Effectively and efficiently grinding workpieces to meet tolerance requirements is no easy task. Machine operators generally don’t perform the calculations for determining optimal grinding parameters because they are too complicated and instead go with the values that worked well in the past or rely on their gut feelings, according to Erhard Kämpf, head of the forms and threads department at grinding machine builder Fritz Studer AG.
“For them, it is often not possible to obtain good results in the desired time and without much optimization effort,” Kämpf said. He explained that the optimization effort involves determining what changes to make if the surface finish or roundness tolerances are not achieved. Those changes cover the dressing speed, infeed speed, spark-out time and rotation ratio of the workpiece and grinding wheel.
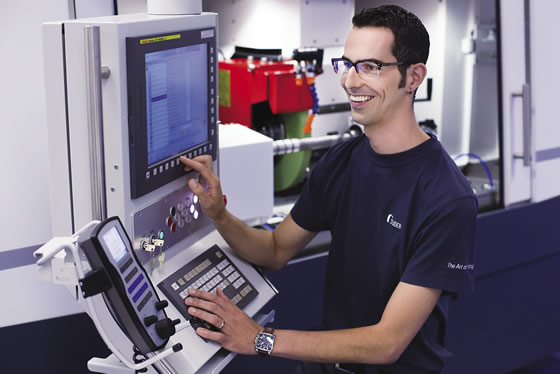
Having Studer-Technology Integrated software determine the correct grinding parameters relieves grinding machine operators from performing complex calculations.
The operator usually starts with one of these influencing factors, regrinds the workpiece and measures the part again, possibly repeating the time-consuming procedure several times until the tolerances are met. He added that most users underestimate the machining output of a wheel and, therefore, rarely dare to approach the limits of what is possible.
The task is particularly daunting when cylindrical grinding because more than 300 grinding parameters determine the process. Kämpf pointed out that in addition to the material-removal rate, feed rate for roughing, finishing and fine finishing, switching points, spark-out time and traverse speed—the most important parameters—grinding values include ones that are not often considered, such as critical speed, or integer, ratios (incorrect ratios for the number of workpiece and wheel revolutions can cause nonround diameters, such as polygons with varying numbers of lobes), part deflection and tangential force.
A new software package, StuderTechnology Integrated, overcomes this obstacle to higher productivity by performing the calculations to determine the optimal cylindrical grinding parameters based on operator entry of just a few critical process variables, such as the type of grinding wheel, workpiece material (including its hardness), and coolant, according to the company. Studer and its software partner, mcs software ag, developed the software, which is included at no additional charge in Studer grinders with StuderWIN controls.
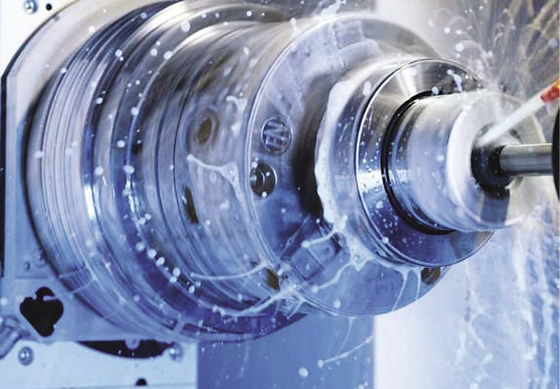
In most cases, StuderTechnology Integrated cuts cylindrical grinding time in half, according to the company.
“StuderTechnology Integrated allows shops, in most cases, to grind workpieces in half the time,” Kämpf said, adding that the return on investment for a grinder with the software is 25 percent quicker than the same grinder without it. “But because almost no optimization time is required, savings per workpiece is probably more than half.”
The company reports that the program contains the “best of cylindrical grinding” data from Studer’s nearly century of experience and that database is improved as Studer and its customers gain more process knowledge. “StuderTechnology is an open system,” Kämpf said. “The operator can accept the proposals and adapt his values at any time and save them as his own company know-how.”
