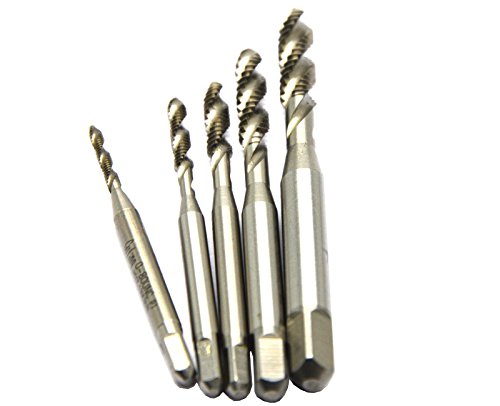
I received an email from a reader letting me know that he disagreed with my recent article on tapping versus thread milling. In it, I stated, “There’s little chance of successfully thread milling metals much above 45 HRC. And if you’re going to try to tap them, be prepared to duck the flying shrapnel when the tap explodes!”
We all make mistakes. So when Tom Fares, president of TNT Custom Equipment in Stow, Ohio, called me out on that section of the article, saying that he routinely taps holes in 45 HRC steel alloy and thread mills into “the low 60s,” I listened to what he had to say.
Fares uses an OSG EXOPRO S-XPF oil tap to form M30 × 3.5 threads in a proprietary alloy similar to 1050 steel but heat-treated to 45 HRC. He said he tried “every M30 forming tap I could find,” but this was the only one his Hurco VMX-84 50-taper belt-driven vertical machining center could actually turn without stalling the spindle.
He has nothing but good to say about the OSG oil tap, citing another example of a long-running job where he taps M30 holes in A514 grade 50 plate (a high-strength structural steel). At 250 rpm, the OSG averages up to 9,000 holes through 1.575" thick material compared with 1,750 holes per tap with “the other brand.” That spindle speed is faster than Fares likes, and he thinks tool life would be even better by slowing things down, but he needs to run at that rpm to keep the spindle from stalling.
He also breaks the rules somewhat by using a water soluble, semisynthetic cutting fluid with a chlorinated lube additive. (Speaking for myself, I’d use a sulfur-based oil or squirt a little tapping wax into the hole.) “I know they say water soluble coolant isn’t recommended for form tapping, but it works for me,” said Fares.
On the thread-milling side, he cuts 62 HRC flame-hardened 1045 and 52100 steels for prototypes and fixturing, although this is admittedly “one-off stuff, but it can be done.”
Don’t get me wrong. I’ve tapped thousands of holes over the years. Cut taps, roll taps, spiral, plug and bottoming taps—I’ve used them all in everything from nickel-based superalloys to Teflon. And while thread milling wasn’t possible when I started in the trades, I did my fair share of that as well in later years.
In my defense, Fares is using a coolant-through-the-tool tap. This is one of those “newer” cutting tool technologies that makes a huge difference in many applications but especially when you’re pushing the limits as TNT Custom Equipment does. The tap is also advertised to reduce torque by up to 50 percent compared with competing brands, which is surely another factor in Fares’ success.
Anyway, my bad. My wife is enthusiastic about pointing out my mistakes, but I don’t often hear it from my readers. So thank you for your email, Tom, and for sharing the details with me. That’s the wonderful thing about manufacturing: There are always new things to learn.
P.S. Here’s the link to the original article, in case you didn’t see it. And here’s a link to an OSG video on the EXOPRO XPF oil taps.
Related Glossary Terms
- coolant
coolant
Fluid that reduces temperature buildup at the tool/workpiece interface during machining. Normally takes the form of a liquid such as soluble or chemical mixtures (semisynthetic, synthetic) but can be pressurized air or other gas. Because of water’s ability to absorb great quantities of heat, it is widely used as a coolant and vehicle for various cutting compounds, with the water-to-compound ratio varying with the machining task. See cutting fluid; semisynthetic cutting fluid; soluble-oil cutting fluid; synthetic cutting fluid.
- cutting fluid
cutting fluid
Liquid used to improve workpiece machinability, enhance tool life, flush out chips and machining debris, and cool the workpiece and tool. Three basic types are: straight oils; soluble oils, which emulsify in water; and synthetic fluids, which are water-based chemical solutions having no oil. See coolant; semisynthetic cutting fluid; soluble-oil cutting fluid; synthetic cutting fluid.
- gang cutting ( milling)
gang cutting ( milling)
Machining with several cutters mounted on a single arbor, generally for simultaneous cutting.
- machining center
machining center
CNC machine tool capable of drilling, reaming, tapping, milling and boring. Normally comes with an automatic toolchanger. See automatic toolchanger.
- milling
milling
Machining operation in which metal or other material is removed by applying power to a rotating cutter. In vertical milling, the cutting tool is mounted vertically on the spindle. In horizontal milling, the cutting tool is mounted horizontally, either directly on the spindle or on an arbor. Horizontal milling is further broken down into conventional milling, where the cutter rotates opposite the direction of feed, or “up” into the workpiece; and climb milling, where the cutter rotates in the direction of feed, or “down” into the workpiece. Milling operations include plane or surface milling, endmilling, facemilling, angle milling, form milling and profiling.
- semisynthetic cutting fluid
semisynthetic cutting fluid
Water-based chemical solution that contains some oil. See synthetic cutting fluid.
- superalloys
superalloys
Tough, difficult-to-machine alloys; includes Hastelloy, Inconel and Monel. Many are nickel-base metals.
- tap
tap
Cylindrical tool that cuts internal threads and has flutes to remove chips and carry tapping fluid to the point of cut. Normally used on a drill press or tapping machine but also may be operated manually. See tapping.
- tapping
tapping
Machining operation in which a tap, with teeth on its periphery, cuts internal threads in a predrilled hole having a smaller diameter than the tap diameter. Threads are formed by a combined rotary and axial-relative motion between tap and workpiece. See tap.