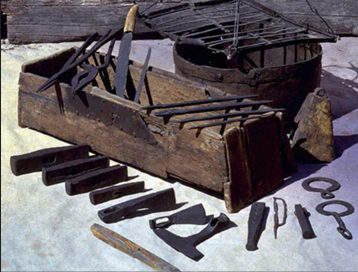
By Aaron Burnett
Toolboxes and bags go back a long way in human history. Once a tool was found to be useful, it became valuable and was worth keeping. A tool and the skills to use it are closely connected. Mechanical people object strongly to any interference with their tools just as musicians would object to someone tampering with their instruments.
In the industrial age, toolboxes became popular. While working as a mould maker, around 1904, Harry Gurstner made a chest for his personal use as a pattern-maker. His coworkers liked it and wanted him to make more. In 1906, he started his own tool chest company in Dayton, Ohio.
This type of box can still be purchased today. They are beautiful, made with felt lined drawers that display the tools and gages like jewelry. In many cases, the contents of these personal toolboxes cost more than $10,000.
Many employers had regular, interest free payroll deductions for tools and gages purchased by the machinist. Some companies even dictated which gages the machinist could buy.
This was done to ensure that only quality equipment was used. They replaced damaged gages free of charge from company stock so the machinist was never without what he or she needed.
Borrowing tools and gages

I started working in a shop in 1981 with nothing but an adjustable wrench and two screwdrivers. I had to borrow everything else including micrometers and calipers. The machinists who loaned these to me on an as-needed basis made it clear they expected to be asked before I borrowed.
I had to leave a token with my name on it in the drawer where I borrowed from, leaving that drawer slightly open. I had to make sure the gage or tool was cleaned and lubricated. I returned it where I had found it and took my token.
If I dropped something, I was responsible for repairs or replacement. In less than a year I had purchased 0-1” and 1-2” micrometers, 0-5” depth micrometers and 0-6” calipers. I bought these from older machinists who had upgraded their own gages. I also purchased a new locking tool box for my tools and micrometers.
Perishable supply
In the job shop where I started, we had a tool crib manned by a machinist. It was his job to make sure we never ran out of anything. He watched the remaining stock and ordered more based on known lead times and usage patterns.
He also kept a keen eye on usage. If I broke a tap he would give me another with the advice to check the drilled hole size and depth. If I broke another tap he was likely to get one of the experienced machinists to help me figure out what was wrong before he gave me a third chance. I learned quickly to keep losses to a minimum!
The personal toolbox in OEM shops
My next job was at a large company working in the role of Manufacturing Engineer. I thought that tools would be easier to get…I couldn’t have been more wrong! Managers had incentives based on low budgets and kept the machinists starved for tools and inserts.
To keep the machines running, machinists learned to keep perishable tool supplies in their personal toolbox. This meant they could keep running when the tool crib ran out … and caused the company tooling inventory to increase.
To combat this practice, many companies installed vending machines for perishable tooling. These systems require the employee to use their ID card to get perishable tooling. In many cases, the good machinist who is replacing the tooling before catastrophic failure gets demerits for using more tooling. As a result, product quality suffers.
The 5S and the Personal Tool Box
The word “Seiri” which best translates into “sorting” is the first word in 5S. When applied correctly everything that is ever needed gets a storage location1. Unfortunately the popular interpretation is “if hasn’t been used recently, throw it out.” In order to save valuable tooling, much of it ended up in personal toolboxes. This limited access to vital tooling. Managers often eliminated the “problem” by making the machinists take their boxes home. Usually the setup tooling was thrown out. Designated common tool boxes replaced personal ones. These social boxes are often poorly maintained and tools are usually missing. These problems can be reduced if some procedures are followed.
1. Key access - This is especially important when tools and gages disappear.
2. Inspection - Regular checks to make sure everything is still there and in good condition. This works best if one of the machinists takes ownership of the box. This could be a full time job in most situations.
3. Supply greater than demand - If two machinists need calipers at the same time, three calipers are needed. The third is a backup to cover when one set is out for calibration.
4. Make sure perishable tooling never runs out unless the process can shut down periodically. Because perishable tooling gets used in variable amounts in manufacturing, a buffer needs to be kept available for all tooling. This would include clamps, screws, seats, etc. By the way, a popular Japanese car manufacturer does this. Some perishable tooling vendors will keep open PO’s and only charge when the stock comes out of the drawer they stock. They often underestimate what will be used at a given moment.
5. Available on all shifts - If night shifts are running, they generally need access to more tools, hardware and gages because the support available is often greatly reduced.
Machine Maintenance & Tool Boxes
The number of tools and gages needed for machine maintenance is much larger. Most of the manufacturers I am familiar with require some or all of this maintenance to be done by their machinists. As the number of shifts supported goes up the supply in these toolboxes becomes critically important. The more diversified the machinist needs to be, the more tools and gages they will need. Here is a simple checklist to discover if your toolbox system is sustainable:
1. How many different tasks need to be performed? (See Table1)
![]() |
![]() |
![]() |
![]() |
2. How many shifts use this box?
3. How many people per shift are using the box?
4. Number of operating days per week (If 5 or less put down 1) If more than 5 days per week put down 10
5. Average age of machines which are supported by this box (years)?
6. Stock tools available? Refer to Table 3
7. Is the box kept locked with only those who need access supplied with a key? If “YES” put down 1, if “NO” put down 10.
8. Replenishment system? Refer to Table 2
Multiply all the answers from 1-8 above and divide by 1000 and check the answer against Table 4. If the result is higher than 100, make every effort to correct the problem.
