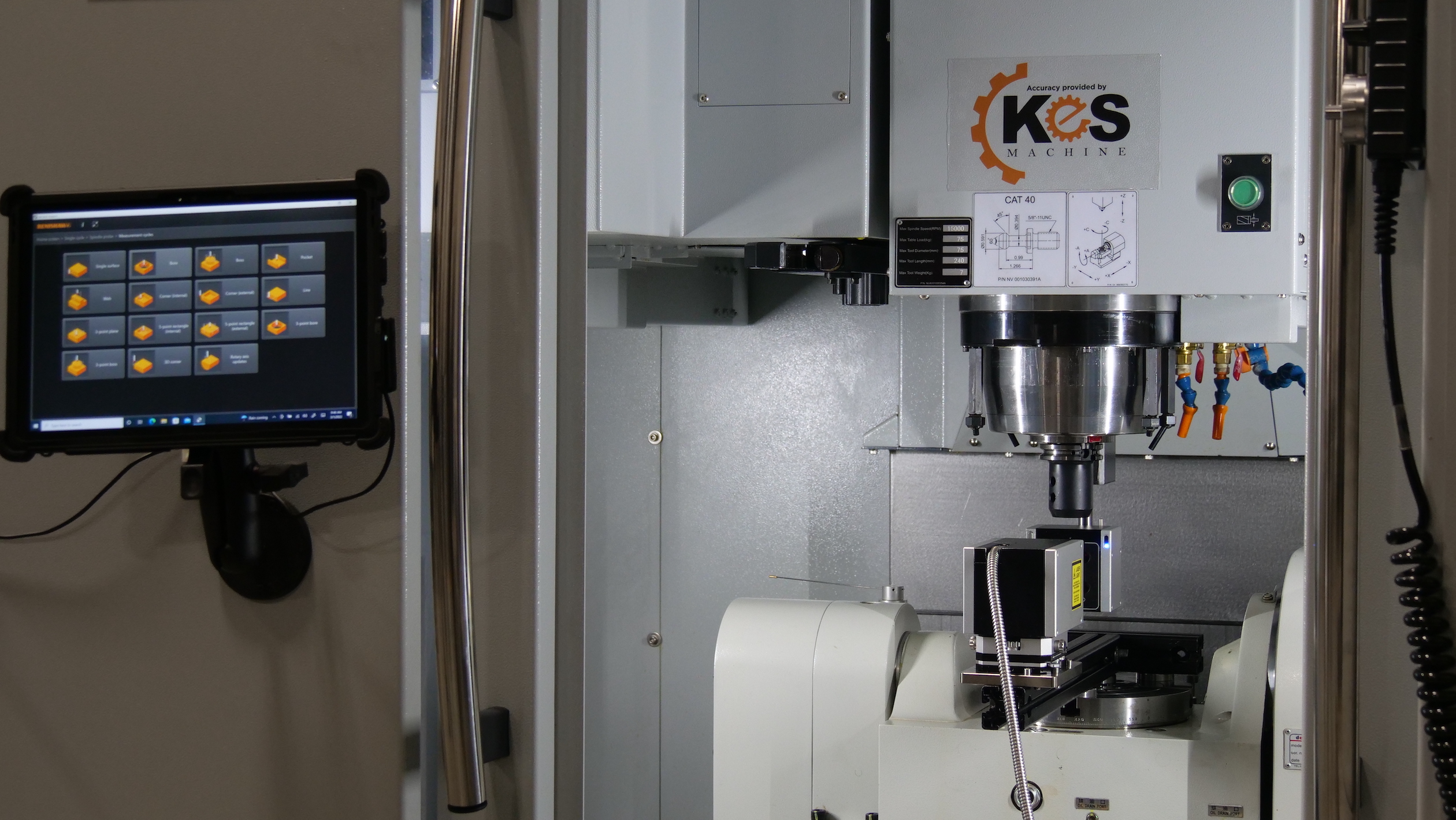
After moving from Poland in 2000, Greg Kordalski founded KES Machine LLC in Connecticut. Since then, the business has helped engineering and manufacturing companies maximize productivity and minimize downtime with its accredited calibration and repair services.
KES Machine LLC’s technicians help machinists solve geometry errors, lead screw errors and repeatability concerns — sometimes the team can diagnose errors before they become critical problems, saving downtime.
While the company initially focused on CNC service work, in 2008, it invested in its first Renishaw ML10 laser system and began developing its calibration services. Based in Newington, Connecticut, the company works with machine tool builders, importers, distributors and end-users, primarily in the aerospace, defense, nuclear and medical sectors across the region.
