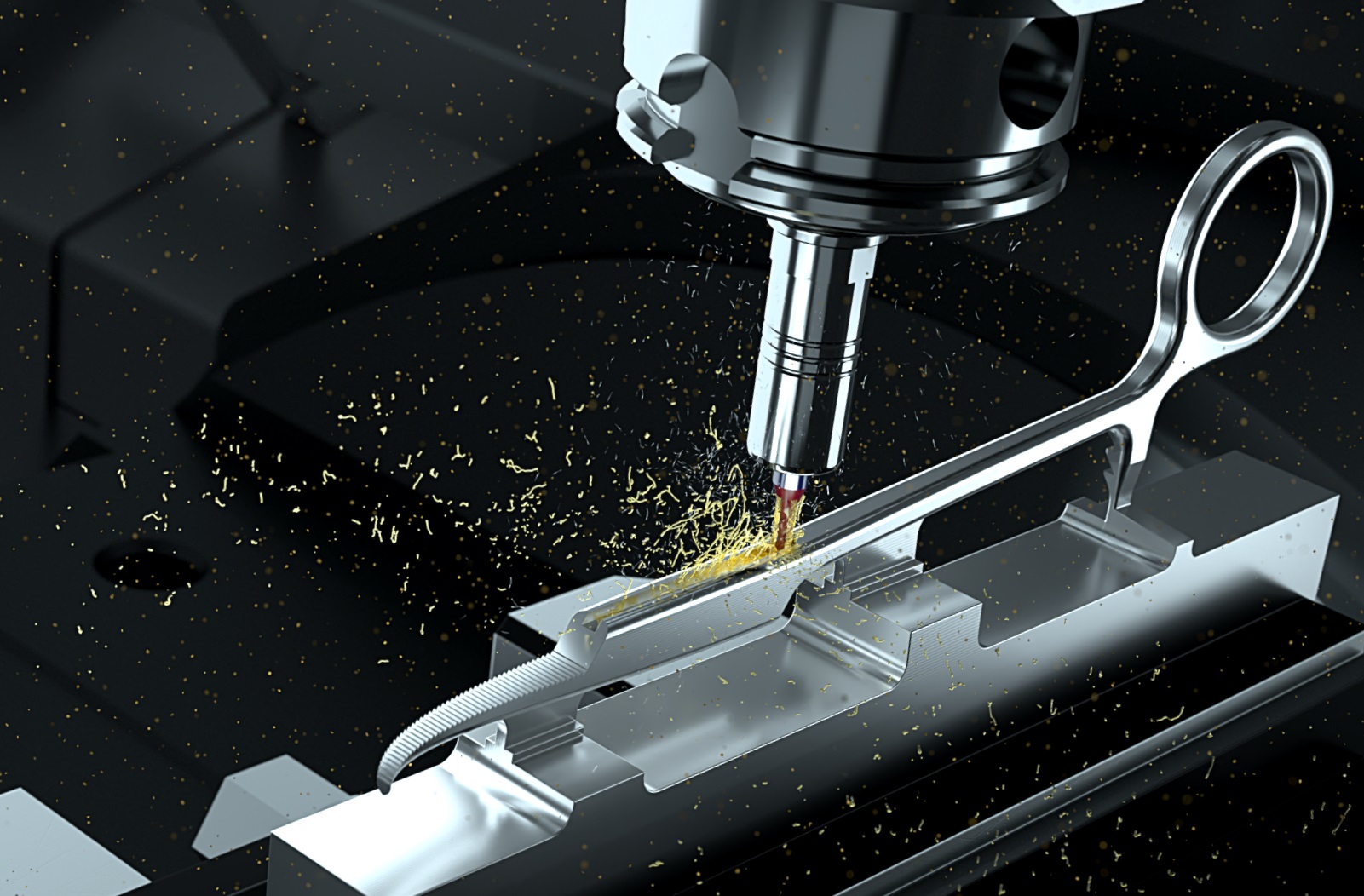
The hemostatic clamp. An inconspicuous tool, but one that saves lives every single day.
The clamp is a crucial and reliable instrument to stop bleeding. In the early stages of surgery, for instance, it is common for the first incision to be lined with hemostats that occlude, or block, the blood vessels, which are then tied off with a ligature.
