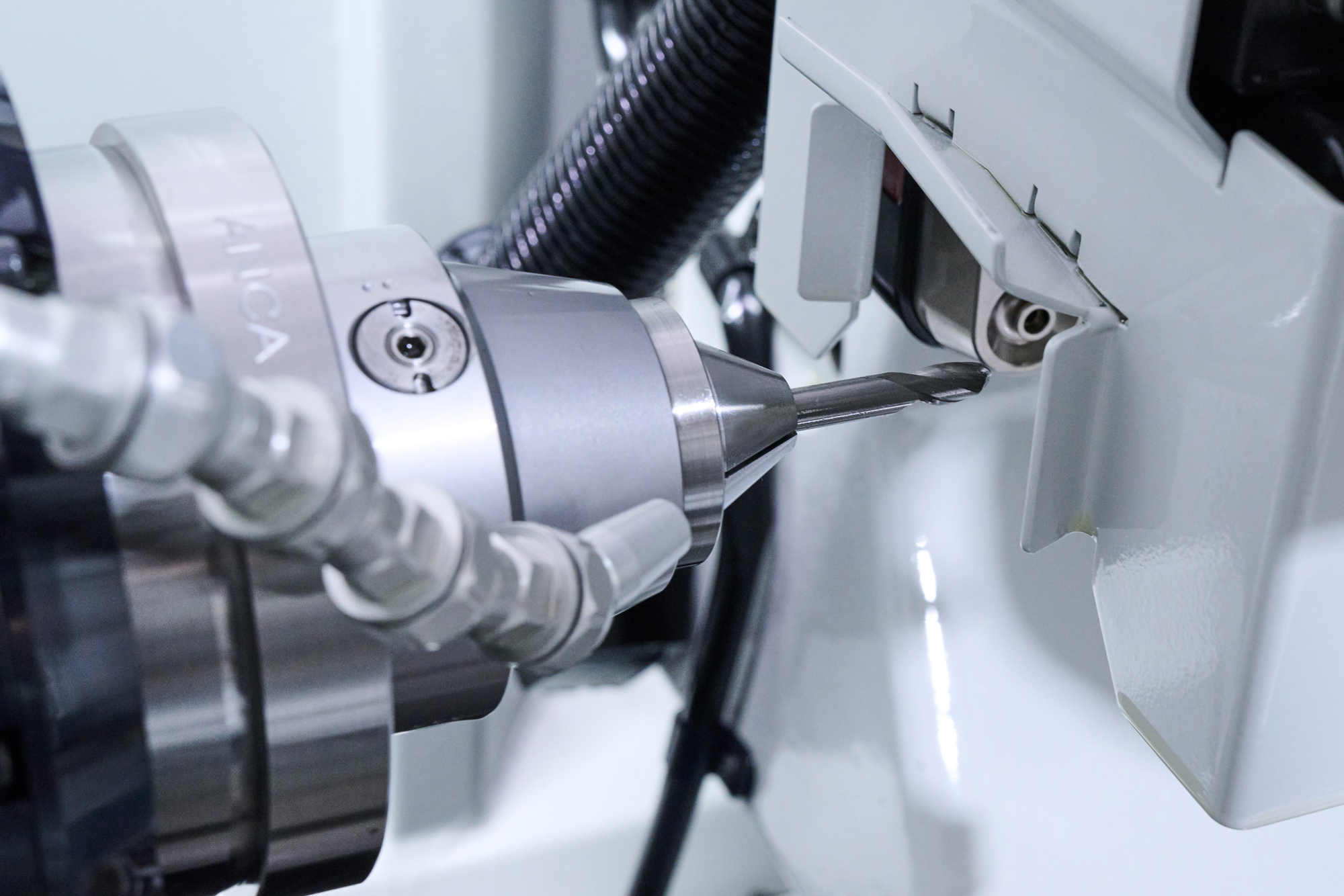
FX7 ULTRA
The FX7 ULTRA introduces several cutting-edge technologies, including ANCA’s nanometer control, that can achieve precision grinding for small and micro tools down to 0.1mm diameter.
New software, hardware and design features significantly improve surface finish, accuracy, and controlled runout, ensuring batch consistency from the first ground tool to the last. These advancements ensure that the FX7 ULTRA is the go-to solution for precision grinding in industries that rely on small tools, including electronics, telecommunications, medical devices, aerospace, automotive, diemold, and general machining.
Peel grinding combined with blanket grinding
From blank to a finished high-quality tool, all on one machine – ANCA’s single setup solution for complete machining of cutting tools will be demonstrated on the MX7 ULTRA at EMO.
Following a legacy of machine efficiency, this latest solution combines peel grinding and tool grinding on the one platform, enhanced with additional power to extend capability. The MX7 ULTRA's spindle power of 26kW can handle demanding tools like larger taper ballnose endmills, step drills, and aerospace components ranging from 0.1 to 25.4 mm. This leads to reduced cycle times and increased productivity. Short setup times, optional collet change and proven blanket grinding processes round out the capabilities.
