Oil mist filtration for machine tools makes for a cleaner working environment and better operating conditions for machines.
Every workday, Francine boots up her computer in the office at the machine shop where she works and contends with oily smoke pouring from the PC. A likely scenario? Hardly!
However, it doesn’t seem so outrageous for shop floor personnel to be exposed to oil mist and oily smoke generated during the machining process, even with worker safety rules regulating the amount. But that sentiment is rapidly changing. More metalworking facilities are equipping their machine tools with systems that collect and filter oil mist to clear the air and recycle the captured coolant.
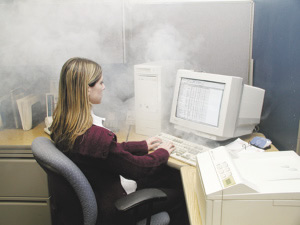
Courtesy of Royal Products
If a shop owner wouldn’t expect office personnel to work with oily smoke pouring out of their computers, they shouldn’t expect shop workers to operate machines with oil mist coming out of them.
“The most important reason we’re selling more mist collectors today than ever before is people just expect a good working environment,” said Tom Sheridan, vice president of marketing for Royal Products, Hauppauge, N.Y., which is the U.S. and Mexican agent for the Filtermist oil mist filtration system. “It’s hard enough to get young people interested in manufacturing. They are going to be a heck of a lot less inclined to come into a dirty environment.”
In addition to minimizing the amount of oil mist shop workers breathe, oil mist filtration prevents mist from damaging a machine’s control because electronics and moisture don’t mix well. “The cleaner you keep the environment your machine tools are operating in, the longer they last,” said Mark Eve, owner of Diversified Air Systems Inc., Louisville, Ky., which offers Maxflo oil mist collectors.
Eve added that an oil mist collector keeps heat from building up inside the machine cabinet so the machine runs cooler, which can enhance part accuracy, and exhausting the mist and smoke through the collector improves cabinet visibility.
Not only does airborne oil mist eventually land on workers, posing a risk of dermatitis and other skin ailments, it lands on lights, darkening a shop; on machines and walls, increasing housekeeping; and on floors, creating a slipping hazard. The oil mist also enters the heating, ventilation and air-conditioning system, creating expensive problems.
“I’ve gone into plants where the cost to heat and cool the plant is ridiculous,” Eve said. “Two reasons: They are exhausting too much air outside [to reduce indoor mist] and the oil mist gets into the coils and clogs them, so the HVAC guys are repeatedly changing the filters and cleaning the coils.”
In addition, airborne oil mist doesn’t instill confidence in a shop’s abilities to visiting prospects. “It’s kind of like if you go into a shop to get your car serviced and it’s a dirty mess—you don’t expect the quality of work to be as good as at a clean shop,” Eve said.
Equipment Choices
Various types of equipment are available for collecting and filtering oil mist, including media filtration, fiber-bed and electrostatic precipitator systems, each with certain benefits. With electrostatic filtration, filter replacement costs are virtually eliminated, according to Patrick Cherry, owner of distributor Environmental Clean Air Co., Loganville, Ga. Instead, users clean the filters, or collection cells, about once a month, depending on the application.
“We recommend our customers have a spare set of filters so they can pull the dirty filter, put the new filter in, wash that dirty filter and have it ready to go into the next system or back into the same unit,” Cherry said. He cautioned, however, to clean the filters with a noncaustic solution and to soak and rinse them, possibly in an industrial dishwasher, rather than scrub them. This is because scrubbing can alter cell spacing and create pockets where filtration doesn’t occur. “Electrostatic filters are meant to be permanent filters with proper care,” he added, noting the rated media filtration efficiency is 95 percent at 0.3µm.
