END USER: Micro-Tronics Inc., (602) 437-8995, www.micro-tronics.com.
CHALLENGE: Prevent sealed bearings from overheating in a live tooling head.
SOLUTION: A live tooling head with coolant-fed bearings.
SOLUTION PROVIDER: Planet Products Corp., (513) 984-5544, www.planet-products.com.
As live tooling becomes more popular in CNC turning centers, tooling with sealed bearings can pose a challenge for shops that produce parts in high volumes or with long cycle times. Most conventional live tooling designs have sealed bearings in the tool head, which may overheat during continuous use or under heavy loads. This may reduce performance of a precision machine, reduce tool life and result in frequent and costly maintenance issues.
Micro-Tronics Inc., a Tempe, Ariz., machine shop that produces metal valves, bearing races and related products for the aerospace and automotive industries, was facing the challenge of using conventional live tooling with sealed bearings. The shop produces 250 to 1,000 parts with cycle times of more than 30 minutes.
“If a shop produces high-cycle-time or high-volume parts, then thermal growth usually occurs in the tool head,” said Mike Thompson, lathe supervisor at Micro-Tronics. “The sealed bearings warm up after 6 to 8 hours.”
Thompson noted the occurrence of thermal growth requires offset deviations. “If you are holding really tight tolerances, you have to start moving your offsets around to hold dimensional size,” he said.
To avoid such problems, Micro-Tronics acquired a new type of live tooling head for its Puma 300M lathe. The tooling from Planet Products Corp., Cincinnati, has a coolant-fed bearing assembly.
PPC’s live tooling design for turret lathes utilizes the continuous flow of coolant to cool and lubricate the tool/workpiece interface. The fluid is directed through the tool head, cooling the bearings. Live tooling with coolant- fed bearings can run at high speeds and long cycle times without the accuracy and failure problems of conventional live tooling with sealed bearings, according to Thompson. “With this design, those bearings are constantly being lubricated with water-based synthetic coolant.”
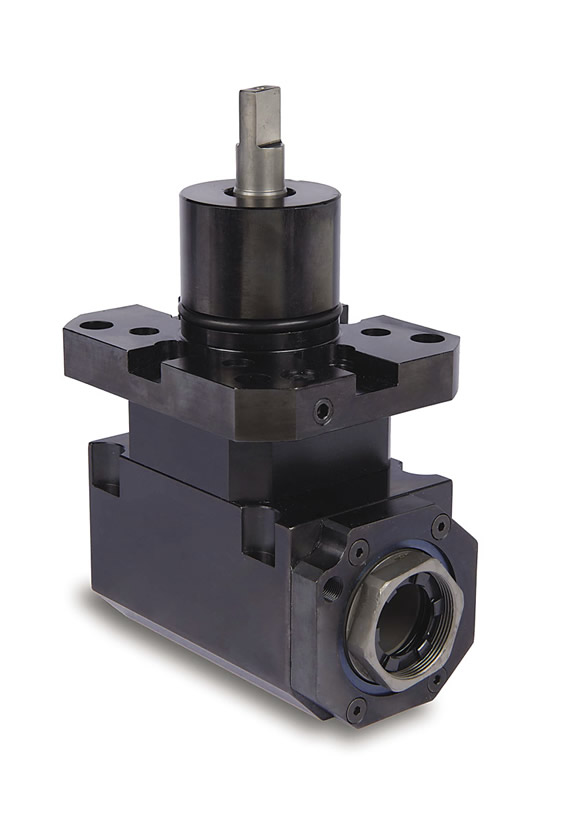
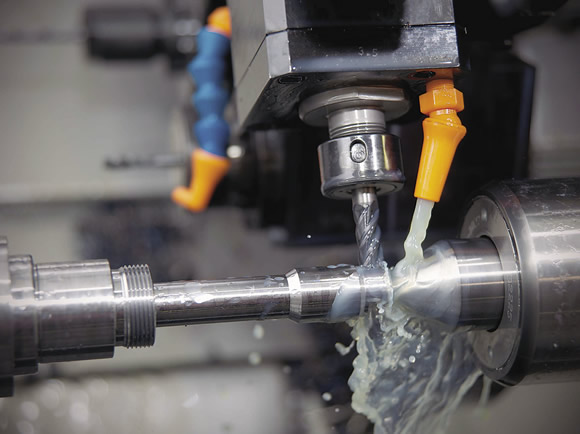
Planet Products’ live tooling design for turret lathes has a coolant-fed bearing assembly that prevents the bearings from overheating.