The company says that by utilizing the latest innovations in peel grinding technology, ANCA guarantees exceptional stability, accuracy and value, all achieved on a single machine.
Unattended cutting tool production
ANCA has further developed its AIMS system for automated tool production. At EMO, visitors can see examples from the field, with systems’ operating completely unattended over an extended period as it manufacture tools.
The AIMS automation package is a modular and growing system, spanning across the tool production process. ANCA is set to include additional operations like blank preparation or laser marking in the automated process. The system’s intelligent design allows for progressive steps of automation, including an automated laser marking station AutoMarkX. The versatile laser marking station is tailored to meet the needs of tool manufacturers. It provides reliable and high-quality marking, ensuring traceability, identification, and branding of tools, while eliminating repetitive tasks to free up time for skilled staff, the company says.
The AutoMarkX’s new, retrofittable rotary workholding system allows for unlimited index marking around the tool, with automatic Z-axis focus and compatibility with tool shanks from 3 to 32mm. Moreover, the AIMS Autoline Basic, the standard interface for easy loading at the AutoMarkX enables customers to experience smoother material transfer between machines. By utilizing a manual trolley system, combined with AIMS pallet carriers, Autoline Basic streamlines the transfer of heavy tool pallets between machines, reducing labor-intensive processes.
Wide range of expertise
ANCA's expertise in grinding solutions extends to blank grinding and integrated complete machining of gear tools, including in-process measuring and compensation. The CPX blank preparation machine will feature productivity-enhancing features in Hannover, including automated loading of tools up to 32mm, a flip station for grinding from both ends, tailstock, and extensive probing enabling statistic process control. The machine has been designed to give users high material removal rates and save time and money with unattended production.
The rising demand of gear cutting tools has led ANCA to enhance its product program with the GCX, the turnkey solution for manufacturing and resharpening gear-cutting tools. The Integrated Gear Tool Measurement (IGTM) and ANCA’s expertise in grinding wheel dressing gives customers the benefit of full control over the high-precision skiving cutter grinding process. The company says its motto is first skiving cutter in tolerance, is the motto. ANCA’s widely spread area of grinding applications, can be covered with the versatile GCX and its numerous optional accessories like the LaserUltra for profile tools.
ANCA’s Cutting Tool Award
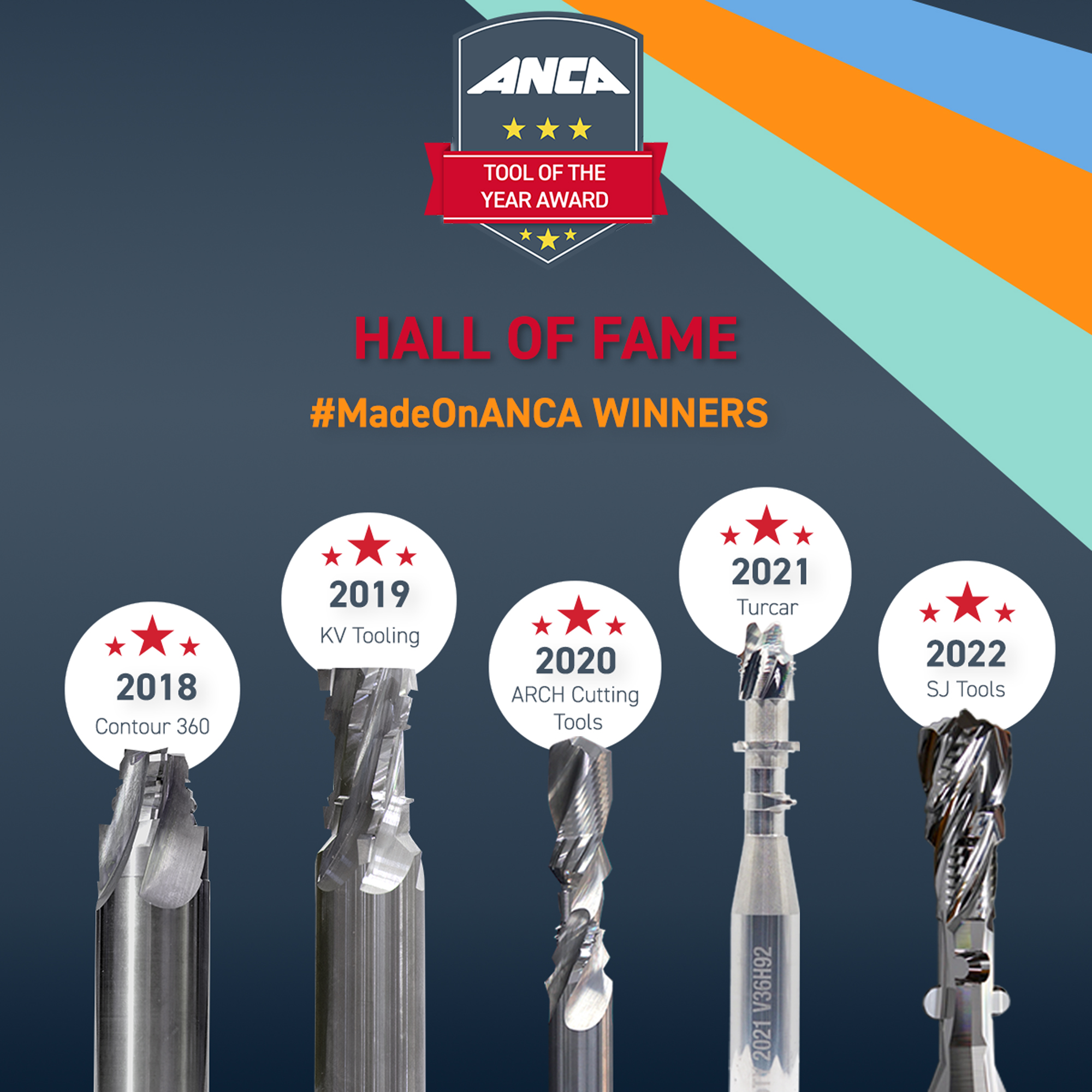
One of the most eagerly awaited events at ANCA's booth will be the winner announcement of the Tool of the Year 2023 competition. This prestigious competition brings together tool manufacturers from around the globe, who compete for the title of the best real and virtual tools. The judging process, overseen by a panel of ANCA and external experts, evaluates precision, surface roughness, creativity, and practical use. The award ceremony promises to be a highlight of the exhibition, recognizing the industry's most innovative and exceptional tools.
