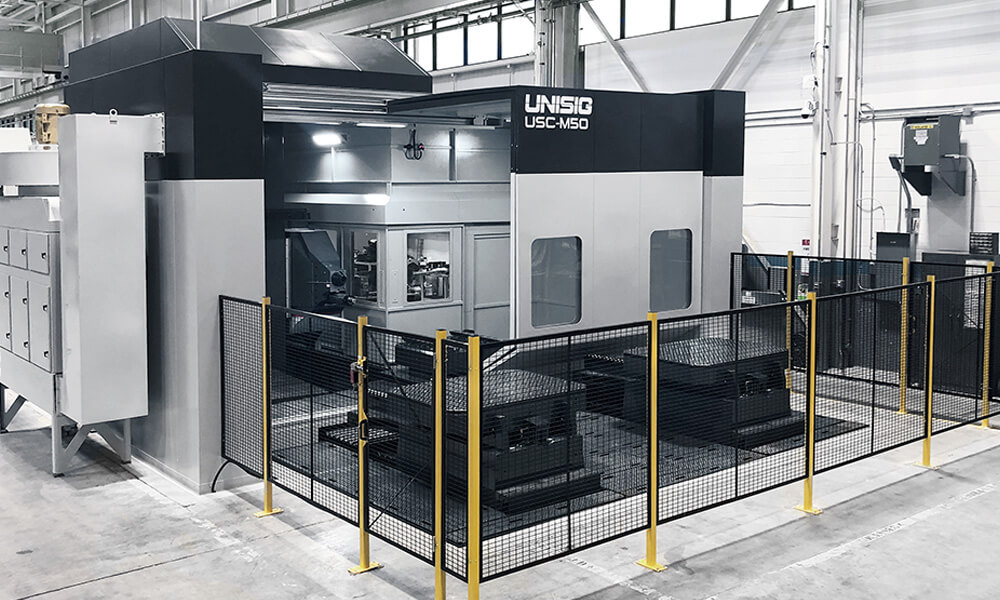
Unisig will showcase its comprehensive portfolio of deep-hole drilling solutions in booth 339159 at IMTS 2024, Sept. 9 – 14, in Chicago.
The company said that manufacturers in industries ranging from aerospace, automotive, medical and moldmaking to energy, firearms, and defense can learn how to achieve a competitive advantage with Unisig’s 50-year leadership in deep hole drilling technology, and automation paired with unmatched engineering, sales, and service support.
Unisig offers an entire deep-hole drilling system – machines, tooling, and automation – that covers the full range of deep-hole drilling applications. Engineered and manufactured in the United States for a global customer base, Unisig machines are used in applications that vary from drilling holes less than 0.040” in diameter for titanium medical components to 20” diameter holes over 30 feet deep in massive high-strength forgings. UNISIG’s USC-M drilling and milling centers combine 5-axis CNC milling and deep hole drilling in one machine platform for maximum versatility with fewer setups and reduced part handling.
Productivity and cost efficiency are maximized with Unisig extensive experience in designing and integrating a variety of standard and specialized automation solutions into its deep hole drilling machines that include pallet changers, robotics, programmable smart conveyors, heavy bar loaders, and bulk feeders.
In addition to discovering the company’s wide range of deep-hole drilling technology, visitors will be able to view an assortment of parts from medical to aerospace components that demonstrate the breadth and depth of Unisig’s deep-hole drilling capabilities. Unisig personnel will also be available to discuss machine tooling and automation solutions for those customers with unique manufacturing needs and challenges and detail the company’s dedication to comprehensive training and support.
Contact Details
Related Glossary Terms
- centers
centers
Cone-shaped pins that support a workpiece by one or two ends during machining. The centers fit into holes drilled in the workpiece ends. Centers that turn with the workpiece are called “live” centers; those that do not are called “dead” centers.
- computer numerical control ( CNC)
computer numerical control ( CNC)
Microprocessor-based controller dedicated to a machine tool that permits the creation or modification of parts. Programmed numerical control activates the machine’s servos and spindle drives and controls the various machining operations. See DNC, direct numerical control; NC, numerical control.
- gang cutting ( milling)
gang cutting ( milling)
Machining with several cutters mounted on a single arbor, generally for simultaneous cutting.
- milling
milling
Machining operation in which metal or other material is removed by applying power to a rotating cutter. In vertical milling, the cutting tool is mounted vertically on the spindle. In horizontal milling, the cutting tool is mounted horizontally, either directly on the spindle or on an arbor. Horizontal milling is further broken down into conventional milling, where the cutter rotates opposite the direction of feed, or “up” into the workpiece; and climb milling, where the cutter rotates in the direction of feed, or “down” into the workpiece. Milling operations include plane or surface milling, endmilling, facemilling, angle milling, form milling and profiling.
- robotics
robotics
Discipline involving self-actuating and self-operating devices. Robots frequently imitate human capabilities, including the ability to manipulate physical objects while evaluating and reacting appropriately to various stimuli. See industrial robot; robot.