Conversely, conventional live tooling prevents coolant from contacting the bearings. Conventional sealed bearings rely on seal integrity or the lubricant packing to keep bearings operating normally under stressful conditions. If coolant does contact the bearing’s grease packing, a sludge forms that hinders bearing functionality and eventually causes failure.
Another benefit Thompson pointed out is that the filtered coolant-fed bearing design keeps metal chips and other contaminants from the bearing assembly. In some cases, contaminants contact the bearings and cause bearing-seal failures.
“However, the real benefit is we can put a cutting tool into production on large orders. We constantly hold tight tolerances without having to make tool offset adjustments,” Thompson said. “It reduces cycle time in the long run because I don’t have to chase the tool around to hold tolerance.”
Related Glossary Terms
- centers
centers
Cone-shaped pins that support a workpiece by one or two ends during machining. The centers fit into holes drilled in the workpiece ends. Centers that turn with the workpiece are called “live” centers; those that do not are called “dead” centers.
- computer numerical control ( CNC)
computer numerical control ( CNC)
Microprocessor-based controller dedicated to a machine tool that permits the creation or modification of parts. Programmed numerical control activates the machine’s servos and spindle drives and controls the various machining operations. See DNC, direct numerical control; NC, numerical control.
- coolant
coolant
Fluid that reduces temperature buildup at the tool/workpiece interface during machining. Normally takes the form of a liquid such as soluble or chemical mixtures (semisynthetic, synthetic) but can be pressurized air or other gas. Because of water’s ability to absorb great quantities of heat, it is widely used as a coolant and vehicle for various cutting compounds, with the water-to-compound ratio varying with the machining task. See cutting fluid; semisynthetic cutting fluid; soluble-oil cutting fluid; synthetic cutting fluid.
- lathe
lathe
Turning machine capable of sawing, milling, grinding, gear-cutting, drilling, reaming, boring, threading, facing, chamfering, grooving, knurling, spinning, parting, necking, taper-cutting, and cam- and eccentric-cutting, as well as step- and straight-turning. Comes in a variety of forms, ranging from manual to semiautomatic to fully automatic, with major types being engine lathes, turning and contouring lathes, turret lathes and numerical-control lathes. The engine lathe consists of a headstock and spindle, tailstock, bed, carriage (complete with apron) and cross slides. Features include gear- (speed) and feed-selector levers, toolpost, compound rest, lead screw and reversing lead screw, threading dial and rapid-traverse lever. Special lathe types include through-the-spindle, camshaft and crankshaft, brake drum and rotor, spinning and gun-barrel machines. Toolroom and bench lathes are used for precision work; the former for tool-and-die work and similar tasks, the latter for small workpieces (instruments, watches), normally without a power feed. Models are typically designated according to their “swing,” or the largest-diameter workpiece that can be rotated; bed length, or the distance between centers; and horsepower generated. See turning machine.
- tolerance
tolerance
Minimum and maximum amount a workpiece dimension is allowed to vary from a set standard and still be acceptable.
- turning
turning
Workpiece is held in a chuck, mounted on a face plate or secured between centers and rotated while a cutting tool, normally a single-point tool, is fed into it along its periphery or across its end or face. Takes the form of straight turning (cutting along the periphery of the workpiece); taper turning (creating a taper); step turning (turning different-size diameters on the same work); chamfering (beveling an edge or shoulder); facing (cutting on an end); turning threads (usually external but can be internal); roughing (high-volume metal removal); and finishing (final light cuts). Performed on lathes, turning centers, chucking machines, automatic screw machines and similar machines.