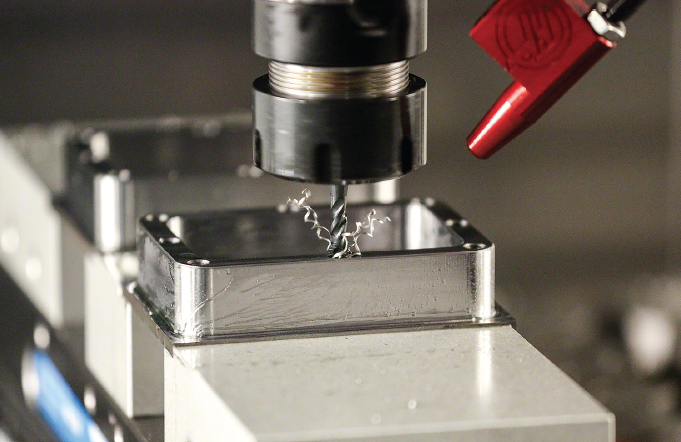
Standing in front of a ma-chining center, waiting for the drilling cycle to end so you can squirt some tapping compound into the holes is a big waste of time. But with challenging materials, such as Hastelloy or Inconel, it’s the only way to avoid a broken tap. Or is it?
Minimum-quantity lubrication, or MQL, has long been touted as an environmentally friendly and cost-effective alternative to flood coolant. MQL involves ap-plying a small quantity of oil mist directly to the cutting area, providing just the right amount of lubrication for efficient metal removal while removing heat from the tool/workpiece interface. But MQL can also be used to augment rather than replace flood coolant, elimi-nating the need for an operator to wait with squeeze bottle in hand.
Bryan O’Fallon, product technical specialist at Haas Automation Inc., Oxnard, Calif., said an increasing num-ber of shops are turning to MQL. “We recently intro-duced an MQL option on our machining centers, which works with the automatic air gun feature many of our customers are already familiar with. So instead of stop-ping the machine to apply some tapping lube, you can just turn off the coolant and use an M code to fire off the MQL. And for some applications, you can eliminate the flood entirely. It’s a nice option to have, especially with cutting fluid and fluid-disposal costs on the rise.”
Contact Details
Related Glossary Terms
- centers
centers
Cone-shaped pins that support a workpiece by one or two ends during machining. The centers fit into holes drilled in the workpiece ends. Centers that turn with the workpiece are called “live” centers; those that do not are called “dead” centers.
- coolant
coolant
Fluid that reduces temperature buildup at the tool/workpiece interface during machining. Normally takes the form of a liquid such as soluble or chemical mixtures (semisynthetic, synthetic) but can be pressurized air or other gas. Because of water’s ability to absorb great quantities of heat, it is widely used as a coolant and vehicle for various cutting compounds, with the water-to-compound ratio varying with the machining task. See cutting fluid; semisynthetic cutting fluid; soluble-oil cutting fluid; synthetic cutting fluid.
- cutting fluid
cutting fluid
Liquid used to improve workpiece machinability, enhance tool life, flush out chips and machining debris, and cool the workpiece and tool. Three basic types are: straight oils; soluble oils, which emulsify in water; and synthetic fluids, which are water-based chemical solutions having no oil. See coolant; semisynthetic cutting fluid; soluble-oil cutting fluid; synthetic cutting fluid.
- minimum-quantity lubrication
minimum-quantity lubrication
Use of cutting fluids of only a minute amount—typically at a flow rate of 50 to 500 ml/hr.—which is about three to four orders of magnitude lower than the amount commonly used in flood cooling. The concept addresses the issues of environmental intrusiveness and occupational hazards associated with the airborne cutting fluid particles on factory shop floors. The minimization of cutting fluid also saves lubricant costs and the cleaning cycle time for workpieces, tooling and machines. Sometimes referred to as “near-dry lubrication” or “microlubrication.”
- tap
tap
Cylindrical tool that cuts internal threads and has flutes to remove chips and carry tapping fluid to the point of cut. Normally used on a drill press or tapping machine but also may be operated manually. See tapping.
- tapping
tapping
Machining operation in which a tap, with teeth on its periphery, cuts internal threads in a predrilled hole having a smaller diameter than the tap diameter. Threads are formed by a combined rotary and axial-relative motion between tap and workpiece. See tap.
- turning
turning
Workpiece is held in a chuck, mounted on a face plate or secured between centers and rotated while a cutting tool, normally a single-point tool, is fed into it along its periphery or across its end or face. Takes the form of straight turning (cutting along the periphery of the workpiece); taper turning (creating a taper); step turning (turning different-size diameters on the same work); chamfering (beveling an edge or shoulder); facing (cutting on an end); turning threads (usually external but can be internal); roughing (high-volume metal removal); and finishing (final light cuts). Performed on lathes, turning centers, chucking machines, automatic screw machines and similar machines.