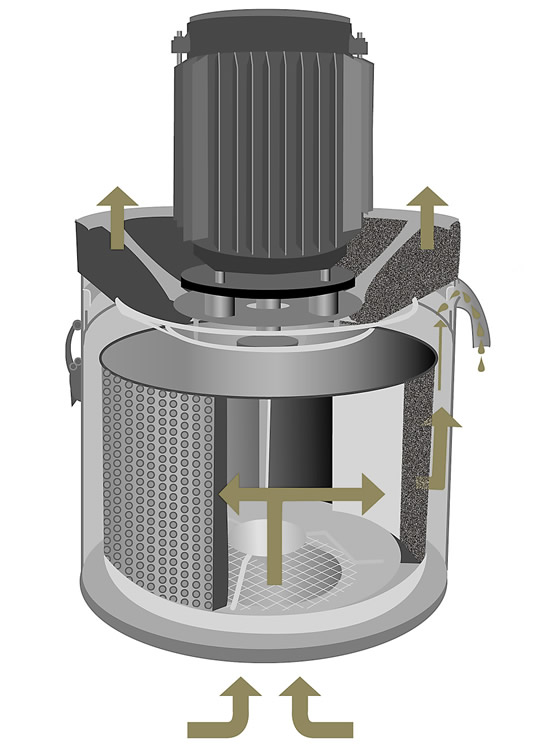
Courtesy of Royal Products
Royal Products’ Filtermist uses the mechanical principle of centrifugal impaction to draw oil mist from the machine tool, grow the particles into droplets and return the coolant to the machine’s coolant tank while blowing oil-free air past the motor and into the shop.
Electrostatic technology uses electricity to generate a positive or negative charge on a collector plate and oppositely charged plates repel one another at 3,000 times the force of gravity, Diversified Air Systems’ Eve noted. A static charge is placed on the airborne particles, which are then drawn to the plates. “Those are very effective on smoke,” he said, but only if maintained. “Most factories have limited maintenance personnel, so cleaning a nonproduction piece of equipment typically gets neglected.”
Fiber-bed systems can remove 99.5 percent of submicron-mist particles using beds of fiberglass in a cage structure to collect oil mist via Brownian diffusion. This is a process by which particles, subject to the random forces that result in Brownian motion, move from areas of higher concentration to areas of lower concentration.
According to Eve, users must typically purchase filters from the system manufacturer at a cost of several thousand dollars each.
On the other hand, filters for media filtration systems are available from a host of suppliers. Eve pointed out that the media method accepts a one-time use, disposable fiberglass bag filter. “Dollar for dollar, the best approach is a media filtration system,” he said. “It’s middle-of-the-road and people are typically happy with it from a filter-cost standpoint and from a cost-of-capital standpoint more than anything else.”
Media filtration captures about 95 percent of the particulate down to 0.1µm, Cherry noted, and the captured oil drains out the bottom of the media filtration unit.
“You don’t need to take out 99.97 percent of the particles, as they would do in a surgical room,” Eve said. “If you can get 90 to 95 percent of it, that’s an acceptable range.”
Mechanical Means
The mechanical principle of centrifugal impaction is another way to filter oil and oily smoke mist. It’s how the Filtermist oil mist filtration system from Royal Products operates, using three main components: a perforated drum, three-phase motor and outer housing. Sheridan explained that the motor rotates the drum at about 3,500 rpm to create suction, drawing mist particles from the machining center into the center of the drum, where they collide with the drum vanes and each other and coalesce to form droplets. The droplets then pass through perforations in the drum, and centrifugal force causes them to be thrown onto the inner wall of the housing.
“They bead up on the inner wall of the housing under pressure until they get to an oil return channel, where they are returned to the machine’s coolant sump, and clean air blows out through the top around the motor,” Sheridan said. “Basically, it’s a closed-loop system.”
