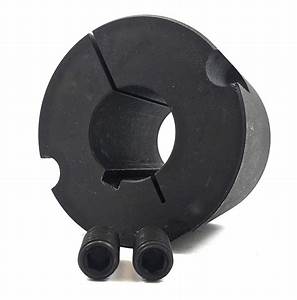
The following letter to the editor is from Kevin Quitberg.
Remember that before there was high-tech there was low-tech. And there still is low-tech! For example, boring and cutting a keyway in a tapered bushing is one of the most often performed tasks a maintenance machinist will perform.
Tapered bushings come in several different configurations, but they all perform the same function: the transmission of torque from a driver to a driven component. They will come with shallow keyways or standard depth keyways, with or without a flange and some small ones will come with no split on the axis.
Typically, a larger bushing comes in a class 30 gray iron. Some of the smaller bushings are sintered. I will almost always run a machine slower when drilling and boring the sintered material as it seems to be quite a bit harder and less friendly to machining than a simple gray iron casting. The exception to this is in an emergency situation, and the drill bit is considered a throwaway item, time being of much greater value.
When setting up a bushing for machining, you will notice that the flange and the taper on the bushing is rarely concentric. It is tempting to turn your chuck jaws around and chuck the flange, then drill and bore your bushing. Doing so will assure you that the sheave or sprocket the bushing is to fit will not run true. Resist doing it this (the easy) way. Use a 4-jaw chuck to clamp the bushing’s flange and indicate the face and OD of the taper. The bushing’s flange has no bearing on whether the bushing will be true in the component it is to fit. That is totally dependent on the tapered portion of the bushing.
It is also tempting to use a 3-jaw chuck and grip the bushing near the flange on the taper. Sometimes there is a small straight area near the flange that is not tapered and it is tempting to grip the bushing there with a 3-jaw chuck. You may get away with that, and you may not.
Before chucking the bushing, you will need to insert some shims in the split line of the bushing. You want enough shims here to keep the bushing from distorting under chucking pressure. So, the shims will be tight when inserting them into the split, but not so tight the bushing bore is actually deformed slightly. Don’t use a screwdriver or wedge to open the bushing to accommodate more shim pieces than necessary. I use the thin ½”-wide blades from a set of feeler gages. You can cut them to a convenient length, and it doesn’t hurt if they extend into the bore of the bushing as they will be machined away. Insert the shim pieces perpendicular to the bore of the bushing, preferably in the flange you are chucking.
I keep the shim pieces in my toolbox after finishing the bushing as they can usually be used over again. When inserting a thin blade, say 0.002” thick, sandwich it between a couple thicker blades. If you do not shim the split line and end up compressing the bushing during chucking you will not have a round bore after machining. This is important!
The drilling and machining itself is pretty straightforward. I rough-out cast iron with about anything handy, but I like to finish with a cut of approximately 0.005”/side with a C-20 carbide with a 1/32” nose radius and a sharp honed edge with approximately a 0.005” feed/revolution. I like that finish in gray iron.
A bushing without a flange is a little different, as there isn’t a safe and convenient way to hold the piece during machining. The split line will need to be shimmed during machining as well, just like the flanged bushing.
In this instance, you will use the sprocket or sheave as the "mandrel" to hold the bushing. After shimming the split, insert the bushing into the sheave and tighten it as you would during installation. In this case, you would indicate the face and OD of the sheave or sprocket rather than try to indicate the bushing. In a worst-case scenario, you could make a dummy piece to pull the bushing into. If your lathe is not big enough to hold the sheave or sprocket you can do the job in a vertical mill with some gage blocks and toe clamps, indicating the OD of the sheave to find center. Then drill and bore from that point. I like to keep worn out sheaves that will hold various size bushings on a shelf so I don’t have to try to hold a big piece in an awkward manner.
Some of the smaller bushings come with no axial split line. You will not need to shim them, but you absolutely do need to remember to cut the split after boring and keying the bushing. I like a vertical bandsaw for this. Wait until after you cut the keyway before doing this operation.
Now for cutting the keyway. In a maintenance shop the keyway will either be done with a broach or a keyseater. For me, the keyseater was almost always quicker on larger bushings. Many bushings will have "standard shallow" keyways. They will be 1/16” or 1/8” deep. The widths on standard shallow keyways can be up to 1¼” wide. Bushings are effective for transmitting torque. In a nonreciprocating or shock-loaded application, you often don’t even need a keyway. This is why a shallow keyway is all that is usually needed.
When using the keyseater (or a broach), position the split at 180° to the keyway. Clamp the bushing as you would any other item being keyed.
When broaching a bushing with the pre-existing split, you will need to put a hose clamp around the flange after inserting the broach carrier. Occasionally, a bushing will break at the split if the wall is relatively thin. It is more prevalent if the broach is a little bit dull and exerts a lot of pressure on the bushing sidewall as it travels through while cutting the keyway. You don’t want to have invested the time and effort thus far only to have the bushing break. So, make a mental note: remember the clamp.
The bushing you bored while contained in the sheave or sprocket should be broached in the same manner. You can take it out of the sheave to cut the keyway if using a keyseater.
