With the many complicated components in an automotive system, one tiny burr, misplaced fit, chip, ding or uneven finish can wreak havoc and affect the performance of the entire engine. The industry looks for perfection down to the micromillimeter, and that’s where technology for finishing comes in. Products exist to tackle various aspects of automotive finishing, including Norton Finium, Orbitool and DeBurr-Z.
Knock Down the Peaks
When it comes to surface condition, smoothness really matters. Ra, or the arithmetic average of surface heights measured across a surface, gives a snapshot of the microscopic peaks and valleys on any given part.
“When you’re talking about bearing surfaces on a crankshaft or camshaft, even at a fine Ra there is wear on the shaft and bearings,” said David Goetz, senior application engineer at Norton | Saint-Gobain Abrasives in Worcester, Massachusetts. “Although it may be slight, all that metal ends up in the engine.”
Norton Finium microfinishing films use a proprietary resin system to hold grains in place for finishing in automotive engine applications. The film-backed ultrafine grit abrasives come in a range of shapes, sizes and grits to fit a wide variety of requirements and eliminate the concern of grain fallout, which could leave coarse scratches and result in defective parts.
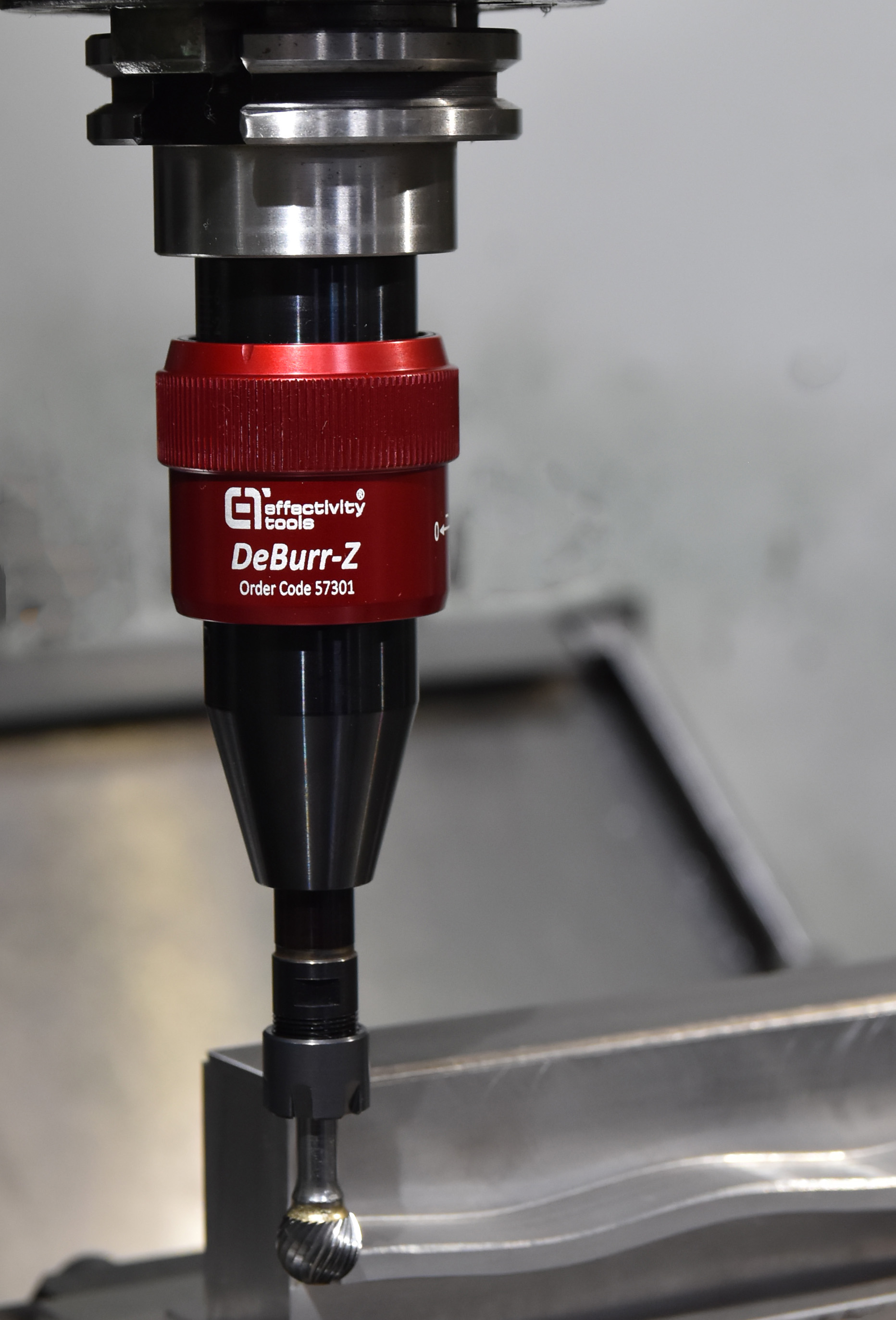
Used to finish the surface of many automotive components — including camshaft lobes and journals; crankshaft mains, pins, thrust walls and oil seals; and transmission shafts — Norton Finium is wound onto a roll that varies in length depending on the machine being used. The width of the film depends on the part being polished. A user places the film over polishing shoes attached to polishing arms while the part is secured in a fixture and the polishing arms are clamped around the part. The array keeps contact with the part and Norton Finium for a given amount of time, generating the desired finish.
