Professional machinists searching for technical assistance on the internet would do well to check out Machiningdoctor.com, a website launched in November 2020 by a mechanical engineer with more than 30 years in the industry.
Erez Speiser, who spent much of his machining career working at Iscar headquarters in northern Israel, said he developed the Machiningdoctor.com website out of boredom during the COVID-19 pandemic. As the website grew—it now has 27 machining related calculators and a reported 250,000 page views per month—Speiser decided to make his online endeavor a full-time job as of March 2023.
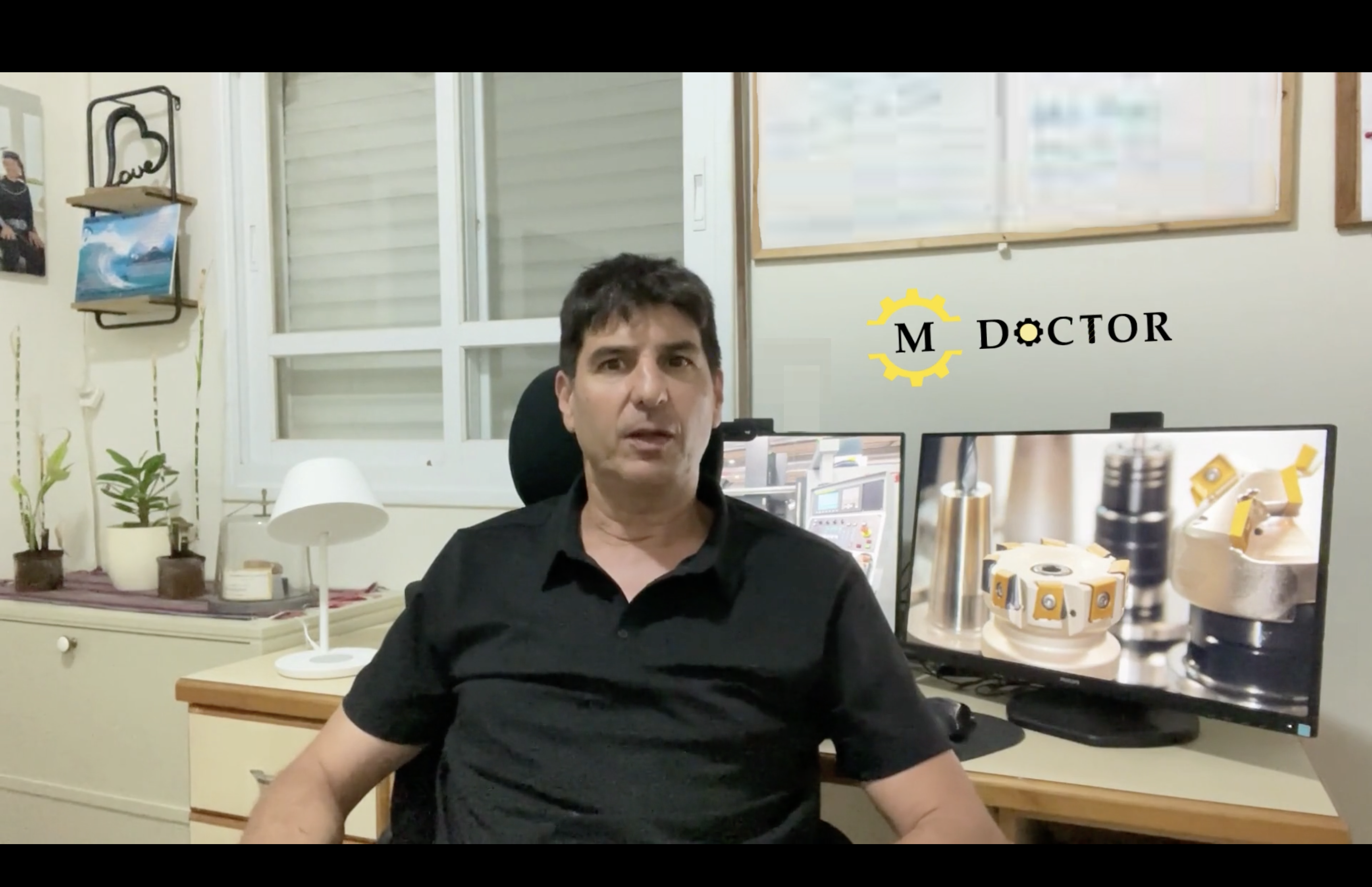
Indeed, the website contains a wealth of information that is well-organized and bound to be of interest to professional machinists.
