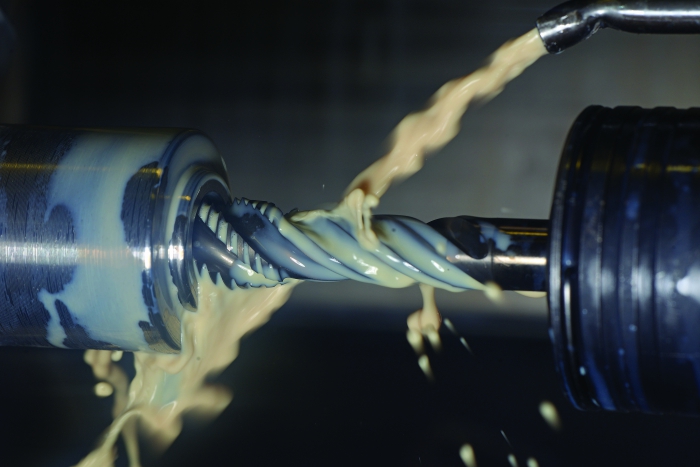
As discussed in the current issue of Cutting Tool Engineering magazine in the feature article “Specialization on tap,” material-specific taps continue to evolve.
Sources anticipate increasing specialization of the materials used for taps across industries.
“I think stuff like carbon steel and tool steel is going to be around forever, but that market share will decrease,” said Applications Engineer Alec Janson at OSG USA Inc., which is headquartered in Irving, Texas. “The range of applications where general-purpose taps will be useful likely will diminish.”
However, he said demand for commodity tooling remains very high and may stay that way for some time, at least until advances in materials drop demand from “very high” to merely “high.”
“Commodity tooling will still be used in more common materials and lower-volume applications,” he said.
Commercially advanced materials, including polymers and “strange” composite metals, increasingly serve specific applications, Janson said. As an example, he cited the slow trend in automobile engines to transition from big, steel blocks to aluminum ones.
“That’s a big change for automotive companies and a big change for us in tapping,” he said. “We’ll see transitions like that happen in other industries. I don’t know what the material will be, but we’ll do the best we can to figure out how to produce tooling that will assist in that material.”
For more information about where tapping is headed, read the article.
Contact Details
Related Glossary Terms
- tap
tap
Cylindrical tool that cuts internal threads and has flutes to remove chips and carry tapping fluid to the point of cut. Normally used on a drill press or tapping machine but also may be operated manually. See tapping.
- tapping
tapping
Machining operation in which a tap, with teeth on its periphery, cuts internal threads in a predrilled hole having a smaller diameter than the tap diameter. Threads are formed by a combined rotary and axial-relative motion between tap and workpiece. See tap.