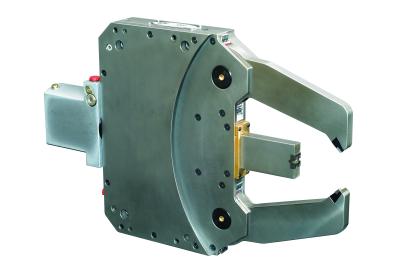
Kitagawa NorthTech Inc. introduces a new series of grinding steady rests. The grinding steady rests feature two models supported with turnkey design, build and installation capabilities dedicated to grinding applications. The new fully retracting KRGU steady rests (pictured) and GHS steady rests are suitable for camshafts, crankshafts and other cylindrical applications where accuracy and repeatability are essential.
Steady rests are a critical requirement for the grinding camshafts, crankshafts and other relative geometries. When the piece length increases relative to the diameter it becomes unstable and will deflect under the grind load. Kitagawa NorthTech says the use of its grinding steady rests will eliminate the problems of part deflection, grind surface finish and centering accuracy.
The KRGU series steady rests are specially designed for crankshaft grinding to accommodate the maximum eccentric throw and journal diameter of crankshafts. Custom designs are available to accommodate automated loading. Available in standard gripping diameters from 2.75” (70 mm) to 7.5” (190 mm).
Key features and benefits include:
• Retractable body using guide ways
• Suitable for all crankshaft, camshaft and cylindrical grinding applications where high eccentric throw is a requirement
• High accuracy, with three-point finely adjustable centering capability
• Modular regrindable carbide or relappable PCD work rest pads
• Works well with retracting in-process gaging (IPG)
The GHS series general-purpose steady rests are for all standard and automated grinding applications, such as cylindrical grinding, camshaft grinding and camlobe grinding. Available in standard gripping diameters from .394” (10 mm) to 4.724” (120 mm).
Key features and benefits include:
• Suitable for all crankshaft, camshaft and cylindrical grinding applications
• High accuracy, with three-point finely adjustable centering capability
• Modular regrindable carbide or relappable PCD work rest pads
• Works well with retracting in-process gaging (IPG)
Contact Details
Related Glossary Terms
- centering
centering
1. Process of locating the center of a workpiece to be mounted on centers. 2. Process of mounting the workpiece concentric to the machine spindle. See centers.
- cylindrical grinding
cylindrical grinding
Grinding operation in which the workpiece is rotated around a fixed axis while the grinding wheel is fed into the outside surface in controlled relation to the axis of rotation. The workpiece is usually cylindrical, but it may be tapered or curvilinear in profile. See centerless grinding; grinding.
- grinding
grinding
Machining operation in which material is removed from the workpiece by a powered abrasive wheel, stone, belt, paste, sheet, compound, slurry, etc. Takes various forms: surface grinding (creates flat and/or squared surfaces); cylindrical grinding (for external cylindrical and tapered shapes, fillets, undercuts, etc.); centerless grinding; chamfering; thread and form grinding; tool and cutter grinding; offhand grinding; lapping and polishing (grinding with extremely fine grits to create ultrasmooth surfaces); honing; and disc grinding.
- in-process gaging ( in-process inspection)
in-process gaging ( in-process inspection)
Quality-control approach that monitors work in progress, rather than inspecting parts after the run has been completed. May be done manually on a spot-check basis but often involves automatic sensors that provide 100 percent inspection.
- polycrystalline diamond ( PCD)
polycrystalline diamond ( PCD)
Cutting tool material consisting of natural or synthetic diamond crystals bonded together under high pressure at elevated temperatures. PCD is available as a tip brazed to a carbide insert carrier. Used for machining nonferrous alloys and nonmetallic materials at high cutting speeds.