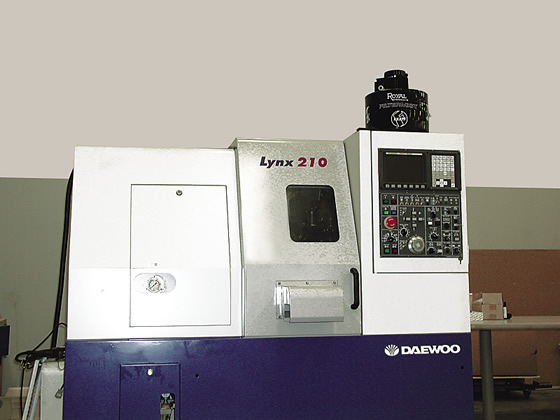
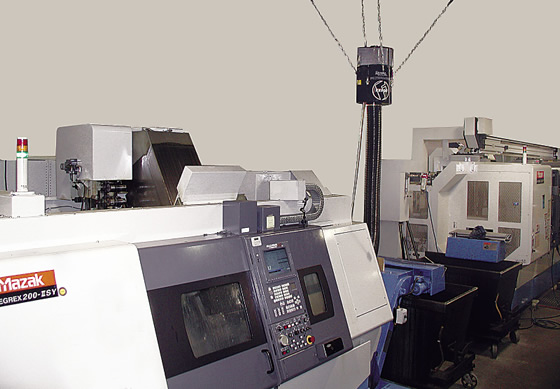
Courtesy of Royal Products
A Royal Products Filtermist unit can mount directly on the machine tool (top) or be suspended above it.
The filtration system also has porous polyether pads. The pads line the drum and slow airflow through the system to maximize contact with the drum vanes for enhanced impaction efficiency. Sheridan emphasized that the pads are not filters and do not become saturated, but should be inspected after 1,000 hours of operation and replaced after 2,000 hours.
The filtration units can be mounted on the machine tool, on an adjacent stand or suspended from the ceiling and connected to the machine with a short piece of duct work. The units can also be mounted on casters to enable rolling a unit from machine to machine. One unit can also be ducted to simultaneously serve more than one machine, but Sheridan recommends one unit per machine. By minimizing the hard or flexible duct work, the ducting doesn’t need to be rearranged every time a shop adds or moves a machine, which can be costly.
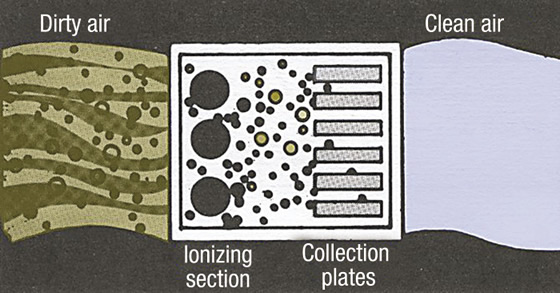
Courtesy of Environmental Clean Air
Electrostatic technology uses electricity to generate a positive or negative charge on a collector plate. A static charge is placed on the airborne particles, which are then drawn to the plates.
Diversified Air Systems’ Eve pointed out that it’s difficult to stop duct leakage, which requires a time-consuming process to clean the duct, make sure it’s dry and regasket or caulk it to put it back together. “That’s one of the biggest headaches to a central, or ducted, system,” he said. “We do duct work all the time, but it takes extra thinking and precaution.”
Eve pointed out that a modular or semimodular filtration approach is generally more beneficial than a central system for operating multiple machines with one filtration system. A modular arrangement allows a user to turn off the filtration system for machines that are temporarily not making parts. “Whereas with the central system, everything is on or everything is off unless you get into some very elaborate controls,” he said. “That can double the cost of the equipment to modulate how much air is going through the mist collector.”
Pressure’s On
As more part manufacturers turn to high-pressure coolant for its productivity and tool-life-boosting benefits, they face an increase in the generation of fine oil mist. After switching to high-pressure, through-coolant drills, as well as faster face- mills, on a horizontal machining center, Liquid Controls LLC found that it needed an oil mist collector, noted Mike Deren, manufacturing engineer for the Lake Bluff, Ill., manufacturer of flow meters, electronic registers and pumps, and a CTE columnist. He explained that the mist would take several minutes to dissipate before an operator could open the door to change parts; otherwise, it would enter the shop environment.
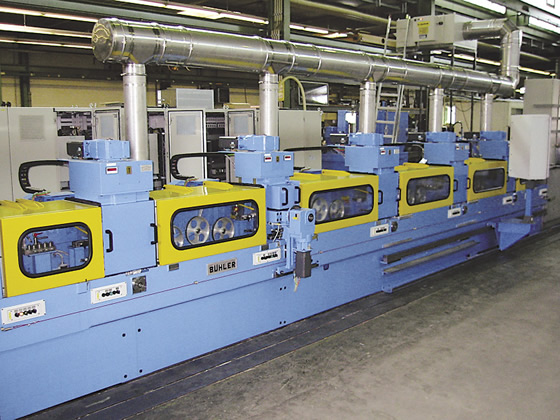
Courtesy of Environmental Clean Air
An electrostatic air cleaner is one option for collecting oil mist from machine tools.