“Polishing is a rubbing or abrasion process where the cutting fluid (mineral seal oil or polishing oil), the Finium abrasive and resin from the bond form a flurry, and that’s what’s doing the finishing,” Goetz said. “Typically, we’re only taking off between 3 and 5 μm when we’re lapping. By polishing, you get a better surface condition and the engine runs more true. In turn, it cuts down on the vibration and noise and adds to the life of the product.”
Smooth the Burrs
In the past, deburring was treated as an afterthought in the automotive industry. The focus always had been on more efficiently making parts and vehicles, but nowadays manufacturers review costs and work hours for all aspects of production. And manual deburring is time-intensive and subject to human error.
“We’ve realized that many shops weren’t factoring in the cost of someone in the deburring department manually damaging or scraping the parts,” said Stan Kroll, partner and general manager of J.W. Done Corp. in Hayward, California. “There were cases where thousands of engine blocks weren’t deburred properly and now they have to go back to fix them. That gets costly very quick.”
From the standpoint of quality, automakers can track engine failures to the tiniest burr in a camshaft. With possibly thousands of complex parts, an engine can be affected by one particular cross-hole shaving that enters a timing system and can cause the entire engine to fail.
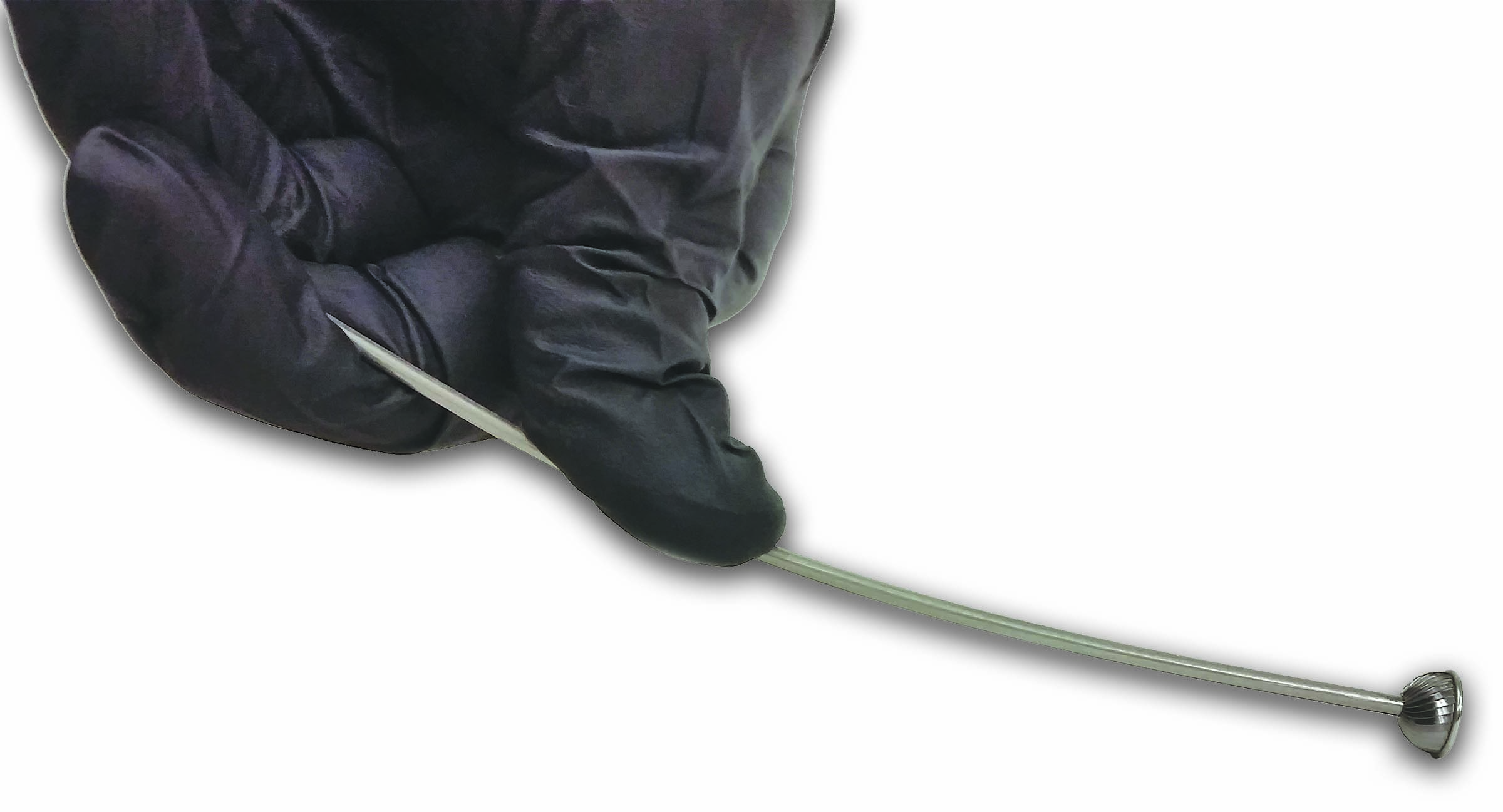
“Improving those cross-holes gets us one step closer to increased reliability,” Kroll said. “Higher-quality reliable parts made economically and quickly is the goal.”