The clamp bears a certain resemblance to surgical scissors, but instead of cutting surfaces, it has two serrated tips. The instrument has handles that can be held in position by a locking mechanism, which consists of a series of interlocking teeth that allow the user to adjust the clamping force of the pliers.
The structure of the tip consists of a fine ribbing that prevents the blood vessel from being damaged. Since it is used in open wounds, it is usually made of stainless steel, which can be a difficult material when it comes to machining. In addition, it must have a perfect surface finish. These are the mechanical challenges that medical device manufacturers must face.

The Swiss precision tool manufacturer Mikron Tool proves that overcoming these challenges is a goal that is within reach. “Our Technology Centre has dealt intensively with the production of this surgical instrument,” said Markus Schnyder, president of Mikron Tool International.
Schnyder said that customer demands are clearly defined: radically reduced production times, complete production in a single clamping, reduction of supports, optimal surface quality, and burr-free edges. This was a challenge, but so was the 17-4PH martensite stainless steel material. It offers excellent corrosion resistance, wear-resistance and hardness and is therefore popular for use in surgical instruments. Unfortunately, when it comes to machinability, it isn’t such a popular choice. On a scale of 1 (= bad) to 10 (= good), it gets a 3. The whole project was a real challenge, he said. The magic lies in ensuring perfect interplay between all components.
5-axis machining
Mikron Tool opted for a dynamic process with milling from a solid blank. A highly dynamic 5-axis machining center DMP 70 from DMG MORI was selected for the machine. By combining several machining processes, the workpiece can be almost completely machined in just one clamping with standardized milling cutters from Mikron Tool.
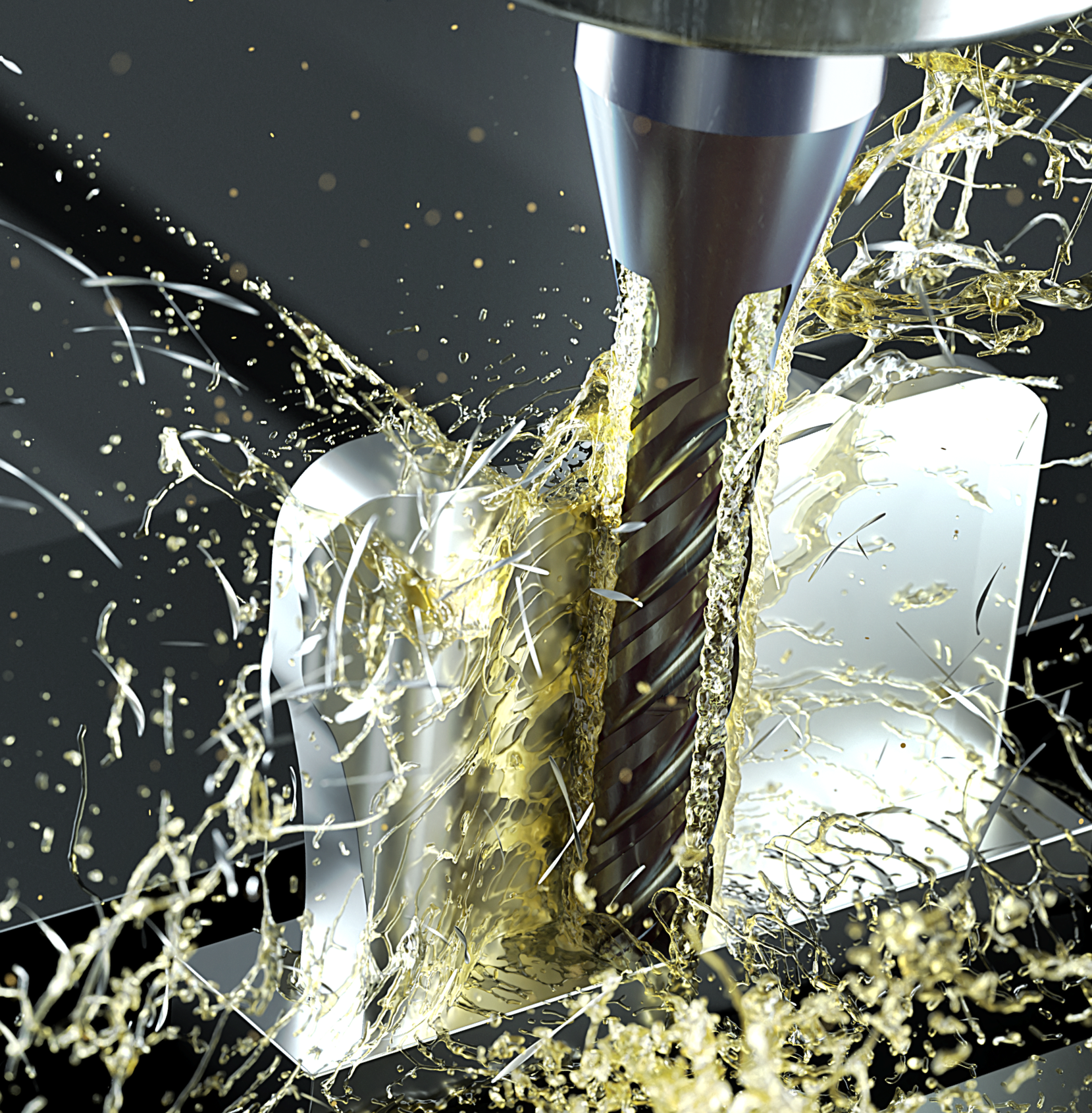
Internal cooling runs through the machine spindle. The cooling channels, integrated into the shank, guide the coolant directly to the cutting edges and ensure continuous and targeted cooling in every position. At the same time, chips are continuously flushed out of the milling zone by a powerful cooling jet. This benefits the surface quality of the component and the tool life. Continuous tool cooling also permits high application parameters in terms of cutting speed, feed, and in-feed, which significantly reduces machining times.
