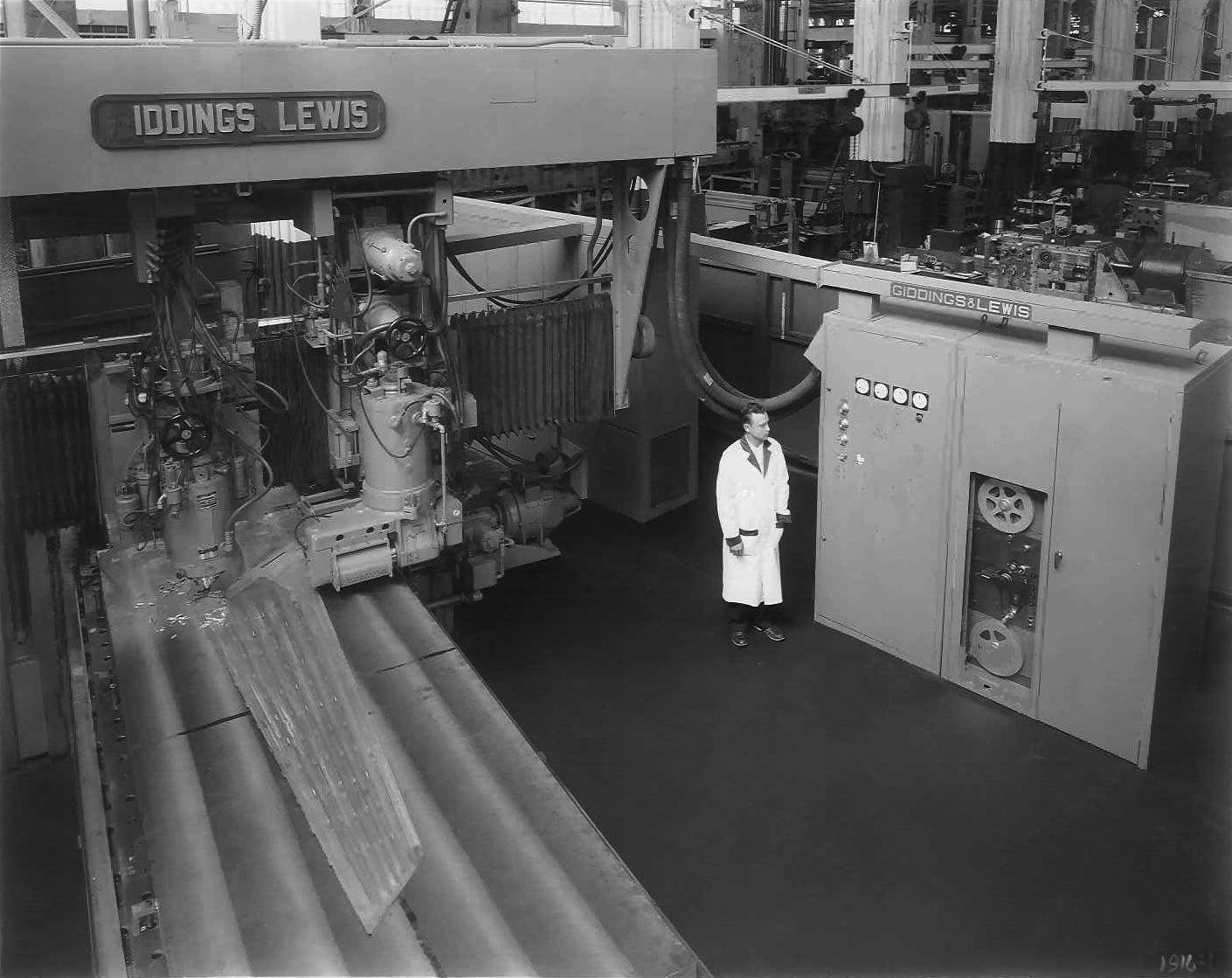
FOND DU LAC, Wis. – 2019 is a big year for Fives Giddings & Lewis as it celebrates its 160th anniversary, with a special celebration happening this summer. What started back in 1859 as a lumber equipment job shop has grown and evolved with the demands of the markets, touching several industries along the way. Fives Giddings & Lewis still stands today in the same location as in 1859, at the corner of Doty and Rees Street. In 1902 we began producing machine tools, starting with engine lathes and boring mills. During WWI and WWII a large portion of the business was in government work as our nation’s defense department and military took first priority. In 1955 the first commercially available CNC was created in partnership with MIT. Current innovations include the Integrated Contouring Head and new Vertical Turning Center and Milling Product Lines. The company has been part of the Fives Group since 2013.
Fives Giddings & Lewis will be running a couple of contests throughout 2019.
Invitations to the celebration later this year will be sent, welcoming customers, suppliers and other key industry partners for an open house event. As part of the year-long celebration of events in 2019, Fives Giddings & Lewis is running a couple of contests! Think you have the longest operating Giddings & Lewis machine on your shop floor? Submit a video of it still in operation at your facility to be entered. Giddings & Lewis will also share the top 160 reasons “Why Buy G & L” throughout the year. The top 3 reasons submitted will receive a prize. If you would like to make sure your name is on the invitation list to join our open house celebration and see the latest machine tool technology, or, if you would like more information on the contests, please contact Kimberly Prophett ([email protected]).
We can’t wait to see you in June!
Contact Details
Related Glossary Terms
- boring
boring
Enlarging a hole that already has been drilled or cored. Generally, it is an operation of truing the previously drilled hole with a single-point, lathe-type tool. Boring is essentially internal turning, in that usually a single-point cutting tool forms the internal shape. Some tools are available with two cutting edges to balance cutting forces.
- computer numerical control ( CNC)
computer numerical control ( CNC)
Microprocessor-based controller dedicated to a machine tool that permits the creation or modification of parts. Programmed numerical control activates the machine’s servos and spindle drives and controls the various machining operations. See DNC, direct numerical control; NC, numerical control.
- gang cutting ( milling)
gang cutting ( milling)
Machining with several cutters mounted on a single arbor, generally for simultaneous cutting.
- milling
milling
Machining operation in which metal or other material is removed by applying power to a rotating cutter. In vertical milling, the cutting tool is mounted vertically on the spindle. In horizontal milling, the cutting tool is mounted horizontally, either directly on the spindle or on an arbor. Horizontal milling is further broken down into conventional milling, where the cutter rotates opposite the direction of feed, or “up” into the workpiece; and climb milling, where the cutter rotates in the direction of feed, or “down” into the workpiece. Milling operations include plane or surface milling, endmilling, facemilling, angle milling, form milling and profiling.
- turning
turning
Workpiece is held in a chuck, mounted on a face plate or secured between centers and rotated while a cutting tool, normally a single-point tool, is fed into it along its periphery or across its end or face. Takes the form of straight turning (cutting along the periphery of the workpiece); taper turning (creating a taper); step turning (turning different-size diameters on the same work); chamfering (beveling an edge or shoulder); facing (cutting on an end); turning threads (usually external but can be internal); roughing (high-volume metal removal); and finishing (final light cuts). Performed on lathes, turning centers, chucking machines, automatic screw machines and similar machines.