To collect the mist, the company purchased a Model FX-900 Filtermist from Royal Products. In addition, a cyclonic separator acts as a prefilter when applying high-pressure coolant, Deren noted. Accessories for the mist collector include a machine-top stand, a deflector to protect the unit from flying chips, 4 ' of duct, two hose clamps, a flange adapter and a coolant return hose.
“Our upfront cost was less than $4,000 and a day of labor by our maintenance team to install it,” Deren said. “The only ongoing maintenance required is annual replacement of the four drum pads.”
In addition, Liquid Controls has two MistBlaster oil mist collectors from ChipBlaster Inc. for its ChipBlaster high-pressure coolant systems on two other HMCs. Those collectors are mounted on the coolant systems so they consume no additional floor space, Deren noted. He added that the company also has several approximately 20-year-old, floor-mounted vertical oil mist collectors for CNC cylindrical grinders, which use a large-diameter hose to connect to a machine.
System Sizing
Deren emphasized that an oil mist collector needs to be sized to collect just the mist, not the raw coolant or droplets.
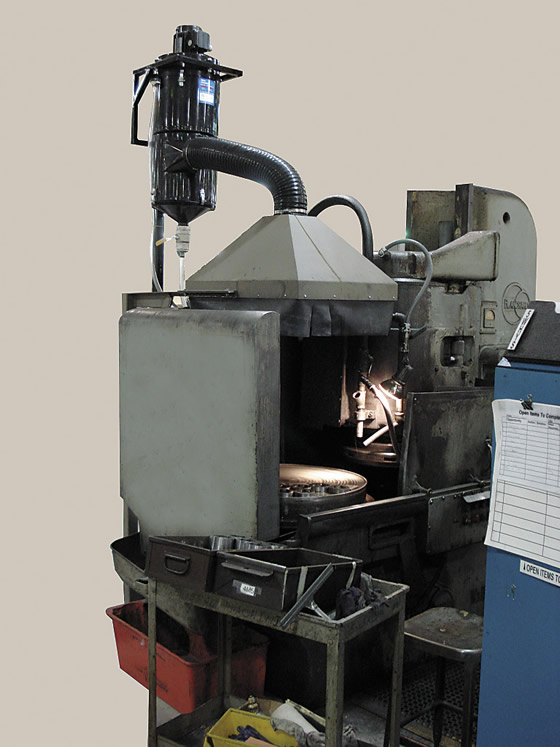
Courtesy of Royal Products
When a machine isn’t enclosed, such as this Blanchard grinder, a Royal Products Filtermist can be configured with a hood to capture oil mist.
Sheridan explained that, as a rule of thumb, Royal Products sizes a Filtermist throughput in cubic feet per minute to be five times the internal enclosure volume of a machine tool. For example, if a CNC lathe has a work envelope of 4 '×3 '×4 ', or 48 cu. ft., it requires an oil mist collector that provides 240 cfm. “That will more or less guarantee the air inside the machine tool enclosure is changed five times a minute, or once every 12 seconds,” he said.
However, with better-sealed machine tools, the unit size must be scaled down so it only pulls in the mist and not the coolant. For example, a bar-fed machine with an automatic parts catcher will need a unit with a smaller cfm than a machine with the same work envelope where the operator is opening the door every 35 seconds to change a part.
When a machine isn’t enclosed, Environmental Clean Air’s Cherry recommends first identifying where the oil mist is coming from and then minimizing the area to be treated with hoods and other types of enclosures to more effectively contain the mist.
Regardless of the type of oil mist filtration system, worker health and safety is paramount. “The key is to protect the employee and keep the mist and smoke inside the machine cavity so it can be exhausted through the mist collector,” said Diversified Air Systems’ Eve. CTE
About the Author: Alan Richter is editor of CTE. He joined the publication in 2000. Contact him at (847) 714-0175 or [email protected].