Traditional deburring methods include using abrasive brushes, reamers and carbide balls attached to a grinder, with an operator going after every hole to remove extra material. Some dedicated deburring tools, such as J.W. Done’s Orbitool, are designed strictly for cross-drilled hole deburring. The tool is used just like any cutting tool found on a lathe turret or a tool magazine of a CNC or milling machine.
Orbitool expressly removes burrs from the intersection of cross-holes. The operation can be tailored to leave a minimally broken edge or a blended radius.
“The original idea for the Orbitool came about specifically for aerospace fittings because of the difficult nature of their intersections and radius requirements,” Kroll said. “But it was applicable to one of our earliest customers, which was Ford, using it on camshafts.”
The cutting method is fairly traditional using a carbide rotary burr, but Orbitool features the combination of a flexible drive shaft made of tool steel, a carbide shaped cutter and a polished steel disk. This commonly is referred to as a lollipop cutter. The larger-diameter polished disk negates the risk of damage to a part.
“The flexible shaft allows us to bend and pre-load the tool,” Kroll said. “We have a protective ring to place against the wall, bend the shaft slightly and pre-load the cutting tool. The toolpath uses helical interpolation, otherwise known as a thread spiral or helix spiral. With the Orbitool, the operator doesn’t have to program any complex contours or even know precisely where their edge is or its precise shape. We pre-load the tool and place the helix spiral where deburring is needed. It’s the tool’s ability to self-select and constantly bend and flex to the environment around it that allows it to deal with an interrupted cut. It only cuts material in the area where you need deburring but won’t damage anywhere else.”
