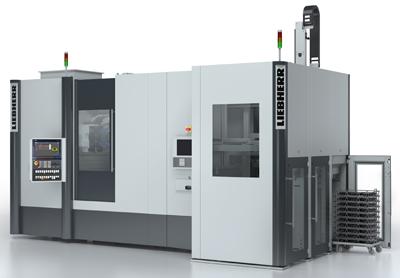
Liebherr's new LGG 180 machine for profile and generating grinding combines short grinding times with consistent high large-scale production quality, thanks to a one-table design. The advantage to the one-table solution is higher quality throughout the entire production, according to the company. Every machined part is manufactured under the same conditions for the highest reproducibility, said Dr.-Ing. Andreas Mehr, Grinding and Shaping Technology Development and Consultancy at Liebherr-Verzahntechnik GmbH.
"A key argument in favor of the one-table solution is the statistical capability and reliability in continuously producing controlledµm-range finish quality," Mehr emphasizes.
The new grinding head allows for rotation speeds up to 10,000 rpm and has spindle power of 35 kW. Given this performance data, the head enables high cutting speeds and high feed rates. The new grinding machine can exploit the considerable potential of the innovative abrasive Cubitron II. The machine will enable undulations to be applied specifically to gear wheel flanks for noise optimization purposes for the first time. The ability to produce submicron range waviness cost-effectively reportedly gives designers a whole new range of optimisation options.
The LGG machine delivers fast processing combined with the set-up advantages of a one-table solution. In addition, the machines for both 180mm and 280mm gears have the same compact external dimensions, facilitating installation within production lines.
Vehicle manufacturers can thus develop a complete production line, in which all gearing components for a passenger vehicle transmission can be ground: planetary and sun gears, bore-type gears, as well as drive and pinion shafts with lengths up to 500mm.
To minimize any thermal impacts, the machine bed is of a thermally stable material. The core of the machine is the newly developed grinding head. Conventional solutions have been chosen here in several areas in order to be prepared for yet higher quality requirements.
Related Glossary Terms
- abrasive
abrasive
Substance used for grinding, honing, lapping, superfinishing and polishing. Examples include garnet, emery, corundum, silicon carbide, cubic boron nitride and diamond in various grit sizes.
- feed
feed
Rate of change of position of the tool as a whole, relative to the workpiece while cutting.
- grinding
grinding
Machining operation in which material is removed from the workpiece by a powered abrasive wheel, stone, belt, paste, sheet, compound, slurry, etc. Takes various forms: surface grinding (creates flat and/or squared surfaces); cylindrical grinding (for external cylindrical and tapered shapes, fillets, undercuts, etc.); centerless grinding; chamfering; thread and form grinding; tool and cutter grinding; offhand grinding; lapping and polishing (grinding with extremely fine grits to create ultrasmooth surfaces); honing; and disc grinding.
- grinding machine
grinding machine
Powers a grinding wheel or other abrasive tool for the purpose of removing metal and finishing workpieces to close tolerances. Provides smooth, square, parallel and accurate workpiece surfaces. When ultrasmooth surfaces and finishes on the order of microns are required, lapping and honing machines (precision grinders that run abrasives with extremely fine, uniform grits) are used. In its “finishing” role, the grinder is perhaps the most widely used machine tool. Various styles are available: bench and pedestal grinders for sharpening lathe bits and drills; surface grinders for producing square, parallel, smooth and accurate parts; cylindrical and centerless grinders; center-hole grinders; form grinders; facemill and endmill grinders; gear-cutting grinders; jig grinders; abrasive belt (backstand, swing-frame, belt-roll) grinders; tool and cutter grinders for sharpening and resharpening cutting tools; carbide grinders; hand-held die grinders; and abrasive cutoff saws.
- shaping
shaping
Using a shaper primarily to produce flat surfaces in horizontal, vertical or angular planes. It can also include the machining of curved surfaces, helixes, serrations and special work involving odd and irregular shapes. Often used for prototype or short-run manufacturing to eliminate the need for expensive special tooling or processes.
- waviness
waviness
The more widely spaced component of the surface texture. Includes all irregularities spaced more widely than the instrument cutoff setting. See flows; lay; roughness.