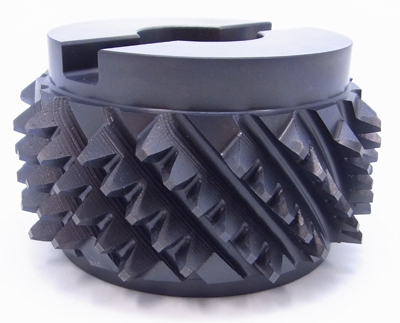
Mitsubishi Heavy Industries Ltd. (MHI) has completed development of the "Mitsubishi Super Skiving System" for machining internal gears with high speed and precision. The new system has overcome technical issues characteristic of conventional skiving by use of an MHI developed, innovative barrel-shaped multiple-cutting-edge rotary tool (patent pending), enabling mass production of difficult-to-machine internal gears. In addition, longer tool life, combined with shorter machining times, enables significant reductions in production costs. MHI is aiming to commence marketing of the new tool and dedicated skiving machine in April 2015.
The main breakthrough achievement for the Mitsubishi Super Skiving System was the development of the "Super Skiving Cutter." It was designed in-house by applying skiving technology to MHI's barrel-shaped grinding wheel developed for MHI's ZI20A gear grinding machine. A machine designed for mass-production applications in 2009.
MHI has also developed new cutting simulation software specifically for skiving's needs. Through precise simulation of cutting forces applied to the tool's cutting blades, long tool life is realized in combination with maximum process cutting speed matching that of the skiving machines capabilities. By offering an integrated package consisting of Mitsubishi's newly developed tool, simulation technology, skiving machine and machining software, users can realize optimal capabilities for the machining of internal gears.
Skiving is a cutting technology whereby a pinion type cutter or other rotary tool is engaged with a workpiece at a crossed-axes angle, and synchronously rotated together. At the points where the two contact, the effect of the crossed-axes angle generates a sliding velocity of the tool in the axial direction, resulting in high-speed machining. Use of a pinion cutter type tool, however, typically makes the cutting (skiving) angle obtuse, a drawback that impedes improvements in cutting precision and also causes significant tool wear.
With MHI's newly developed tool, the adoption of a barrel shape, averts interference with the workpiece and prevents the cutting angle from becoming obtuse. As a result, a large crossed-axes angle can be achieved, enabling the realization of cutting speeds and precision levels surpassing those of pinion-cutter type skiving. It is said to even exceed the corresponding levels achievable with a gear shaper. Furthermore, the adoption of multiple cutter blades more than triples the standard tool life.
Contact Details
Related Glossary Terms
- cutting speed
cutting speed
Tangential velocity on the surface of the tool or workpiece at the cutting interface. The formula for cutting speed (sfm) is tool diameter 5 0.26 5 spindle speed (rpm). The formula for feed per tooth (fpt) is table feed (ipm)/number of flutes/spindle speed (rpm). The formula for spindle speed (rpm) is cutting speed (sfm) 5 3.82/tool diameter. The formula for table feed (ipm) is feed per tooth (ftp) 5 number of tool flutes 5 spindle speed (rpm).
- gear shaper
gear shaper
Machine that, in contrast to mills and hobbing machines, reciprocates the tool to cut the gear. See hobbing machine.
- grinding
grinding
Machining operation in which material is removed from the workpiece by a powered abrasive wheel, stone, belt, paste, sheet, compound, slurry, etc. Takes various forms: surface grinding (creates flat and/or squared surfaces); cylindrical grinding (for external cylindrical and tapered shapes, fillets, undercuts, etc.); centerless grinding; chamfering; thread and form grinding; tool and cutter grinding; offhand grinding; lapping and polishing (grinding with extremely fine grits to create ultrasmooth surfaces); honing; and disc grinding.
- grinding machine
grinding machine
Powers a grinding wheel or other abrasive tool for the purpose of removing metal and finishing workpieces to close tolerances. Provides smooth, square, parallel and accurate workpiece surfaces. When ultrasmooth surfaces and finishes on the order of microns are required, lapping and honing machines (precision grinders that run abrasives with extremely fine, uniform grits) are used. In its “finishing” role, the grinder is perhaps the most widely used machine tool. Various styles are available: bench and pedestal grinders for sharpening lathe bits and drills; surface grinders for producing square, parallel, smooth and accurate parts; cylindrical and centerless grinders; center-hole grinders; form grinders; facemill and endmill grinders; gear-cutting grinders; jig grinders; abrasive belt (backstand, swing-frame, belt-roll) grinders; tool and cutter grinders for sharpening and resharpening cutting tools; carbide grinders; hand-held die grinders; and abrasive cutoff saws.
- grinding wheel
grinding wheel
Wheel formed from abrasive material mixed in a suitable matrix. Takes a variety of shapes but falls into two basic categories: one that cuts on its periphery, as in reciprocating grinding, and one that cuts on its side or face, as in tool and cutter grinding.
- slotting machine ( shaper)
slotting machine ( shaper)
Vertical or horizontal machine that accommodates single-point, reciprocating cutting tools to shape or slot a workpiece. Normally used for special (unusual/intricate shapes), low-volume runs typically performed by broaching or milling machines. See broaching machine; mill, milling machine.