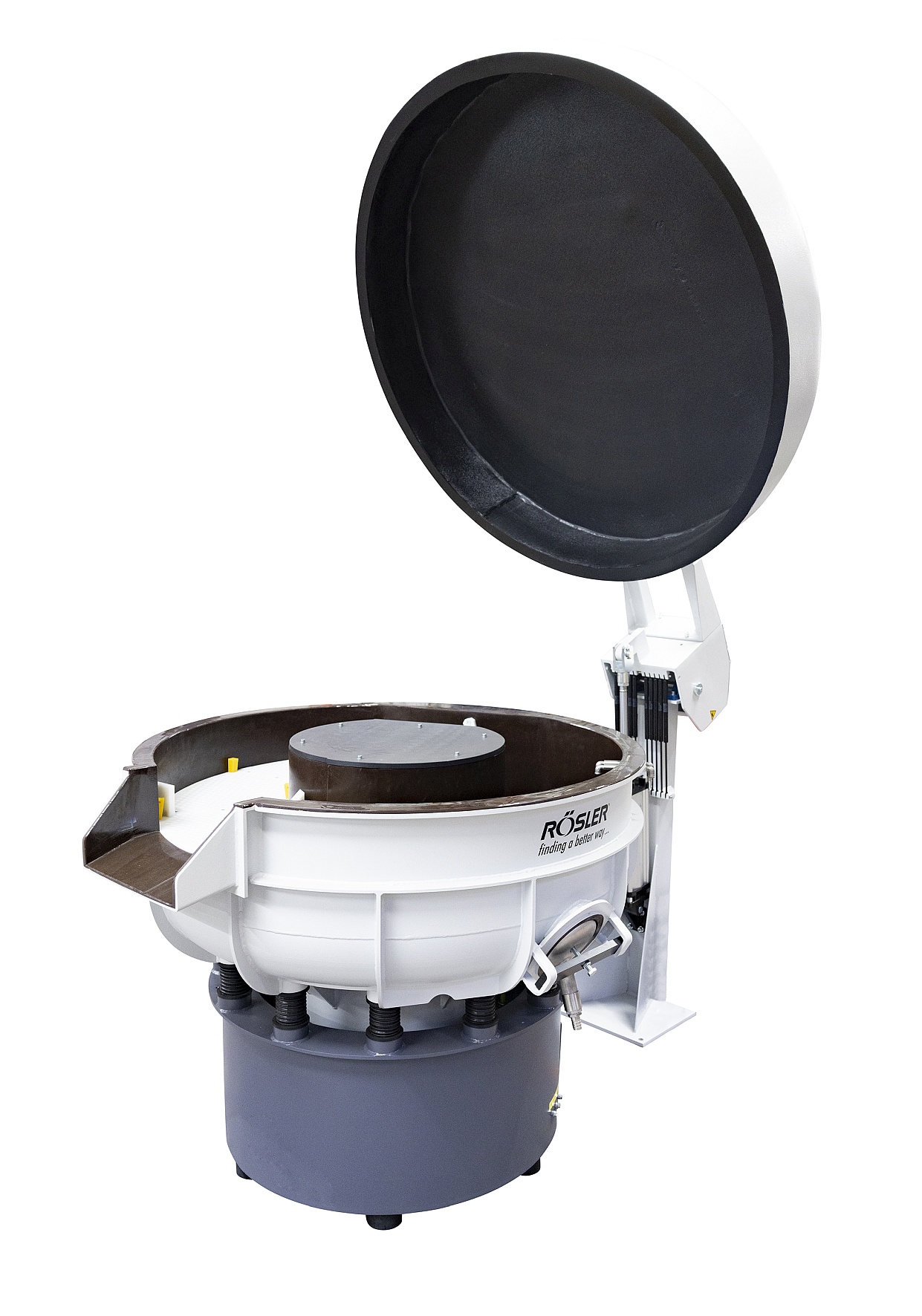
For more than 100 years The Ottobock company’s innovative products and services in the fields of prosthetics, orthotics, human mobility, and patient care have helped to achieve independence and quality of life for patients with restricted mobility.
The company’s developments include the microprocessor-controlled knee join C-Leg, controlled by an app, the computer-controlled leg prosthesis C-Brace, the multi-articulated hand Bebionic, and Juvo electrical wheelchairs.
Since 2018 Ottobock SE & Co. KGaA is also utilizing its mechanical and medical know-how for creating and maintaining a healthy working environment sustainably, for example, with the exoskeletal Paexo product range.
A commitment to improving quality of life helped this company, founded in 1919, to become the global technological leader in “wearable human bionics”. With more than 8,000 employees and a sales volume of over one billion Euros, the company is represented in approximately 60 countries.
Newly organized manufacturing

For the production of its products, the company is utilizing different manufacturing technologies. In this context, mass-finishing processes play an important role: On the one hand, they must ensure that the products meet all functional requirements, for example, to be free of burs. On the other hand, the mass finishing operations must produce an optically pleasing surface finish.
This also includes the creation of a highly homogeneous surface structure on the components, which are primarily made from aluminum and stainless steel.
Some products even require a high-gloss polish. For many years, Ottobock has been using equipment and consumables supplied by Rösler.
When the company was looking for new mass finishing solutions for producing its components in an optimized and more sustainable manner, it was only natural that it turned to Rösler for help. For the initial processing trials, the Customer Experience Center at Rösler represented the ideal platform.
The center is not only equipped with the latest equipment for practically all finishing technologies. But it can also resort to a portfolio of more than 15,000 media and compounds, all developed and produced in-house.