Work satisfaction
A recent survey asked Shop owners and machinists the question: “What tools should a modern machinist expect be asked to purchase themselves? 74% responded that all but specialty tools should be supplied by the machinist. Ownership in the process brings great satisfaction in the results. For the machinist, that ownership is a pride that they have the skills and equipment to make quality product.
Contents of a non-maintenance machining toolbox
When it is difficult to obtain perishable tooling and hardware, there is a greater need for a “buffer drawer” full of critical and hard to get items. The following list shows what is needed assuming perishable tooling is always available. Bold print indicates best quality items are needed. Some items are optional depending on the types of work you are performing.
1. 0-6” Dial or Digital Calipers are essential but get the range that matches your work.
2. Edge Finder or wiggler - for locating edges.
3. Center Finder - for locating centers.
4. Dial Indicator with 0.0001”resolution - Used in setups and verification.
5. Deburring tool
6. 0-1” Micrometer - It’s reasonable that a set to 5-6” will be needed if work size warrants.
7. Machinists’ Precision Square
8. 6” Steel Ruler
9. Calculator / cell phone
10. Center Punch
11. Metric and English Allan wrench sets
12. Flat Stone.
13. Scotch brite
14. Mirror
15. Flashlight
16. Gage oil
17. Phillips and Flat screw driver sets
18. Open-Box Metric and English wrench sets.
19. T-Slot cleaners
20. Tap handles (large and small)
21. 0-6 Depth Micrometers
22. Vise grip set.
23. Pliers
24. Chanel locks
25. Thread gages (Optional)
26. Loc-Line Pliers (Optional)
27. Eyeglass kit with screwdriver (Optional)
28. Magnetizer (Optional)
29. Fine and course files
30. Rags or shop towels
31. Desiccant bags (Optional)
32. Dead blow hammer
33. 8” pipe to fit wrenches for breaking loose bolts (NEVER USED FOR TIGHTENING)
34. G / M /MACRO code standard meaning card (Optional)
35. Drill chart
36. Die blue.
37. Scriber
38. Magnetic Base
39. Ball peen hammer
40. Needle nose Pliers
41. Tweezers (Optional)
42. Set of easy-outs (Optional)
43. Die Bars (Optional)
44. Set of Plastic Shims
45. Set of Metal Shims
46. Wheel dressing stick set. (Optional)
47. Precision adjustable parallel set.
48. Rubber bands
49. Pencils / Pens / Sharpie / Grease Pencil
50. 1-2-3 Blocks (Optional)
51. Stem indicator
52. Thread profile gages
53. Flat plate
54. Left Hand drill
55. Machinist Handbook
56. Centering gage (fish)
Managing tool boxes
Managers need to be careful to get all the details before making toolbox decisions because the boxes play a vital role in the cost of operation and the quality of the product.
Seemingly small differences in product mix and processes can change toolbox needs considerably. For instance, some food processing plants inventory all tools at the end of each shift so no tool ends up in your breakfast food.3 If you own a job shop, your toolbox needs will be very different than an assembly line operation’s toolbox needs.
Likewise, if your average machine is 25 years old, your needs will be greater than a shop with new machines. There are some great toolbox resources for machinists on-line.4,5,6 If you are a manager or shop owner, seek expert help when determining toolbox needs.
The ultimate tool box
It is extremely important to give the machinist the right mental tools to be successful. Good machinists are highly intelligent and very creative. Encouraging their creativity usually unlocks tremendous potential. If management tries their ideas, the machinist is empowered to make other suggestions. I have found that while monetary rewards for success are always helpful, a simple handshake and thanks for a job well done are more encouraging in the long run. Machinists work their entire career to attain many areas of knowledge but there is always more to learn. For this reason, all good machinists learn from older machinists. Encouraging this mentoring will increase the overall health of an organization.
Author: Aaron Burnett is a quality and manufacturing engineer with more than 40 years of close tolerance work in the military, aerospace, medical device, automotive and glass industries.
Scott Tarntino assisted on this story. He is a retired Journeyman Toolmaker and Moldmaker with 35 years of experience.
Related Glossary Terms
- calibration
calibration
Checking measuring instruments and devices against a master set to ensure that, over time, they have remained dimensionally stable and nominally accurate.
- centering
centering
1. Process of locating the center of a workpiece to be mounted on centers. 2. Process of mounting the workpiece concentric to the machine spindle. See centers.
- centers
centers
Cone-shaped pins that support a workpiece by one or two ends during machining. The centers fit into holes drilled in the workpiece ends. Centers that turn with the workpiece are called “live” centers; those that do not are called “dead” centers.
- dressing
dressing
Removal of undesirable materials from “loaded” grinding wheels using a single- or multi-point diamond or other tool. The process also exposes unused, sharp abrasive points. See loading; truing.
- edge finder
edge finder
Gage mounted in the spindle of a vertical mill and used, while rotating, to find the center of a part relative to the toolholder.
- flat ( screw flat)
flat ( screw flat)
Flat surface machined into the shank of a cutting tool for enhanced holding of the tool.
- inner diameter ( ID)
inner diameter ( ID)
Dimension that defines the inside diameter of a cavity or hole. See OD, outer diameter.
- micrometer
micrometer
A precision instrument with a spindle moved by a finely threaded screw that is used for measuring thickness and short lengths.
- parallel
parallel
Strip or block of precision-ground stock used to elevate a workpiece, while keeping it parallel to the worktable, to prevent cutter/table contact.
- tap
tap
Cylindrical tool that cuts internal threads and has flutes to remove chips and carry tapping fluid to the point of cut. Normally used on a drill press or tapping machine but also may be operated manually. See tapping.
- tolerance
tolerance
Minimum and maximum amount a workpiece dimension is allowed to vary from a set standard and still be acceptable.