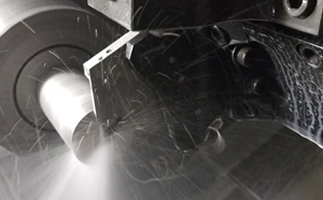
Minneapolis, MN – Premier Industries’ proprietary pressure regulators are subjected to tough duty in the oil & gas, aerospace and welding industries, but their precision performance is also critical, as regulator outlet pressure determines downstream pressure. In short, these parts are built to last and perform – made from a variety of materials and with tight tolerances throughout. The Minneapolis-based designer and manufacturer needed a solution for faster cycle times and a better finish on custom, grooved pressure regulator parts. It found it in the HORN base holder for system 960 and modular grooving system 845, used on a Euro Tech twin/spindle/twin turret lathe.
The application requires parting off 2.5" diameter, 316 stainless steel or aluminum into pieces that utilized a 3.0mm wide grooved insert. “The tooling system we were using was running very slow, and our finishes were not up to standard,” said Chuck Wimer, Operations manager at Premier Industries. “We went from cycle times of 1 minute, 40 seconds per part to 35 seconds per part, and cutting speeds went from 120 SFM to 250 SFM. Our finish improved from 51-55 Ra to 11-16 Ra consistently, and flatness went from .003-.0035 in. to .0001-.0003 in. across the 2.5-in. diameter. The parts are straight to under 0.001", so, we are very pleased with these results.”
With this approach, Premier also increased tool life from 25 parts per edge to 75 parts per edge, while reducing cost per part from $4.30 to $0.91. “This has had a huge impact on our operations and our bottom line,” added Wimer. “The solution is performing very well, actually better than we thought it would. We are vertically integrated, so after designing and producing the parts, we assemble and test them in our facilities. We’ve seen labor costs decrease in the downstream assembly phase simply because we’re working with better parts. The surface finishes and seals are excellent.”
Premier offers regulators with varying degrees of corrosion resistance, weights, strengths, etc., in size from 0.7" to 8.0", and equipment versatility is important in a custom-product environment. “We’ve been pleased with flexibility we have with this system, and its ability to process a wide variety of materials,” added Wimer. “We’ve cut diameters up to 2.75". Almost all of our parts are now touched by HORN tooling at some point.”
Located in Franklin, TN, Horn USA is a US subsidiary of Horn S.A. Luxemburg, and a supplier of grooving tools and developer of precision grooving technology. The company’s modular grooving system 845 consists of a base plate for turrets with BMT connection, a height-adjustable grooving tool holder and a matching cartridge range for various grooving widths and depths. The widths range in size from 2.0mm (0.078") to 4.0mm (0.157"), and the depths of cut range from 0.669" to 2.165". This allows the system to part off material as large as 4.33" diameter to center using a 4mm wide insert, and allows for coolant to be delivered directly to the cutting zone. The grooving tool holders with integrated coolant supply allow the cartridge heights to be adjusted and adapters set in a normal or overhead position, on the left or right of the grooving tool holder for maximum versatility.
Edited from information provided by HORN USA.
Related Glossary Terms
- chuck
chuck
Workholding device that affixes to a mill, lathe or drill-press spindle. It holds a tool or workpiece by one end, allowing it to be rotated. May also be fitted to the machine table to hold a workpiece. Two or more adjustable jaws actually hold the tool or part. May be actuated manually, pneumatically, hydraulically or electrically. See collet.
- coolant
coolant
Fluid that reduces temperature buildup at the tool/workpiece interface during machining. Normally takes the form of a liquid such as soluble or chemical mixtures (semisynthetic, synthetic) but can be pressurized air or other gas. Because of water’s ability to absorb great quantities of heat, it is widely used as a coolant and vehicle for various cutting compounds, with the water-to-compound ratio varying with the machining task. See cutting fluid; semisynthetic cutting fluid; soluble-oil cutting fluid; synthetic cutting fluid.
- corrosion resistance
corrosion resistance
Ability of an alloy or material to withstand rust and corrosion. These are properties fostered by nickel and chromium in alloys such as stainless steel.
- grooving
grooving
Machining grooves and shallow channels. Example: grooving ball-bearing raceways. Typically performed by tools that are capable of light cuts at high feed rates. Imparts high-quality finish.
- lathe
lathe
Turning machine capable of sawing, milling, grinding, gear-cutting, drilling, reaming, boring, threading, facing, chamfering, grooving, knurling, spinning, parting, necking, taper-cutting, and cam- and eccentric-cutting, as well as step- and straight-turning. Comes in a variety of forms, ranging from manual to semiautomatic to fully automatic, with major types being engine lathes, turning and contouring lathes, turret lathes and numerical-control lathes. The engine lathe consists of a headstock and spindle, tailstock, bed, carriage (complete with apron) and cross slides. Features include gear- (speed) and feed-selector levers, toolpost, compound rest, lead screw and reversing lead screw, threading dial and rapid-traverse lever. Special lathe types include through-the-spindle, camshaft and crankshaft, brake drum and rotor, spinning and gun-barrel machines. Toolroom and bench lathes are used for precision work; the former for tool-and-die work and similar tasks, the latter for small workpieces (instruments, watches), normally without a power feed. Models are typically designated according to their “swing,” or the largest-diameter workpiece that can be rotated; bed length, or the distance between centers; and horsepower generated. See turning machine.
- parting
parting
When used in lathe or screw-machine operations, this process separates a completed part from chuck-held or collet-fed stock by means of a very narrow, flat-end cutting, or parting, tool.
- turret lathe
turret lathe
Differs from engine lathe in that the normal compound rest is replaced by pivoting, multitool turrets mounted on the cross slide and tailstock. See lathe.