The calculators offered range from simple conversion tools to a more complex speeds and feeds calculator that provides cutting condition recommendations based on dozens of parameters, according to Speiser. Here is a list of the calculators offered on the website:
- Advanced Speed and Feed Calculator
- Advanced Thread Calculator
- Basic Milling Calculator
- Chip Thinning Calculator
- Chip Load Calculator
- Cut Depth Optimizer
- Basic Turning Calculator
- Surface Finish Calculator
- Knurling Calculator
- Facing Calculator
- Metal Removal Rate Calculator
- Machining Power Calculator
- Hardness Converter
- Ra to Rz Converter
- Inch Decimal/Fraction Converter
- SFM to RPM Converter
- Imperial to Metric Converter
- Metric to Imperial Converter
- RPM to SFM Converter
- Carbide Grades Wizard
- Carbide Grades Converter
- Carbide Grades Comparison Tool
- Engineering Tolerances and Fits (ISO 286)
- Drilling Calculator
- True Position Calculator
- Tap Drill Size Calculator
- Sine Bar Calculator
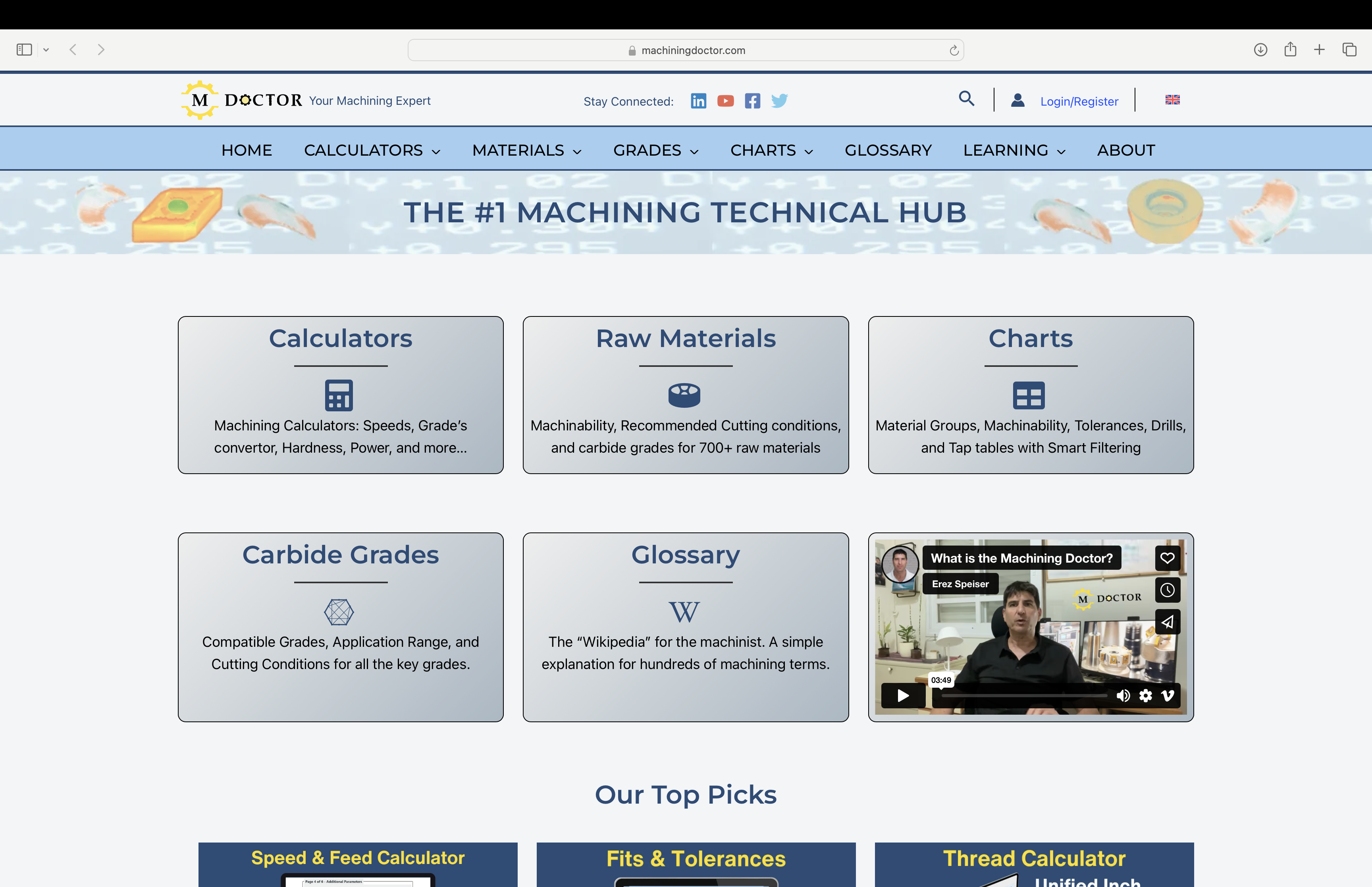
Visit the Machiningdoctor.com website to learn more. While the website carries advertising, Speiser offers an ad-free version of the website to visitors willing to pay a subscription fee of $1.50 per month.
Dennis Spaeth, publisher and owner of Cutting Tool Engineering, will welcome Speiser as the inaugural guest of Bourbon with the Editor, a manufacturing podcast for CTE's 100,000-plus audience of metalcutting professionals. Podcast will take place at 11 a.m. CST Thursday, March 7. More information to come.
Related Glossary Terms
- feed
feed
Rate of change of position of the tool as a whole, relative to the workpiece while cutting.
- gang cutting ( milling)
gang cutting ( milling)
Machining with several cutters mounted on a single arbor, generally for simultaneous cutting.
- hardness
hardness
Hardness is a measure of the resistance of a material to surface indentation or abrasion. There is no absolute scale for hardness. In order to express hardness quantitatively, each type of test has its own scale, which defines hardness. Indentation hardness obtained through static methods is measured by Brinell, Rockwell, Vickers and Knoop tests. Hardness without indentation is measured by a dynamic method, known as the Scleroscope test.
- knurling