Other deburring tools exist to help with the top and underside edges. Tapmatic Corp. in Post Falls, Idaho, created DeBurr-Z, which works on a CNC machine for both compression and extension, allowing the cutting tool to follow the outer contours of the component. With an adjustable force, the pressure may be increased or decreased to accommodate the type of material and the desired edge break.
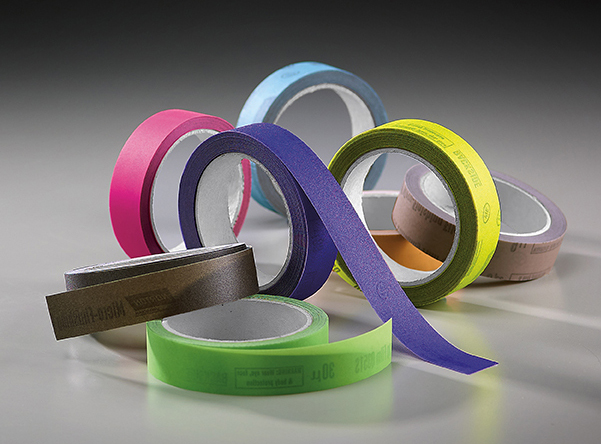
Chamfering holes on a curved surface also presents problems for conventional deburring methods. Using a standard countersink tool results in inconsistent edge breaks. Going around the holes with the axially floating DeBurr-Z produces consistent results, said President Mark Johnson. In general, either angular- or spherical-shaped burr cutting tools are used to apply the right contact to the workpiece for chamfering or deburring the edge.
“The edges of the workpiece can often be a little difficult to identify or clearly define like in the case of castings, cross-holes or slots,” he said. “It can be difficult to follow the edges evenly, but a floating tool has the compensation that lets the burr cutting tool follow the edge even when its position varies.”
Mark the Spot
DeBurr-Z can be used for engraving, allowing a quicker approach to the workpiece and the ability to mark on curved surfaces.
“If you have a part number, logo, date or batch code, you can use it to mark the workpiece,” Johnson said. “The advantage of having the axial compression for engraving is it allows you to approach the workpiece faster and makes the engraving process quicker than it would be if you held the engraving tool in a solid holder. We also offer a ScribeWriter, which is a scribing tool; our TapWriter for dot peen marking, creating dots on the workpiece; and we offer our Marking Head for stamping the workpiece. It uses custom stamps or standard type to mark numbers, date codes and other information.”
When it comes to automotive parts and systems, it could be said that it’s not so much how you start but how you finish.
“They can machine the parts faster and better,” Kroll said, “but deburring and finishing is the last step. It may not be the most important, but it’s still a step you can’t skip. There will always be a finishing process required on the part after the machine but before its final destination. It’s the last, most important step before anything ships out in a sellable condition.”
Contact Details
Contact Details
Contact Details
Related Glossary Terms
- abrasive
abrasive
Substance used for grinding, honing, lapping, superfinishing and polishing. Examples include garnet, emery, corundum, silicon carbide, cubic boron nitride and diamond in various grit sizes.
- arithmetic average ( AA)
arithmetic average ( AA)
The mathematical expression denoting one of several parameters that describe surface texture (same as average roughness Ra). Average roughness is the arithmetic average height deviation of the measured surface profile from the profile centerline. See surface texture.
- burr
burr
Stringy portions of material formed on workpiece edges during machining. Often sharp. Can be removed with hand files, abrasive wheels or belts, wire wheels, abrasive-fiber brushes, waterjet equipment or other methods.
- chamfering
chamfering
Machining a bevel on a workpiece or tool; improves a tool’s entrance into the cut.
- computer numerical control ( CNC)
computer numerical control ( CNC)
Microprocessor-based controller dedicated to a machine tool that permits the creation or modification of parts. Programmed numerical control activates the machine’s servos and spindle drives and controls the various machining operations. See DNC, direct numerical control; NC, numerical control.
- countersink
countersink
Tool that cuts a sloped depression at the top of a hole to permit a screw head or other object to rest flush with the surface of the workpiece.