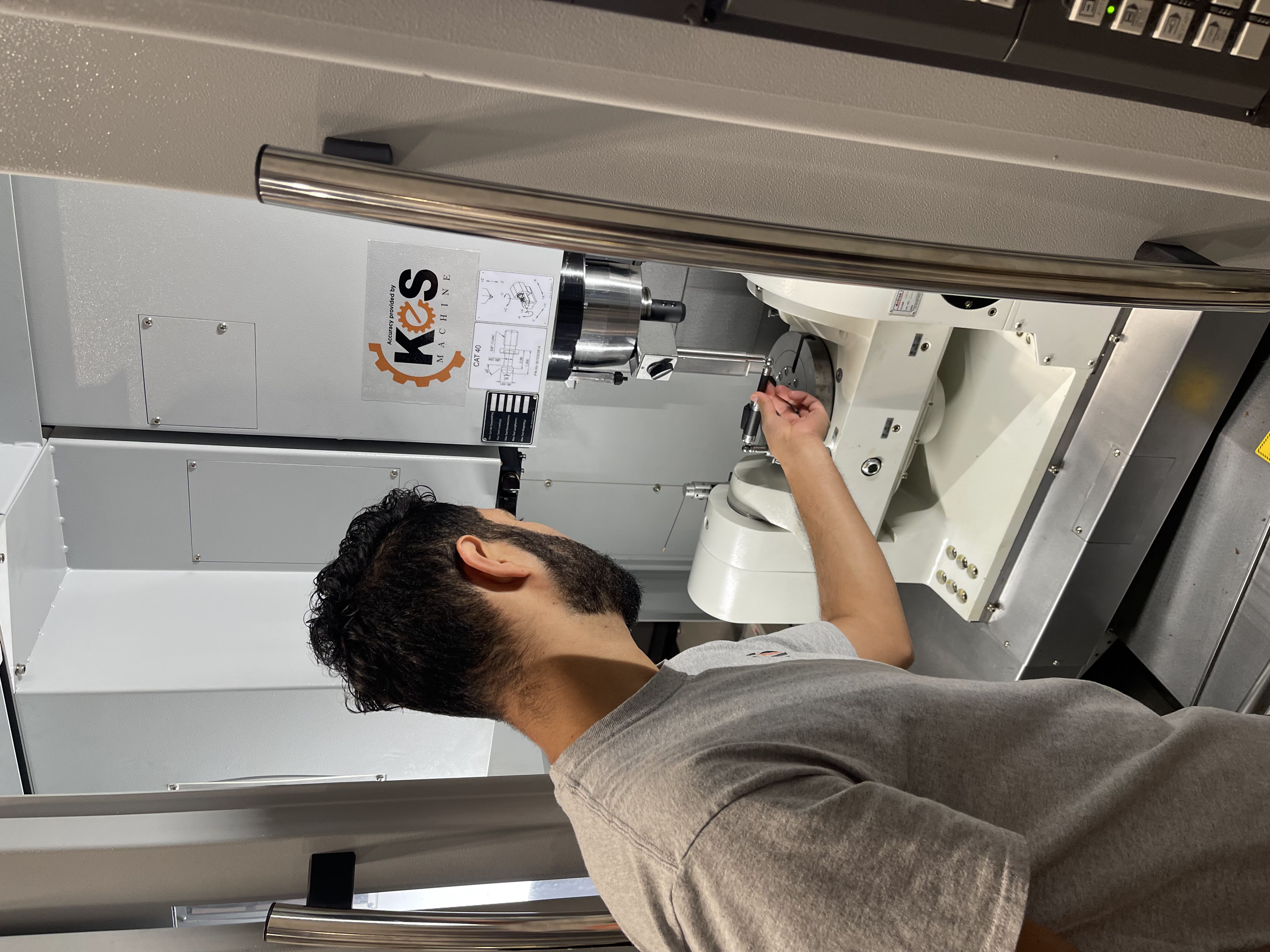
In 2019, KES opened a Polish subsidiary to support manufacturers there. “Since I was born in Poland, I visit quite frequently, so this is why I chose Poland as the first country on the European continent,” said Kordalski. “However, this does not mean that the expansion of the company in Europe will be limited to Poland.”
The company offers in-house and on-site repair services, as well as monthly maintenance contracts to keep equipment operating at optimal efficiency and accuracy. In 2016, KES obtained ISO 17025 certification and became a fully capable calibration service company.
“ISO 17025 accreditation demonstrates our capabilities to our customers,” he said. “Showing that we follow industry requirements for testing and calibration enables us to provide a value-added service to engineers and ensures all our equipment is up-to-date and our technicians offer the best service to customers.”
Challenges
Component quality is dependent on machine performance. Without understanding a machine’s error profile, it is impossible to have confidence that components will fall within specifications during manufacture. KES works with high-precision industries, such as aerospace, defense and medical. It aims to be the go-to calibration service provider and deliver the solutions its customers are asking for. This led KES to investigate volumetric machine tool compensation and explore the systems available on the market.
“In the past few years, we have seen manufacturers invest in more automated machining systems,” said Kordalski. “Probes and calibration are key to the success of these systems, so we’ve seen a growing interest in the annual calibration of equipment and machines using probing systems.”