Clamping is tricky when milling from a solid blank. It is crucial to ensure all-around, unrestricted access to the workpiece without any obstructions so that the tools are clamped as reduced as possible. Because of the zero-point clamping system was chosen by Mikron Tool, the workpiece, fixtures, and clamping devices can be positioned, fixed and clamped quickly and precisely in one operation. This drastically reduces set-up times.
This is a decisive factor for optimizing process chain cost savings. To minimise the use of material, the blank was fixed at a clamping height of only 3mm. But care is required: this determines the entire milling strategy, as the lateral forces must be kept to a minimum.
Dynamic milling strategies
The machine is dynamic, as is the milling strategy. All in all, Mikron Tool uses 10 tools to machine a hemostat, all specially designed for machining stainless steel: a plunge cutter, various 4-tooth roughing and finishing cutters, a deburring cutter and two dovetail cutters.
The R&D Manager Gotti, Ph.D. highlights a few details of the milling strategy: “Due to zero-point clamping and completion in just one clamping, our main concern was to avoid high forces. Our professionals went for a dynamic strategy: high cutting speeds (up to 220 m/min when roughing), high feed rates fz (up to 0.15 mm) and a high axial (ap) but low radial in-feed (ae).
To achieve high feed rates when roughing, 4-tooth milling cutters were used. When milling out the eye of the handle, spiral interpolation proved to be time-saving. To achieve the fine corrugations on the tip, a dovetail cutter was used, which resulted in rapid processing thanks to its special shape.
The elongated groove on the inner contour was made using a 3-tooth plunge cutter. This produced a small, but sharp edge during milling, which proved to be particularly problematic. However, the workpiece could be deburred without having to change clamping position, with the use of a spherical deburring cutter (CrazyMill Radiuschamfer or CrazyMill chamfer).
The teeth of the locking mechanism were cut in one of the last steps using another special tool. The last step consisted of separating the workpiece from the raw blank and reducing the number of supports to a minimum. It was obvious that post-processing needed to be limited as well, to keep costs down.
The hemostat, which has now been almost perfectly machined, still requires further machining because the clamps must be completely burr-free and ensure a secure grip 100% of the time. Surgeons in the operating room will appreciate it.
