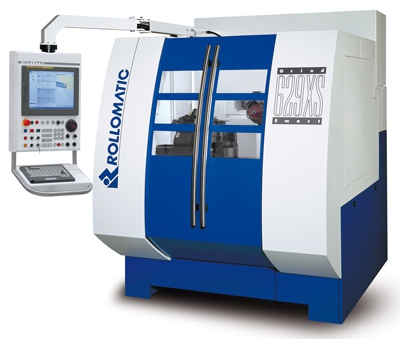
Precise and highly productive in a wide range of applications – this is what the new tool grinding machine GrindSmart629XS from Rollomatic SA stands for. Equipped with ultra-modern technology, it produces standard as well as specialty tools of the highest quality standards. The sixth axis along with numerous other new features ensure extraordinary flexibility and ultra-high tool quality of the GrindSmart629XS.
Consistent quality in a wide range of different applications – these are the requirements today. To allow its customers to produce such versatility, the premier Swiss grinding machine manufacturer Rollomatic is offering the new GrindSmart629XS. This precision tool grinding machine is ideal for producing high-performance tools as well as inserts, threading tools, medical or dental tools and many more.
"It's definitely the first choice for tool manufacturers when it comes to a reliable, efficient and accurate production process," notes Damien Wunderlin, Head of Marketing and Sales at Rollomatic SA.
Much like its predecessor, the new GrindSmart629XS is designed for tools ranging between 0.1 and 16mm in diameter and features a unique sixth axis. This allows the operator to incline grinding wheels during operation and offers increased flexibility and freedom of movement especially for producing complex tool geometries. "In addition, the sixth axis ensures that the contact point on the grinding wheel remains constant at all times – resulting in even more precision," adds Damien Wunderlin.
The kinematics of the machine is also of fundamental importance to achieve unbeatable grinding results. The GrindSmart629XS is designed so that the movements of the axis between the operations are minimized. In addition, scales on all linear axes as well as the rotation axes are fitted as standard. The highlight among all features is the direct drive motor on the rotary B-axis. This precision technology enables high-performance servo tuning which provides an outstanding surface finish quality and form tolerance, particularly on tools with corner radii and a ball shape. In addition, the patented SmartGuide – the new shank guide system developed by Rollomatic – ensures perfect concentricity within 0.002mm.
To further increase productivity, the GrindSmart629XS features an extremely reliable integrated robot loader with a capacity of up to 20mm in diameter. Thanks to the compact design of the loading system, work pieces are changed in just over eight seconds. With a machine availability of 99 percent, the GrindSmart629XS thus produces an average of between 6,000 and 10,000 tools a month, depending on the tool type in question. The StickSmart system automatically cleans up the grinding wheels during the grinding process to ensure that abrasive wheels have the same performance for short and long batches. A further step towards light out production is offered by the JobManager in the VirtualGrindPro software. This new feature allows the user to produce a series of tools with different geometries out of the same blank diameter with no human intervention.
The GrindSmart629XS is equipped as standard with Rollomatic's latest generation of programming software. This powerful and flexible software offers total freedom of design while its user-friendly interface enables programming of standard or specific tools in only a few clicks using the programming wizard. To stay in tune with the latest software capabilities on the GrindSmart629XS, software upgrades are free of charge during the entire machine life. Damien Wunderlin: "Current and future tooling solutions can be easily retrofitted at any time to always keep your GrindSmart629XS up to date and give you a competitive edge."
Contact Details
Related Glossary Terms
- abrasive
abrasive
Substance used for grinding, honing, lapping, superfinishing and polishing. Examples include garnet, emery, corundum, silicon carbide, cubic boron nitride and diamond in various grit sizes.
- grinding
grinding
Machining operation in which material is removed from the workpiece by a powered abrasive wheel, stone, belt, paste, sheet, compound, slurry, etc. Takes various forms: surface grinding (creates flat and/or squared surfaces); cylindrical grinding (for external cylindrical and tapered shapes, fillets, undercuts, etc.); centerless grinding; chamfering; thread and form grinding; tool and cutter grinding; offhand grinding; lapping and polishing (grinding with extremely fine grits to create ultrasmooth surfaces); honing; and disc grinding.
- grinding machine
grinding machine
Powers a grinding wheel or other abrasive tool for the purpose of removing metal and finishing workpieces to close tolerances. Provides smooth, square, parallel and accurate workpiece surfaces. When ultrasmooth surfaces and finishes on the order of microns are required, lapping and honing machines (precision grinders that run abrasives with extremely fine, uniform grits) are used. In its “finishing” role, the grinder is perhaps the most widely used machine tool. Various styles are available: bench and pedestal grinders for sharpening lathe bits and drills; surface grinders for producing square, parallel, smooth and accurate parts; cylindrical and centerless grinders; center-hole grinders; form grinders; facemill and endmill grinders; gear-cutting grinders; jig grinders; abrasive belt (backstand, swing-frame, belt-roll) grinders; tool and cutter grinders for sharpening and resharpening cutting tools; carbide grinders; hand-held die grinders; and abrasive cutoff saws.
- grinding wheel
grinding wheel
Wheel formed from abrasive material mixed in a suitable matrix. Takes a variety of shapes but falls into two basic categories: one that cuts on its periphery, as in reciprocating grinding, and one that cuts on its side or face, as in tool and cutter grinding.
- shank
shank
Main body of a tool; the portion of a drill or similar end-held tool that fits into a collet, chuck or similar mounting device.
- threading
threading
Process of both external (e.g., thread milling) and internal (e.g., tapping, thread milling) cutting, turning and rolling of threads into particular material. Standardized specifications are available to determine the desired results of the threading process. Numerous thread-series designations are written for specific applications. Threading often is performed on a lathe. Specifications such as thread height are critical in determining the strength of the threads. The material used is taken into consideration in determining the expected results of any particular application for that threaded piece. In external threading, a calculated depth is required as well as a particular angle to the cut. To perform internal threading, the exact diameter to bore the hole is critical before threading. The threads are distinguished from one another by the amount of tolerance and/or allowance that is specified. See turning.
- tolerance
tolerance
Minimum and maximum amount a workpiece dimension is allowed to vary from a set standard and still be acceptable.