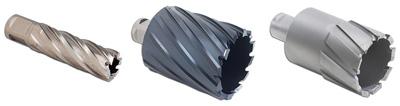
Walter Surface Technologies has redesigned their line of annular core cutters making the updated product line even more resistant to impact and stress, less brittle and impervious to deformation. The Walter core cutters now utilize a sophisticated mixture of high speed steel and aluminum (M2Al).
Walter offers three main product lines in this category: the SST Core Cut, the ICECUT and the Carbide Core Cutters.
The SST Core Cut is made with a surface treatment that reduces heat transfer and is the longest lasting uncoated core cutter available. The SST Core Cut is perfect for construction sites and in manufacturing processes.
The ICECUT core cutter provides unparalleled performance when compared to other coated cutters. It is coated with aluminum-chromium nitride PVD coating (AlCrN) which makes this core cutter ideal where lubricants are not permitted or problematic to apply. This special coating forms a nano-sized lubrication layer when heated, which prevents debris from rubbing, melting or deforming onto the metal.
In addition, the ICECUT core cutter has a heat resistance over 500°C higher than a titanium-coated cutter, and over 200°C than a titanium-aluminium blend, making it heat resistant. In addition, both the SST and ICECUT are designed with an exclusive multiple tooth design. The teeth of the core cutters are made at various heights and depths so that they can provide a faster drilling time.
The carbide core cutter is Walter's top performing cutter, allowing users to maximize productivity when cutting hard metals and uneven surfaces. It's primarily designed for extreme applications and can pierce through abrasive materials and non-ferrous metals such as stainless steel. It has a special lubricant zone which allows lubricants to get closer to the teeth, resulting in a cooler and smoother cut.
"This new generation of annular core cutters sets the standard for efficiency, reliability and high performance" said Stephane Drainville, Product Manager at Walter Surface Technologies. "Annular core cutters are already a cost effective solution when drilling large holes through thick and flat metal surfaces. By formulating our core cutters with this new blend of high speed steel and aluminum, we can increase the life of the product, precision and quality of the hole being drilled, which leads to additional cost savings to our customers."
Contact Details
Related Glossary Terms
- abrasive
abrasive
Substance used for grinding, honing, lapping, superfinishing and polishing. Examples include garnet, emery, corundum, silicon carbide, cubic boron nitride and diamond in various grit sizes.
- flat ( screw flat)
flat ( screw flat)
Flat surface machined into the shank of a cutting tool for enhanced holding of the tool.
- physical vapor deposition ( PVD)
physical vapor deposition ( PVD)
Tool-coating process performed at low temperature (500° C), compared to chemical vapor deposition (1,000° C). Employs electric field to generate necessary heat for depositing coating on a tool’s surface. See CVD, chemical vapor deposition.