“KES Machine has always been at the forefront of technological advancements. Accuracy, software, and support are important factors when looking for new products. When we see equipment that makes processes more accurate and efficient, we go in that direction.”
Krzysztor Siergiejczyk, head of KES Machine in Poland said, “After having a good experience working with Renishaw in the USA, when opening the Polish subsidiary, we quickly established contact with Renishaw Poland. We were the first company in Poland to adopt Renishaw’s XM-60 and we have a big ambition to take care of customers within the European market over the upcoming years.”
Solution
Renishaw has had a long-standing relationship with KES. As Kordalski explained: “When Renishaw comes out with a new product, it sparks our interest. As a result, we’ve worked with Renishaw for many years.”
When he first founded KES, Kordalski purchased his first ML10 laser and QC10 ballbar from Renishaw. Since then, KES has purchased a range of Renishaw equipment, including XL-80 laser systems, XR20 rotary calibrators, off axis rotary software and QC20 ballbar systems. The company is also an advocate of Renishaw’s machine tool probes, tool setters and broken tool detection systems, and is a full-service representative of Renishaw products.
KES Machine LLC ultimately selected Renishaw’s XM-60 and XM-600 multi-axis calibrator because of its ease of use, flexibility, and ability to capture large amounts of data. KES can use the equipment on both CNC machine tools and CMMs to perform volumetric compensation. This laser measurement system is capable of measuring errors in six degrees of freedom along a linear axis, simultaneously from a single set-up. It provides a powerful diagnostic tool to measure all geometric errors in the axis from a single capture.
Additionally, the XM-600 multi-axis calibrator is designed with extra functionality, enabling it to communicate directly with Renishaw’s UCC controllers, and is compatible with Renishaw’s CARTO software suite. These features make it the ideal calibration solution for any manufacturing facility that uses both machine tools and CMMs, such as KES.
“Renishaw offers a range of calibration solutions for improved machine performance, increased machine up-time and preventative maintenance schedules,” explained Jeffrey Seliga, Marketing Manager at Renishaw Inc. “By using the XM-60, the KES team can collect a range of measurements, including the pitch, yaw, roll, linear positioning, horizontal and vertical straightness at the same time it takes to collect a single measurement using conventional techniques.”
Results
“I would say that about 80 per cent of our equipment is now Renishaw,” explained Kordalski. “Although we still investigate other brand systems, ultimately, we are looking for the best technology, and Renishaw typically wins. For example, we recently invested in the XK10 alignment laser system. While it’s still a new product for us, we’ve already seen its benefits when testing spindle direction or when installing machines, to help adjust straightness and squareness.”
KES Machine used the XM-600 to implement CNC volumetric compensation and will soon offer CMM calibration to its customers, as well as support for Renishaw CMM hardware, as the XM-600 directly interfaces with Renishaw UCC controllers. For years prior to the release of the XM-60 and XM-600, KES typically used multiple pieces of different equipment to measure linear positioning, pitch, yaw and roll. The XM-60 manages this process with one pass and will include horizontal and vertical straightness over the completed travel. Measurements that used to take two to four hours are now reduced to under 30 minutes, depending on the length of the machine axis.
The equipment can also be used to diagnose machine errors. KES uses CARTO software, along with its own custom software, to simplify its processes. The KES team uses the “cut and paste” feature in CARTO software to help the compensation process and saves time using the report builder feature.
“Volumetric compensation is a relatively new process in the United States, but we have had great success in the past two years,” continued Kordalski. “We can now better support our customers and provide solutions that they demand to ensure machine precision. For example, we’re now seeing some of our customers installing these solutions onto new machines and performing volumetric compensation during installation, ensuring machine accuracy from the very beginning.”
“The support from Renishaw has been outstanding. When first introducing the product, Renishaw arranged to visit our facility to review the system and features, and the team is also on hand for support and regularly asks for feedback and recommendations about its software. Our team is out in the field using Renishaw equipment and software daily, so we are happy to make recommendations — it is a great feeling when a new version is released, and your suggestion has been added,” concluded Kordalski.
For more information visit, www.renishaw.com/calibration.
Contact Details
Related Glossary Terms
- calibration
calibration
Checking measuring instruments and devices against a master set to ensure that, over time, they have remained dimensionally stable and nominally accurate.
- computer numerical control ( CNC)
computer numerical control ( CNC)
Microprocessor-based controller dedicated to a machine tool that permits the creation or modification of parts. Programmed numerical control activates the machine’s servos and spindle drives and controls the various machining operations. See DNC, direct numerical control; NC, numerical control.
- degrees of freedom
degrees of freedom
Number of axes along which a robot, and thus the object it is holding, can be manipulated. Most robots are capable of maneuvering along the three basic Cartesian axes (X, Y, Z). More sophisticated models may move in six or more axes. See axis.
- pitch
pitch
1. On a saw blade, the number of teeth per inch. 2. In threading, the number of threads per inch.