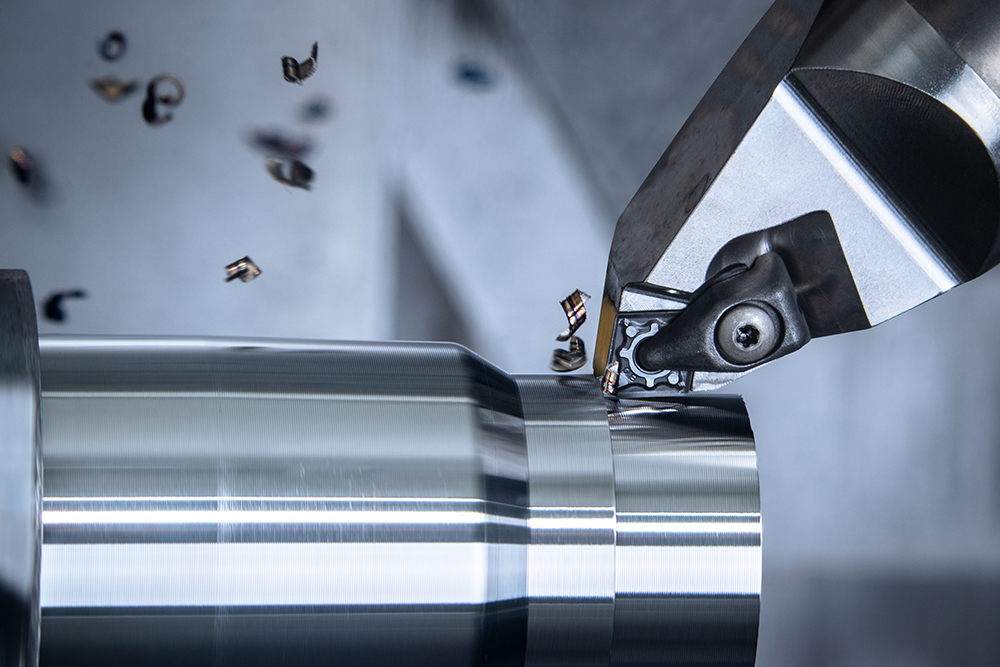
Every cutting insert experiences a drop in performance when approaching the end of its life cycle. If this condition goes undetected for any amount of time, part-machining performance, as well as part quality, may have already suffered.
Shops may also continue to push the worn tool to its limit where it might fail in the middle of a critical process. While the failed cutting insert is the least of a shop’s problems, damage to the workpiece is a much more serious issue.
However, if shops can identify the extent of insert wear, they can replace it promptly and avoid any tool or part damage. What makes this possible are advancements in cutting tool coatings that essentially warn shops of impending insert disasters.
Such coatings typically involve multi-layers, the top layer providing early warning wear detection while the others ensure optimum performance and longer tool life. However, the effectiveness of these coatings is also dependent on how they are applied. In most instances, special mechanical post-treatments are used and will ensure the layer surface’s unique state of residual stress.
To prevent insert waste and easily detect wear, the gold-colored TiN outer layer of the Dragonskin multilayer CVD Ti(C,N)/Al 2 O 3 /TiN coating from the cutting tool OEM CERATIZIT, for example, acts as an indicator. It not only enables users to identify insert wear and index before a breakage but also prevents sharp cutting edges from going unused and the insert from being discarded.
For its Dragonskin coating, the company not only incorporated the three-layer approach and mechanical post treatments, but it also applied these to indexable insert grades engineered for the intended part material applications. One example is the company’s recently released ISO-P steel turning inserts featuring the Dragonskin coating that extends the working lives of the new inserts by as much as 20 percent when compared to their predecessors.
ISO-P steels are by far the largest material group in part machining and include materials from ductile, low-carbon steels to high-alloy steel grades. Added to this are variations in hardness, application types, and machining conditions during the turning operation.
To make choosing an appropriate indexable insert grade easier, indexable insert grades were developed and tailored to ISO-P materials.
