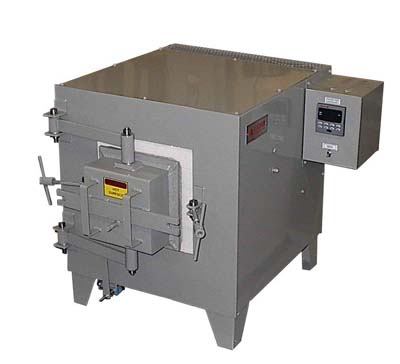
Lucifer Furnaces Inc. recently built an HL7-A12 box furnace for SunCoast Automation 2000 Inc., which designs and builds automated systems for various industries. One of the Series 7000 line of box furnaces, the HL7 model has heating elements located on both side walls and reaches 2300°F. The heavy gauge, low watt density coiled elements are housed in easy-to-replace holders. The 6"H x 6"W x 12"L chamber is insulated with 2.5" low iron insulating brick as well as 2.5" of mineral wool block for energy efficient operation and low outside shell temperature. A 1" thick hearth plates provides a solid, strong work surface for parts.
The double pivot horizontal swing door keeps the hot surface away from the operator at all times and is designed with a safety microswitch to shut power to heating elements when the door is opened. The heavy duty hinge and cam latch insure a positive door seal. An automated Honeywell digital time proportioning temperature controller for precision heat treating is mounted on the side wall of the unit. Series 7000 furnaces are ideal for hardening, preheating, annealing, brazing and normalizing.
Contact Details
Related Glossary Terms
- annealing
annealing
Softening a metal by heating it to and holding it at a controlled temperature, then cooling it at a controlled rate. Also performed to produce simultaneously desired changes in other properties or in the microstructure. The purposes of such changes include improvement of machinability, facilitation of cold work, improvement of mechanical or electrical properties and increase in stability of dimensions. Types of annealing include blue, black, box, bright, full, intermediate, isothermal, quench and recrystallization.
- computer-aided manufacturing ( CAM)
computer-aided manufacturing ( CAM)
Use of computers to control machining and manufacturing processes.
- hardening
hardening
Process of increasing the surface hardness of a part. It is accomplished by heating a piece of steel to a temperature within or above its critical range and then cooling (or quenching) it rapidly. In any heat-treatment operation, the rate of heating is important. Heat flows from the exterior to the interior of steel at a definite rate. If the steel is heated too quickly, the outside becomes hotter than the inside and the desired uniform structure cannot be obtained. If a piece is irregular in shape, a slow heating rate is essential to prevent warping and cracking. The heavier the section, the longer the heating time must be to achieve uniform results. Even after the correct temperature has been reached, the piece should be held at the temperature for a sufficient period of time to permit its thickest section to attain a uniform temperature. See workhardening.
- normalizing
normalizing
Heating a ferrous alloy to a temperature above the transformation range and then cooling in air to a temperature below the transformation range.
- preheating
preheating
Heating before some further thermal or mechanical treatment.