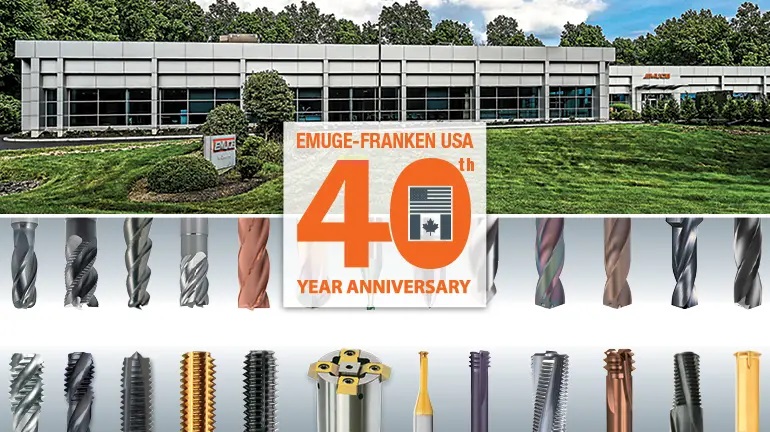
This year, Emuge-Franken USA, a manufacturer of taps, thread mills, drills, end mills, and other rotary cutting tools, is celebrating its 40th anniversary.
Emuge-Franken officially entered the United States' marketplace with a handful of employees under the name Emuge in 1984 in a Northborough, Massachusetts, sales and warehousing facility. The Emuge brand was aggressively marketed and demand for EMUGE products grew rapidly. Today 40 years later, Emuge-Franken is recognized as a leading brand in cutting tool innovation, quality, and performance throughout a wide range of industries and products across North America, with over 80 employees in the U.S. and Canada.
“We are very proud to celebrate this milestone,” said Bob Hellinger, president of Emuge-Franken USA. “Over the past forty years, we have experienced strong and continual growth in North America, which is a testament to our people and our reputation for quality, innovation, and expertise in the metalworking manufacturing marketplace.”
Since Emuge was incorporated in the U.S., many changes and developments have taken place with the company. Sustained growth required more employees, a larger warehouse, and a machining technology center. In 2006, the company constructed an all-new 50,000-square-foot facility in West Boylston, Massachusetts.
With more employees and a larger facility, product line expansion continued steadily for the next 10 years. In 2015, Emuge began manufacturing some of the company’s products in the U.S. with the opening of a reconditioning center for Emuge cutting tools. Emuge U.S.A. headquarters were expanded again in 2019, doubling the size of its U.S. facility to over 100,000 square feet with an expanded technology center and additional manufacturing space. By 2021, the Emuge Corp. name was officially changed in North America to “Emuge-Franken”. The new branding was incorporated in recognition of Emuge’s Franken milling division and the addition of full-scale carbide end mill manufacturing in West Boylston.
Today, Emuge-Franken USA is committed to further expanding its precision engineering capabilities to innovate and manufacture high-quality cutting tools that meet the challenges of industries such as aerospace and space exploration, automotive, and medical. The company’s growth strategy is focused on leveraging the most advanced cutting tool technology to increase productivity for machinists, job shop owners and OEMs. By continuously developing innovative products and strengthening customer relationships, Emuge-Franken USA is poised to help shape the future of cutting tool technology for manufacturing excellence. As the company grows, it never loses sight of what made it successful: craftsmanship, innovation, and quality.
Contact Details
Related Glossary Terms
- gang cutting ( milling)
gang cutting ( milling)
Machining with several cutters mounted on a single arbor, generally for simultaneous cutting.
- metalworking
metalworking
Any manufacturing process in which metal is processed or machined such that the workpiece is given a new shape. Broadly defined, the term includes processes such as design and layout, heat-treating, material handling and inspection.
- milling
milling
Machining operation in which metal or other material is removed by applying power to a rotating cutter. In vertical milling, the cutting tool is mounted vertically on the spindle. In horizontal milling, the cutting tool is mounted horizontally, either directly on the spindle or on an arbor. Horizontal milling is further broken down into conventional milling, where the cutter rotates opposite the direction of feed, or “up” into the workpiece; and climb milling, where the cutter rotates in the direction of feed, or “down” into the workpiece. Milling operations include plane or surface milling, endmilling, facemilling, angle milling, form milling and profiling.
- milling machine ( mill)
milling machine ( mill)
Runs endmills and arbor-mounted milling cutters. Features include a head with a spindle that drives the cutters; a column, knee and table that provide motion in the three Cartesian axes; and a base that supports the components and houses the cutting-fluid pump and reservoir. The work is mounted on the table and fed into the rotating cutter or endmill to accomplish the milling steps; vertical milling machines also feed endmills into the work by means of a spindle-mounted quill. Models range from small manual machines to big bed-type and duplex mills. All take one of three basic forms: vertical, horizontal or convertible horizontal/vertical. Vertical machines may be knee-type (the table is mounted on a knee that can be elevated) or bed-type (the table is securely supported and only moves horizontally). In general, horizontal machines are bigger and more powerful, while vertical machines are lighter but more versatile and easier to set up and operate.