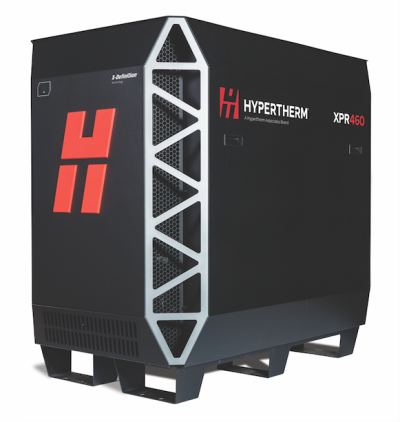
Hypertherm Associates, a U.S. based leading manufacturer of industrial cutting systems and software, has announced the release of its latest innovation: the Hypertherm® XPR460® plasma cutting system. Positioned as the newest addition to the XPR line with X-Definition® technology, this advanced plasma system pays you back with maximum versatility, productivity, and precision.
“We are very excited to bring this highly anticipated product to the market. Customers will be pleased to see the precision in the cut quality and the wide range of capabilities for the XPR460,” stated Jorge Santana, marketing project manager at Hypertherm Associates. “Between the range of thicknesses and materials it can cut, it is the most versatile cutting technology available.”
The XPR460 pays you back by providing these key business benefits:
Versatility
- Superior cutting versatility for mild steel, stainless steel, and aluminum
- Performs multiple applications with SureCut™ technology for bolt-ready holes and smooth 45-degree bevels
- Great solution for XY and robotic cutting applications
Productivity
- Cutting speed increased by an average of 12% through 50 mm (2 in) mild steel
- Piercing up to 64 mm (2.5 in) mild steel
- Future-enabled for Smart Factory integration and connectivity
- Increase of 12% in consumable life versus HPR400XD®
Precision
- Highest cut quality available for thicker metal, providing cleaner, sharper, and more consistent edge quality
- Excellent part-to-part consistency over the life of the consumable, ensuring quality from the first cut to the last
With enhanced thickness and speed capabilities, the XPR460 sets a new standard for precision and productivity. The system delivers superior performance in cut quality, thickness capacity, and cutting speeds. This innovative technology ensures consistent part quality from the initial cut to the last, delivering superior cutting versatility for mild steel, stainless steel, and aluminum.
SureCut technology optimizes Hypertherm plasma performance by automatically embedding advanced cutting capabilities and delivering improved customer outcomes. The system's optimization for productivity and cost-efficiency extends to its ability to maintain exceptional cut quality on 45-degree bevels and ensure uniform hole aesthetics throughout.
With Arc response technology, the XPR460 is engineered for system optimization. Ramp-down error protection significantly increases realized consumable life, and torch protection reduces the impact of catastrophic electrode blowouts, which can damage the torch at high current levels.
Designed for seamless operation, the XPR460 features Argon-assist technology for effortless extended piercing capability and edge-starting on thick mild steel and stainless steel. Additionally, its advanced process control mechanisms prioritize plate protection and consumable efficiency, minimizing downtime and maximizing output.
With four gas-connect console options, the XPR460 offers unparalleled flexibility and control over the cutting process. Each console is seamlessly integrated with the CNC interface, ensuring ease of use and high productivity. Moreover, CorePlus, VWI, and OptiMix gas-connect consoles enable improved marking applications, enhancing the system's versatility and efficiency.
Contact Details
Related Glossary Terms
- computer numerical control ( CNC)
computer numerical control ( CNC)
Microprocessor-based controller dedicated to a machine tool that permits the creation or modification of parts. Programmed numerical control activates the machine’s servos and spindle drives and controls the various machining operations. See DNC, direct numerical control; NC, numerical control.
- cutting speed
cutting speed
Tangential velocity on the surface of the tool or workpiece at the cutting interface. The formula for cutting speed (sfm) is tool diameter 5 0.26 5 spindle speed (rpm). The formula for feed per tooth (fpt) is table feed (ipm)/number of flutes/spindle speed (rpm). The formula for spindle speed (rpm) is cutting speed (sfm) 5 3.82/tool diameter. The formula for table feed (ipm) is feed per tooth (ftp) 5 number of tool flutes 5 spindle speed (rpm).
- process control
process control
Method of monitoring a process. Relates to electronic hardware and instrumentation used in automated process control. See in-process gaging, inspection; SPC, statistical process control.