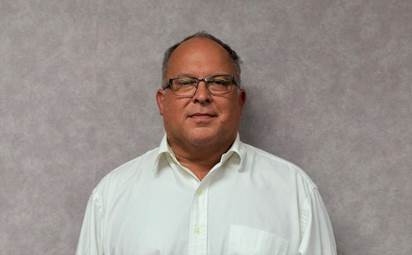
Kitagawa North-Tech Inc., Schaumburg, Ill., which manufactures standard chucks, advanced chucks, custom-engineered workholding and steady rests, hired Mike Johnston as regional sales manager. Mr. Johnston’s sales territory for Kitagawa NorthTech will include Pennsylvania, Ohio and Indiana of the Great Lakes regions of the USA. He is supporting Kitagawa’s offering of workholding which includes standard power chucks, advanced chucks, automated workholding (AJPS), engineered rotational and prismatic workholding solutions, turning and grinding line of steady rests, hydraulic cylinders, grippers and rotary tables.
Johnston will also sell and represent Kitagawa NorthTech’s inhouse repair, rebuild and preventative maintenance services. Johnston adds, “Kitagawa NorthTech’s Machine Tool accessories such as their Tri-Kote grease for lubricating power chucks and their digital grip force analyzer software and kit for measuring grip force are unique products that every machine shop should use for everyday chuck maintenance, as if you do not know your grip force you cannot optimize your machine tool to produce the maximum amount of parts safely.”
Johnston will be servicing and supporting a wide range of customers for the company including: end-users, OEMs, machine tool distributors and cutting tool distributors for the Kitagawa workholding and chuck offering. With over 30 years of metalworking industry experience, Johnston has an extensive and broad background. Throughout his career in metalworking and machining, he has worked in several capacities including: CNC programming, design engineering, applications engineering, machine tool sales and accessories sales, as well as owned a machine shop focused on machining parts for the Medical industry. Most recently Mr. Johnston was a regional sales manager for workholding manufacturer ATS Systems.
Mr. Johnston resides in Euclid, Michigan and will be report out of Kitagawa NorthTech’s headquarters and full-service manufacturing facility for the Americas based in Schaumburg, IL. The Kitagawa NorthTech facility features in-house design, engineering, manufacturing and repair services for workholding.
Contact Details
Related Glossary Terms
- chuck
chuck
Workholding device that affixes to a mill, lathe or drill-press spindle. It holds a tool or workpiece by one end, allowing it to be rotated. May also be fitted to the machine table to hold a workpiece. Two or more adjustable jaws actually hold the tool or part. May be actuated manually, pneumatically, hydraulically or electrically. See collet.
- computer numerical control ( CNC)
computer numerical control ( CNC)
Microprocessor-based controller dedicated to a machine tool that permits the creation or modification of parts. Programmed numerical control activates the machine’s servos and spindle drives and controls the various machining operations. See DNC, direct numerical control; NC, numerical control.
- grinding
grinding
Machining operation in which material is removed from the workpiece by a powered abrasive wheel, stone, belt, paste, sheet, compound, slurry, etc. Takes various forms: surface grinding (creates flat and/or squared surfaces); cylindrical grinding (for external cylindrical and tapered shapes, fillets, undercuts, etc.); centerless grinding; chamfering; thread and form grinding; tool and cutter grinding; offhand grinding; lapping and polishing (grinding with extremely fine grits to create ultrasmooth surfaces); honing; and disc grinding.
- metalworking
metalworking
Any manufacturing process in which metal is processed or machined such that the workpiece is given a new shape. Broadly defined, the term includes processes such as design and layout, heat-treating, material handling and inspection.
- turning
turning
Workpiece is held in a chuck, mounted on a face plate or secured between centers and rotated while a cutting tool, normally a single-point tool, is fed into it along its periphery or across its end or face. Takes the form of straight turning (cutting along the periphery of the workpiece); taper turning (creating a taper); step turning (turning different-size diameters on the same work); chamfering (beveling an edge or shoulder); facing (cutting on an end); turning threads (usually external but can be internal); roughing (high-volume metal removal); and finishing (final light cuts). Performed on lathes, turning centers, chucking machines, automatic screw machines and similar machines.