The result must be right
To get the most out of production, a perfect machining strategy must take center stage. Machine, tools, clamping, cooling: a smooth interplay of all parts, coordinated down to the last detail, to deliver the desired result. Processing time was reduced by 46% (from 65 to 35 minutes) and the required surface quality of Ra 0.4 µm was significantly improved by achieving 0.2 µm. The values for Rz were 0.6 µm.
“Increasingly, achieving higher levels of medical performance comes down to mastering an interdisciplinary synergy between different technologies,” said Alberto Gotti. “That’s why the drive to innovate and research activities of the Mikron Tool company, together with their collaboration with partners at all levels, are crucial in achieving such service.”
Contact Details
Contact Details
Related Glossary Terms
- coolant
coolant
Fluid that reduces temperature buildup at the tool/workpiece interface during machining. Normally takes the form of a liquid such as soluble or chemical mixtures (semisynthetic, synthetic) but can be pressurized air or other gas. Because of water’s ability to absorb great quantities of heat, it is widely used as a coolant and vehicle for various cutting compounds, with the water-to-compound ratio varying with the machining task. See cutting fluid; semisynthetic cutting fluid; soluble-oil cutting fluid; synthetic cutting fluid.
- corrosion resistance
corrosion resistance
Ability of an alloy or material to withstand rust and corrosion. These are properties fostered by nickel and chromium in alloys such as stainless steel.
- cutting speed
cutting speed
Tangential velocity on the surface of the tool or workpiece at the cutting interface. The formula for cutting speed (sfm) is tool diameter 5 0.26 5 spindle speed (rpm). The formula for feed per tooth (fpt) is table feed (ipm)/number of flutes/spindle speed (rpm). The formula for spindle speed (rpm) is cutting speed (sfm) 5 3.82/tool diameter. The formula for table feed (ipm) is feed per tooth (ftp) 5 number of tool flutes 5 spindle speed (rpm).
- dovetail cutter
dovetail cutter
Cutter for milling dovetail slots. See milling cutter.
- feed
feed
Rate of change of position of the tool as a whole, relative to the workpiece while cutting.
- gang cutting ( milling)
gang cutting ( milling)
Machining with several cutters mounted on a single arbor, generally for simultaneous cutting.
- hardness
hardness
Hardness is a measure of the resistance of a material to surface indentation or abrasion. There is no absolute scale for hardness. In order to express hardness quantitatively, each type of test has its own scale, which defines hardness. Indentation hardness obtained through static methods is measured by Brinell, Rockwell, Vickers and Knoop tests. Hardness without indentation is measured by a dynamic method, known as the Scleroscope test.
- interpolation
interpolation
Process of generating a sufficient number of positioning commands for the servomotors driving the machine tool so the path of the tool closely approximates the ideal path. See CNC, computer numerical control; NC, numerical control.
- machinability
machinability
The relative ease of machining metals and alloys.
- machining center
machining center
CNC machine tool capable of drilling, reaming, tapping, milling and boring. Normally comes with an automatic toolchanger. See automatic toolchanger.
- martensite
martensite
Formed during rapid cooling of austenite at the temperature rate higher than 500º F (260º C) per second. Such rapid cooling causes restructuring of crystalline lattice of gamma iron into crystalline lattice of alpha iron in which carbon is fully dissolved. Because only 0.04 percent carbon can be dissolved in alpha iron, the excessive amount of carbon transforms into supersaturated solution of carbon in alpha iron. This type of solution is called martensite, which is characterized by an angular needlelike brittle structure and high hardness (greater than 60 HRC).
- milling
milling
Machining operation in which metal or other material is removed by applying power to a rotating cutter. In vertical milling, the cutting tool is mounted vertically on the spindle. In horizontal milling, the cutting tool is mounted horizontally, either directly on the spindle or on an arbor. Horizontal milling is further broken down into conventional milling, where the cutter rotates opposite the direction of feed, or “up” into the workpiece; and climb milling, where the cutter rotates in the direction of feed, or “down” into the workpiece. Milling operations include plane or surface milling, endmilling, facemilling, angle milling, form milling and profiling.
- shank
shank
Main body of a tool; the portion of a drill or similar end-held tool that fits into a collet, chuck or similar mounting device.