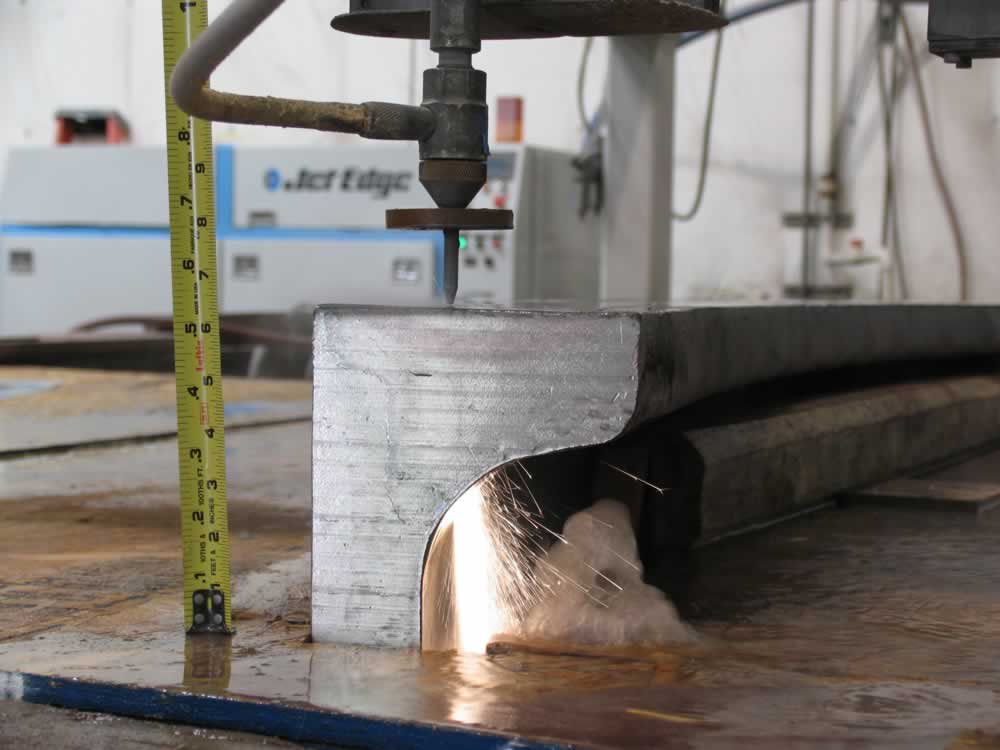
In connection with the abrasive waterjet machining article scheduled for our March issue, I spoke with Jim Draper, owner of Rocky Mountain Waterjet, Greeley, Colo., who said when a parts manufacturer finds that waterjetting is a suitable process for a part or family of parts, the decision to outsource that work to a waterjet job shop or buy a waterjet machine for in-house production depends on the part quantity.
Draper added that if a waterjet machine will be cutting 4 hours per day on a consistent basis, it makes sense to bring the operation in-house. However, the cost of the equipment isn’t the only consideration. A parts manufacturer also need the space to place a waterjet machine or face the added expense of expanding the existing facility.
In addition, abrasive waterjetting is a “dirty operation” that creates a large quantity of dust, so if a company, such as a medical device manufacturer, must maintain a fairly clean or even clean-room environment, creating a separate waterjet room or new facility will extent the payback, he said.
Draper said RMW is seeing an increase in waterjetting business, even though the company has expanded into fiber laser cutting, which is an alternative to waterjetting for certain applications. A waterjet, however, can cut virtually any material, with the exception of high-tempered glass, while lasers are more restricted. Although a waterjet can cut ceramic and some other very hard materials, it takes too long to be cost-effective.
Some waterjet job shops serve a greater metropolitan area, state or region, but Draper said his company has customers in the Caribbean, East Coast, Michigan and California. Some customers have switched to local waterjet shops, only to return because of quality and service issues. Rocky Mountain Waterjet works with entrepreneurs, for example, to develop waterjet-machined products, provides completed products including weldments and up to powder coat and machines parts for job shops, government agencies, OEMs and others.
I also spoke with Simon Arthur, owner of Big Blue Saw in Atlanta. He indicated that in addition to avoiding the expense of buying an abrasive waterjet machine and relying on the expertise of a waterjet job shop, some of his customers outsource work to BBS to avoid putting additional wear and tear on the waterjet machines they own. Those customers will waterjet parts with their own machines for the jobs that generate the most profit and require the most productivity.
Arthur added that a large quantity of his work is waterjetting aluminum parts. Customers include machine shops and range from garage inventors to large corporations needing R&D and prototype work. Big Blue Saw also offers laser cutting.
Related Glossary Terms
- abrasive
abrasive
Substance used for grinding, honing, lapping, superfinishing and polishing. Examples include garnet, emery, corundum, silicon carbide, cubic boron nitride and diamond in various grit sizes.
- abrasive waterjet ( AWJ)
abrasive waterjet ( AWJ)
System that uses high-pressure waterjets in combination with a slurry of fine abrasive grains to machine materials. See waterjet cutting.
- family of parts
family of parts
Parts grouped by shape and size for efficient manufacturing.
- lapping compound( powder)
lapping compound( powder)
Light, abrasive material used for finishing a surface.
- sawing machine ( saw)
sawing machine ( saw)
Machine designed to use a serrated-tooth blade to cut metal or other material. Comes in a wide variety of styles but takes one of four basic forms: hacksaw (a simple, rugged machine that uses a reciprocating motion to part metal or other material); cold or circular saw (powers a circular blade that cuts structural materials); bandsaw (runs an endless band; the two basic types are cutoff and contour band machines, which cut intricate contours and shapes); and abrasive cutoff saw (similar in appearance to the cold saw, but uses an abrasive disc that rotates at high speeds rather than a blade with serrated teeth).