According to Kämpf, because the software ensures an ideal result in a few seconds at the push of a button, operators with only a basic understanding of CNC machining can effectively run grinding machines. “They should at least know the types of workpiece materials, what heat treatment is and, roughly, the existing types of abrasives,” he said.
For more information about Fritz Studer AG, Thun/Steffisburg, Switzerland, contact United Grinding Technologies Inc., Miamisburg, Ohio, at (937) 859-1975 or www.grinding.com. For more information about mcs software ag, Bern, Switzerland, visit www.mcs.ch/en. CTE
Related Glossary Terms
- computer numerical control ( CNC)
computer numerical control ( CNC)
Microprocessor-based controller dedicated to a machine tool that permits the creation or modification of parts. Programmed numerical control activates the machine’s servos and spindle drives and controls the various machining operations. See DNC, direct numerical control; NC, numerical control.
- coolant
coolant
Fluid that reduces temperature buildup at the tool/workpiece interface during machining. Normally takes the form of a liquid such as soluble or chemical mixtures (semisynthetic, synthetic) but can be pressurized air or other gas. Because of water’s ability to absorb great quantities of heat, it is widely used as a coolant and vehicle for various cutting compounds, with the water-to-compound ratio varying with the machining task. See cutting fluid; semisynthetic cutting fluid; soluble-oil cutting fluid; synthetic cutting fluid.
- cylindrical grinding
cylindrical grinding
Grinding operation in which the workpiece is rotated around a fixed axis while the grinding wheel is fed into the outside surface in controlled relation to the axis of rotation. The workpiece is usually cylindrical, but it may be tapered or curvilinear in profile. See centerless grinding; grinding.
- dressing
dressing
Removal of undesirable materials from “loaded” grinding wheels using a single- or multi-point diamond or other tool. The process also exposes unused, sharp abrasive points. See loading; truing.
- feed
feed
Rate of change of position of the tool as a whole, relative to the workpiece while cutting.
- grinding
grinding
Machining operation in which material is removed from the workpiece by a powered abrasive wheel, stone, belt, paste, sheet, compound, slurry, etc. Takes various forms: surface grinding (creates flat and/or squared surfaces); cylindrical grinding (for external cylindrical and tapered shapes, fillets, undercuts, etc.); centerless grinding; chamfering; thread and form grinding; tool and cutter grinding; offhand grinding; lapping and polishing (grinding with extremely fine grits to create ultrasmooth surfaces); honing; and disc grinding.
- grinding machine
grinding machine
Powers a grinding wheel or other abrasive tool for the purpose of removing metal and finishing workpieces to close tolerances. Provides smooth, square, parallel and accurate workpiece surfaces. When ultrasmooth surfaces and finishes on the order of microns are required, lapping and honing machines (precision grinders that run abrasives with extremely fine, uniform grits) are used. In its “finishing” role, the grinder is perhaps the most widely used machine tool. Various styles are available: bench and pedestal grinders for sharpening lathe bits and drills; surface grinders for producing square, parallel, smooth and accurate parts; cylindrical and centerless grinders; center-hole grinders; form grinders; facemill and endmill grinders; gear-cutting grinders; jig grinders; abrasive belt (backstand, swing-frame, belt-roll) grinders; tool and cutter grinders for sharpening and resharpening cutting tools; carbide grinders; hand-held die grinders; and abrasive cutoff saws.
- grinding wheel
grinding wheel
Wheel formed from abrasive material mixed in a suitable matrix. Takes a variety of shapes but falls into two basic categories: one that cuts on its periphery, as in reciprocating grinding, and one that cuts on its side or face, as in tool and cutter grinding.
- spark-out ( sparking out)
spark-out ( sparking out)
Grinding of a workpiece at the end of a grind cycle without engaging any further down feed. The grinding forces are allowed to subside with time, ensuring a precision surface.
- tolerance
tolerance
Minimum and maximum amount a workpiece dimension is allowed to vary from a set standard and still be acceptable.