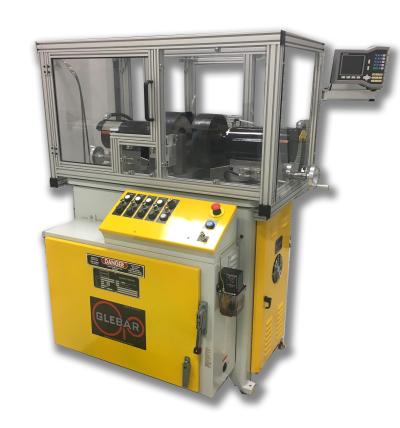
Glebar has developed a double-disc grinding process on its DD-7 double-disc grinder for materials suppliers and manufacturers of high-performance composites that expedites the grinding of composite strips used as low friction, bearing elements in various industries from aerospace to automotive, leading to reduced production costs and enhanced quality.
A case study for a major supplier of sealing solutions demonstrates how the automated DD-7 was able to cut the grinding rate down nearly four times versus the previous manual method utilized by the customer.
The main challenge was to achieve the tight flatness tolerances required in a continuous spool to spool process by double side grinding the strip at a fast throughput rate. This process was facilitated by the use of a tractor and two 10” grinding wheels with material feeding and extraction using spool assemblies. A unique grinding wheel configuration allowed the material to be rapidly removed while maintaining a thickness tolerance on a product that is engineered to be wear resistant by nature.
Results of the case study are as follows:
Feed rate: 6 meters per minute (19 sfm)
Grind: 25mm strip 2.9 down to 2.42
Material removal: 0.25mm per side (0.010” per side)
Tolerance: (+/-0.025mm) +/-0.001”
“The double-disc grinding development process for composite strips can be an arduous task. Prior to using the DD-7, one of the largest challenges our customers had with grinding this type of material and shape was the limitations of belt sanding machines which require multiple passes on each side, requiring operator handling and take up a lot of floor space,” said Robert Gleason, vice president of engineering for Glebar Co. “By utilizing the DD-7’s tractor infeed extractor coupled with spool feeding and collection systems, the ability for continuous feeding, grinding and extracting the material without operator intervention was possible.”
The machine also had to be built, assessed and tested to accept the CE mark. Several standards including the EU Machinery Directive and EMC directive insured that the DD-7 is in conformity with CE standards.
Contact Details
Related Glossary Terms
- composites
composites
Materials composed of different elements, with one element normally embedded in another, held together by a compatible binder.
- feed
feed
Rate of change of position of the tool as a whole, relative to the workpiece while cutting.
- grinding
grinding
Machining operation in which material is removed from the workpiece by a powered abrasive wheel, stone, belt, paste, sheet, compound, slurry, etc. Takes various forms: surface grinding (creates flat and/or squared surfaces); cylindrical grinding (for external cylindrical and tapered shapes, fillets, undercuts, etc.); centerless grinding; chamfering; thread and form grinding; tool and cutter grinding; offhand grinding; lapping and polishing (grinding with extremely fine grits to create ultrasmooth surfaces); honing; and disc grinding.
- grinding wheel
grinding wheel
Wheel formed from abrasive material mixed in a suitable matrix. Takes a variety of shapes but falls into two basic categories: one that cuts on its periphery, as in reciprocating grinding, and one that cuts on its side or face, as in tool and cutter grinding.
- tolerance
tolerance
Minimum and maximum amount a workpiece dimension is allowed to vary from a set standard and still be acceptable.