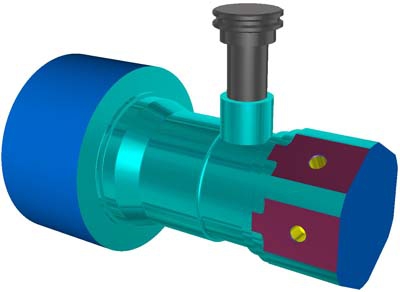
Delcam has launched the 2012 R2 release of its FeatureCAM feature-based CAM system, which includes important new strategies for roughing and turn-mill operations, alongside a range of more general enhancements to allow faster toolpath generation.
The main addition to FeatureCAM 2012 R2 is a series of new strategies for 2.5D roughing. These include a continuous spiral option to minimise wear on the cutter and machine tool, high-speed roughing options, including trochoidal machining and Delcam's patented Race Line Machining, and "tear-drop" moves to clear corners more smoothly. In addition, more styles of leads and links can now be used to give greater overall efficiency for the toolpaths.
Stepovers for 2.5D mill roughing can now be set as large as the tool diameter itself. Previously, stepovers were limited to 50 percent of the tool diameter and, if this limit was exceeded, the toolpath would leave stands. The new algorithm supports larger stepovers by providing extra moves automatically to clean up those stands.
Other milling improvements include an option to add an extra profile pass exactly at the base of flat pockets, the ability to use face-milling tools with chamfered edges to machine chamfers as well as faces and so minimise the number of tools needed, a choice of right- or left-handed thread-milling tools resulting in either climb or conventional machining of the thread, and the ability to reduce calculation times by saving boundaries as curves if they will be needed for subsequent calculations.
Roughing has also been improved for users of turning equipment that can operate with live tooling. A new option allows cutting with a live milling tool, while the workpiece is rotating in the turning spindle. This approach avoids the issues associated with interrupted cutting and ensures regular chip breakage, so removing any chance of wrap-around by the swarf. T
urn-mill programming has been improved with the addition of more flexible five-axis positioning. For example, any amount of negative b-axis movement available can be used, so avoiding extending the y limit too far back into the machine. Switching the positioning angles in this way makes editing easier to keep the machine within its travel limits. Another turn-mill improvement is support for cylindrical interpolation, which allows toolpaths to be created with NC code for a plane and then wrapped around a cylinder. This approach, which can also be used for four-axis milling, allows cutter compensation to be applied when calculating the toolpath and gives smaller NC code files.
All FeatureCAM users will benefit from improvements to the simulation module. In particular, they will see much faster results through the use of multiple cores for these calculations. In addition, the ability has been included to save a position during the simulation, for example, while toolpaths are being edited, and then to run the simulation from that position rather than from the start.
Other general enhancements include direct cutting and pasting of models between FeatureCAM and Delcam's PowerSHAPE design and data repair software, and the ability to create machining configurations on a network as well as on an individual computer, so saving time and encouraging consistent results from different users.
Contact Details
Related Glossary Terms
- computer-aided manufacturing ( CAM)
computer-aided manufacturing ( CAM)
Use of computers to control machining and manufacturing processes.
- cutter compensation
cutter compensation
Feature that allows the operator to compensate for tool diameter, length, deflection and radius during a programmed machining cycle.
- flat ( screw flat)
flat ( screw flat)
Flat surface machined into the shank of a cutting tool for enhanced holding of the tool.
- gang cutting ( milling)
gang cutting ( milling)
Machining with several cutters mounted on a single arbor, generally for simultaneous cutting.
- interpolation
interpolation
Process of generating a sufficient number of positioning commands for the servomotors driving the machine tool so the path of the tool closely approximates the ideal path. See CNC, computer numerical control; NC, numerical control.
- milling
milling
Machining operation in which metal or other material is removed by applying power to a rotating cutter. In vertical milling, the cutting tool is mounted vertically on the spindle. In horizontal milling, the cutting tool is mounted horizontally, either directly on the spindle or on an arbor. Horizontal milling is further broken down into conventional milling, where the cutter rotates opposite the direction of feed, or “up” into the workpiece; and climb milling, where the cutter rotates in the direction of feed, or “down” into the workpiece. Milling operations include plane or surface milling, endmilling, facemilling, angle milling, form milling and profiling.
- milling machine ( mill)
milling machine ( mill)
Runs endmills and arbor-mounted milling cutters. Features include a head with a spindle that drives the cutters; a column, knee and table that provide motion in the three Cartesian axes; and a base that supports the components and houses the cutting-fluid pump and reservoir. The work is mounted on the table and fed into the rotating cutter or endmill to accomplish the milling steps; vertical milling machines also feed endmills into the work by means of a spindle-mounted quill. Models range from small manual machines to big bed-type and duplex mills. All take one of three basic forms: vertical, horizontal or convertible horizontal/vertical. Vertical machines may be knee-type (the table is mounted on a knee that can be elevated) or bed-type (the table is securely supported and only moves horizontally). In general, horizontal machines are bigger and more powerful, while vertical machines are lighter but more versatile and easier to set up and operate.
- numerical control ( NC)
numerical control ( NC)
Any controlled equipment that allows an operator to program its movement by entering a series of coded numbers and symbols. See CNC, computer numerical control; DNC, direct numerical control.
- swarf
swarf
Metal fines and grinding wheel particles generated during grinding.
- toolpath( cutter path)
toolpath( cutter path)
2-D or 3-D path generated by program code or a CAM system and followed by tool when machining a part.
- turning
turning
Workpiece is held in a chuck, mounted on a face plate or secured between centers and rotated while a cutting tool, normally a single-point tool, is fed into it along its periphery or across its end or face. Takes the form of straight turning (cutting along the periphery of the workpiece); taper turning (creating a taper); step turning (turning different-size diameters on the same work); chamfering (beveling an edge or shoulder); facing (cutting on an end); turning threads (usually external but can be internal); roughing (high-volume metal removal); and finishing (final light cuts). Performed on lathes, turning centers, chucking machines, automatic screw machines and similar machines.