EMO 2023 offers an exclusive opportunity for industry professionals to explore ANCA's latest advancements in grinding technology, witness revolutionary world premieres, and engage with experts from the field. Visitors will also experience exclusive product launches to be revealed at the show. ANCA invites all attendees to visit their booth in Hall 6, F52, where they can experience firsthand the cutting-edge solutions and industry-specific grinding innovations that are shaping the future of manufacturing.
Strategic Partnerships with Industry leaders
ANCA's commitment to excellence is further emphasized through strategic partnerships with industry leaders. At EMO 2023, ANCA will collaborate with Mitsubishi, presenting their EDM machine at the booth, and GDS clamping technology, presenting a cohesive ecosystem of solutions that streamline processes across the process chain.
Contact Details
Related Glossary Terms
- collet
collet
Flexible-sided device that secures a tool or workpiece. Similar in function to a chuck, but can accommodate only a narrow size range. Typically provides greater gripping force and precision than a chuck. See chuck.
- computer numerical control ( CNC)
computer numerical control ( CNC)
Microprocessor-based controller dedicated to a machine tool that permits the creation or modification of parts. Programmed numerical control activates the machine’s servos and spindle drives and controls the various machining operations. See DNC, direct numerical control; NC, numerical control.
- dressing
dressing
Removal of undesirable materials from “loaded” grinding wheels using a single- or multi-point diamond or other tool. The process also exposes unused, sharp abrasive points. See loading; truing.
- electrical-discharge machining ( EDM)
electrical-discharge machining ( EDM)
Process that vaporizes conductive materials by controlled application of pulsed electrical current that flows between a workpiece and electrode (tool) in a dielectric fluid. Permits machining shapes to tight accuracies without the internal stresses conventional machining often generates. Useful in diemaking.
- grinding
grinding
Machining operation in which material is removed from the workpiece by a powered abrasive wheel, stone, belt, paste, sheet, compound, slurry, etc. Takes various forms: surface grinding (creates flat and/or squared surfaces); cylindrical grinding (for external cylindrical and tapered shapes, fillets, undercuts, etc.); centerless grinding; chamfering; thread and form grinding; tool and cutter grinding; offhand grinding; lapping and polishing (grinding with extremely fine grits to create ultrasmooth surfaces); honing; and disc grinding.
- grinding wheel
grinding wheel
Wheel formed from abrasive material mixed in a suitable matrix. Takes a variety of shapes but falls into two basic categories: one that cuts on its periphery, as in reciprocating grinding, and one that cuts on its side or face, as in tool and cutter grinding.
- process control
process control
Method of monitoring a process. Relates to electronic hardware and instrumentation used in automated process control. See in-process gaging, inspection; SPC, statistical process control.
- shaping
shaping
Using a shaper primarily to produce flat surfaces in horizontal, vertical or angular planes. It can also include the machining of curved surfaces, helixes, serrations and special work involving odd and irregular shapes. Often used for prototype or short-run manufacturing to eliminate the need for expensive special tooling or processes.
- tolerance
tolerance
Minimum and maximum amount a workpiece dimension is allowed to vary from a set standard and still be acceptable.