I don’t know if your readers have any experience with machining cast iron, but I really like kerosene for a cutting fluid on gray iron. I use it when tapping and cutting keyways, rarely ever when just turning. The graphite in gray iron really makes a mess. Other than the mess, cast iron is a wonderful material in the applications it is designed for.
Related Glossary Terms
- bandsaw
bandsaw
Machine that utilizes an endless band, normally with serrated teeth, for cutoff or contour sawing. See saw, sawing machine.
- boring
boring
Enlarging a hole that already has been drilled or cored. Generally, it is an operation of truing the previously drilled hole with a single-point, lathe-type tool. Boring is essentially internal turning, in that usually a single-point cutting tool forms the internal shape. Some tools are available with two cutting edges to balance cutting forces.
- broach
broach
Tapered tool, with a series of teeth of increasing length, that is pushed or pulled into a workpiece, successively removing small amounts of metal to enlarge a hole, slot or other opening to final size.
- broaching
broaching
Operation in which a cutter progressively enlarges a slot or hole or shapes a workpiece exterior. Low teeth start the cut, intermediate teeth remove the majority of the material and high teeth finish the task. Broaching can be a one-step operation, as opposed to milling and slotting, which require repeated passes. Typically, however, broaching also involves multiple passes.
- bushing
bushing
Cylindrical sleeve, typically made from high-grade tool steel, inserted into a jig fixture to guide cutting tools. There are three main types: renewable, used in liners that in turn are installed in the jig; press-fit, installed directly in the jig for short production runs; and liner (or master), installed permanently in a jig to receive renewable bushing.
- chuck
chuck
Workholding device that affixes to a mill, lathe or drill-press spindle. It holds a tool or workpiece by one end, allowing it to be rotated. May also be fitted to the machine table to hold a workpiece. Two or more adjustable jaws actually hold the tool or part. May be actuated manually, pneumatically, hydraulically or electrically. See collet.
- cutting fluid
cutting fluid
Liquid used to improve workpiece machinability, enhance tool life, flush out chips and machining debris, and cool the workpiece and tool. Three basic types are: straight oils; soluble oils, which emulsify in water; and synthetic fluids, which are water-based chemical solutions having no oil. See coolant; semisynthetic cutting fluid; soluble-oil cutting fluid; synthetic cutting fluid.
- lathe
lathe
Turning machine capable of sawing, milling, grinding, gear-cutting, drilling, reaming, boring, threading, facing, chamfering, grooving, knurling, spinning, parting, necking, taper-cutting, and cam- and eccentric-cutting, as well as step- and straight-turning. Comes in a variety of forms, ranging from manual to semiautomatic to fully automatic, with major types being engine lathes, turning and contouring lathes, turret lathes and numerical-control lathes. The engine lathe consists of a headstock and spindle, tailstock, bed, carriage (complete with apron) and cross slides. Features include gear- (speed) and feed-selector levers, toolpost, compound rest, lead screw and reversing lead screw, threading dial and rapid-traverse lever. Special lathe types include through-the-spindle, camshaft and crankshaft, brake drum and rotor, spinning and gun-barrel machines. Toolroom and bench lathes are used for precision work; the former for tool-and-die work and similar tasks, the latter for small workpieces (instruments, watches), normally without a power feed. Models are typically designated according to their “swing,” or the largest-diameter workpiece that can be rotated; bed length, or the distance between centers; and horsepower generated. See turning machine.
- milling machine ( mill)
milling machine ( mill)
Runs endmills and arbor-mounted milling cutters. Features include a head with a spindle that drives the cutters; a column, knee and table that provide motion in the three Cartesian axes; and a base that supports the components and houses the cutting-fluid pump and reservoir. The work is mounted on the table and fed into the rotating cutter or endmill to accomplish the milling steps; vertical milling machines also feed endmills into the work by means of a spindle-mounted quill. Models range from small manual machines to big bed-type and duplex mills. All take one of three basic forms: vertical, horizontal or convertible horizontal/vertical. Vertical machines may be knee-type (the table is mounted on a knee that can be elevated) or bed-type (the table is securely supported and only moves horizontally). In general, horizontal machines are bigger and more powerful, while vertical machines are lighter but more versatile and easier to set up and operate.
- outer diameter ( OD)
outer diameter ( OD)
Dimension that defines the exterior diameter of a cylindrical or round part. See ID, inner diameter.
- tapping
tapping
Machining operation in which a tap, with teeth on its periphery, cuts internal threads in a predrilled hole having a smaller diameter than the tap diameter. Threads are formed by a combined rotary and axial-relative motion between tap and workpiece. See tap.
- turning
turning
Workpiece is held in a chuck, mounted on a face plate or secured between centers and rotated while a cutting tool, normally a single-point tool, is fed into it along its periphery or across its end or face. Takes the form of straight turning (cutting along the periphery of the workpiece); taper turning (creating a taper); step turning (turning different-size diameters on the same work); chamfering (beveling an edge or shoulder); facing (cutting on an end); turning threads (usually external but can be internal); roughing (high-volume metal removal); and finishing (final light cuts). Performed on lathes, turning centers, chucking machines, automatic screw machines and similar machines.