To enhance productivity for its customers CERATIZIT rethought its new CTCP135-P, CTCP125P-P and CTCP115-P turning grades from the substrate to the geometries and through to the Dragonskin coating. This was done to optimize process security and hardness of insert edges to ensure they withstand extreme cutting zone temperatures without plastic deformation. This also ensures that they handle a full range of machining challenges such as when materials are extremely hard.
Each of the three grades is engineered for optimizing specific production scenarios. The CTCP115-P (ISO P15) grade has enhanced resistance to high temperatures and is ideal for use at higher cutting speeds in smooth, continuous cuts in stable cutting conditions. The CTCP125-P (ISO P25) universal steel-cutting grade balances toughness and wear resistance to provide consistent reliability in turning operations ranging from finishing to rough machining, while the CTC135-P (ISO P35) is a tough carbide grade for lower cutting speeds, interrupted cuts, and unstable machining conditions.
Machining steel is anything but easy, and most experienced machining specialists are open to any solution that helps them turn ISO-P steel. This is why CERATIZIT continues to refine its insert grades and apply its Dragonskin coating to prevent waste, extend tool life and further ensure a shop’s overall long-term success. Those shops that fail to evaluate new alternatives and best-practices when selecting an indexable insert grade will be squandering the potential for considerable savings.
Contact Details
Related Glossary Terms
- chemical vapor deposition ( CVD)
chemical vapor deposition ( CVD)
High-temperature (1,000° C or higher), atmosphere-controlled process in which a chemical reaction is induced for the purpose of depositing a coating 2µm to 12µm thick on a tool’s surface. See coated tools; PVD, physical vapor deposition.
- hardness
hardness
Hardness is a measure of the resistance of a material to surface indentation or abrasion. There is no absolute scale for hardness. In order to express hardness quantitatively, each type of test has its own scale, which defines hardness. Indentation hardness obtained through static methods is measured by Brinell, Rockwell, Vickers and Knoop tests. Hardness without indentation is measured by a dynamic method, known as the Scleroscope test.
- indexable insert
indexable insert
Replaceable tool that clamps into a tool body, drill, mill or other cutter body designed to accommodate inserts. Most inserts are made of cemented carbide. Often they are coated with a hard material. Other insert materials are ceramic, cermet, polycrystalline cubic boron nitride and polycrystalline diamond. The insert is used until dull, then indexed, or turned, to expose a fresh cutting edge. When the entire insert is dull, it is usually discarded. Some inserts can be resharpened.
- low-carbon steels
low-carbon steels
Group of carbon steels designated by American Iron and Steel Institute numerical classification as AISI 1005, 1006, 1008, etc., up to AISI 1026, for a total of 16 grades. They are softer and more ductile than other carbon steels. Composition of low-carbon steels is 0.06 to 0.28 percent carbon, 0.25 to 1.00 percent manganese, 0.040 percent (maximum) phosphorus and 0.050 percent (maximum) sulfur. See high-carbon steels; medium-carbon steels.
- plastic deformation
plastic deformation
Permanent (inelastic) distortion of metals under applied stresses that strain the material beyond its elastic limit.
- residual stress
residual stress
Stress present in a body that is free of external forces or thermal gradients.
- titanium nitride ( TiN)
titanium nitride ( TiN)
Added to titanium-carbide tooling to permit machining of hard metals at high speeds. Also used as a tool coating. See coated tools.
- turning
turning
Workpiece is held in a chuck, mounted on a face plate or secured between centers and rotated while a cutting tool, normally a single-point tool, is fed into it along its periphery or across its end or face. Takes the form of straight turning (cutting along the periphery of the workpiece); taper turning (creating a taper); step turning (turning different-size diameters on the same work); chamfering (beveling an edge or shoulder); facing (cutting on an end); turning threads (usually external but can be internal); roughing (high-volume metal removal); and finishing (final light cuts). Performed on lathes, turning centers, chucking machines, automatic screw machines and similar machines.
- wear resistance
wear resistance
Ability of the tool to withstand stresses that cause it to wear during cutting; an attribute linked to alloy composition, base material, thermal conditions, type of tooling and operation and other variables.