Oil mist filtration to the rescue
Meeting the Occupational Safety and Health Administration’s requirement for air quality doesn’t necessarily mean shop personnel are working in the healthiest environment. Air quality surveys conducted at Hurst Jaws of Life’s machine shop found that the level of oil mist fell within acceptable levels, noted Jim Mosteller, manufacturing engineer for the Shelby, N.C., company. But that wasn’t good enough. The company wanted even better air quality to protect its workers and its parts.
Mosteller explained that the machining department, which primarily cuts 7075 aluminum, H-13 tool steel and 4140 and 4340 alloy steel to produce parts for rescue tools to extricate vehicle crash victims from the “jaws of death,” is part of an ISO 9001-certified company. Therefore, it tries to be proactive with its environmental responsibilities to fully comply with the standard. After discussing its options, the company decided to invest in oil mist filtration equipment.
“It was partly driven by the ISO project for continuous improvement,” Mosteller said, “and finally getting people to understand that the air quality could be better, because the air quality in a machine shop can get pretty thick sometimes.”
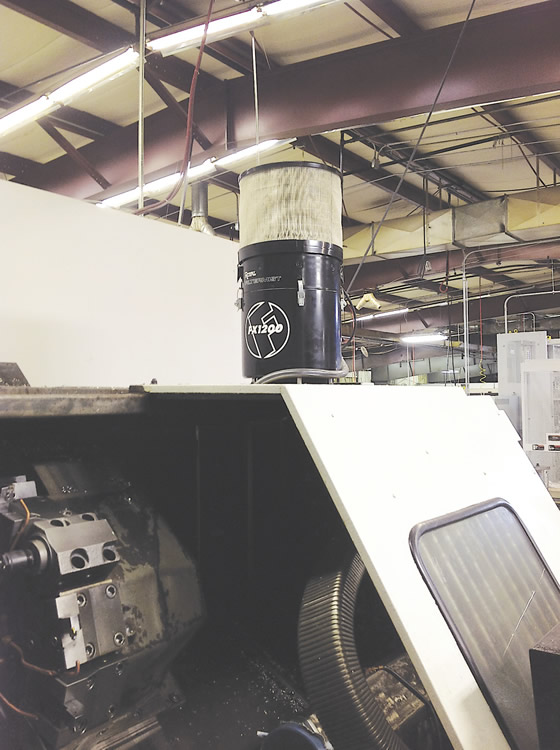
Courtesy of Hurst Jaws of Life
Mounted on an Okuma LC30 CNC lathe, this FX1200 Model Filtermist oil mist filtration unit at Hurst Jaws of Life has an after-filter on top to remove oily submicron-size smoke particles.
Operators would often stand back after opening a machine door to let a mist cloud dissipate or blow the mist away with an air hose before gaging or changing a part, thereby reducing efficiency, he added. “If it was up to the operators, they probably would have slowed the speeds and feeds to cut down on the oil mist, but that wasn’t an option because the programming/manufacturing engineering department controls those.”
Based on its research and budget, Hurst selected a Filtermist system from Royal Products to filter oil mist from one of its eight CNC machine tools. “It worked really well, so we went ahead and purchased units for the rest of the machines,” Mosteller said.
He pointed out that Gene McDonald, regional business manager for Royal Products, measured the internal dimensions of the machines to size the filtration systems and recommended mounting procedures, brackets and attachments. Hurst installed the filtration systems, and the units mount directly to the machines except for a Mazak lathe, which required a unit suspended from the ceiling because the machine configuration prevented it from being directly mounted.
In addition, an Okuma LC30 lathe generates a significant amount of heat when turning steel piston rods and, therefore, produces oily smoke as well as oil mist, Mosteller noted. As a result, Hurst outfitted the filtration system with an after-filter to capture submicron particles.
Although the operators greeted the mist collectors with curiosity and even some skepticism, according to Mosteller, they quickly realized the benefits. “With the Filtermist units running, when the operators open the machine door, they are no longer hit in the face with a cloud of mist and smoke, but with a nice breeze pulling air into the machine,” he said.