knurling
Chipless material-displacement process that is usually accomplished on a lathe by forcing a knurling die into the surface of a rotating workpiece to create a pattern. Knurling is often performed to create a decorative or gripping surface and repair undersized shafts.
- metalcutting ( material cutting)
metalcutting ( material cutting)
Any machining process used to part metal or other material or give a workpiece a new configuration. Conventionally applies to machining operations in which a cutting tool mechanically removes material in the form of chips; applies to any process in which metal or material is removed to create new shapes. See metalforming.
- milling
milling
Machining operation in which metal or other material is removed by applying power to a rotating cutter. In vertical milling, the cutting tool is mounted vertically on the spindle. In horizontal milling, the cutting tool is mounted horizontally, either directly on the spindle or on an arbor. Horizontal milling is further broken down into conventional milling, where the cutter rotates opposite the direction of feed, or “up” into the workpiece; and climb milling, where the cutter rotates in the direction of feed, or “down” into the workpiece. Milling operations include plane or surface milling, endmilling, facemilling, angle milling, form milling and profiling.
- tap
tap
Cylindrical tool that cuts internal threads and has flutes to remove chips and carry tapping fluid to the point of cut. Normally used on a drill press or tapping machine but also may be operated manually. See tapping.
- turning
turning
Workpiece is held in a chuck, mounted on a face plate or secured between centers and rotated while a cutting tool, normally a single-point tool, is fed into it along its periphery or across its end or face. Takes the form of straight turning (cutting along the periphery of the workpiece); taper turning (creating a taper); step turning (turning different-size diameters on the same work); chamfering (beveling an edge or shoulder); facing (cutting on an end); turning threads (usually external but can be internal); roughing (high-volume metal removal); and finishing (final light cuts). Performed on lathes, turning centers, chucking machines, automatic screw machines and similar machines.