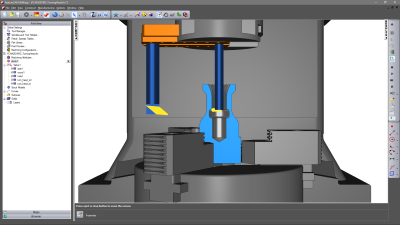
Delcam incorporates a wealth of new features into every release of its FeatureCAM product for automating CNC programming. FeatureCAM 2016 R3 available now, delivers a range of new features and improvements such as new toolpath strategies and access to Autodesk A360 collaboration software.
The FeatureCAM 2016 R3 enhancements begin with the capability to automatically control rotational machine axes during indexing or 3+2 machining. Machine limits can be used; from a machine design file, by specifying custom limits or using the shortest rotation the machine can take.
The new enhancements also include the ability to program two tools mounted to the same turning head tool holder. Turning heads are tool holders that enable turning operations when used on a milling machine.
Next, FeatureCAM 2016 R3 users can now create spiral toolpaths for facemilling operations. Depending on the part shape, this can reduce air cutting for a more efficient toolpath.
The FeatureCAM 2016 R3 user interface improvements also enable an improved workflow. The improvements include a new apply button within the transform dialogue for faster transformations, quicker navigation to feature coolants from the results tab, a new feature tab for post-processor variables to improve navigation, and a change to the simulation algorithm that results in better simulation speeds.
Finally, the incorporation of Autodesk A360 enables project collaboration, file viewing and file sharing—all within a single, central workspace.
“FeatureCAM automates the workflow from design to NC code,” said Sanjay Thakore, product marketing manager at Delcam. “Automation tools including feature recognition reduce programming time and increase programming consistency. The new features in FeatureCAM 2016 R3 will further enhance programming capabilities, ultimately resulting in increased productivity.”
Contact Details
Related Glossary Terms
- computer numerical control ( CNC)
computer numerical control ( CNC)
Microprocessor-based controller dedicated to a machine tool that permits the creation or modification of parts. Programmed numerical control activates the machine’s servos and spindle drives and controls the various machining operations. See DNC, direct numerical control; NC, numerical control.
- facemilling
facemilling
Form of milling that produces a flat surface generally at right angles to the rotating axis of a cutter having teeth or inserts both on its periphery and on its end face.
- gang cutting ( milling)
gang cutting ( milling)
Machining with several cutters mounted on a single arbor, generally for simultaneous cutting.
- milling
milling
Machining operation in which metal or other material is removed by applying power to a rotating cutter. In vertical milling, the cutting tool is mounted vertically on the spindle. In horizontal milling, the cutting tool is mounted horizontally, either directly on the spindle or on an arbor. Horizontal milling is further broken down into conventional milling, where the cutter rotates opposite the direction of feed, or “up” into the workpiece; and climb milling, where the cutter rotates in the direction of feed, or “down” into the workpiece. Milling operations include plane or surface milling, endmilling, facemilling, angle milling, form milling and profiling.
- milling machine ( mill)
milling machine ( mill)
Runs endmills and arbor-mounted milling cutters. Features include a head with a spindle that drives the cutters; a column, knee and table that provide motion in the three Cartesian axes; and a base that supports the components and houses the cutting-fluid pump and reservoir. The work is mounted on the table and fed into the rotating cutter or endmill to accomplish the milling steps; vertical milling machines also feed endmills into the work by means of a spindle-mounted quill. Models range from small manual machines to big bed-type and duplex mills. All take one of three basic forms: vertical, horizontal or convertible horizontal/vertical. Vertical machines may be knee-type (the table is mounted on a knee that can be elevated) or bed-type (the table is securely supported and only moves horizontally). In general, horizontal machines are bigger and more powerful, while vertical machines are lighter but more versatile and easier to set up and operate.
- numerical control ( NC)
numerical control ( NC)
Any controlled equipment that allows an operator to program its movement by entering a series of coded numbers and symbols. See CNC, computer numerical control; DNC, direct numerical control.
- toolpath( cutter path)
toolpath( cutter path)
2-D or 3-D path generated by program code or a CAM system and followed by tool when machining a part.
- turning
turning
Workpiece is held in a chuck, mounted on a face plate or secured between centers and rotated while a cutting tool, normally a single-point tool, is fed into it along its periphery or across its end or face. Takes the form of straight turning (cutting along the periphery of the workpiece); taper turning (creating a taper); step turning (turning different-size diameters on the same work); chamfering (beveling an edge or shoulder); facing (cutting on an end); turning threads (usually external but can be internal); roughing (high-volume metal removal); and finishing (final light cuts). Performed on lathes, turning centers, chucking machines, automatic screw machines and similar machines.