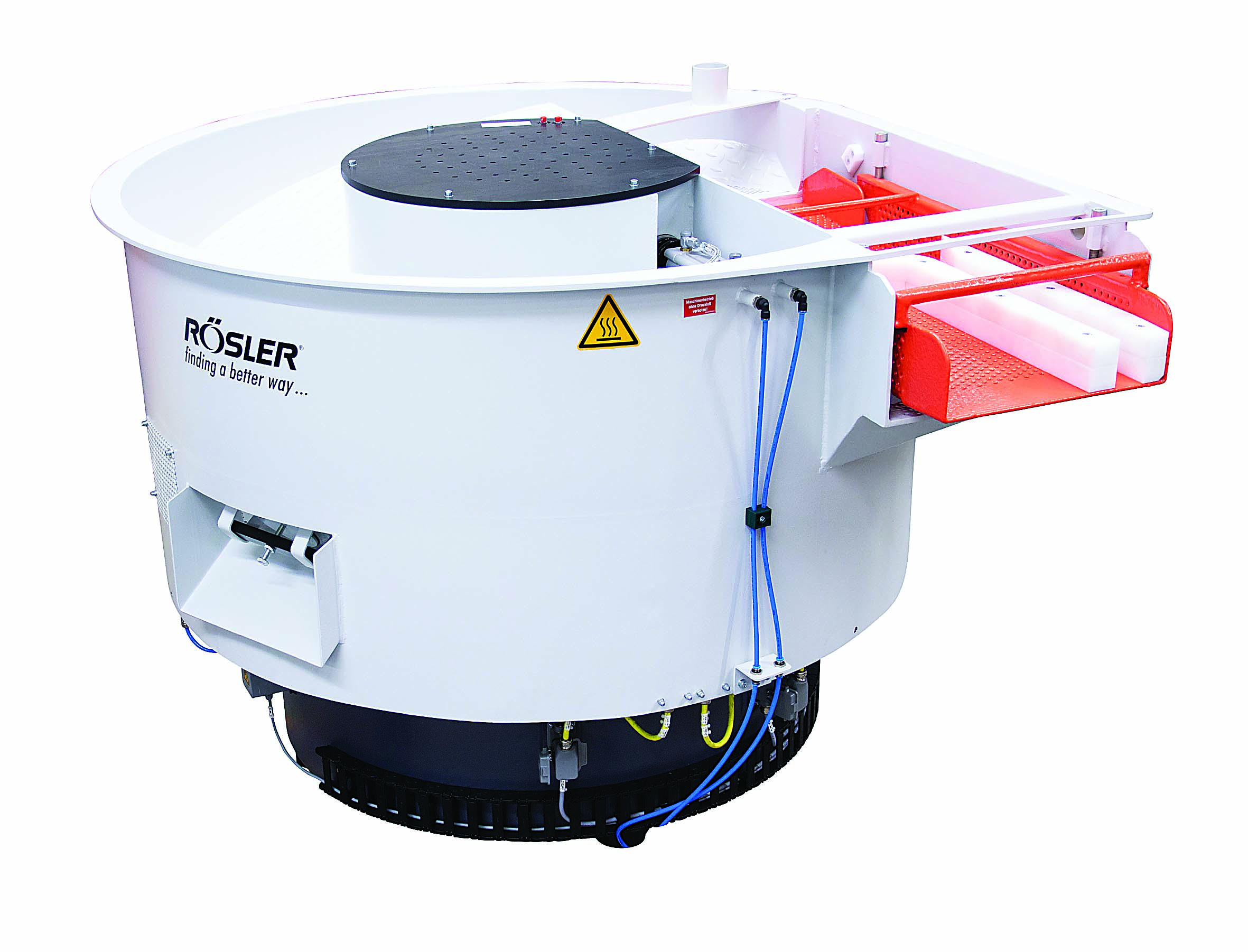
Replacing a process utilizing acidic compounds
Among other measures, an acid-based process for creating a high-gloss polish was replaced by a tailormade Keramo-Finish operation. This includes the utilization of a porcelain polishing media in combination with a special paste and a brightening compound.
The new, acid-free process allows the complete recycling of the process water. This has not only resulted in a significant decrease in water and compound consumption but also a sizable cost reduction.
The polishing operation takes place in a new, high-performance rotary vibrator, model R 780 EC. The special shape of the processing bowl creates a gentle, homogeneous flow of the media and workpiece mix. This ensures that small and delicate as well as large and bulky workpieces are quickly polished and separated efficiently and gently.
The same operational benefits are also achieved with the second new rotary vibrator, model R 420 EC. Together with specially selected media and compounds, Ottobock uses this machine for a broad spectrum of applications ranging from deburring and edge radiusing to surface smoothing.
For the eco-friendly cleaning and recycling of the process water, the two mass finishing machines are connected to a semi-automatic Rösler centrifugal cleaning system, model Z 800.
Energy-efficient drying operation
For drying, the finished work pieces Ottobock chose the latest version of the RT 550 Euro-DH rotary dryer, also supplied by Rösler.
This patented direct-heat dryer is equipped with an innovative heat-block heating system directly mounted to the base plate of the processing bowl. This ensures a highly efficient heat transfer with a minimum of heat loss. Thus, the dryer guarantees not only a quick, reliable, and spot-free drying operation, but also allows significant energy savings, which, compared to conventional drying systems, can amount up to 40%.
Therefore, the rotary dryer Euro-DH plays a key role in more effective energy management within the framework of the recently introduced standard DIN EN ISO 50001. The new dryer also helps reduce CO2 emissions and, as a result, represents an important contribution towards achieving the required environmental and climate targets.
Contact Details
Related Glossary Terms
- polishing
polishing
Abrasive process that improves surface finish and blends contours. Abrasive particles attached to a flexible backing abrade the workpiece.