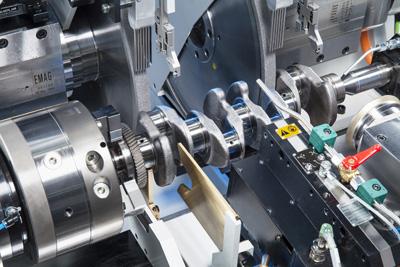
International competition in the automotive industry continues to increase, as do the technological demands on vehicles, and with them the costs. But increasing prices in the face of stiff competition in the market is no longer easily defensible. According to a McKinsey study, the costs incurred in the manufacture of passenger cars must be reduced three to four percent per year to retain current profitability levels. This is a staggering percentage, yet many manufacturers remain unclear how to achieve these numbers. EMAG offers precision solutions, for example with crankshafts, where a lot is dependent on the grinding process carried out on this core engine component. In the future, the process must be of greater precision and subject to an even higher degree of efficiency. The grinding experts at EMAG offer an interesting alternative in their PMD 2 crankshaft grinder. This machine incorporates EMAG NAXOS-UNION technology and provides high output rates with an impressive price-performance ratio.
Prospects for the international automotive industry are promising, with expected growth in the coming years supported by growing demand in the Asian markets. Competition continues to increase, especially from Asian companies. In addition, more rigorous national emission limits and safety requirements lead to an increase in production costs, causing planners to review their manufacturing technologies for potential savings. In the example of the crankshaft, which the engine depends on for efficiency and stability, a work-intensive grinding operation in the micrometer range is required.
EMAG experts also develop tailor-made grinding solutions for shaft-type components. The new PMD 2 machine complements this crankshaft grinder know-how. It is designed for the machining of passenger car crankshafts and features twin grinding heads that allow the simultaneous grinding of two pin or main bearings in a single setup using two grinding wheels. Its capacity covers small components up to 500mm length.
"With this machine we are rounding out our range of crankshaft grinders to include the machining of smaller components," explains Dr. Guido Hegener, Managing Director of EMAG Maschinenfabrik GmbH. "Up to now, our range of machines did not include a horizontal twin-head grinder for smaller crankshafts. This gap is now filled with the PMD 2, a machine with an excellent price-performance ratio ideally suited to combat the increasing competition in the automotive industry."
Relying on their technologies that have proven successful in the market, the basis for the PMD 2 is the established "Series 2" from EMAG NAXOS-UNION and EMAG KOPP. These machines combine high-tech grinding technology with precision, great efficiency, process integrity and simple operation. This applies to the PMD 2 as well, where two CBN grinding wheels machine crankshafts to the highest precision. To achieve this, the machine is equipped with a direct-driven workspindle, hydrostatic guideways and a linear motor in the X-axis, as well as an in-process measuring control that allows for roundness monitoring and correction in the machine.
"The operator enters the relevant command in the control and the measuring process is carried out once the bearing has been ground. The software, developed by EMAG, then calculates the relevant correction values from the remaining roundness errors. This allows for the subsequent manufacturing processes to be successively optimized," adds Hegener.
The technology also stands out with its simultaneous use of two grinding wheels. The twin-tool process opens up a number of possibilities for the user, depending on component and machining requirements. Two pin bearings or main and pin bearing are machined simultaneously, reducing cycle times. For instance, a four-cylinder crankshaft is machined in less than two minutes. The grinding wheels can, if required, be arranged very close together so that adjoining pin and main bearings can be machined simultaneously. Both grinding spindles and work headstock are direct-driven, further increasing precision and productivity levels. "We have strung together a technologically very interesting package," states Hegener.
The machine also features a compact but flexible construction, for example the electrical cabinet is included in the enclosure. Connecting an automatic loading system poses no problem, and both emulsion and oil can be used as coolants.
"Flexibility was of great importance in using this technology," confirms Hegener. "We tailor the machine exactly to the customer's requirements. Integration into an existing, complex production line is an important option, but there is the option of the machine being used as a stand-alone solution with manual loading. We expect this approach will give users a competitive edge while component quality and production costs are gaining importance worldwide."
Contact Details
Related Glossary Terms
- cubic boron nitride ( CBN)
cubic boron nitride ( CBN)
Crystal manufactured from boron nitride under high pressure and temperature. Used to cut hard-to-machine ferrous and nickel-base materials up to 70 HRC. Second hardest material after diamond. See superabrasive tools.
- emulsion
emulsion
Suspension of one liquid in another, such as oil in water.
- grinding
grinding
Machining operation in which material is removed from the workpiece by a powered abrasive wheel, stone, belt, paste, sheet, compound, slurry, etc. Takes various forms: surface grinding (creates flat and/or squared surfaces); cylindrical grinding (for external cylindrical and tapered shapes, fillets, undercuts, etc.); centerless grinding; chamfering; thread and form grinding; tool and cutter grinding; offhand grinding; lapping and polishing (grinding with extremely fine grits to create ultrasmooth surfaces); honing; and disc grinding.
- linear motor
linear motor
Functionally the same as a rotary motor in a machine tool, a linear motor can be thought of as a standard permanent-magnet, rotary-style motor slit axially to the center and then peeled back and laid flat. The major advantage of using a linear motor to drive the axis motion is that it eliminates the inefficiency and mechanical variance caused by the ballscrew assembly system used in most CNC machines.
- micrometer
micrometer
A precision instrument with a spindle moved by a finely threaded screw that is used for measuring thickness and short lengths.