In addition to enhanced productivity, part quality and worker morale and attendance improve because of the reduced environmental impact from machining, and the machine shop is cleaner. “After installing these units, we repainted the walls and aisles and they stay clean now,” Mosteller said. “We don’t have mist settling over everything like we used to.”
—A. Richter
Contributors
Diversified Air Systems Inc.
(502) 267-0333
www.diversair.com
Environmental Clean Air Co.
(866) 366-2034
www.environmentalcleanair.com
Hurst Jaws of Life
(800) 537-2659
www.jawsoflife.com
Liquid Controls LLC
(800) 458-5262
www.liquidcontrols.com
Royal Products
(800) 645-4174
www.royalprod.com
Related Glossary Terms
- closed-loop system
closed-loop system
CNC system in which the program output, or the distance the slide moves, is measured and compared to the program input. The system automatically adjusts the output to be the same as the input.
- computer numerical control ( CNC)
computer numerical control ( CNC)
Microprocessor-based controller dedicated to a machine tool that permits the creation or modification of parts. Programmed numerical control activates the machine’s servos and spindle drives and controls the various machining operations. See DNC, direct numerical control; NC, numerical control.
- coolant
coolant
Fluid that reduces temperature buildup at the tool/workpiece interface during machining. Normally takes the form of a liquid such as soluble or chemical mixtures (semisynthetic, synthetic) but can be pressurized air or other gas. Because of water’s ability to absorb great quantities of heat, it is widely used as a coolant and vehicle for various cutting compounds, with the water-to-compound ratio varying with the machining task. See cutting fluid; semisynthetic cutting fluid; soluble-oil cutting fluid; synthetic cutting fluid.
- diffusion
diffusion
1. Spreading of a constituent in a gas, liquid or solid, tending to make the composition of all parts uniform. 2. Spontaneous movement of atoms or molecules to new sites within a material.
- land
land
Part of the tool body that remains after the flutes are cut.
- lathe
lathe
Turning machine capable of sawing, milling, grinding, gear-cutting, drilling, reaming, boring, threading, facing, chamfering, grooving, knurling, spinning, parting, necking, taper-cutting, and cam- and eccentric-cutting, as well as step- and straight-turning. Comes in a variety of forms, ranging from manual to semiautomatic to fully automatic, with major types being engine lathes, turning and contouring lathes, turret lathes and numerical-control lathes. The engine lathe consists of a headstock and spindle, tailstock, bed, carriage (complete with apron) and cross slides. Features include gear- (speed) and feed-selector levers, toolpost, compound rest, lead screw and reversing lead screw, threading dial and rapid-traverse lever. Special lathe types include through-the-spindle, camshaft and crankshaft, brake drum and rotor, spinning and gun-barrel machines. Toolroom and bench lathes are used for precision work; the former for tool-and-die work and similar tasks, the latter for small workpieces (instruments, watches), normally without a power feed. Models are typically designated according to their “swing,” or the largest-diameter workpiece that can be rotated; bed length, or the distance between centers; and horsepower generated. See turning machine.
- machining center
machining center
CNC machine tool capable of drilling, reaming, tapping, milling and boring. Normally comes with an automatic toolchanger. See automatic toolchanger.
- metalworking
metalworking
Any manufacturing process in which metal is processed or machined such that the workpiece is given a new shape. Broadly defined, the term includes processes such as design and layout, heat-treating, material handling and inspection.
- turning
turning
Workpiece is held in a chuck, mounted on a face plate or secured between centers and rotated while a cutting tool, normally a single-point tool, is fed into it along its periphery or across its end or face. Takes the form of straight turning (cutting along the periphery of the workpiece); taper turning (creating a taper); step turning (turning different-size diameters on the same work); chamfering (beveling an edge or shoulder); facing (cutting on an end); turning threads (usually external but can be internal); roughing (high-volume metal removal); and finishing (final light cuts). Performed on lathes, turning centers, chucking machines, automatic screw machines and similar machines.
- work envelope
work envelope
Cube, sphere, cylinder or other physical space within which the cutting tool is capable of reaching.