- cutting fluid
cutting fluid
Liquid used to improve workpiece machinability, enhance tool life, flush out chips and machining debris, and cool the workpiece and tool. Three basic types are: straight oils; soluble oils, which emulsify in water; and synthetic fluids, which are water-based chemical solutions having no oil. See coolant; semisynthetic cutting fluid; soluble-oil cutting fluid; synthetic cutting fluid.
- fixture
fixture
Device, often made in-house, that holds a specific workpiece. See jig; modular fixturing.
- gang cutting ( milling)
gang cutting ( milling)
Machining with several cutters mounted on a single arbor, generally for simultaneous cutting.
- interpolation
interpolation
Process of generating a sufficient number of positioning commands for the servomotors driving the machine tool so the path of the tool closely approximates the ideal path. See CNC, computer numerical control; NC, numerical control.
- interrupted cut
interrupted cut
Cutting tool repeatedly enters and exits the work. Subjects tool to shock loading, making tool toughness, impact strength and flexibility vital. Closely associated with milling operations. See shock loading.
- lapping
lapping
Finishing operation in which a loose, fine-grain abrasive in a liquid medium abrades material. Extremely accurate process that corrects minor shape imperfections, refines surface finishes and produces a close fit between mating surfaces.
- lathe
lathe
Turning machine capable of sawing, milling, grinding, gear-cutting, drilling, reaming, boring, threading, facing, chamfering, grooving, knurling, spinning, parting, necking, taper-cutting, and cam- and eccentric-cutting, as well as step- and straight-turning. Comes in a variety of forms, ranging from manual to semiautomatic to fully automatic, with major types being engine lathes, turning and contouring lathes, turret lathes and numerical-control lathes. The engine lathe consists of a headstock and spindle, tailstock, bed, carriage (complete with apron) and cross slides. Features include gear- (speed) and feed-selector levers, toolpost, compound rest, lead screw and reversing lead screw, threading dial and rapid-traverse lever. Special lathe types include through-the-spindle, camshaft and crankshaft, brake drum and rotor, spinning and gun-barrel machines. Toolroom and bench lathes are used for precision work; the former for tool-and-die work and similar tasks, the latter for small workpieces (instruments, watches), normally without a power feed. Models are typically designated according to their “swing,” or the largest-diameter workpiece that can be rotated; bed length, or the distance between centers; and horsepower generated. See turning machine.
- milling
milling
Machining operation in which metal or other material is removed by applying power to a rotating cutter. In vertical milling, the cutting tool is mounted vertically on the spindle. In horizontal milling, the cutting tool is mounted horizontally, either directly on the spindle or on an arbor. Horizontal milling is further broken down into conventional milling, where the cutter rotates opposite the direction of feed, or “up” into the workpiece; and climb milling, where the cutter rotates in the direction of feed, or “down” into the workpiece. Milling operations include plane or surface milling, endmilling, facemilling, angle milling, form milling and profiling.
- milling machine ( mill)
milling machine ( mill)
Runs endmills and arbor-mounted milling cutters. Features include a head with a spindle that drives the cutters; a column, knee and table that provide motion in the three Cartesian axes; and a base that supports the components and houses the cutting-fluid pump and reservoir. The work is mounted on the table and fed into the rotating cutter or endmill to accomplish the milling steps; vertical milling machines also feed endmills into the work by means of a spindle-mounted quill. Models range from small manual machines to big bed-type and duplex mills. All take one of three basic forms: vertical, horizontal or convertible horizontal/vertical. Vertical machines may be knee-type (the table is mounted on a knee that can be elevated) or bed-type (the table is securely supported and only moves horizontally). In general, horizontal machines are bigger and more powerful, while vertical machines are lighter but more versatile and easier to set up and operate.
- polishing
polishing
Abrasive process that improves surface finish and blends contours. Abrasive particles attached to a flexible backing abrade the workpiece.
- toolpath( cutter path)
toolpath( cutter path)
2-D or 3-D path generated by program code or a CAM system and followed by tool when machining a part.
Contributors
J.W. Done Corp.
888-535-3663
www.jwdone.com
Norton | Saint-Gobain Abrasives
800-551-4413
www.nortonabrasives.com
Tapmatic Corp.
800-854-6019
www.tapmatic.com