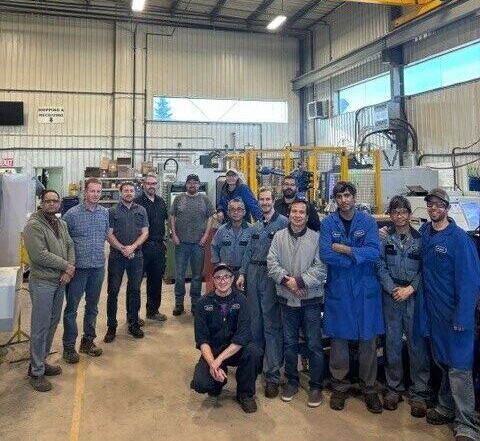
Canerector has acquired Promac Industries Inc., a move that the company says strengthens its machining capabilities, particularly in the energy services sector.
“We’re thrilled to welcome Promac Industries to our network,” said Matt Warden, Canerector’s Senior Vice President. “Promac’s focus on downhole tooling and high-end machining, paired with its extensive technical knowledge in turning and milling, is a great fit for us. Their commitment to design and manufacturing consultations and prototyping brings valuable strength to our network.”
By maintaining a focused approach, Promac has consistently met the demanding needs of the industry. Its technical expertise and strong dedication to its core customers have earned Promac several long-standing relationships.
“Our success is built on a foundation of trust, both in our expertise and our dedication to quality and dependability in the energy services industry,” said Trina Vitolianos, President. “It’s what makes us a leader and will keep us on top for years to come.”
As Canerector continues to expand through acquisitions, we are committed to providing each company the resources to flourish independently while benefiting from access to a network of peers, invaluable insights, and opportunities for growth. It’s this approach that gave Promac’s previous owner Sean Monaghan, the confidence to know we were the best long-term home for the business.
“We were impressed with Canerector’s approach to the transaction process and future commitment to the organization. Plus, their financial capability was exemplary,” said Monaghan. “Joining Canerector marks a significant milestone for our team. With the benefit of a robust network of peers and resources, the team is poised for an exciting future.”
Contact Details
Related Glossary Terms
- gang cutting ( milling)
gang cutting ( milling)
Machining with several cutters mounted on a single arbor, generally for simultaneous cutting.
- milling
milling
Machining operation in which metal or other material is removed by applying power to a rotating cutter. In vertical milling, the cutting tool is mounted vertically on the spindle. In horizontal milling, the cutting tool is mounted horizontally, either directly on the spindle or on an arbor. Horizontal milling is further broken down into conventional milling, where the cutter rotates opposite the direction of feed, or “up” into the workpiece; and climb milling, where the cutter rotates in the direction of feed, or “down” into the workpiece. Milling operations include plane or surface milling, endmilling, facemilling, angle milling, form milling and profiling.
- turning
turning
Workpiece is held in a chuck, mounted on a face plate or secured between centers and rotated while a cutting tool, normally a single-point tool, is fed into it along its periphery or across its end or face. Takes the form of straight turning (cutting along the periphery of the workpiece); taper turning (creating a taper); step turning (turning different-size diameters on the same work); chamfering (beveling an edge or shoulder); facing (cutting on an end); turning threads (usually external but can be internal); roughing (high-volume metal removal); and finishing (final light cuts). Performed on lathes, turning centers, chucking machines, automatic screw machines and similar machines.